Moisture Control in Asphalt Production
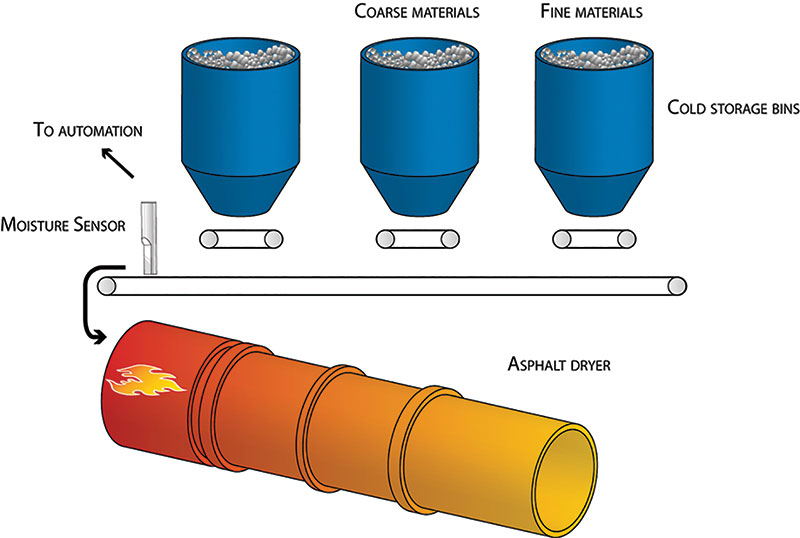
First published in the January 2015 issue of Quarry Management
Hydronix explain how moisture measurement and control reduces costs and ensures product quality
Hydronix have been experiencing increasing interest from North American asphalt producers seeking the addition of moisture control systems to their plants. This trend is continuing to spread across the world as highway agencies are demanding increased value for money and expecting suppliers to guarantee the longevity of their products.
The decision to include moisture measurement and control, or moisture compensation, can be split into two main areas – one is cost reduction and the other quality. These benefits are applicable to both batch- and continuous-type processes, but in quite different ways.
Cost reduction
Cost-reduction benefits for batch-type operations are mainly gained by optimizing the drying cycle of the materials. A number of batch process plants in the US have seen benefits from installing a very simple system utilizing one sensor to measure moisture in the blended material ahead of the dryer. This is used for burner control and for manual adjustment of the feed rates. If the moisture increases, the fine material is fed slightly faster to ensure that the bins are evenly filled for each of the aggregate sizes.
For continuous plants the cost benefit is primarily derived from ensuring that the correct amount of binder, including additives, is used to make the desired volume of finished product. Once properly interfaced to the plant control system, it is possible to automatically control the amount of binder by measuring the moisture of the materials on the cold-feed belt and adjusting the belt speed to ensure that the varying grades of materials are delivered in the correct quantities (ratios) into the burner. The wetter the material, the faster the belt must run to deliver the correct amount and maintain consistent material ratios, and vice versa. Product yield is, therefore, maximized for the amount of asphalt cement used, thus greatly reducing the amount of excess binder needed in the process. Cost savings can immediately be seen in the reduced amount of binders and additives required. In a continuous system, a sensor would be installed underneath both the coarse and fine material bins to ensure the correct blend of materials is delivered to the burner.
Hydronix sensors will reliably give moisture results to ±0.2%, and customers have quoted potential material savings as high as US$45,000 on a single 100,000-tonne production run, if they are able to continually control and adjust for moisture to this level of accuracy. As with the batch process, if the dry materials are kept constant, a correlation between the moisture level of the material and the energy required to dry the material may be made and, hence, the efficiency of the burner monitored. There are two reasons why a burner would require more energy to achieve the same moisture target; the first is that the starting moisture level was higher, the second is that the burner has become inefficient and requires a service (it may even be cost-effective to replace the existing unit altogether with the latest technology). The exact efficiency of the burner can now be monitored.
Quality
The drive for quality, particularly in the US, has largely been a result of specifiers requesting that producers be ‘bonded’. This is a term used to describe the agreement between the producer and the customer to guarantee the asphalt product for a period of up to 15 years. Previously only the suppliers of concrete roads were bonded in such a manner. However, the practice of contracting the supplier with stricter terms is becoming more widespread as highway agencies are increasingly considering the entire life-cycle cost and looking for long-term value. The outcome of this is that greater demands are placed on the supplier to ‘guarantee’ product quality and indemnify the highway agency against ongoing maintenance costs.
Measuring the moisture of the materials during production not only ensures that the maximum yield may be achieved but can also highlight problems upstream with material suppliers or storage. Additional moisture in the material increases the weight, so the producer will purchase less material when buying by weight, or require additional energy to dry the material if it is poorly stored. Perhaps more critically, moisture measurement ensures that the ratios of the materials are maintained exactly as the design stipulates. This ensures consistent product density, which is a critical ingredient in determining the quality and durability of any asphalt product.
While some highway agencies stipulate that moisture is controlled during production, others often ‘bond’ their supplier, leaving it up to the supplier’s self-motivation to produce to the highest-possible specification. With the stakes rising for producers, with the cost implications of poor quality, many are now looking to retrofit moisture-control systems to existing plants. This leaves an opportunity for forward-thinking and innovative suppliers of asphalt plant automation and machinery to bring to market new solutions for their customers, to ensure peace of mind as each project is completed.
Moisture control is clearly not the only issue that asphalt producers have to contend with to ensure they meet quality-control requirements within tight economic constraints. It is, however, a simple improvement that can bring immediate quantifiable returns. Accurate moisture measurement and control is now well established and has been proven to directly reduce costs, ensure consistent quality product and improve competitiveness. Hydronix, who design and develop proven digital microwave moisture sensors, work closely with OEM and automation companies to integrate this technology seamlessly into their products.
For further information visit: www.hydronix.com
- Subscribe to Quarry Management, the monthly journal for the mineral products industry, to read articles before they appear on Agg-Net