Sacrificial Iron – A Needless Cost!
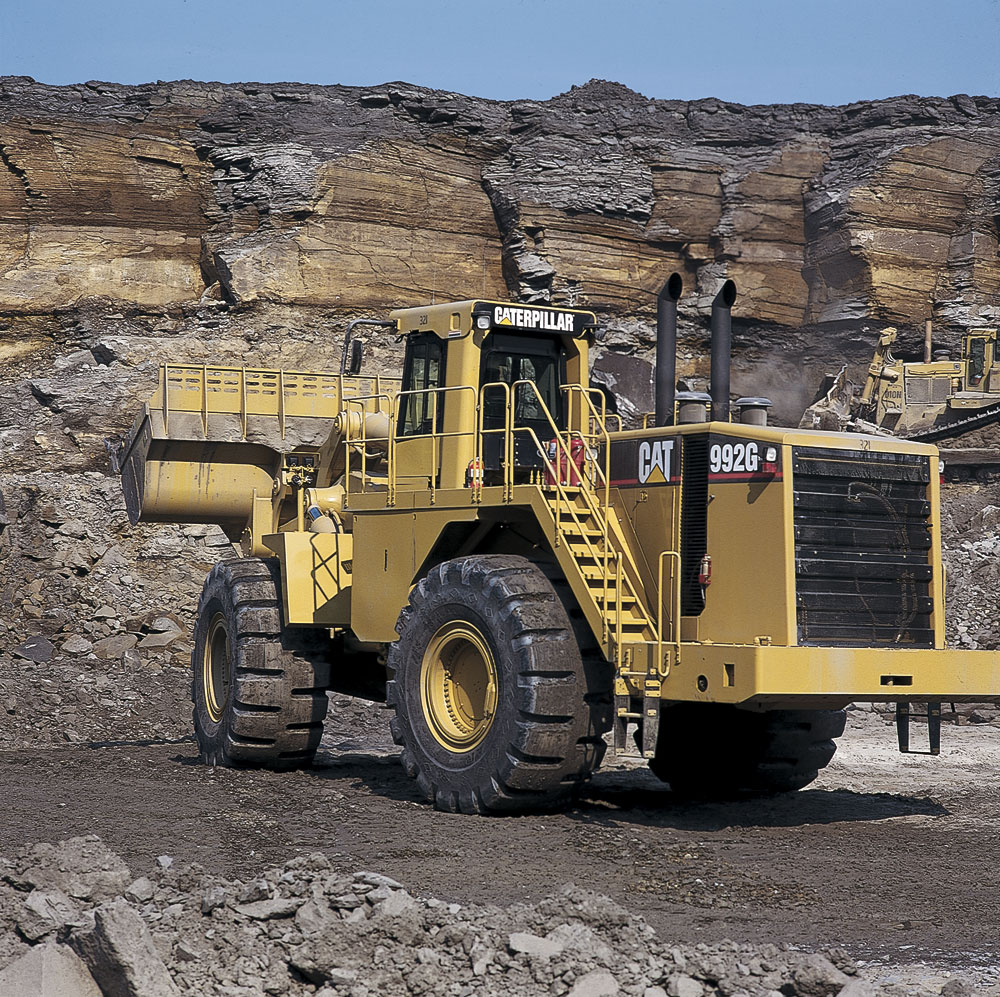
Ground-engaging tools (GET) are wearing parts that are the front line of defence for machines, protecting expensive components against damage and helping to enhance productivity. Marcus Pitt, GET specialist from Finning (UK), highlights GET best practice and how this can be applied to wheel loaders working in quarrying applications.
Correct selection, operation and maintenance of ground-engaging tools (GET) are three factors that can help prevent a quarry’s operational costs from spiralling out of control. GET costs vary depending upon the application, but any cost-per-hour savings will result in a direct improvement to a company’s bottom line. It is essential, therefore, that quarry managers select the right shape and size of GET for a specific application, as this can have a major impact and will significantly affect the cost per hour. Different applications require different combinations of strength, wear material and penetration, and getting the balance right for all three is the key to getting the best GET cost per hour.
