Asphalt Recycling
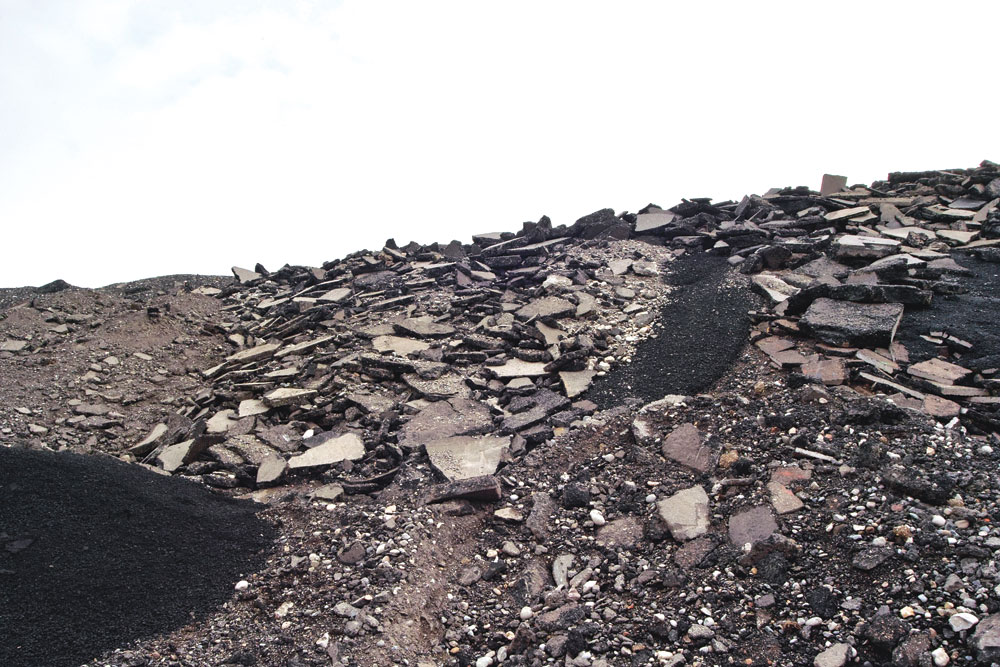
Ammann look to the future with 100% RAP recycling
Every 10 to 20 years or so asphalt road surfaces require either partial or full replacement, due to the effects of ageing, damage or increased traffic loads. The used asphalt obtained during these repairs is often disposed of or used as a supporting layer in new road building. However, more often than not the reclaimed aggregate and bitumen components are still in good condition and can be recovered and reused if the correct technology is accurately applied.
Three of the main arguments for recycling are: preservation of precious aggregate/bitumen resources; minimization of transportation, ie cost savings and reductions in traffic volumes, environmental impacts etc; and avoidance of environmental load, ie reduced waste material, less need for landfill space etc.
The asphalt producing industry and the relevant authorities must, therefore, find solutions and incentives to encourage recycling, and establish a better acceptance of mixes that include recycled material.
Table 1 shows the amount of asphalt recycling in a number of European countries. The Netherlands is considered to be the country with the most expertise in this field. This can be explained by the fact that the country does not possess its own aggregates and, therefore, has to import materials. Germany, Italy and Switzerland have a significant number of asphalt plants with good recycling facilities, and the amount of recycling has increased in these countries during the past few years, while France is about to embark upon asphalt recycling. In contrast, as a strong primary aggregate supplier, the UK has not had the same incentive to invest in asphalt recycling and, as yet, is not a fully integrated recycling market, but this will continue to develop in the future, driven by rising oil prices and environmental issues.
There are four main ways of handling/recycling recuperated asphalt:
- Reclaimed materials are thrown away at a waste disposal site, which results in a loss of aggregates and bitumen.
- Reclaimed materials are crushed and reused as gravel substitute, which results in a loss of bitumen.
- Reclaimed material can be recycled on site. This requires special machinery, can be problematic in practice and is only useful in restricted circumstances.
- Reclaimed materials can be crushed and reused in asphalt plants. This solution has gained worldwide acceptance and is the most common technique. The quality of mixes has been proven to be as good as totally new mixes and they are capable of meeting the same standards.
The process of recycling in asphalt plants is well established and several alternatives are available, depending on the desired amount of recycled material in the mix. Ammann, who offer a comprehensive range of recycling equipment, from new plants to retrofit solutions, and have more than 800 recycling installations in operation around the world, claim to have taken a lead in the industry with their new recycling drum (fig. 1).
Unlike the company’s conventional parallel drum, which can utilize up to 60% reclaimed asphalt planings (RAP), Ammann say the new drum takes asphalt recycling a step further, thanks to a new recycled hot-air system, making it possible to process 100% recycled road planings at high output rates (up to 240 tonnes/h) and at temperatures of around 160°C, while at the same time meeting emission limits.
With Ammann’s standard parallel drum system (fig. 2), heat from the burner flame is used to heat the RAP, which means the flame is in direct contact with the recycled material. This can be problematic if not controlled correctly, as the flame has the potential to damage the bitumen binder.
However, the new drum uses a special process air system, which takes super-heated air and cools it to a modest 650°C before reintroducing it back into the recycling drum. According to Ammann, the recycling drum looks similar to a conventional parallel drum, but its new combustion unit is the first of its type, several of which are now in operation producing up to 240 tonnes/h of 100% recycled asphalt.
With more than 500 million tonnes of RAP produced around the world each year, Ammann believe the new drum will help meet the growing market demands for the recycling and reuse of valuable aggregate and bitumen resources in an environmentally friendly and cost-efficient way, without any loss of production capacity.