Thin On Top
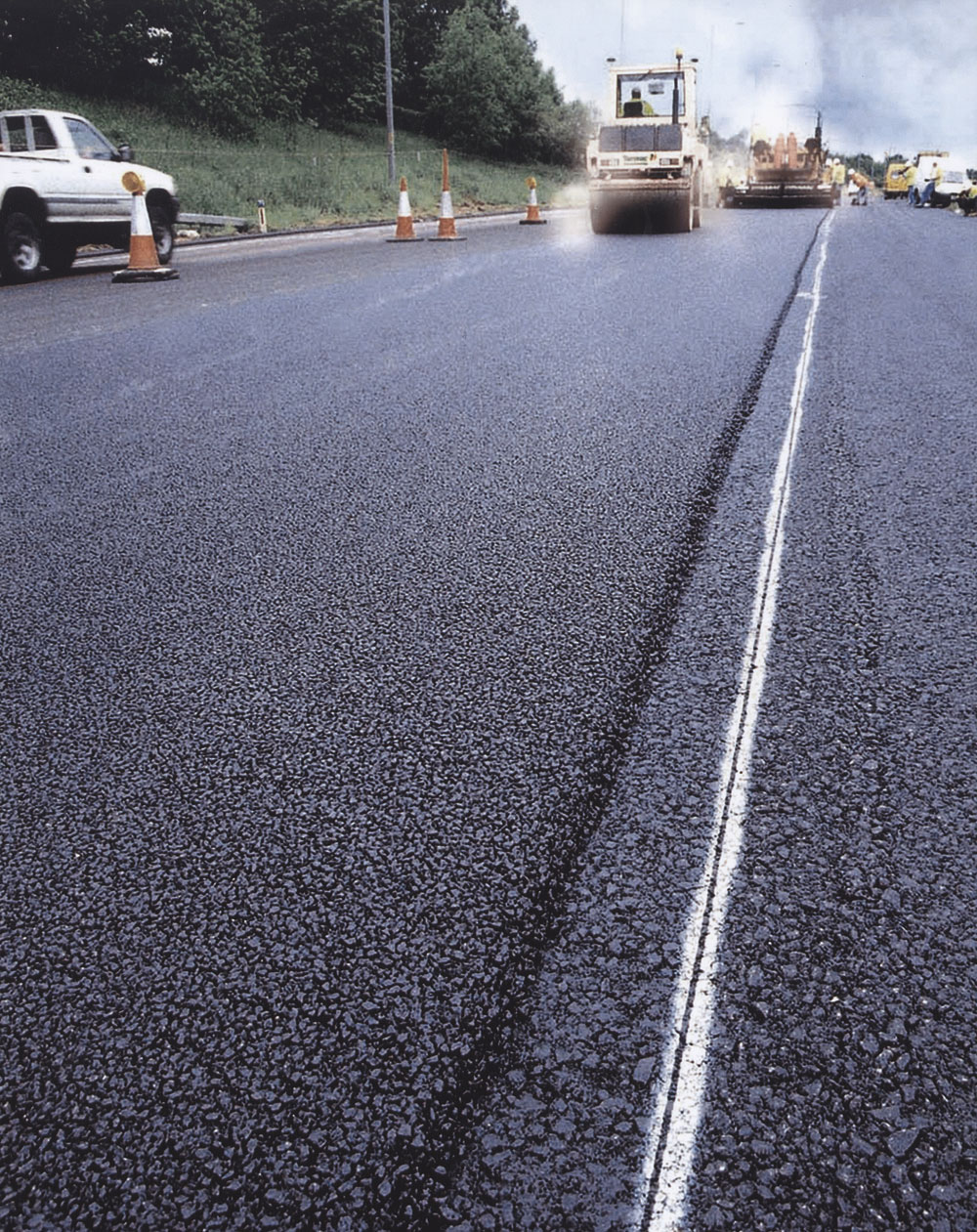
The selection and use of thin surfacings
The author, Ian D. Walsh, is technical director with Babtie Laboratory
Thin surfacings comprise a wide range of materials now used for maintenance and new construction on highways. They give engineers a sometimes bewildering array of options. This paper is intended to provide information on the advantages and disadvantages of particular systems discussed below.