Selection
Although a sharper tooth will provide better penetration and therefore greater productivity, it is also thinner and will wear quicker, thus increasing downtime and replacement frequency. It is important always to look at the application in relation to the shape of the tooth. For example, a machine loading poorly shot rock will require a sharper tooth than a machine in a rehandling operation. The strength of GET is also important; where ground conditions place excessive loads on bucket teeth, it is important to have a shorter, stronger profile rather than a longer, sharper profile, which could be prone to breakage.
Operation
Like any other machine component, the operator is central to maximizing the life of GET and delivering optimum productivity. With the constant pressure to hit production targets, it is easy for an operator to overlook GET best practice, so it is important to keep reiterating the do’s and don’ts.
In order to maintain clean site floors, operators often run for excessive periods with the bucket flat to the floor. While this can help to clear debris, such action will also place excessive wear on the underside of the bucket. Evidence of this can often be seen with bucket teeth that are completely worn through on the underside while being relatively unworn on their top side. In addition, if the bucket positioner is angled incorrectly there can be a significant reduction in productivity and an increase in wear rates; the incorrect angle changes material flow into the bucket, lowering the fill rate and causing the material to contact areas of the bucket that are not protected by GET.
Whether a machine is fitted with bolt-on cutting edges or bucket teeth, Caterpillar GET are designed to have more than one life. In practice, wheel loader bucket teeth will normally suffer more wear on the underside than on the top side. To obtain a second life, bucket teeth can be flipped over, allowing all of the wear material that is built into the part to be used. Standard or heavy-duty bolt-on cutting edges are designed to wear from the front backwards towards the bolt holes. Again, before they become fully worn the edges can be turned to utilize the additional life built into the edge.
Owing to the way material flows around a bucket, it is often the case that bucket teeth on the outer edge of the bucket wear more rapidly than those at the centre. Swapping tips over when they are approximately 50% worn maximizes wear life and ensures that all tips can generally be replaced at the same time.
Operator driving style and manoeuvring of wheel loaders can also have implications for productivity, fuel economy, tyre, bucket and GET wear. Machines working at the face should always approach the pile face on. If the bucket enters the pile at an angle it will cause uneven wear on one side of the bucket. Furthermore, loading in this manner is often significantly less productive than approaching the pile straight on and can therefore increase cycle times.
Maintenance
It is very important that all operators conduct a detailed daily check of their machine. As part of a quick walk around they should check the bucket and look for any broken, missing or cracked bucket teeth and adaptors. A bare bucket on a machine offers no protection and should be avoided at all times.
In addition, base edge or adapter weld cracks should also be reported and repaired as soon as possible. As with many preventative-maintenance techniques, spotting and acting on a problem in its infancy can be significantly cheaper than when it has escalated into major downtime.
When replacing or swapping bucket teeth, the retainer and pin should always be checked. It is imperative never to reuse a retainer if it is bent or broken, and operators should always tap the end of the pin and replace it if it moves easily. Within a quarry environment a lost tooth can have a high cost as well as health and safety consequences. A broken tooth could easily find its way into a crusher, causing significant damage and downtime.
Records
Selection, operation and maintenance are vital to controlling GET costs. However, they may be worthless unless they are backed up by accurate record-keeping. By keeping track of what is replaced, repaired, rotated or swapped, an accurate picture of true GET costs can be built up.
Boneyard analysis
Worn and replaced GET is often kept for short periods of time before being scrapped, however these components are not just another pile of junk. By examining wear patterns, combined with accurate record-keeping, it is possible for a Finning product support representative to identify potential improvements that could impact on a company’s cost per hour and/or productivity. Careful analysis of site practices and GET selection could also lead to a different choice of GET or the identification of a simple maintenance technique to help fully utilize the wear material.
GET Golden Rules for wheel loaders
Correct selection, operation and maintenance of ground-engaging tools (GET) are three factors that can help prevent a quarry’s operational costs from spiralling out of control. GET costs vary depending upon the application, but any cost-per-hour savings will result in a direct improvement to a company’s bottom line. It is essential, therefore, that quarry managers select the right shape and size of GET for a specific application, as this can have a major impact and will significantly affect the cost per hour. Different applications require different combinations of strength, wear material and penetration, and getting the balance right for all three is the key to getting the best GET cost per hour.
