Eurovia Roadstone resurface Port of Felixstowe access road
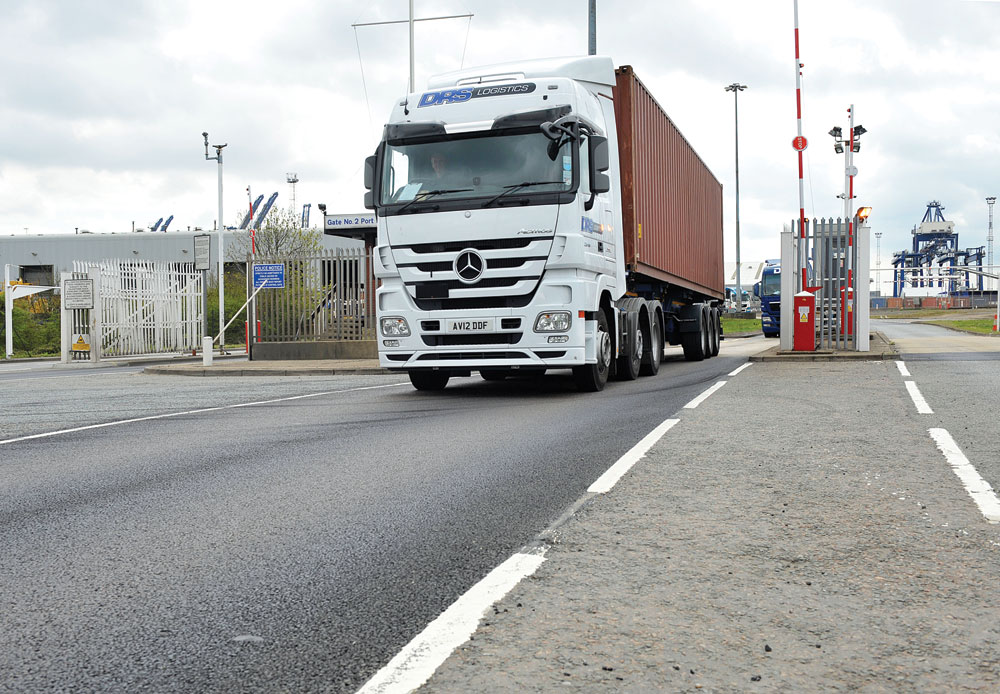
First published in the September 2013 issue of Quarry Management as Smoothing the Flow
UL-M thin surfacing from Eurovia helps keep traffic rolling in and out of Britain’s biggest and busiest port
The Port of Felixstowe is not just Britain’s biggest and busiest port, it also boasts the best connections. Shipping lines operating from the port – which is the main hub of the ‘Haven area’ that includes Harwich and Ipswich – serve 365 ports around the world. And on terra firma, Felixstowe is just as well situated to distribute goods throughout the country. Some 70% of the containers coming through the port are delivered to the ‘Golden Triangle’ – an area in the middle of Britain where the high street brands and online retailers have their national distribution centres – only a short haul away.
Although the port has developed good rail links, the bulk of the 3 million-plus container units it handles travel through the port gates by road. The toll from the many thousands of trucks beating a path along the access road to this import and export hub is also, inevitably, heavy.
Over the years the Port Authority’s engineers have specified a range of materials to combat the problem of deformation. The materials used have ranged from traditional hot-rolled asphalt (HRA) to advanced thin-surfacing materials, but until now, those efforts have met with limited success.
The biggest issue has been the rutting of the pavement. Trucks passing through the gates of the port use a two-way, two-lane access road. Unlike on a motorway where there is a mix of vehicles and choice of lanes, the unrelenting ‘channelized’ flow to and from the port is of heavy goods vehicles that barely deviate from the same track. Ploughing the same furrows, their wheels accelerate wear on the road surface, leading to ruts, cracking and further damage as the weather elements go to work beneath the rapidly deteriorating surface.
The civil engineering team at Felixstowe, and their contractors, R W Hill (Felixstowe) Ltd and Waveney Surfacing, had already decided to use a thin surfacing with a polymer-modified bitumen when they approached asphalt suppliers Eurovia Roadstone. Both the contractors have been associated with maintenance of the Port of Felixstowe’s infrastructure for over three decades and have been supplied by Eurovia for more than 24 years.
‘Several solutions were considered but the nature of the site and the type of traffic involved meant that UL-M would be the most resilient for this application,’ explained David Jones, technical and systems manager with Eurovia Roadstone.
UL-M has a proven international track record (see UL-M facts box) but Mr Jones could also point to a similar application closer to home. Lanes one and two of the Queen Elizabeth II Bridge were resurfaced with UL-M more than five years ago, when the Thames crossing was operated by the Eurovia Group’s joint venture, Le Crossing. This surfacing is still bearing up well under the daily onslaught (more than 140,000 vehicles use the M25’s Dartford–Thurrock crossing each day) and it is believed to be the longest life cycle yet for the toll booth sections.
Resurfacing of the port’s access road was postponed twice due to adverse weather before going ahead on Saturday 20 April 2013. Waveney’s team planed off the old, failing surface to a depth of 40–50mm for the UL-M course. During production of the 116 tonnes of material, samples were tested at Eurovia’s Ipswich laboratory to ensure it conformed to the design mix. On site in Felixstowe, Eurovia Roadstone’s technician carried out an audit of the laying process, ensuring the material was installed to the system’s specific guidelines, an integral part of which is the use of a bond coat. This provides an excellent bond to the underlying substrate while also providing waterproofing, ensuring a greater service life from the whole pavement.
‘The whole operation went exceptionally well,’ said John Murphy, contracts manager of Waveney Surfacing. ‘The material supplied and the co-operation from the plant were first-class, and the attention of Eurovia Roadstone’s materials technician also played such an important part in the successful completion of the contract.’
With Felixstowe aiming to double its capacity by 2030, the toll of traffic on the access road can only get heavier and the port’s infrastructure – like its link to the British road network – will have to bear the burden of this growing trade.
Felixstowe facts
- Receives more than 4,000 ships each year
- Handles more than 3.4 million TEUs (20ft equivalent units)
- Its 33 shipping lines offer 90 services to and from 365 world ports
- Can accommodate the world’s largest container vessels.
The port is owned and operated by Hutchison Ports UK, a member of the Hutchison Port Holdings Group, which is a subsidiary of Hutchison Whampoa Ltd (HWL), the Hong Kong-based multinational conglomerate. HWL claim to be the largest foreign investor in the UK.
UL-M facts
Developed in France during the 1980s, UL-M was the first conventionally installed thin-surfacing system to be introduced to the UK.
UL-M utilizes high-performance polymer-modified bitumen, which has high cohesion, low thermal sensitivity and excellent resistance to aging. Different degrees of modification make it possible to adapt the choice of binder to the performance requirements, nature and characteristics of the substrate, traffic loading and weather conditions.
HAPAS-approved, the UL-M thin-surfacing system has been proven worldwide, with more than 100 million m2 laid around the world, of which some 20 million m2 are within the UK – mainly on motorways and urban roads, including notable locations such as London’s Park Lane, Victoria Embankment and Tower Hill.
UL-M can be specified with aggregates of varying sizes (6mm, 10mm and 14mm) and laid to thicknesses of 15–50mm.
- Subscribe to Quarry Management, the monthly journal for the mineral products industry, to read articles before they appear on Agg-Net