Astec Launch New Asphalt Dryer/Drum Mixer
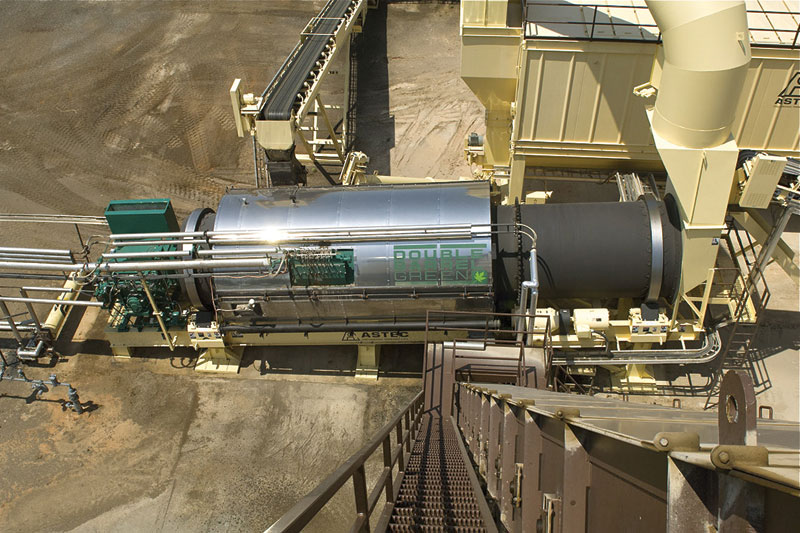
First published in the January 2014 issue of Quarry Management as Astec launch new Double Barrel HR
The Double Barrel dryer/drum mixer combines the functions of a dryer and a continuous-process mixer in a single compact and efficient system. Drying of the virgin aggregate takes place in the inner drum, followed by mixing of the aggregate and other ingredients in the outer stationary shell
Astec have recently launched the new Double Barrel HR dryer/drum mixer, which facilitates the mixing of higher levels of recycled asphalt planings (RAP) and virgin aggregate in a specially designed double barrel that also encompasses the mixing of the RAP/virgin mixture with bitumen and additives in an external twin-shaft synchronous mixer.
The benefits of the Double Barrel HR include the ability to incorporate 60%+ RAP at 5% RAP moisture, or 70% RAP at 3% RAP moisture.
Process mixing
The Double Barrel features state-of-the-art V-PAC drying technology, which includes variable-frequency drive, V-flights, exhaust temperature control and optional WMA system.
Virgin material enters the dryer and is dried in the inner drum within 160–200 seconds. Just beneath the burner cone, the virgin material drops out of the dryer into the mixing chamber where the RAP is added. The virgin aggregate and RAP are gently and thoroughly mixed over a period of 60–87 seconds. As the RAP is introduced, there is a continuous release of steam as the RAP is heated. This is one of the keys to the success of the Double Barrel as a processor of RAP; the steam that is produced blankets the superheated virgin aggregate and RAP displacing the oxygen and resulting in less oxidation.
Fines are introduced further along the mixing chamber where they are incorporated into the mix over a period of 45–60 seconds.
External mixer
The pre-mixed virgin aggregate/RAP/fines blend then enters the external twin-shaft synchronous mixer where it is vigorously mixed with bitumen.
The external mixer provides many benefits, allowing the addition and mixing of additives. It provides product flexibility, eg production of emulsion mixes, coloured mixes, and ‘cold mix’ with optional components; and it also provides process flexibility, eg allows for additional mix time and anticipation/control of process temperature excursions.
Due to the virgin material temperatures required for high-percentage RAP addition, as an additional process safety measure, a temperature-suppression system, which blankets both mixing chambers with inert gas (steam), can be fitted.
Double Barrel HR drum features
V-PAC stack temperature control (patent pending)
- Provides positive control of bag-house temperature
- Enables running of mixes ranging from virgin WMA to high-percentage RAP and open grades without flight changes.
External synchronous twin-shaft mixer
- Allows for greater separation of bitumen from hot virgin aggregate
- Allows for even longer mixing of hot virgin aggregate/RAP in mixing chamber.
Combustion zone drum enhancements
- Shell material change allows for higher temperatures at high-percentage RAP
- Flight material change allows for higher temperatures at high-percentage RAP
- Flight design change eliminates shell wear and protects shell from radiation.
The stainless steel drum shell allows higher temperatures when running high-percentage RAP. The stainless steel combustion flight incorporates a special flight design which eliminates drum shell wear, protects the drum shell from radiation and maximizes radiation input to the virgin aggregate.
Patented Astec WMA system (part of V-PAC)
- Enhanced mix compaction and temperature reduction with no additives.
What is V-PAC stack temperature control?
Incorporating the unique Astec V-flight, a variable-frequency drum drive (VFD) is utilized to balance the drum exhaust temperature. VFD allows the operator to control veil density by changing the drum’s rotational speed. Stack and mix temperatures can be controlled by increasing or decreasing the drum speed. An increase in speed will decrease stack temperature, and a decrease in speed will increase stack temperature. A feedback drum-speed control is also specified to hold stack temperature steady.
Why V-Flights?
The Astec V-flight has a v-shaped notch that allows the flight to more evenly veil at both high and low tonnage rates. The flight is taller than ordinary flights so that the entire flight carries a similar amount of material when completely full. Higher RAP percentages result in lower tonnages through the drying zone, causing flights to only partially fill. V-flights allow veiling over a wider range of tonnages.
Available in the UK
In the UK, BG Europa (UK) Ltd have retained strong links with Astec Inc., co-ordinating with them to promote their range of equipment in the UK and holding stocks of genuine Astec parts.
BG Europa (UK) Ltd were established in 1988 from the Barber Greene England company following their acquisition by Astec. Technology and expertise existing within Barber Greene at that time was incorporated within BG Europa (UK) Ltd, and this expertise has been utilized to develop equipment that integrates new technologies whilst retaining the traditional quality and dependability of Barber Greene.
For further information visit: www.bgeuropa.co.uk
- Subscribe to Quarry Management, the monthly journal for the mineral products industry, to read articles before they appear on Agg-Net