Selection
Although a sharper tooth will provide better penetration and therefore greater productivity, it is also thinner and will wear quicker, thus increasing downtime and replacement frequency. It is important always to look at the application in relation to the shape of the tooth. For example, a machine loading poorly shot rock will require a sharper tooth than a machine in a rehandling operation. The strength of GET is also important; where ground conditions place excessive loads on bucket teeth, it is important to have a shorter, stronger profile rather than a longer, sharper profile, which could be prone to breakage.
Operation
Like any other machine component, the operator is central to maximizing the life of GET and delivering optimum productivity. With the constant pressure to hit production targets, it is easy for an operator to overlook GET best practice, so it is important to keep reiterating the do’s and don’ts.
In order to maintain clean site floors, operators often run for excessive periods with the bucket flat to the floor. While this can help to clear debris, such action will also place excessive wear on the underside of the bucket. Evidence of this can often be seen with bucket teeth that are completely worn through on the underside while being relatively unworn on their top side. In addition, if the bucket positioner is angled incorrectly there can be a significant reduction in productivity and an increase in wear rates; the incorrect angle changes material flow into the bucket, lowering the fill rate and causing the material to contact areas of the bucket that are not protected by GET.
Whether a machine is fitted with bolt-on cutting edges or bucket teeth, Caterpillar GET are designed to have more than one life. In practice, wheel loader bucket teeth will normally suffer more wear on the underside than on the top side. To obtain a second life, bucket teeth can be flipped over, allowing all of the wear material that is built into the part to be used. Standard or heavy-duty bolt-on cutting edges are designed to wear from the front backwards towards the bolt holes. Again, before they become fully worn the edges can be turned to utilize the additional life built into the edge.
Owing to the way material flows around a bucket, it is often the case that bucket teeth on the outer edge of the bucket wear more rapidly than those at the centre. Swapping tips over when they are approximately 50% worn maximizes wear life and ensures that all tips can generally be replaced at the same time.
Operator driving style and manoeuvring of wheel loaders can also have implications for productivity, fuel economy, tyre, bucket and GET wear. Machines working at the face should always approach the pile face on. If the bucket enters the pile at an angle it will cause uneven wear on one side of the bucket. Furthermore, loading in this manner is often significantly less productive than approaching the pile straight on and can therefore increase cycle times.
Maintenance
It is very important that all operators conduct a detailed daily check of their machine. As part of a quick walk around they should check the bucket and look for any broken, missing or cracked bucket teeth and adaptors. A bare bucket on a machine offers no protection and should be avoided at all times.
In addition, base edge or adapter weld cracks should also be reported and repaired as soon as possible. As with many preventative-maintenance techniques, spotting and acting on a problem in its infancy can be significantly cheaper than when it has escalated into major downtime.
When replacing or swapping bucket teeth, the retainer and pin should always be checked. It is imperative never to reuse a retainer if it is bent or broken, and operators should always tap the end of the pin and replace it if it moves easily. Within a quarry environment a lost tooth can have a high cost as well as health and safety consequences. A broken tooth could easily find its way into a crusher, causing significant damage and downtime.
Records
Selection, operation and maintenance are vital to controlling GET costs. However, they may be worthless unless they are backed up by accurate record-keeping. By keeping track of what is replaced, repaired, rotated or swapped, an accurate picture of true GET costs can be built up.
Boneyard analysis
Worn and replaced GET is often kept for short periods of time before being scrapped, however these components are not just another pile of junk. By examining wear patterns, combined with accurate record-keeping, it is possible for a Finning product support representative to identify potential improvements that could impact on a company’s cost per hour and/or productivity. Careful analysis of site practices and GET selection could also lead to a different choice of GET or the identification of a simple maintenance technique to help fully utilize the wear material.
GET Golden Rules for wheel loaders
- Ensure daily inspection is undertaken
- Never operate bare buckets
- Ensure the bucket positioner is set correctly
- Minimize ground contact
- Rotate and flip bucket tips
- Include GET and buckets in a maintenance schedule.