Bunker building partnership success
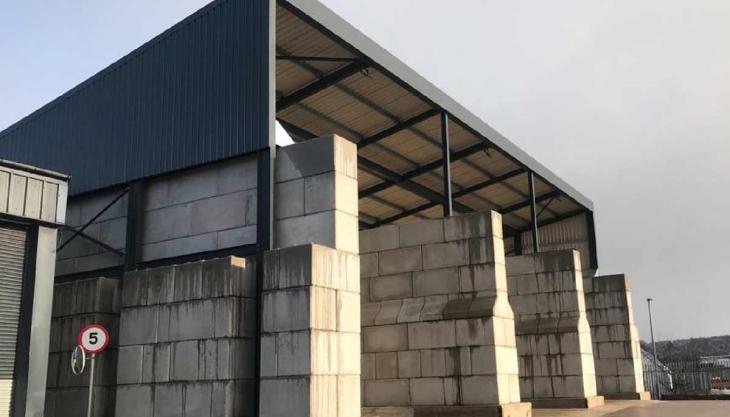
Elite Precast Concrete and RSG Structures join forces to deliver innovative bunker solution
RSG Structures operate as independent designers, suppliers and installers of a range of precast, pre-stressed concrete as well as traditional steel frame and membrane covers and canopies.
One recent bunker project involved a client requirement for high walls (6–7m) on an existing base slab of varying levels, together with a cover over the whole bunker structure. As the slab was in good condition, it made sense to utilize it, but the different levels meant that placing walls directly on to it would be an issue.
To overcome this, a plinth of varying height (0.4m at its lowest and just over 1.2m at its highest) was used to cater for the different levels of the slab, thereby allowing a level surface for walls and roof to be formed.
At the plinth’s maximum height, very few wall options available; L walls or horizontal panels are a possibility, but the foot on an L wall at this height is around 2.6m, which would increase the footprint dramatically, whilst panels would require either stub stanchions or a heavy-duty steel frame with correspondingly large foundations. Options for division walls are also very limited at this height and would not be particularly operator friendly, with feet or steelwork in the way.
Elite Precast say this is where their high-strength Legato block comes into its own. Each weighing 2,400kg, the standard blocks are cast from high-quality 50N/mm sq. concrete and measure 1.6m x 0.8m x 0.8m. The blocks are very simple to reconfigure into different heights and layouts, and when designed and installed correctly can form very large walls capable of taking large loads, including roof canopies.
Moreover, the use of double-thickness walls at the base allows the structure to take both product loading and the impact loading of the operating machinery with ease, whilst the division walls feature a self-cleaning ‘footblock’, which creates a very neat detail.
The cover for this structure was formed using a steel monopitch frame which is founded to the ground externally and to the top of the walls internally, and includes a spill flashing at the top of the wall.
Using this combination of products has given the client great flexibility, as the concrete plinth is the only part of the bunker complex that cannot be unbolted and taken away for reconstruction at another site.
Meanwhile, RSG Structures have announced the launch of an ‘industry first’ inspection service called SiteSafe. Where clients have existing walls constructed from interlocking blocks, timber sleepers, L shapes, panels etc, they can organize a SiteSafe report that includes a survey of current wall layouts, systems, types, designs and how the walls are being used.
The client receives a factual report noting where systems in place are working within their design capability, highlighting any areas of concern and recommending remedial actions to make their site safe, signed off by an RSG director and structural engineer.