The relative merits of the systems and ranking in table 1 are, by their very nature, subjective and this paper is based on the author’s experience with the materials, in the case of hot-mix systems over the last 10 years since their introduction and usurpation of HRA surface course.
The development of the BBA HAPAS approval system has had a very beneficial effect on the introduction and control of the innovative proprietary products discussed here. Standard products are controlled by SHW Clauses and Sector Schemes for Quality Assurance (12A – Surface Dressing, 12B – Slurry Surfacing and 14 – Asphalt, which includes materials for use in thin surfacings). Clients are strongly recommended to take an interest in the paperwork generated by and available for these systems, using specialist advice if necessary to ensure that contractors are demonstrating that the specified quality is being or will be achieved.
Properties of thin-surfacing materials
Thin surfacings have a wide range of properties, as indicated in table 1. It can be seen that the materials are not all equal in their performance; this is because of their formulation, method of installation and thickness.
One of the benefits of thin surfacings is that they can be laid within the width of a lane, very quickly and safely and without the need to apply precoated chippings. Traffic should be able to use the surface soon after laying without causing damage.
Hot-mix materials and microasphalt all have excellent rut resistance. However, the thinner the surface, the more load is transferred to the underlying layer. In maintenance applications, if the existing surface is not rutted, this is unlikely to be a problem. On new construction, particularly for heavy/channelled trafficked sites, the deformation of the binder course must be assessed by the vacuum RLAT test and the wheel-tracking test to ensure that it will be adequate.
The tyre noise, rolling resistance and skid resistance of a thin surfacing is closely related to the aggregate size, as shown in figures 1, 2 and 3.
Thin surfacing comes in a range of thicknesses, as follows:
High-friction surfacing: 3–6mm
Slurry surfacing: 3–6mm
Surface dressing: 6–10mm
Cold thin surfacing Type A [microasphalt]: 4–12mm
Hot-mix thin surfacing Type A: 10–18mm
Hot-mix thin surfacing Type B: 18–25mm
Hot-mix thin surfacing Type C: 25–50mm.
A 6mm aggregate Type A and 10mm Type B thin surfacing can easily become smooth and hence slippery. This can be overcome by using a highly voided mixture with suitable mix design and installation for durability. The use of retained texture depth is included as a contract-specific requirement by many clients to ensure adequate long-term performance of all thin surfacings.
High-friction surfacing
High-friction surfacing (HFS) material has been available for many years as a spray- or squeegee-applied two-part epoxy system with calcined bauxite aggregate (3mm nominal size).
The use of this material has been remarkably successful in reducing accidents at high-risk sites as a result of its very high skid resistance. This is due in part to the polished-stone value of the aggregate, but more importantly to the aggregate shape and size. The small aggregate with angular shape generates very high hysteresis in the tyre rubber as the vehicle skids. The very hard aggregate is slow to abrade and the binder film reduces embedment; both of these contribute to durability. Expected life is in excess of eight years.
Because of the long curing time in cold weather, the need to surface small sites at the approaches to crossings and traffic lights and the problems of coverage of adhesive on thin surfacing, there was a need for processes to overcome these issues. The industry responded by developing hot-applied thermoplastic HFS. This coincided with the introduction of the HAPAS guideline document, which introduced performance-related tests such as the scuffing test for wear resistance and the tensile adhesion test. The original specification (SHW Clause 924) was essentially a recipe-based approach; the HAPAS approach greatly assisted with the innovative introduction of hot-mix materials.
The small aggregate size also significantly reduces tyre noise and makes HFS very quiet to drive on.
HFS must be applied to a surface with a low/medium surface texture otherwise excessive material will fill the voids, which is expensive and undesirable. Epoxy and polyurethane binder systems in particular have very different thermal characteristics from bitumen-bound materials. In conjunction with the high horizontal forces induced as traffic brakes, the surface can be torn, leading to wide cracks at the road surface. These can lead to fretting and potholing of the surface.
Polyurethane adhesive is applied by squeegee and the aggregate broadcast; whereas thermoplastic systems are applied using a screed box. The box can introduce ridges in the overlap which are not significant technically and may even be beneficial as they affect car comfort in slow-speed installations. However, they can be unsatisfactory for higher-speed locations, such as village gateways.
Coloured HFS can be achieved by colouring the binder and coating the aggregate. The latter is comparatively short-lived. Calcined bauxite can be grey or buff. The choice is aesthetic and generally left to the contractor, although some local authorities have a policy on the colour used.
