A Grand Prix Finish
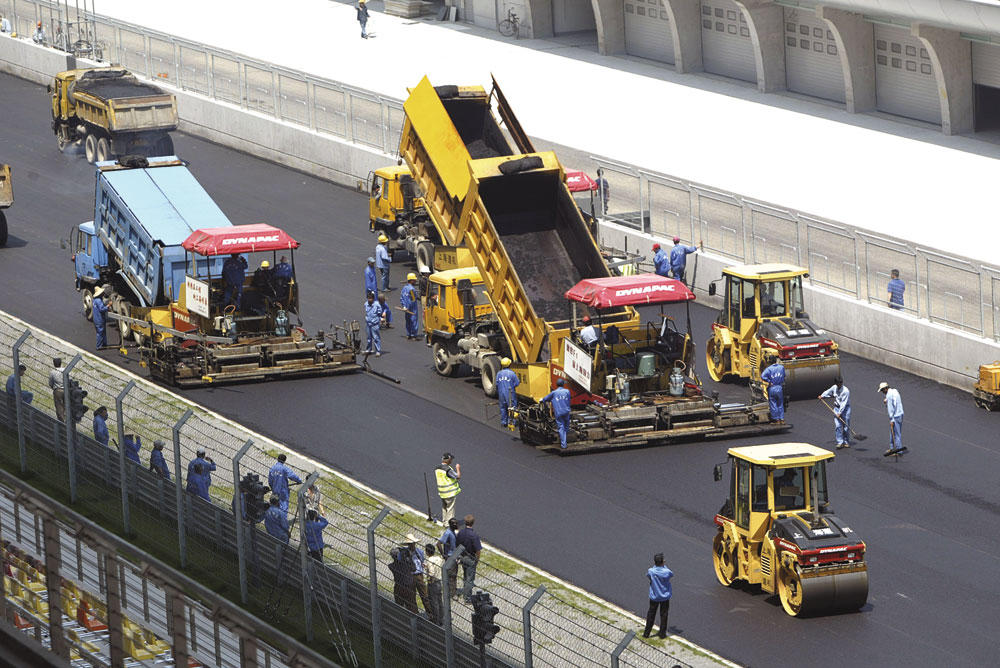
Dynapac help finish the Shanghai Formula 1 racing circuit
Dynapac equipment was used to help finish Shanghai’s exciting new F1 racing circuit. With an overall length of 5.5km, incorporating seven left and seven right turns, and standard widths ranging from 13m to 20m, Dynapac machines handled some 75,000 tonnes of material to complete the circuit’s paving and compaction work.
The circuit
On top of a 40cm road base of crushed aggregates, the circuit comprises a total of three layers of asphalt. The lowest is a 10cm thick asphalt basecourse, the middle layer is made of a 4cm thick binder course and the top wearing course layer is a polymer-modified bitumen with a combination of fine and coarse aggregates and a mineral filler.
The polymer-modified bitumen is used in accordance with specifications set up by the FIA (Fédération Internationale de l’Automobil) and provides an even surface with good grip, smoothness and durability, while withstanding extreme impacts and high temperature deformation. With speeds reaching 320km/h, constant acceleration/braking and corner taking, the stress on the track’s surface is extreme and far above that of ordinary roads.
The circuit was designed by Herman Tilke GmbH of Germany, who were also responsible for the Sepang track in Malaysia and the new circuit in Bahrain. The contractors were Shanghai Road Construction Co. and it was due to the close co-operation between the design company, contractors and equipment suppliers, such as Dynapac, that the entire project was brought to a successful completion.
Surface evenness
In Formula 1 racing a segregated asphalt is totally unacceptable as the top layer must be absolutely even. Dynapac therefore suggested that the contractors used four F141C tracked pavers with extended-drive drive units at the outer ends of the auger. The auger’s function is to distribute the asphalt mix as evenly and as continuously as possible in front of the screed.
