Red Power
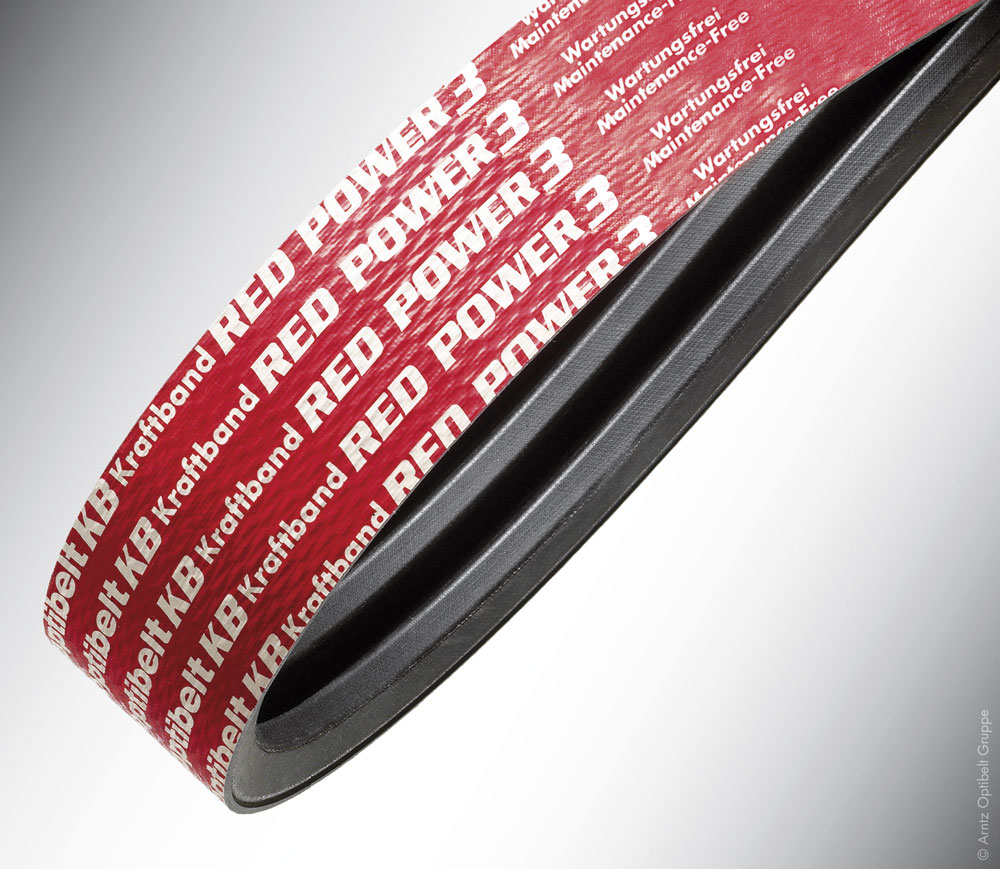
Optibelt develop their most cost-effective and highest performing heavy-duty drive belt – RedPower 3
The ongoing global recession has seen many quarry operators implementing more efficient ways of improving energy efficiency, increasing productivity and minimizing costs across their operations. In some cases, companies have had to diversify in order to become more flexible towards customer needs while adopting energy-saving strategies and cost-reduction programmes as part of efforts to balance growing costs with a static return rate.
Whether it is reduced maintenance costs, increased machinery uptime or better fuel economy, every part of a business operation is now carefully monitored, as quarry firms look to manage their operating expenses efficiently in a highly competitive market.
Part of the Germany-based Arntz Optibelt Group, Optibelt are one of the world’s leading manufacturers of drive belts with a strong focus on giving customers best value for money through the lowest belt usage costs and highest productivity wherever possible.
At Hillhead 2012 the company showcased its latest advances in ‘V-belt’ drive technology, including the much talked about Red Power 3 drive belts. ‘We always strive for continuous improvement across our product range to ensure that Optibelt are at top end of the market in terms of quality and reliability,’ explained Chris Rice, managing director of Optibelt UK.
