Accessible LiDAR Technology Drives Efficiency and Planning in Quarries
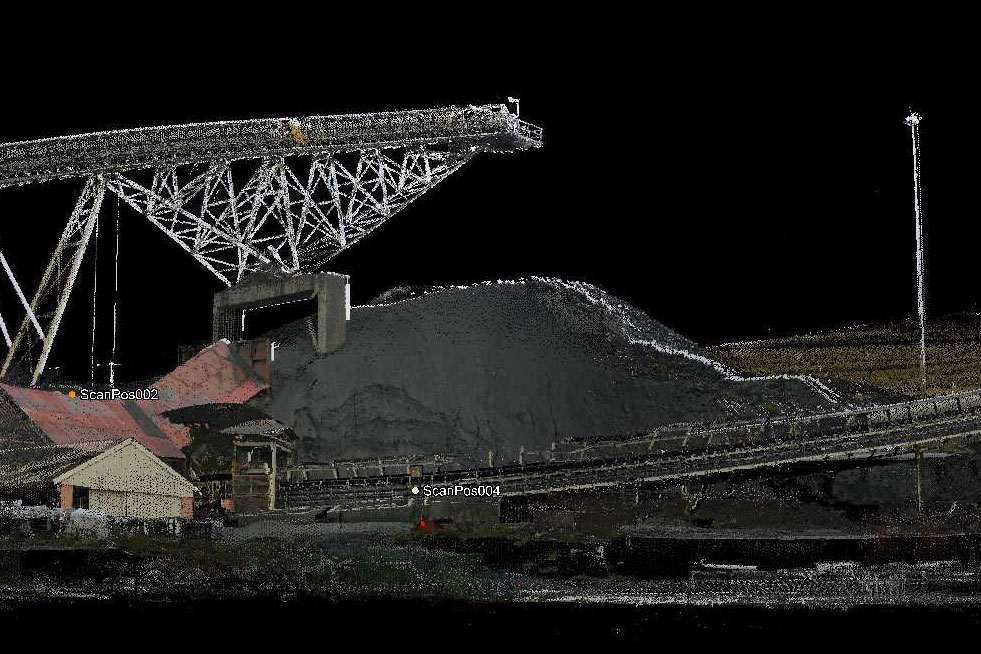
First published in the September 2018 issue of Quarry Management as Surveying the Future
Madeleine Lake of 3D Laser Mapping explains how LiDAR technology is driving efficiency and planning in quarries
With media reports suggesting that the British economy is facing tough times ahead, economic growth remains slow with only the services and manufacturing sectors continuing to drive optimism in post-Brexit predictions. All eyes are now on the industries that have the ability to further create jobs and opportunities for self-sufficiency once the UK leaves the EU.
This leaves heavy-side manufacturers in the spotlight and, to facilitate the necessary growth, mineral products will need to be extracted and processed at an increased rate. With public opinion strongly opposed to new extractives sites, and plans taking years to pass, how can the industry meet expectations for increased productivity without rapid expansion?
In this article, Madeleine Lake, technical sales manager at geospatial technology providers 3D Laser Mapping, discusses how a new wave of data-driven solutions can help quarrying operations to improve efficiencies.
Increased house-building targets and other major infrastructure projects, such as Crossrail and HS2, indicate the heavy industries are optimistic that life will go on after Brexit. This level of increased spending on public services and infrastructure is already having a positive knock-on effect for extractives operations, with more than £20 billion worth of materials and services supplied into the economy during 2016.
Mines and quarries currently contribute 12% towards the IoP (Index of Production) of the UK – which is one of the most important short-term economic indicators used to measure and calculate GDP figures. With this in mind, mineral products are key when it comes to supporting the stability of a range of other sectors such as construction, transportation and environmental activities, meaning that every effort needs to be made to increase output in line with demand.
Mining and quarrying operations face considerable challenges over the coming years. Worsening weather conditions, as a result of the harsher winters seen in recent years, are having a severe impact on productivity, with many quarries simply unable to operate in freezing conditions. Business planning and logistical tasks are also made harder thanks to unpredictable demand when the aforementioned weather conditions affect construction projects. When any business faces the challenge of increasing efficiency, it is data-driven technology that can hold the key to scalable improvements.
LiDAR (light detection and ranging) is one technology that is starting to see widespread use in the quarrying sector. Traditionally used for analysing the geotechnical properties of mineral and aggregate quarries, this technology is now being developed to become more accessible for other tasks that will contribute to tangible business improvements.
Remote-sensing methods such as LiDAR and photogrammetry have been used to great effect in both mining and quarrying settings. Capable of collecting geological data that are accurate to less than a centimetre, laser scanning systems collect millions of measurements that can be used in rock mass classification, as well as to monitor areas prone to rockfall. Each measurement collected is processed into a single data set to create a three-dimensional representation of the target area, known as a point cloud. Because of the sheer number of measurements collected, these data sets can often run into multiple terabytes, necessitating the help of dedicated processing resources and a delay in getting results.
