Lee Tunnel Project scoops top award
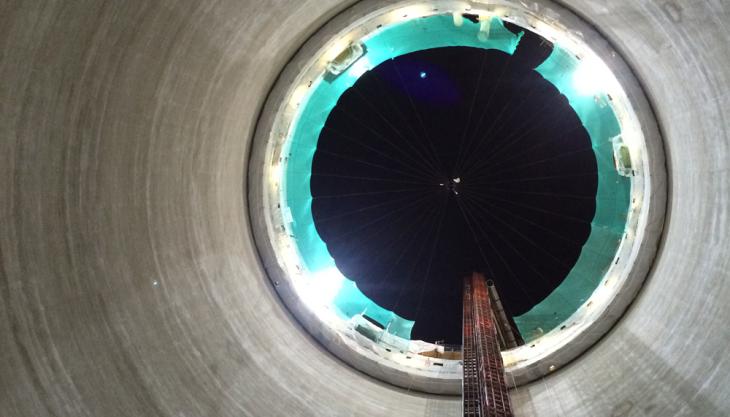
MVB joint-venture project judged Outright Winner in 2016 Concrete Society Awards
LEE Tunnel in Beckton, London – the MVB joint-venture project pushing the technical boundaries of what is possible with concrete – was the Outright Winner at this year’s prestigious Concrete Society Awards in London.
More than 400 members, guests and construction industry representatives attended the Concrete Society Awards dinner held at the Grosvenor House Hotel on 17 November. Now in its 48th year, the event celebrates excellence in concrete and is the longest-running awards programme in the UK construction industry.
Broadcaster and journalist Kate Silverton was this year’s guest host, presenting awards to the winners and compering the programme for the evening.
The Outright Winner was the MVB joint venture for its Lee Tunnel Project, which comprises five shafts with diaphragm walls that are the deepest ever undertaken in the UK at 90m. A 7m diameter x 7km long tunnel connects the shafts.
The steel-fibre-reinforced concrete for the slipformed tunnel lining took 18 months to develop, resulting in a self-compacting concrete with a retention time of 4h encompassing up to 15 constituent materials. The innovative slipformed shaft construction also incorporated steel fibres to reduce substantially the quantity of standard reinforcement.
Richard Kershaw of CEMEX UK Materials, concrete suppliers to the project, said: ‘We are very honoured to receive such acclaim from this most prestigious of awards. Concrete was the only realistic material choice for this structure. CEMEX are proud to be part of this momentous scheme and part of a legacy to London which will help prevent 16 million tonnes of sewage entering the river Lee and the Thames each year.’
The Concrete Society’s judging panel said: ‘The Lee Tunnel was the most outstanding structure and, therefore, outright winner for its technical achievements in the use of concrete, its demanding placement conditions and innovative structural solutions. The statistics for concrete volume placed are impressive; the innovation required and final execution is exemplary. This project pushed the technical boundaries of what is possible with concrete.’