Adding RAP – a hot topic in the asphalt industry
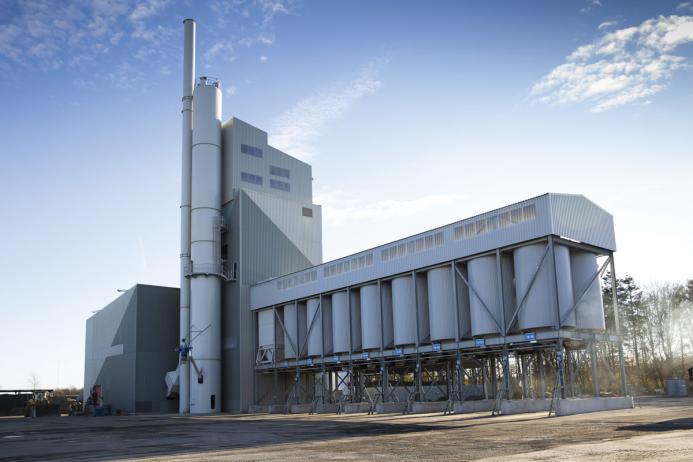
First published in the January 2024 issue of Quarry Management
KVM explain how the recycling of asphalt is the most effective way to go green and create a circular economy
KVM have a long tradition of working in partnership with their customers to create innovation within the production of asphalt. One of the key areas is the adding of recovered asphalt pavement (RAP) during production. The recycling of asphalt is the most effective way to go green and create a circular economy in an industry that is under more pressure than ever from high fuel prices and other raw material costs.
Recycling of asphalt saves the Earth’s limited resources and means that we avoid the energy-intensive processes that virgin materials must undergo before they can be used in asphalt production. The goal of achieving higher levels of recycling, therefore, makes good sense for the entire industry.
KVM can provide a number of solutions for customers when it comes to deciding on their requirements for recycling in their new asphalt plants, whether this be addition into the mixer box, into the dryer drum, or a combination of both to provide maximum opportunity. However, in addition to being able to include these within their newest production options, KVM also have the ability to retrofit systems into existing equipment so that pre-existing sites can benefit from the latest solutions.
Adding cold RAP to the mixer
The obvious method for a medium-sized asphalt plant is to add cold RAP to the mixer. The investment in the necessary equipment is moderate and the benefits of reusing the asphalt ensure a quick payback time.
Over many years, KVM have gained experience and developed the concept with a particular focus on large RAP volumes and efficient extraction of vapour. The equipment has exceptional flexibility when switching between the different recycling fractions and is particularly suitable for fractions with a high bitumen content. The design of the weighing belt means that the material is constantly kept in motion to prevent the recycled material from accumulating and interfering with the machinery. At the same time, high weighing accuracy is ensured when weighing each batch.
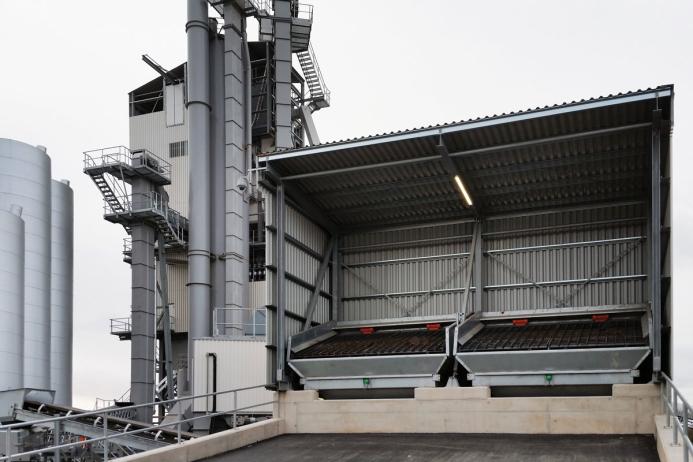
The method of RAP addition using a weighing belt is often combined with a drying drum equipped with a RAP ring. In this way, the two different methods can be used simultaneously, thereby increasing the total amount of RAP added. The advanced AMC (Asphalt Manufacturing Control) controller from KVM is specifically designed for fully variable addition using the two methods with precise compensation of bitumen content and penetration according to the RAP percentage.
KVM have recently delivered these systems to customers in Scandinavia and Germany. Two Norwegian examples illustrate the different conditions where KVM delivered a solution for RAP: Retro fitting of RAP equipment to an existing KVM Freja plant in Mo i Rana and a similar delivery to a third-party plant in Ballanger, where many details had to be determined in advance. This canlution was assembled from standard KVM components and then set up by KVM installers.
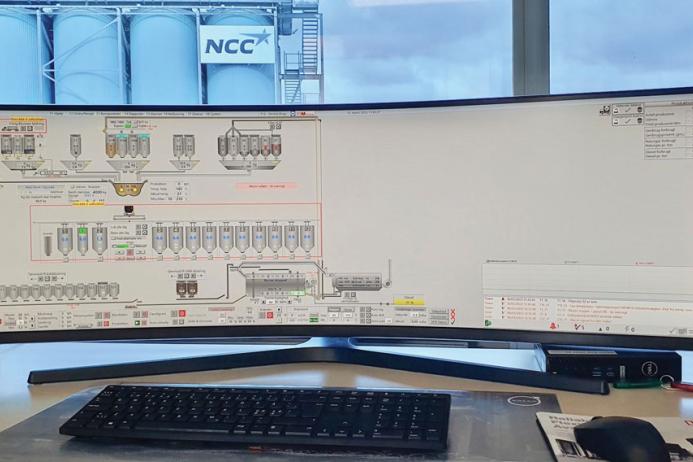
Increased RAP addition with new AMC control
In the summer of 2023, KVM upgraded NCC’s plant in Kolding, Denmark, with the implementation of a new KVM RAP drying drum and feed hoppers. In combination with the existing addition of RAP in the mixer, this allows RAP to be added to both the mixer and the dryer drum simultaneously, increasing the RAP content without compromising the quality of the finished product.
At the same time, the plant’s control system was replaced with KVM AMC. The AMC controller is very flexible and scalable, and the existing hardware in the control panels could therefore be reused for the new software. Only the Windows server was replaced. The new 49in monitor provides an unparalleled overview and ensures simple and easy operation for the operator. All RAP dosages can be adjusted seamlessly during production. This provides maximum flexibility and the ability to optimize the addition of RAP according to the weather conditions. The AMC controller’s RAP algorithm allows for automatic correction of bitumen, filler, and cold dosing, so that the stone skeleton, bitumen percentage, and hardness remain intact.
The RAP dryer drum is equipped with KVM’s patented four-point temperature sensor system, which provides a unique insight into the temperature development through the drum. In combination with the AMC, it provides fast and efficient temperature control. A variable drum speed also allows the operator to optimize energy consumption in the drying process.
Customized software solution
The AMC control makes it easy to add the features the customer wants. In this case, the contents of the hot storage silos are displayed in a web browser so that the staff serving the customers at the weighbridge always know how much asphalt is ready for collection and from which silo the drivers should collect it.
The burner was remodelled and adapted to the new dryer drum, so it was natural to replace the old burner control. The new TÜV-approved automatic burner control system provides an improved ability to ensure optimal combustion throughout the burner’s entire performance range.
The new CMS burner controller is connected to the AMC controller, so that all status information is available to the operator. At the same time, KVM’s service engineers can quickly and efficiently help with troubleshooting.
Subscribe to Quarry Management, the monthly journal for the mineral products industry, to read articles before they appear on Agg-Net.com