‘There’s no denying the fact that the current market is flooded with cheap, imported low-quality belts, but at the same time there is an increasing demand for high-quality V-belts, as we have experienced with Red Power 3, because end-users are now beginning to pay more attention to total costs and cost savings in the long term.’
What makes Red Power 3 V-belts a superior choice over conventional belts in quarrying applications? The belts are a direct replacement for conventional V-belts and can be fitted without making any modification to the drive or pulleys. According to Optibelt, drive efficiencies of up to 97% can be achieved with Red Power 3, and the belts have been designed to be maintenance-free and energy-efficient.
Available in all popular V-belt profiles (eg SPA, SPB, SPC, SPZ etc), the new-generation belts can deliver up to 50% increased performance over standard Optibelt V-belts while providing a maintenance-free service life of typically 25,000h – equivalent to three years of continuous running, with no re-tensioning required.
‘This is all down to new production processes and high-quality components making Red Power 3 truly maintenance-free,’ said Mr Rice. ‘The belts feature a unique construction; the tension cord for all sections and cross sections consists of a special polyester cord with an abrasion-resistant cover. This means the Red Power 3 V-belt is very low stretch and no re-tensioning is required throughout its life.’
Drive optimization
It is perhaps not surprising, therefore, that Red Power belts are increasingly being specified by operators of belt-driven machinery, such as crushers and screens, due to their proven ability to reduce costs and improve productivity.
Engineers at Tarmac’s Dene Quarry, near Matlock, for example, decided to fit Red Power belts on a range of plant across the site, including conveyors, exhaust fans and a rotary drum dryer, after they had shown significant improvements over conventional belts on a crusher application.
Optibelt found that the original belts on a Mansfield crusher required re-tensioning every two weeks or so due to stretching and, as a result, they needed to be replaced frequently. As an alternative, Optibelt recommended Red Power belts to Tarmac and after operating these same belts for more than three years, they are still running without any problems and have required no adjustment or attention during this time.
Utilizing Red Power drive belts has also reaped cost savings and environmentally friendly benefits for Tarmac. Red Power’s higher power rating means fewer belts on a drive and there is little material waste during the service life of the drive belts.
Mr Rice said that power measurements taken before and after fitting a set of Red Power belts on the crusher have shown a 5.2% reduction in power consumption, while further power savings have also been recorded on conveyor and mill applications. ‘With the success of the trial, it is very encouraging to see Red Power belts being used extensively at Dene Quarry because the total cost savings from the reduction in energy usage can potentially reach thousands of pounds each year,’ he explained.
Red Power belts have also been specified by CEMEX at Willington Quarry, in Derbyshire, on a Metso HP200 cone crusher. The previous belts lasted around 3-4 months and it took approximately 2h (downtime) to replace the substandard belts. Utilizing the newly installed V-belts has eradicated the premature belt wear caused by pulley misalignment and incorrect belt tension, and more importantly, the costly production downtime that CEMEX were facing.
Following the success of switching to Optibelt’s premium products, CEMEX have now fitted the energy-efficient transmission belts to all their drive systems on site in order to achieve further cost savings and operational efficiency at Willington.
As well as quarry operators, equipment manufacturers are also starting to use Red Power V-belts on their machinery. A leading crushing and screening specialist, for example, has specified the heavy-duty belts on one of its mobile impact crusher models and, according to Mr Rice, will be fitting Red Power 3 belts on the redesigned drive chains in newer machines to help meet Tier 4 Interim emission standards while also delivering a number of improved design features to achieve greater productivity and ease of maintenance.
With a wide range of belts and tools on offer, Optibelt’s sophisticated logistics system ensures products are supplied to customers quickly and efficiently. The company’s belts are stocked extensively across the country not just through Optibelt UK but also Brammer, IADA and a number of independent suppliers. Optibelt UK also provide on-site training sessions and technical support to assist end-users in optimizing belt life and efficiency.
‘We want our customers to achieve the most from their machines and only well-trained staff guarantee an increase in productivity and product quality,’ explained Mr Rice. ‘When Red Power 3 belts are deployed in the most difficult of conditions – quarries being a prime example — as suppliers of a product with proven reliability and capability, we also want to ensure operators gain the best return on their investment, this can only be achieved through drive optimization.’