Slurry surfacing
This is a mixture of bitumen emulsion, cement/filler and fine aggregate, applied with a squeegee. It may be supplied in drums, which should be agitated prior to use.
It is particularly suitable for the aesthetic improvement of footways, particularly in lightly trafficked housing development locations. It is capable of filling small depressions, such as slightly settled trenches, while deeper depressions, ie up to 10mm, may need two coats locally. Wear resistance is poor so slurry surfacing should not be used on the highway.
The material usually fails by wearing away/abrasion or delamination. Life expectancy is four to eight years.
Surface dressing
Surface dressing is, without doubt, the cheapest way of restoring the skid resistance of a road. It also seals a porous surface and may fill narrow ‘micro-cracks’. On rutted roads, ie those with settled trenches and poor profile and those with wider cracks, such as old concrete surfaces, it is unlikely to be cost-effective as a medium-term solution.
Wherever possible, surface dressing should be installed using the ‘design and install’ Clause (SHW Clause 922). All the evidence shows that this costs no more than client design with all the deficiencies inherent in shared responsibility as defects occur. It does require the client to make available all the site details to permit a design to be carried out, which is normally but not necessarily in accordance with Road Note 39. Additionally, particularly with emulsion binders, good surface dressing requires a correct match of aggregate type to binder; this is solely in the contractor’s control. Similarly, the size of aggregate may need to be matched to the road surface hardness at the time of construction; too small a stone on a soft substratum will rapidly embed, losing texture and becoming slippery.
Emulsion binders have become the norm, largely on health, safety and environmental grounds, and in most situations are excellent binders. However, they need chemical setting, the use of polymers and plenty of compaction if they are to be successful on high-speed roads and roads where significant braking and turning occur, unless traffic control can be put in place for many hours. Dictating the maximum time before all signs can be removed and unrestricted traffic can use the road is one way of specifying surface dressing in a performance-related way to stimulate the contractor to use the optimal process within his armoury.
Cold thin surfacing Type A [microasphalt] 4–12mm thick
Microasphalt is superficially similar to slurry surfacing, in that a bitumen emulsion slurry is used to hold the fine aggregate. However, microasphalt generally uses specially formulated polymer-modified bitumen to increase the cohesion of the binder and grip the aggregate better and may contain fibres to improve wear resistance and crack resistance.
Microasphalt may be used on a wide range of highway sites to improve skid resistance and reduce tyre noise if there is excessive texture depth. It contributes no structural strength and will not have good durability where there is significant braking and turning; in this regard it is probably more sensitive than surface dressing. It is particularly suitable where potholes, settled trenches and rutting have affected the surface profile. For rutted surfaces, an investigation may be necessary to assess the rut resistance of the existing surface; if it is poor, inlay using a hot-mix thin surfacing is preferred. Since the aggregate is trapped within the filled binder mixture once compaction is complete, subsequent chip loss is reduced.
This makes microasphalt particularly suitable for low-traffic sites such as estate roads where embedment from traffic will be low. It has a high degree of customer acceptance.
These systems are normally proprietary products. The two most well known are Ralumac from Colas, particularly formulated to be rut resistant, and Gripfibre from Ringway, which is more crack resistant.
Materials cannot be laid in cold weather; a sensible close season is November to February inclusive.
The materials will be certified by the British Board of Agrément to ensure consistency and durability. Life expectancy is six to 10 years.
Hot-mix thin surfacing Type A 10–18mm thick
Hot-mix thin surfacings Type A are porous (open-graded) mixtures normally made with single-sized 6mm aggregate, though 10mm aggregate may be used. They must be laid on a thick polymer-modified bond coat normally using a tracked paver to provide a stable platform.
The material must be laid on a base that does not contain depressions that can hold water. It is therefore generally not suitable for rutted or potholed sites without planing or pre-filling. It is suitable for all highway sites, although its use on sites where heavy traffic is braking or turning may be risky, as this will transfer very high stresses to the bond coat.
Planing 500mm at the kerb edge is usually sufficient to give 75mm minimum kerb height (25mm at crossovers) and drain the nearside rut, if any, without creating undue camber.
