Noise Control for Quarries
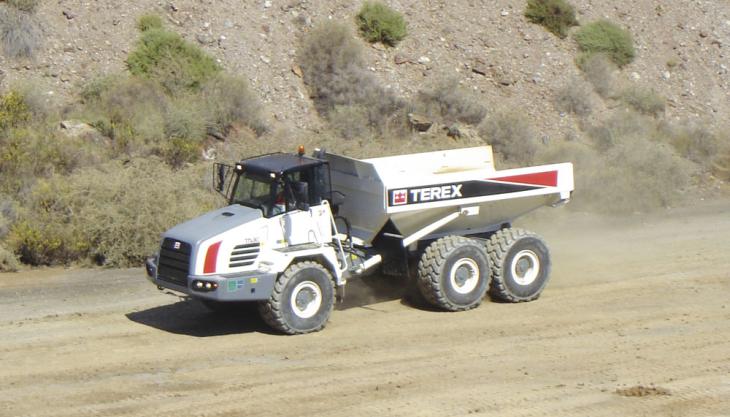
It is perhaps stating the obvious to say that the very nature of a quarry or surface mineral working means it has the potential to be an inherently noisy operation. Heavy machinery, heavy vehicles, blasting operations and even vehicle reversing alarms are all obvious sources of noise in quarrying operations that can cause significant disturbance to the site’s neighbours and increase noise at work issues.
Documents such as the BS 5228 Code of Practice for Noise and Vibration Control on Construction and Open Sites, and MP11 Controlling and Mitigating the Environmental Effects of Minerals Extraction in England, discuss the importance of planning with regard to noise control.
MP11, for example, suggests that by progressively working away from the noise-sensitive locations, the noise exposure will reduce with time. Conversely, it is pointed out that if the excavation proceeds towards the noise-sensitive location, the quarry face itself can act as a noise screen. Given that the reduction of noise with distance is of the order of six decibels per doubling of distance (not including factors such as ground effect, prevailing weather etc), the reductions achieved with the first method may have diminishing returns depending on the relative distances involved.
The use of acoustic screens or baffle mounds is a mainstay for noise control on open sites. The basic principle of this control method is that the further the noise has to travel relative to a straight line from the noise source to receiver, the more the noise is attenuated. This means that, depending on the positioning of the barrier relative to the source, the effectiveness of the measure may be reduced with distance.
The ability of sound to diffract (bend) around a barrier is inversely proportional to its frequency, so higher-frequency noise is more effectively treated by barriers than low-frequency noise, which can easily diffract over a barrier which is low in height relative to the wavelength, eg the wavelength of 100Hz is 3.4m at 20°C. Noise reduction due to vegetation and trees around a noise source is minimal and rarely of any practical use.
One of the most effective ways of minimizing noise problems at a site is at source. Machinery and vehicles are tested, rated and labelled for their noise emissions under the European directive 2000/14/EC, which relates to noise emissions in the environment by equipment designed for use outdoors.
Under this directive, equipment and vehicles are labelled with their A-weighted sound power level (LwA dB). Legal noise limits are specified in the directive, and because of the clear labelling, the quieter of two or more equivalent vehicles (eg dumptrucks) that are compliant with the directive can easily be identified. As document MP11 points out, it is possible to reduce noise emissions by 3–10dB by using quieter earthmoving plant.
This parameter can also be used in the planning stage to assess the likely impact of a noise source on neighbouring noise-sensitive locations. The sound power level of a noise source (LwA – a decibel measurement based on watts) can be used by someone trained in acoustics to predict, at a noise-sensitive location, the sound pressure level. In environmental noise assessment, the most common parameter is the A-weighted equivalent continuous sound pressure level, LpAeq dB, although in practice the not as precise ‘average’ noise level over a given period of time is used.
In the automotive industry, acoustic engineering has been an essential part of the skill set for decades. This is not generally the case in the manufacturing of heavy equipment, but it means that with the application of good acoustic principles the emissions from many currently noisy vehicles and machines can be significantly reduced at source.
Ventac specialize in reducing the noise emissions of industrial, earthmoving, agricultural and other off-road vehicles by acoustically assessing each vehicle and then designing and manufacturing a vehicle noise-control solution. Typically working in partnership with OEMs to incorporate the solution at the manufacturing stage. Ventac use a systematic approach combining precision testing techniques, acoustic expertise and extensive experience to achieve the maximum reduction in a practical form.
A typical project involves a visit to the client’s site, anywhere in Europe, with test equipment and sample noise control materials. Approximately one day’s work can produce a vehicle noise assessment with noise-control options, resulting in a vehicle that is physically quieter and a reduction that is audible to the ear.
The Ventac strategy is based on continual improvement, and to this end the following take place on an ongoing basis:
- Sophisticated test techniques, such as sound intensity measurement and noise mapping, to not only develop new noise solutions, but to optimize and develop existing kits.
- Ventac’s laboratory suite of reverberation chambers acoustically tests new materials coming on to the market and new composites manufactured on site.
- Ventac seek to develop emerging acoustic technologies in a practical manner and to develop further patentable solutions of their own.