Making the Case for Rubber Roads
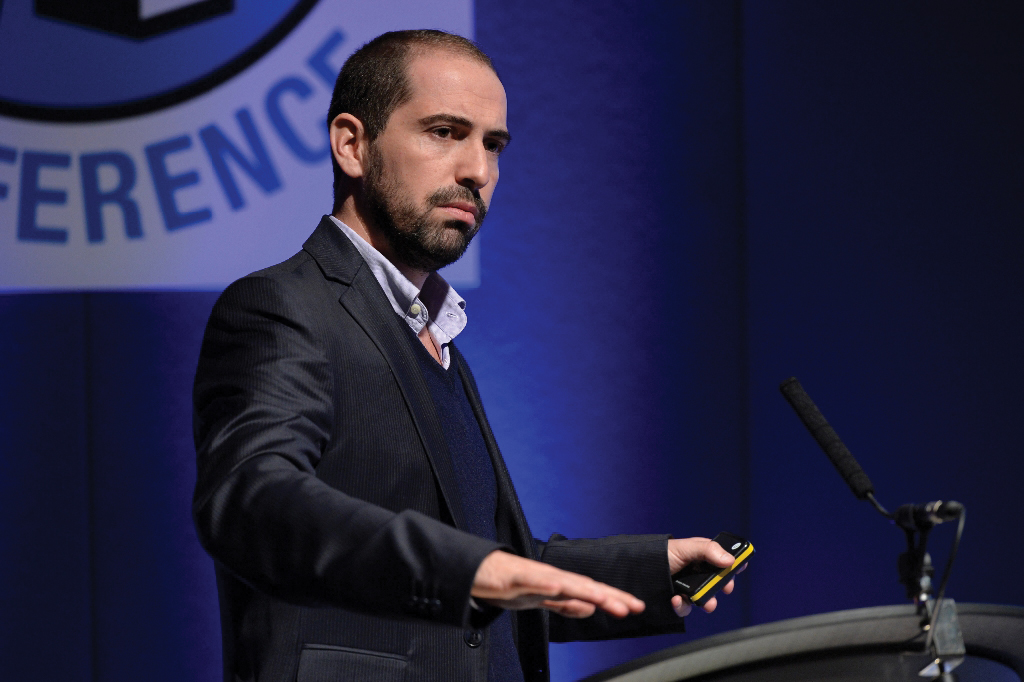
First published in the January 2018 issue of Quarry Management
Rubberized asphalt could help in the disposal of waste tyres (which are banned from landfills in the EU) and in reducing levels of noise pollution, so why is there not more widespread use in the UK? Dr Davide Lo Presti from the Nottingham Transportation Engineering Centre (NTEC) outlines the case for rubber roads.
Rubber roads have long been presented as a solution to the issues of waste tyres and noise pollution, yet despite their popularity in the US, China and, more recently, Malaysia, the trend has seen limited take-up in the UK.
Now, Dr Davide Lo Presti from the Nottingham Transportation Engineering Centre (NTEC), at the University of Nottingham, is calling for the Government and the tyre industry to offer incentives to encourage manufacturers and suppliers of construction and building materials to scale up the reuse end-of-life tyres (ELTs) in civil engineering applications, particularly to build roads.
‘Pavement engineers already have solutions to decrease the noise produced by road traffic. This comes from using ‘quiet pavements’ as surface courses,’ said Dr Lo Presti. ‘These technologies provide an improved level of safety, even in wet conditions, and it is possible to manufacture them by reusing ELTs. Incorporating ELTs in asphalt not only makes the surface courses quieter and smoother, it also creates a more flexible pavement with a longer lifespan.’
Dr Lo Presti has long advocated the use of recycled tyre rubber as an alternative material to build roads given its resilience and ability to be reused in other products. ‘Our research shows that ‘rubberized asphalt’, which consists of regular asphalt incorporating ‘crumb rubber’, bears significantly improved engineering properties over asphalt mixes made with conventional paving-grade bitumen. It also performs as well in asphalt mixes that incorporate synthetic polymers,’ he said.