Alternatively, it may be possible to stop the surfacing 20mm from the kerb to give a ‘chip-free channel’ effect without creating a hazard. Slow-lay inlay must be taken out to the road edge to ensure drainage. The material performs best where kerb-edge drainage exists, set to drain the underside of the materials. The material can be used to regulate during the laying operation (up to 60mm thick).
The bond coat gives good crack sealing ability but the resistance to cracking of the material itself is poor. It can have high texture, good skid resistance (as a result of PSV, texture depth and aggregate size) and exceptional tyre noise reduction.
While not significant for local road applications, it also reduces spray. The material bonds well to the carriageway and does not ‘peel back’ from any cracks. It cannot be used alone with geotextile or polymer binder SAMI, as it is too thin.
Because it is both thin and porous it has little structural strength. Where it is part of a thicker overlay, it should be laid on an SMA binder course (SHW Clause 937), normally 35mm thick and designed to be rut resistant, to ensure water does not enter the pavement structure. This may need to be considered when carrying out a structural design.
The PSV of the coarse aggregate shall be in accordance with HD28; however, the surface coverage, size of aggregate and shape of the texture may mean that a lower PSV could be used. Suppliers would have to demonstrate this by presenting comparative SCRIM or Griptester results.
A smaller machine has now increased availability for smaller sites, but hand laying can be difficult. It cannot be laid in cold weather; a sensible close season is November to February inclusive.
Possible construction faults include — fatting up, fretting joints, dragging, and clogging of the texture. Subject to temperature constraints, it is not susceptible to faults from poor compaction as the paver compacts the layer.
Hot-mix thin surfacing Type B 18–25mm thick
Hot-mix thin surfacing Type B is normally made with 10mm nominal size aggregate. It is usually laid with a tracked paver to provide a stable platform on a thick bond coat, which may be polymer modified. This gives good crack sealing ability. It has good skid resistance (as a result of PSV, texture depth and aggregate size) and noise-reducing characteristics. When formulated to achieve high texture depth, the material will be porous, initially reducing spray in damp weather but outside the wheel track may become clogged.
High texture is, however, achievable initially but on slow-speed sites this may reduce to low texture with time. A contract specification for retained texture depth requirement is essential to ensure the correct formulation is provided.
It is generally suitable for rutted or potholed sites without planing or pre-filling. Any site with more than 20% to be patched would be suitable for consideration. The material can be used to regulate during the laying operation (up to 60mm thick) or may be used for pre-filling.
Resistance to cracking depends on the material thickness. Therefore, Type B is better than Type A thin surfacing but not as good as Type C. However, provided the cracks are only moving slightly, the heavy bond coat will seal them. It probably cannot be used alone with geotextile or polymer-modified SAMI, as it is too thin for laying.
Planing 500mm at the kerb edge is usually sufficient to give 75mm minimum kerb height (25mm at crossovers) and obviates the need for gully raising without creating undue camber. It can be used for inlay — a useful technique for rutted areas in the vicinity of traffic lights, depending on the cause of the rut.
Dense materials have similar structural strength to DBM, ie slightly better than HRA surface course, and may be laid on a C1 929 base material. A 20mm overlay gives about a 50% increase in the life of a road. Those formulated to give ‘high texture’ have about half this strength and should be laid on an SMA binder course to SHW Clause 937 normally 35mm thick. Allowance for this should be made when carrying out a structural pavement design.
The PSV of the coarse aggregate shall be in accordance with HD28; however the surface coverage, size of aggregate and shape of the texture may mean that a lower PSV could be used. Again, suppliers would have to demonstrate this by presenting comparative SCRIM or Griptester results.
Type B material is very difficult to lay satisfactorily in cold weather; a sensible close season is December to February inclusive, as lack of compaction can lead to extensive premature surface fretting failure.
In conjunction with the impermeable SMA binder course, Type B thin surfacing probably offers the ideal combination of durability of the surface and of the road as a whole, together with very good rut resistance, spray reduction and low noise levels. It may, however, be up to 15% more expensive than a single course of Type C material. The binder course needs to be designed for rut resistance, particularly for sites with heavy channelled traffic.
Construction faults, which are rare, include fretting joints, dragging and closing up of texture. Life expectancy based on Safepave and ULM laid in Kent is in excess of 10 years defect free when laid on a sound substratum.
