Moisture In Asphalt Production
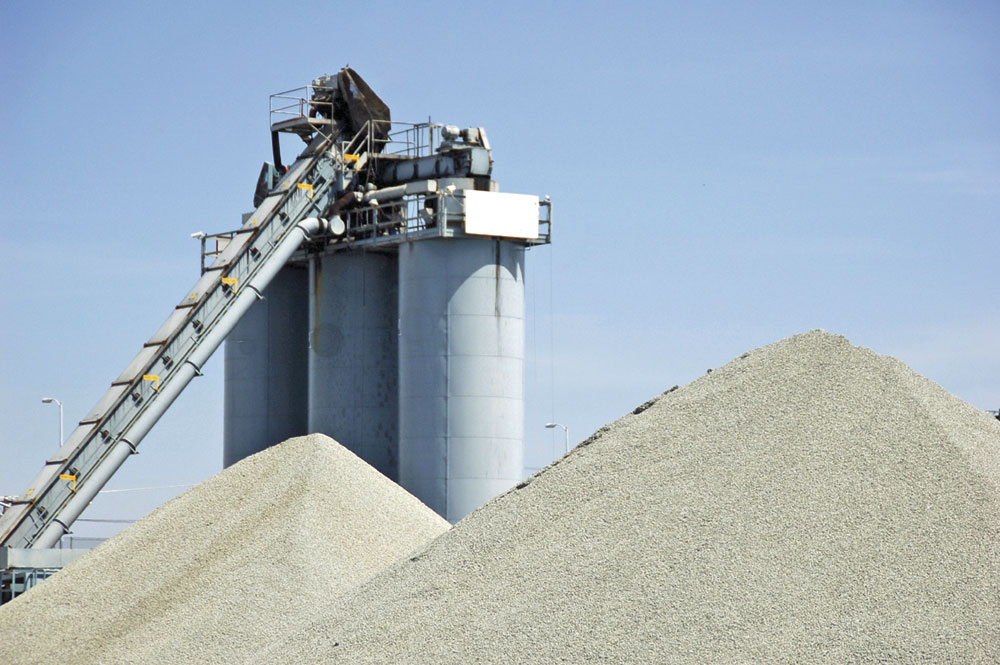
The importance of accurate moisture measurement and control
By David Serra, international sales manager with Hydronix Ltd
When a panel of industry quality-control experts was asked what automated measurements would add value to asphalt production, ‘moisture content on belts/in bins’ and ‘automatic gradation and moisture measurement from belt sampling’ came in the top three.
The increasing cost of raw materials and energy has made asphalt producers look into their production process in much greater detail than in the past. Proven in-line technologies are now available that can provide very real economic benefits and allow greater process control, thereby reducing costly on-site testing and off-line forms of control. The need for more exact process control is further reinforced by a move towards more plant/process certification. Instrumentation has become a major part in allowing asphalt producers to differentiate themselves from others through repeatable quality, reliability and efficiency. This differentiation and ‘getting it right first time’ can be the difference between winning a job and losing an important customer.
Increased quality control and assurance has also been reflected by developments in national standards. In France, the asphalt standards have recently been updated to require producers to measure moisture continuously for the production of Level 2 asphalt (NF P 98 728). In the US, NCAT (National Centre for Asphalt Technology) carried out an investigation into improving hot-mix asphalt (HMA) production technologies and in their conclusions recommended on-line belt-sampling of materials and moisture content compensation.
Sources of variation in moisture and their effects
Moisture contents can change in aggregates stored in cold-feed bins, in the RAP (if used) and in the finished HMA or other ‘warm’ asphalt. By measuring moisture in the incoming materials, the moisture content of the finished asphalt product can be controlled in a proactive, real-time manner.
A change in the moisture content of the raw materials due to rainfall or dry weather will have a very large impact on the grading of the aggregates being loaded into the dryer and, therefore, on the quality of the asphalt produced. It also changes the energy consumption of the dryer considerably and can result in under-yielding.
In practice, fine aggregates can hold considerably higher moisture contents than coarser gravels, and it has been found, therefore, that the greatest benefit in moisture measurement is usually achieved in aggregates with particle sizes less than 10mm. Field trials have proved that by using microwave moisture sensors, measurement accuracies of ±0.2% are achieved and that these more than exceed the industry requirement.
Batch plant operations
Uniform cold feeding of aggregates from cold bins is necessary for several reasons, and moisture affects all of these:
- Large moisture variations in the aggregates in the cold feed can lead to moisture content changes in the HMA.
- Moisture variations can lead to aggregates leaving the dryer at different temperatures. This can lead to incorrect temperatures of the materials in the pugmill or mixer.
- Moisture variations can cause the dryer to work inefficiently, over-drying already dry aggregate or outputting insufficiently dry material.
- Inconsistent feeding of aggregates from the cold bin can, in extreme cases, lead to differential feeding of the hot bins, resulting in some hot bins overfilling while others remain low on materials.
