Barnet Council uses recycled rubber asphalt
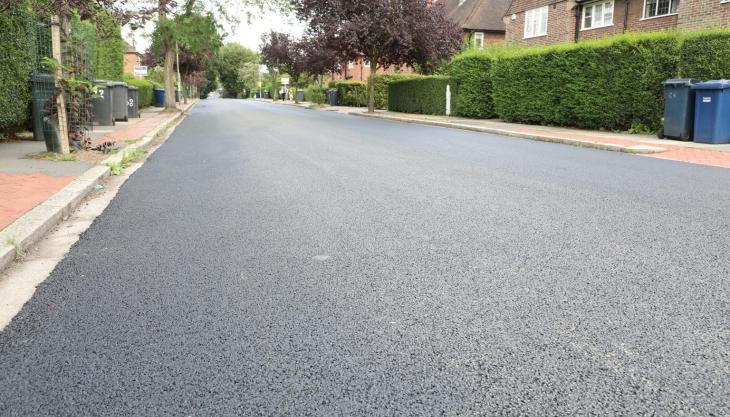
London borough helps drive climate agenda by maximizing use of waste tyres in highway works
BARNET Council is maximizing the use of rubber waste tyres while reducing embodied carbon within highways works, thanks to the use of new asphalt technology.
A road in the London borough was recently resurfaced by Tarmac Kier Joint Venture (TKJV), the contractor responsible for highways maintenance and improvements across the borough, using granulated rubber from end-of-life recycled tyres.
Tarmac’s ULTIPAVE R, a rubber-modified stone-mastic asphalt (SMA), uses warm-mix asphalt technology to achieve a reduced carbon footprint, typically 8% lower than the equivalent conventional SMA.
Around 240 tonnes of rubber-modified SMA was laid as part of a new surface course on Hill Top Road by the TKJV’s surfacing team in a single shift. The chosen surface used 35mm of 10mm rubber-modified SMA 40/60 with a polished stone value (PSV) 60 and incorporating steel slag aggregate, with rubber crumb added in place of fibres, and warm-mix binder.
Steel slag aggregate, sourced from Tarmac’s facility at its steel works in Port Talbot, South Wales, was transferred to London by rail to reduce embodied carbon and is classed as zero-CO2 rated.
Peter Hyde, Tarmac Kier JV board member, said: ‘Rubber modified SMAs offer a more sustainable option for local authorities. It’s extremely positive to see Barnet Council delivering environmental savings by leveraging this new technology and unlocking the benefits of a circular economic approach.’
Barnet Council trialled the use of recycled tyres for road surfacing as part of its commitment to building a borough fit for the future where residents and businesses can benefit from sustainable services, amenities, and infrastructure.
Councillor Peter Zinkin, vice-chairman of Barnet Council’s environment committee, said: ‘This approach in Barnet helps the council as part of its demanding sustainability strategy, while maximizing the reuse of end-of-life tyres which would have been exported as waste.
‘Materials’ technology in road resurfacing has moved forward and really significant improvements in the sustainability of road resurfacing are being achieved with our new joint-venture contractor and Tarmac’s materials skills.’
Depending on the thickness of the road surfacing, Tarmac Kier have calculated that up to 500 waste tyres could be recycled in every kilometre of road resurfaced with the ULTIPAVE R solution, helping to reduce the 120,000 tonnes of rubber waste, including 500,000 tyres, that are exported from the UK annually.
Approved for use on motorways and the strategic road network, the material is a high-performance asphalt using SMA technology suitable for most locations, from heavily trafficked motorways to rural roads. Using high-grade aggregates, it is said to deliver outstanding lasting texture, along with skid resistance and impressive reductions in road noise and surface spray.
The development of rubber asphalt is part of Tarmac’s commitment to sustainability, with the business recycling 7 million tonnes of waste from other industries every year. It also builds on the company’s reuse of waste tyres to power its cement kilns, and its commitment as a net user of waste.