Subject to temperature constraints, Type B thin surfacing is not susceptible to faults due to poor compaction. Early-life skid resistance is covered by the same requirements as Type C material.
Surprisingly, this is often the most expensive option, as specialist machinery should be used to lay it, it requires a good polymer-modified bond coat and the 10mm aggregate, which has to be of good shape, is in short supply.
Hot-mix thin surfacing Type C 25–50mm thick
This is also commonly known as SMA though the material is not the same as the continental product of the same name, as changes have been made to satisfy UK texture requirements. These can make the material more porous.
The material is normally made with 14mm aggregate but 10mm may also be used depending on texture depth and noise-reducing requirements. It is designed with a high binder content, which may be polymer modified for durability, and contains cellulose fibres to hold the binder in the mixture. It is laid on a thin or thick tack coat, which may be polymer modified, the latter giving some general sealing ability. The texture is often less than Type A and Type B surfacing initially and can reduce further on heavily trafficked slow lanes. A retained texture depth requirement in the contract is considered essential.
It is generally suitable for rutted or potholed sites without planing or pre-filling. Any site with more than 20% to be patched would be suitable for consideration. The material can be used to regulate during the laying operation (up to 60mm thick) or may be used for pre-filling.
Resistance to cracking depends on the thickness; therefore it is better than both Type A and Type B thin surfacing. It may be used with geotextile or polymer-modified SAMI alone or with a binder course. A project on the M5 in October 2003 completed 70,000m2 of proprietary spray-applied SAMI in five working days with a binder course and Type C surfacing above, to overlay a jointed concrete carriageway to delay reflective cracking.
Planing 500mm at the kerb edge may be possible to give 75mm minimum kerb height (25mm at crossovers) and obviate the need for gully raising without creating undue camber. It can be used for inlay – a useful technique for rutted areas in the vicinity of traffic lights, depending on the cause of the rut.
It has similar structural strength to DBM 100; a 30mm overlay gives about a 70% increase in the life of the road. It may be laid up to 50mm thick where permitted by the HAPAS Certificate. However, this may lead to a faster loss of texture depth and rutting if manufactured with excess binder. Accordingly, some clients do not recommend Type C material for very heavily trafficked sites.
The PSV of the coarse aggregate shall be in accordance with HD28; however the surface coverage, size of aggregate and shape of the texture may mean that a lower PSV could be used. Once again, suppliers would have to demonstrate this by presenting comparative SCRIM or Griptester results.
Type C material can be laid throughout the year subject to temperature controls on the existing road to ensure bonding (road heating may be required) and on air temperature/exposure to windy conditions to ensure adequate compaction.
Construction faults include: fatting up, fretting joints, dragging, delamination at junctions when laid in adverse weather conditions, closing up of texture, and high voids through poor compaction with consequent effects on durability.
Notwithstanding this, life expectancy is thought to exceed 10 years if laid correctly initially.
Early-life skid resistance has been the subject of advice from both Highways Agency Interim Advice Note (IAN) 49/03 and from the CSS. This followed problems particularly with non-HAPAS-approved stone-mastic asphalt surface-course material. IAN 49/03 requires the investigatory skid-resistance level (IL) by SCRIM to be obtained from HD 28; if it is 0.45 or above, the early-life skid resistance could fall below this. Warning signs must be erected and maintained for a period of six months and the skid resistance monitored; a Griptester may be used, provided a correlation with SCRIM is available.
Treatment by removal of surface binder may be necessary. Surface texture measurements must be carried out to ensure adequate texture is always available for the traffic speed. CSS guidance has to take account of the fact that on many roads the binder film will not have worn off in six months and many local authorities do not want a plethora of signs on new surfacing. CSS draws attention to the fact that light gritting of the surface during installation, commonly used in Europe, can improve the early-life skid resistance. A number of authorities use this on approaches to junctions where a minimum IL of 0.45 is required. Some erect some form of warning sign.
Conclusions
Thin surfacings rightly dominate the market and achieve a high degree of customer acceptance. Selection of the appropriate treatment for a site should be based on an objective evaluation of factors such as skidding, cracking and resistance to rutting, as well as considerations relating to noise and texture depth. Some compromises may be necessary.
This paper was first published in The Asphalt Yearbook 2004 and is reproduced here by kind permission of The Institute of Asphalt Technology.