Over recent years, LiDAR systems have become smaller, more mobile and easier to use. Mobile laser scanners (MLS) can now carry out surveys around 80% faster than their terrestrial predecessors. Advancements in processing software are also having an impact on the speed at which results are made available. When faced with an unpredictable economic climate and fluctuating demand, enhanced, immediate business intelligence can be critical to stability.
Planning for the future
One of the greatest challenges to the extractives industry is public opinion. Nobody wants a busy, noisy quarrying facility on their doorstep, adding to road traffic levels and destroying air quality and picturesque environments. Planning new quarry works is time-consuming and expensive for a reason, with the added headache of local people and businesses having to be assured that the impact of the facility will be minimal. Environmental impact assessments, land surveys and geological surveys can all take months to prepare, with life-span considerations needed to cover even the eventual closure and restoration of sites. This is where LiDAR data can be invaluable.
There is often concern raised by communities that quarry works will pollute local water supplies, compromise local footpaths and forever change the landscape in the proposed area. Quarry design can be enhanced by using mobile laser-scanning equipment to establish boundaries, identify minor tributaries and even identify ground-level features that are not obviously apparent using standard equipment.
Because of the detail and three-dimensional characteristics contained within a point cloud, LiDAR data sets can be used for multiple purposes. As well as providing planning teams with accurate measurements, 3D modelling software can be used to generate tangible maps of the terrain and visualizations of future planned changes. This can go a long way towards providing communities with assurances and visual references of planned works.
Do more with less
In uncertain economic times, the burden on all businesses is to do more with less. Increase output with fewer resources, bill more hours with fewer staff – the pressure can be insurmountable. In a quarrying setting, the aim is often to speed up processes whilst creating less waste. On average, only 60–80% of extracted material finds a commercial use, so keeping an eye on waste levels and quarry fines is critical to the efficiency and profitability of any extractives operation.
In the initial planning stages, a site manager or operator should have identified an area to locate waste tips and stockpiles that would have the least impact on the surrounding environment. This should have taken into account surface water flow, as well as safety considerations should an issue occur. Any place where loose matter, such as fines, is collected can become susceptible to erosion and collapse, yet it is a balancing act when it comes to revegetating waste tips before they become unstable and using valuable space while it is still viable.
In addition to distance measurements, laser scanning can also perform volumetric calculations. The same level of accuracy and detail can be applied to measuring mass as measuring length. Short- and long-range LiDAR systems can provide results that are more than 95% accurate for measuring waste and stockpile volumes. This can help site managers to keep a watchful eye on waste tips before they get to ‘tipping point’.
This same logic can be applied to the measurement of viable, saleable stockpiles. Depending on the level of detail required, different laser scanner set-ups can be configured to scan single or multiple stockpiles to allow accurate inventories to be taken, or even to calculate blast quantities and monitor productivity levels. Previously, this would have necessitated manual measurements and calculations to be made – something which can use up valuable work hours and put site operatives at risk while measurements are taken.
With close to real-time outputs, automated inventory management systems such as SITEMONITOR LIVE +VOLUMES provide critical business intelligence to support logistical planning without having to use additional resources.
Site-wide intelligence
Active monitoring is critical when it comes to analysing productivity trends, and monitoring relies on being able to compare data collected over a period of time. This is one of the greatest benefits of LiDAR data and the new wave of processing software becoming available. SITEMONITOR LIVE is a patented scanner and software package that allows for operation-wide monitoring. Single or multiple scanners can be set up across an entire site to monitor critical assets remotely.
Another major advantage of monitoring assets remotely is in on-site safety. Scanners can be used to replace the need for manual inspections, not just of stockpiles and assets, but also of critical infrastructure such as berms and benches where stability is an issue. This removes the need to send survey teams into hazardous areas and can also provide operators with prior warning of imminent slope failure.
Business intelligence is only meaningful if the information can be applied across different areas of the operation. With the option to integrate single or multiple scanners, SITEMONITOR LIVE has been designed to collect LiDAR data that can simultaneously monitor slope stability, structural features such as berms and waste sites, as well as measure and monitor stockpiles and other assets. Integrated into a single interface, the three different software elements represent a step-change in the way that mines and quarries can monitor their productivity and safety levels automatically.
Conclusion
Whilst the future of the UK’s economy may be unpredictable, it is the reliance of other critical industries on the country’s quarries that will assure their future. Demand may be sporadic and changeable, and this will always be out of the hands of operators, yet embracing connected, data-driven systems can and will help the industry plan for success.
For more information visit: www.3dlasermapping.com
- Subscribe to Quarry Management, the monthly journal for the mineral products industry, to read articles before they appear on Agg-Net.com