Lignacite launch world’s first carbon-negative block
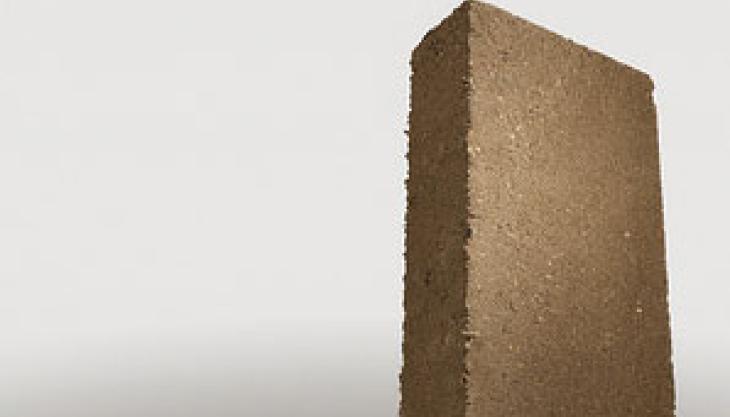
The Carbon Buster – first masonry block to capture more CO2 than is emitted during manufacture
MASONRY products manufacturers Lignacite have launched the world’s first carbon-negative building block.
Named ‘The Carbon Buster’, the new building block from Lignacite is a British innovation, which has been developed by the company in partnership with Carbon8 Aggregates, using their award winning Accelerated Carbonation Technology.
The Carbon Buster incorporates more than 50% recycled aggregates and combines this with Carbon8’s carbonated aggregates derived from by-products from waste-to-energy plants.
The result is a high-performing masonry product, and the first ever building block which has captured more carbon dioxide than is emitted during its manufacture (14kg of CO2 per tonne).
Carbon8’s technical director, Dr Paula Carey, explained: ‘On the back of research carried out at The University of Greenwich’s School of Science, Carbon8 identified an end use for thermal residues from waste-to-energy plants.
‘By mixing the residue with water and carbon dioxide, we were able to transform the material into what the Environment Agency (EA) has agreed is a product suitable for use as a virgin aggregate replacement.’
Following the EA review, Carbon8 erected a £1 million carbonation plant in Brandon, Suffolk, adjacent to Lignacite’s masonry plant. Here, the residue is carbonated, then mixed with binders and fillers before being pelletized and used as a key ingredient in the Carbon Buster block.
Lignacite use sand and gravel from their quarry adjacent to the block plant. This, combined with the use of recycled waste material, such as wood shavings, glass and shells, means the company’s masonry products have always had a minimal carbon footprint.
Despite these efforts, however, the cement content previously used made it impossible to generate products that were carbon negative. Thanks to carbonated aggregates, however, the Carbon Buster now boasts a negative CO2 content.
For Lignacite, which is a family owned company that dates back nearly 70 years, the use of carbonation technology is an extension to their long-standing commitment to sustainability.
‘We were the first block manufacturer in the country to introduce recycled and waste materials into our products, and one of our ranges already contained 90% waste materials,’ explained Lignacite’s chief executive, Giles de Lotbiniere.
‘However, we firmly believe that constant innovation is key to creating a more sustainable future for everyone. We are now working with a number of forward-thinking architects and specifiers and are incredibly excited to be taking this strategy to the next level with the launch of the Carbon Buster.
‘With the Government’s commitment to zero-carbon homes, we are confident the Carbon Buster has an important role to play in helping to meet the 2016 targets.’