With the extended-drive system there is no obstacle to the free flow of material as the drives are placed at the auger ends instead of in the middle of the stream of material. This gives the screed an optimum operating condition, resulting in a top asphalt layer without material segregation and a better pre-compaction. The screed was hydraulically extended to its maximum width and achieved 89% of screed pre-compaction measured with a nuclear gauge. Surface structure and evenness were better than 2mm measured over 4m.
The Dynapac F141C paver features a flow-through capacity of 750 tonnes/h and a hopper capacity of 5.7m3. It ensures a maximum paving width of up to 9.0m and a maximum laying thickness of 300mm. All four pavers were fitted with Dynapac’s VB 1105 TV (tamper and vibration) screed.
Roller types
For the 10cm asphalt base-course, using a 0–35mm aggregate mix, the Dynapac rollers were able to achieve a 98% density in just eight passes. Similar passes and compaction densities were also achieved for the 4cm binder with a 0–16mm aggregate mix.
For the 4cm wearing course, a polymer-modified bitumen top layer with a SPS content greater than 5% (ASTM D5, 0–13mm aggregate mix) was used, together with granite aggregates with a PSV of 66 to match the colour and hardness specified — key factors stipulated by the FIA. The choice of binder ensured a ‘softening point’ above 75ºC to ensure durability under the region’s high ambient temperatures.
Dynapac CC 322 and CC 232 hydrostatically-driven tandem rollers were used. These rollers can initially be set on a high-amplitude/low-frequency mode to complete the compaction of the upper part of the thick layers and compact the overlaying wearing course. The rollers are then switched to a low-amplitude/high-frequency setting to complete the compaction of the upper part of the thicker layers, and to compact the final overlaying wearing course. This technique eliminates the tendency to over-compact the thinner layers.
Generally, only the CC 322 rollers were used for compacting the wearing course working in the low-amplitude mode. The CC 232 rollers were used on the tight bends with the advantage of their split drums avoiding any tears in the mat.
A 95% degree of compaction was achieved in four passes in the low-amplitude mode with a high-frequency setting, followed by another six to eight passes to reach the stipulated degree of compaction, set at 99%. The compaction was constantly monitored with the help of nuclear density gauges.
Throughout the laying of all three asphalt courses, the rollers worked over a minimum pass length of 50m with cooling times ranging from approximately 40min on the basecourse to 11–12min on the wearing course.
According to Shanghai Road Construction, while cold jointing was permitted on the base asphalt course, it was unacceptable to the FIA on the wearing course.
FIA approval
Throughout the paving work, Shanghai Road Construction generally used two or three Dynapac trains led by the F141C pavers. For the shortest U-bends, however, asphalting was undertaken using all four pavers. This allowed them to achieve the specified high-quality finish across the track width by staggering the pavers over the extremely tight curve.
By mid-May the contractors had completed paving all the connection roads and the circuit’s first asphalt course. The binder and wearing course were completed before the end of the month, paving up to 2,100 tonnes/day.
The wearing course was approved by the FIA on 3 June 2004 for Formula 1 racing and the first Grand Prix took place on 26 September.
Dynapac Ltd, Parkfield Road, Rugby, Warks CV21 1QJ; tel: (01788) 532107; fax: (01788) 541195; website: www.dynapac.com
Dynapac equipment was used to help finish Shanghai’s exciting new F1 racing circuit. With an overall length of 5.5km, incorporating seven left and seven right turns, and standard widths ranging from 13m to 20m, Dynapac machines handled some 75,000 tonnes of material to complete the circuit’s paving and compaction work.
The circuit
On top of a 40cm road base of crushed aggregates, the circuit comprises a total of three layers of asphalt. The lowest is a 10cm thick asphalt basecourse, the middle layer is made of a 4cm thick binder course and the top wearing course layer is a polymer-modified bitumen with a combination of fine and coarse aggregates and a mineral filler.
The polymer-modified bitumen is used in accordance with specifications set up by the FIA (Fédération Internationale de l’Automobil) and provides an even surface with good grip, smoothness and durability, while withstanding extreme impacts and high temperature deformation. With speeds reaching 320km/h, constant acceleration/braking and corner taking, the stress on the track’s surface is extreme and far above that of ordinary roads.