‘In addition, when it is properly engineered, rubberized asphalt offers specific benefits that make the roads even better. These are:
- Reduced noise – incorporating rubber crumbs into the formulation creates porous asphalt that does not require the use of fibres. This will lead to an appreciable reduction in traffic noise due also to the fact that rubber crumbs dissipate vibrations.
- Roads remain black – better long-term colour contrast in pavement markings enhances safety (carbon black in the rubber acts as a pigment that retains the roads’ dark colouring for longer).
- Enabling the circular economy – using the vast amount of ELTs to build roads saves energy and natural resources, and also creates an end-of-life solution.
‘Despite the success of trials on rubberized asphalt, at present there is little industrial development and use of recycled tyre rubber (RTR) in the UK. This can be attributed to a lack of information, insufficient training of staff and stakeholders, and poor support of local policies.
‘The tyre industry recently created a forum for stakeholders to share their views and this was a great first step. If it was developed further, it could bring about some positive change. The lack of policies and product specifications has limited the widespread use of rubberized asphalt. However, reusing ELTs to build roads is a successful example of an end-of-life solution for the tyre industry. For this reason, the tyre industry should also act independently and recognize its responsibility in the process,’ said Dr Lo Presti.
Barriers to widespread adoption
Dr Lo Presti’s research has shown that the most successful technologies linked with incorporating recycled tyre rubber in asphalt mixes are based on modifying the bituminous binders with this recycled polymer to produce recycled tyre rubber modified bitumens (RTR-MBs).
These better-performing binders are produced in a process that requires continuous agitation with special equipment to keep the RTR particles uniformly distributed. Phase separation, where the RTR sinks to the bottom during storage, is one issue that manufacturers have to contend with. In addition, rubberized asphalt needs to be handled by trained personnel who are familiar with the laying and compaction process due to the mixture’s reduced workability. Contractors in the UK and EU do not normally practise this particular method, so the adoption of this technology would need up-front costs from contractors and specialized training for the workers.
Moreover, rubberized asphalt mixtures cost more than conventional asphalt, mainly because the related benefits are linked to the need for a larger amount of this type of costly bitumen.
‘NTEC’s research has led to several solutions. These include modifying the binder by combining it with other polymers, reducing storage temperatures and using waxes to reduce operating temperatures, among other measures,’ said Dr Lo Presti.
‘These solutions work in principle, but when set in the larger industrial context they are usually not economically viable in the short term. However, the evidence shows that in the long term they are a more economically and environmentally sustainable solution. For this reason, further intersectoral collaboration between academia and industry is needed to enhance the transfer of knowledge in order to devise solutions for widespread application.
‘Crumb rubber can be successfully incorporated into asphalt mixtures to create innovative mix designs, and these are now being used in the EU. These technologies are known as the ‘dry’ or ‘semi-wet’ process and do not require adaptations to asphalt plants. However, they are still not considered a viable option when it comes to building roads.’
Fuel for thought
The only really successful applications of rubberized asphalt in road pavements occur when governments, supported by research centres, work to exploit these technologies.
The state of California, for instance, has had a government mandate in place since 2005 that supports increasing the adoption of these technologies. From 2013, the use of rubberized asphalt pavements had to rise to at least 35% of the total weight of asphalt paving materials produced in the state. This level recently rose even further to 50%, due mainly to predicted substantial savings in the long term.
Dr Lo Presti commented: ‘I believe that the widespread use of rubberized asphalt technologies is a sustainable practice that should be supported in the UK. There is much evidence that rubberized asphalt works, and if it can be introduced on a wider scale it offers a readily available solution to reuse large amounts of waste tyres.
‘Offering tax benefits to companies that recycle waste is a viable option. Another approach involves supporting collaborative academia and industry research to solve technical issues in order to make this application more economically and commercially viable. This should be led by policymakers and supported by the tyre industry, to create initiatives to open this particular market.’
Investing in research and supporting the industry are ways in which it is possible to address environmental issues instead of resorting to burning and exporting waste tyres. While these practices may be economically convenient, they most certainly contribute to higher global emissions and, worse still, delay a viable and tangible solution.
- Subscribe to Quarry Management, the monthly journal for the mineral products industry, to read articles before they appear on Agg-Net.com