HotShot – an electronic detonator system that is simple to use
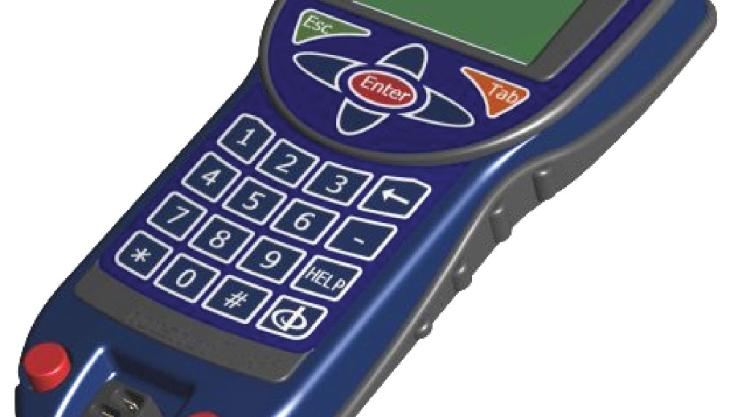
HotShot – described as the world’s first auto-programmable electronic detonator system – is manufactured in South Africa by DetNet and marketed in the UK, with full technical and training support, by Exchem Explosives.
HotShot offers all the advantages of other electronic detonator systems, such as: delay accuracy, giving improvements in fragmentation and face conditions along with the potential to deliver greatly enhanced vibration control; and two-way communication, resulting in enhanced safety as a full health check is undertaken for each detonator prior to the blast, thereby reducing the chances of misfires.
However, where HotShot has the advantage over other electronic detonator systems is in its ease of use. This simplicity stems from the way that the HotShot system operates. Effectively, the system senses the way that the blast has been connected by looking at the physical order in which the detonators are arranged – in the same way that all shock-tube-based systems work. As the system looks at what items have been physically connected at the end of the loading process, there is no need for preloading of a blast design into the hand-held logging unit. Trials in the UK have shown that shotfirers familiar with shock-tube systems immediately recognize the way that HotShot works and become very confident in its use over a relatively small number of blasts.
An item of hardware, known as a ‘row controller’, is used to indicate to the system the location of each row in a blast and from where in the row the initiation is to start. If there are detonators connected to the left and right of a row controller, the shotfirer has the chance to choose a right or left delay offset during the blast-design process.
For situations where the shotfirer has to deal with out-of-sequence detonators, such as in blasts with toe-holes or a pre-split line, an additional piece of hardware, called a ‘branch controller’, can be used. These units can be used anywhere in a blast. During the blast-design process the shotfirer has complete control over the timing and delays of the detonators connected on the branch. The UK trials have shown that the vast majority of blasts can be undertaken without the use of any branches.
All testing and blast-design operations are carried out on a device known as the ‘tagger’. This is effectively a highly robust, waterproof, hand-held computer designed for use under adverse conditions.
The auto-sensing of the initiation layout means that once the blast has been connected and tested, the shotfirer is presented with a map of the blast showing the physical layout and the number of detonators in each section of the blast. This map is a great aid in determining if the blast has been connected up correctly.
The blast-design process can be undertaken on the bench without any need to be physically connected to the blast, and consists of answering a number of simple questions relating to the arrangement of the detonators in the holes, the inter-hole delay, inter-deck delay and inter-row delay. Indeed, a single row of single-decked holes fired from a free-end simply requires the input of a single delay value – the inter-hole delay. Even a complicated blast with multiple rows of double-decked holes fired from the middle only requires the input of four numbers.
Once the design process is complete, the calculated initiation plan is presented on the tagger screen for final checking. A blast simulation can even be carried out on screen to check the firing sequence is as intended. The blast is fired by a combination of the tagger, blasting cradle and a blast key.
The blast key is an electronic device and requires the user to enter a unique six-digit password before the blast can be fired, giving enhanced security. Once the blast has been fired, a complete record, including detonator times and the initiation plan, can be downloaded from the tagger on to a computer for printing or archiving.
After successfully completing extended UK trials in both quarrying and civil engineering projects, the HotShot system is now being offered to all sectors of the UK explosives industry.
Exchem Explosives, Venture Crescent, Alfreton, Derbyshire DE55 7RA; tel (01773) 832253.
HotShot offers all the advantages of other electronic detonator systems, such as: delay accuracy, giving improvements in fragmentation and face conditions along with the potential to deliver greatly enhanced vibration control; and two-way communication, resulting in enhanced safety as a full health check is undertaken for each detonator prior to the blast, thereby reducing the chances of misfires.
However, where HotShot has the advantage over other electronic detonator systems is in its ease of use. This simplicity stems from the way that the HotShot system operates. Effectively, the system senses the way that the blast has been connected by looking at the physical order in which the detonators are arranged – in the same way that all shock-tube-based systems work. As the system looks at what items have been physically connected at the end of the loading process, there is no need for preloading of a blast design into the hand-held logging unit. Trials in the UK have shown that shotfirers familiar with shock-tube systems immediately recognize the way that HotShot works and become very confident in its use over a relatively small number of blasts.
An item of hardware, known as a ‘row controller’, is used to indicate to the system the location of each row in a blast and from where in the row the initiation is to start. If there are detonators connected to the left and right of a row controller, the shotfirer has the chance to choose a right or left delay offset during the blast-design process.
For situations where the shotfirer has to deal with out-of-sequence detonators, such as in blasts with toe-holes or a pre-split line, an additional piece of hardware, called a ‘branch controller’, can be used. These units can be used anywhere in a blast. During the blast-design process the shotfirer has complete control over the timing and delays of the detonators connected on the branch. The UK trials have shown that the vast majority of blasts can be undertaken without the use of any branches.
All testing and blast-design operations are carried out on a device known as the ‘tagger’. This is effectively a highly robust, waterproof, hand-held computer designed for use under adverse conditions.
The auto-sensing of the initiation layout means that once the blast has been connected and tested, the shotfirer is presented with a map of the blast showing the physical layout and the number of detonators in each section of the blast. This map is a great aid in determining if the blast has been connected up correctly.
The blast-design process can be undertaken on the bench without any need to be physically connected to the blast, and consists of answering a number of simple questions relating to the arrangement of the detonators in the holes, the inter-hole delay, inter-deck delay and inter-row delay. Indeed, a single row of single-decked holes fired from a free-end simply requires the input of a single delay value – the inter-hole delay. Even a complicated blast with multiple rows of double-decked holes fired from the middle only requires the input of four numbers.
Once the design process is complete, the calculated initiation plan is presented on the tagger screen for final checking. A blast simulation can even be carried out on screen to check the firing sequence is as intended. The blast is fired by a combination of the tagger, blasting cradle and a blast key.
The blast key is an electronic device and requires the user to enter a unique six-digit password before the blast can be fired, giving enhanced security. Once the blast has been fired, a complete record, including detonator times and the initiation plan, can be downloaded from the tagger on to a computer for printing or archiving.
After successfully completing extended UK trials in both quarrying and civil engineering projects, the HotShot system is now being offered to all sectors of the UK explosives industry.
Exchem Explosives, Venture Crescent, Alfreton, Derbyshire DE55 7RA; tel (01773) 832253.