W.S Tyler introduce F-Class vibrating screen
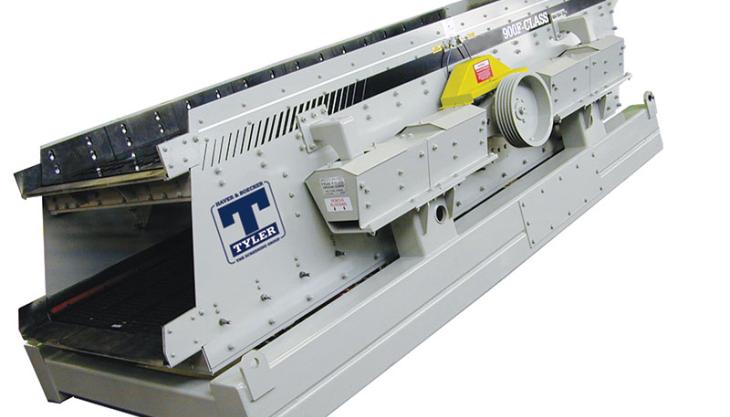
Compact unit offers tandem operation, multiple machine installations and reduced operational costs
W.S TYLER, providers of screening solutions to the aggregates and mining industries, are offering an alternative to screens larger than 10ft x 24ft with their F-Class vibrating screen configuration.
The company says placing two 10ft x12ft F-Class machines in tandem (one unit feeds the other) offers many benefits, including cleaner operation, less maintenance and longer life for the structure that houses them when compared with other units on the market.
Whether using a two- or three-deck unit, overall screening is enhanced with a 3in drop between the screens that leads to additional material tumbling so any fines remaining on top are more likely to fall through. Discharge lips and rubber skirting minimizes spillage during the transition.
Large vibrating screens operate horizontally which requires force, thereby causing more wear. W.S Tyler’s smaller F-Class units, however, run at a 15-25 degree incline, requiring lower g-force and causing less wear on machine components.
Running the tandem F-Class configuration is said to be a less expensive option both in terms of initial purchase price and maintenance/repair. First, large units require more robust construction due to the high stresses they endure when processing larger loads. Longer side plates are also weaker than shorter ones, which leads to more opportunity for damage. Furthermore, the cost of replacing a large machine exceeds the cost of replacing a single module from the tandem set-up. W.S Tyler, therefore, believe operating two smaller units in tandem is a more durable, efficient option.
The F-Class vibrating screen has been specially designed for use in a tandem configuration. The machine features proven four-bearing technology and counterbalance weights to cancel the forces generated by the body, so it produces minimal structural vibration. The advanced eccentric shaft – which is supported by four high-performance, double spherical roller bearings – creates a constant positive stroke that handles material volume spikes without losing momentum.
In addition, the continual circular screening action produces a constant, optimized g-force. This minimizes blinding and pegging, and maximizes screening efficiency, which makes the F-Class an effective solution in both wet and dry applications. The unit is also suitable for screening applications that require consistent, load-independent performance at constant g-force in all operational modes.
The F-Class scalps and classifies ores, minerals, stones, sand and gravel. It processes up to 1,200 tonnes/h while providing fast, accurate sizing. In addition to traditional screening, the F-Class unit is often used before primary crushers to screen out fines and help reduce crusher wear. It precisely screens material from 20 mesh to 6in.
All F-Class vibrating screens undergo extensive testing, inspections and vibration analysis prior to shipping. During commissioning on site, W.S Tyler test their machine again to ensure it achieves optimal performance within the customer’s specific operation and performance targets.