Dewatering Decision
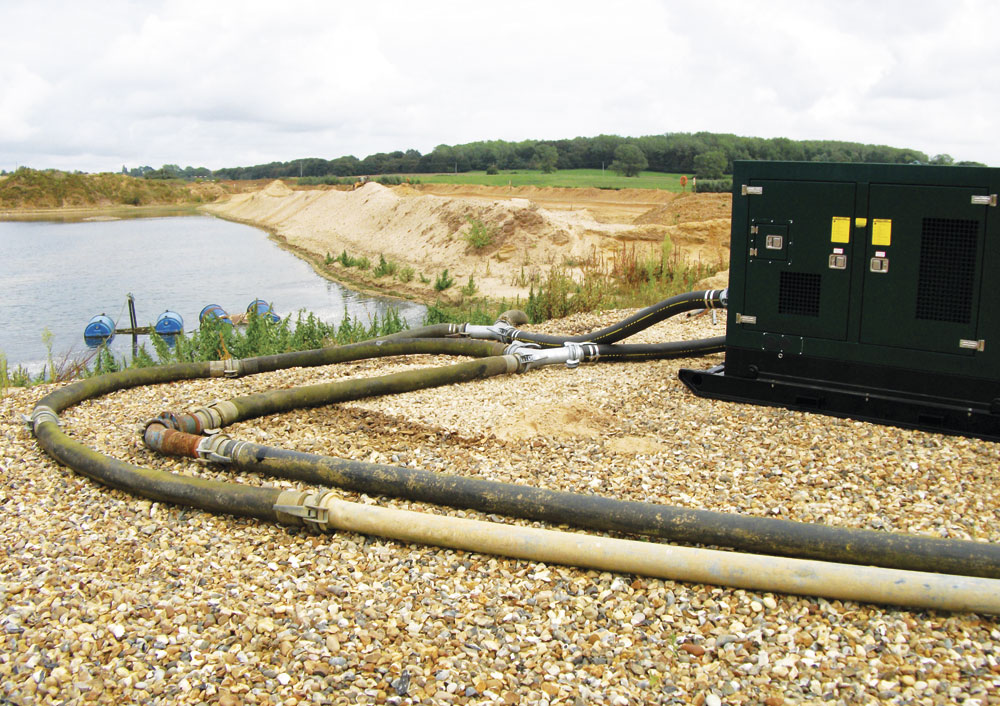
Choosing the correct type of pump for dewatering applications
Managing water is one of the most important aspects of any quarrying application, whether controlling/dewatering site ingress or ensuring a steady supply for process plant applications.
Quarries, like many other major industrial applications, use a wide variety of pumps including centrifugal and positive-displacement types, both of which can be further broken down into sub-products such as submersible, self-priming, progressive cavity, AOD, end suction etc.
It is perhaps not surprising, therefore, that many quarries around the world end up using pumps that are not best suited to the application in hand, resulting in low-efficiency pumping and, more importantly, increased costs.
As this subject area is vast, this article focuses solely on dewatering pumps and their use in keeping a quarry dry in very wet conditions.
In simple terms, three main types of pumps are used to keep quarries dry, two of them being centrifugal and the third being positive displacement. Accepting that a positive-displacement pump is generally used as a low-flow, low-energy solution, the focus of this article is on centrifugal pumps, which are often misused and can cost operators a significant amount in terms of increased energy use and reduction in profits.
In broad terms, centrifugal pumps for quarry applications come in two forms, solids or slurry handling and those for clean or dirty water. The design of the pumps for these two applications differs quite considerably and, therefore, their operating performances also are different, causing large disparities in the energy required for the pumps to operate successfully.
In broad terms, slurry pumps are hard iron pumps with open clearances, heavy-duty design and minimal machining involved in their production. As such, these pumps are well suited to pumping large solids or large amounts of solids contained in slurry.
Dredging/slurry pumps such as Warman or Metso (end suction) and Dragflow/Toyo (submersible) are prime examples of these types of pumps where hydraulic efficiency is not as important as their ability to handle rocks, sand, ore and solids-laden fluids, without experiencing excessive wear or downtime, while operating in highly arduous conditions for extended periods.
Clear or dirty water pumps, such as those manufactured by Pioneer Pump, are very different from slurry pumps in terms of their hydraulic performance. These pumps are designed to be rugged enough to operate in mining and quarrying applications (thanks to the use of materials such as ductile iron and CA6NM stainless steel as standard in most versions) where their primary use is in dewatering a site as fast as possible using the least amount of energy.
Dewatering a quarry often does not require a slurry pump, yet many sites, whether for historic reasons or through resistance to change, suffer from increased costs through the use of such pumps when a dewatering pump may be far more suitable.
For example, consider a dewatering application that requires four pumps, each capable of 450m3/h of flow at 120m head, to dewater a site on a continuous basis. Because of the lack of electricity on site these pumps have to be engine driven. Table 1 shows the operating parameters of a slurry pump versus a high-efficiency dewatering pump and the savings that could be made by using the correct pump in this application.
As can be seen from the figures, use of the correct pump for the application can save enormously on running costs and directly impact the bottom line of a quarry’s profit and loss account.
Equally important is the environmental impact. Based on the above comparison, the dewatering pump would be able to operate using a 9-litre engine with a maximum output of 225kW, whereas the slurry pump, because of its reduced efficiency, would need a larger engine, eg an 11- or 13-litre unit, thereby resulting in increased emissions.
When comparing the overall cost, including capital and running costs, choosing the correct dewatering pump is business critical but is often overlooked. Quarries tend to look for an overall package that includes spares and support, but most international pump companies offer these capabilities and therefore the decision comes down to choosing the right type of pump for the application. And in dewatering applications, where the pumps are often large, making the correct choice is paramount.