By measuring moisture using a sensor installed at the base of the cold bins or on the cold bin discharge belts, and integrating this measurement into a process control system, it is possible to achieve a real-time solution to the above issues. The benefits are:
- The ability to ensure that the correct grading of materials is discharged.
- The ability to adjust the dryer rate taking into account the moisture content of the aggregates being fed, resulting in energy savings.
- The correct aggregate temperature leading to optimum binder adhesion.
Continuous (drum) plant operations
In the production of asphalt by drum mixing, aggregate gradation is controlled at the cold feed and, therefore, ensuring the accuracy of the cold feed is essential. Installing moisture sensors at the belt weighers or at the base of the cold-feed bins allows real-time feed adjustment, ensuring that the correct dry weight of aggregates is loaded into the drum mixer, resulting in:
- Increased yield and reduced asphalt binder usage through correct aggregate gradation.
- The ability to adjust the burner rate to suit the moisture content of incoming materials, allowing efficiency monitoring.
- Energy savings (see section opposite on return on investment).
- Control of final HMA moisture content.
- Reduction in inadequate adhesion between asphalt binder and aggregates.
Warm asphalt operations – low-energy asphalt and foamed asphalts
Warm asphalt production techniques require a higher degree of accuracy in aggregate gradation to ensure asphalt quality comparable with other HMAs. The role of water is essential to achieve the desired ‘foaming’ effect when mixed with the bitumen, allowing the system to uniformly coat all the aggregates.
The introduction of moisture sensors into the process allows real-time and online moisture measurement of the aggregates before they are fed into the pugmill, mixer or drum. With a feed-forward automation system, producers can correct aggregate weights in real time. For techniques that use the water in the aggregates themselves for the foaming effect, information about the quantity of water being fed into the mixer or pugmill can also be ascertained.
Return on investment
It has been found that a 1% increase in moisture in one tonne of aggregate can result in an additional 0.6 litres of fuel being consumed to evaporate it. At 6% moisture, four litres of fuel are required to dry one tonne of aggregate. Once dry, three litres of fuel are required to heat the aggregate to 150°C, meaning that more energy is used in drying the aggregate than in heating it.
In practice, the dryer or drum’s exhaust temperatures are already measured and used for feeding back information into the burner control. However, on-line moisture measurement allows real-time dryer/drum adjustments relating to the material inside, not the material already discharged. This reduces the process control time lag and ensures that the correct dry weights are being loaded into the dryer, resulting in savings and quality improvements.
If a plant produces 300 tonnes of asphalt per hour at 6% moisture, it will be using 1,200 litres of fuel per hour to dry the aggregate before it is heated up to the correct temperature. If the moisture content then changed from 6% to 5% without the dryer being adjusted for 1h, that would equate to 180 litres of fuel being wasted in that 60min period. Were this to be the case, moisture-measurement equipment would pay for itself in approximately 30 production hours. A reduced process control time lag continuously improves the efficiency of the plant. In most cases, moisture measurement systems will pay back within the first three to six months of operation.
Moisture measurement can also be used to evaluate the dryer’s performance. Should the exhaust temperatures and incoming moistures not match (exhaust temperature increases with reducing moisture contents or vice-versa), there may be a requirement to tune the dryer.
There are other economic effects to moisture measurement. By knowing the correct moisture content in the aggregates, it is possible to maximize the efficiency of the drying process to reduce over-drying and wasted production time, thus increasing the yield of the plant. Customers using automated moisture measurement consistently report improved output rates.
Installation and commissioning of a moisture sensor
Digital moisture measurement sensors can be installed at the base of the cold-feed bins, on the feed belts or, alternatively, on a loading ‘plate’, as used by CETE (Centre D’Études Techniques de l’Équipement) in testing. In practice, it has been found that the first two positions are generally the easiest installation locations.
Typically, sensors take 25 readings per second, allowing them to measure changes in moisture immediately. Integration with the customer’s control system is simple, via the use of standard analogue outputs. Full digital communication with the control system is also available via RS485/RS232, and the latest asphalt plants are now using Ethernet adapters for communication with sensors.
Calibration consists of finding the linear correlation between the sensor’s ‘unscaled’ reading (always 0 in air and 100 in water, allowing easy sensor swap-out if required) and the moisture content in a particular aggregate. This is done by simply running material past the sensor’s face and taking a reading of the sensor’s unscaled value. A sample of the material is taken and then oven-dried to find its moisture content as per the applicable standard. Once the above procedure has been carried out for a few points over the moisture range of the aggregate, the sensor will accurately read moisture – online and in real time.
It pays to invest in moisture control
Moisture is clearly not the only issue that the asphalt producer has to contend with to ensure that quality-control requirements are met within tight economical constraints. However, it is a simple improvement that brings immediate, quantifiable returns. Accurate moisture measurement and control is now well established and has been proven to directly reduce costs as well as ensuring a consistent-quality product, thereby improving competitiveness.
Hydronix Ltd are specialists in microwave moisture measurement and have supplied over 50,000 digital microwave measurement units into aggregate-related applications. For more information, contact David Serra, international sales manager, on tel: +44 (0)1483 468900; or email: dserra@hydronix.com