The circuit was designed by Herman Tilke GmbH of Germany, who were also responsible for the Sepang track in Malaysia and the new circuit in Bahrain. The contractors were Shanghai Road Construction Co. and it was due to the close co-operation between the design company, contractors and equipment suppliers, such as Dynapac, that the entire project was brought to a successful completion.
Surface evenness
In Formula 1 racing a segregated asphalt is totally unacceptable as the top layer must be absolutely even. Dynapac therefore suggested that the contractors used four F141C tracked pavers with extended-drive drive units at the outer ends of the auger. The auger’s function is to distribute the asphalt mix as evenly and as continuously as possible in front of the screed.
With the extended-drive system there is no obstacle to the free flow of material as the drives are placed at the auger ends instead of in the middle of the stream of material. This gives the screed an optimum operating condition, resulting in a top asphalt layer without material segregation and a better pre-compaction. The screed was hydraulically extended to its maximum width and achieved 89% of screed pre-compaction measured with a nuclear gauge. Surface structure and evenness were better than 2mm measured over 4m.
The Dynapac F141C paver features a flow-through capacity of 750 tonnes/h and a hopper capacity of 5.7m3. It ensures a maximum paving width of up to 9.0m and a maximum laying thickness of 300mm. All four pavers were fitted with Dynapac’s VB 1105 TV (tamper and vibration) screed.
Roller types
For the 10cm asphalt base-course, using a 0–35mm aggregate mix, the Dynapac rollers were able to achieve a 98% density in just eight passes. Similar passes and compaction densities were also achieved for the 4cm binder with a 0–16mm aggregate mix.
For the 4cm wearing course, a polymer-modified bitumen top layer with a SPS content greater than 5% (ASTM D5, 0–13mm aggregate mix) was used, together with granite aggregates with a PSV of 66 to match the colour and hardness specified — key factors stipulated by the FIA. The choice of binder ensured a ‘softening point’ above 75ºC to ensure durability under the region’s high ambient temperatures.
Dynapac CC 322 and CC 232 hydrostatically-driven tandem rollers were used. These rollers can initially be set on a high-amplitude/low-frequency mode to complete the compaction of the upper part of the thick layers and compact the overlaying wearing course. The rollers are then switched to a low-amplitude/high-frequency setting to complete the compaction of the upper part of the thicker layers, and to compact the final overlaying wearing course. This technique eliminates the tendency to over-compact the thinner layers.
Generally, only the CC 322 rollers were used for compacting the wearing course working in the low-amplitude mode. The CC 232 rollers were used on the tight bends with the advantage of their split drums avoiding any tears in the mat.
A 95% degree of compaction was achieved in four passes in the low-amplitude mode with a high-frequency setting, followed by another six to eight passes to reach the stipulated degree of compaction, set at 99%. The compaction was constantly monitored with the help of nuclear density gauges.
Throughout the laying of all three asphalt courses, the rollers worked over a minimum pass length of 50m with cooling times ranging from approximately 40min on the basecourse to 11–12min on the wearing course.
According to Shanghai Road Construction, while cold jointing was permitted on the base asphalt course, it was unacceptable to the FIA on the wearing course.
FIA approval
Throughout the paving work, Shanghai Road Construction generally used two or three Dynapac trains led by the F141C pavers. For the shortest U-bends, however, asphalting was undertaken using all four pavers. This allowed them to achieve the specified high-quality finish across the track width by staggering the pavers over the extremely tight curve.
By mid-May the contractors had completed paving all the connection roads and the circuit’s first asphalt course. The binder and wearing course were completed before the end of the month, paving up to 2,100 tonnes/day.
The wearing course was approved by the FIA on 3 June 2004 for Formula 1 racing and the first Grand Prix took place on 26 September.
Dynapac Ltd, Parkfield Road, Rugby, Warks CV21 1QJ; tel: (01788) 532107; fax: (01788) 541195; website: www.dynapac.com