Truly Captivating
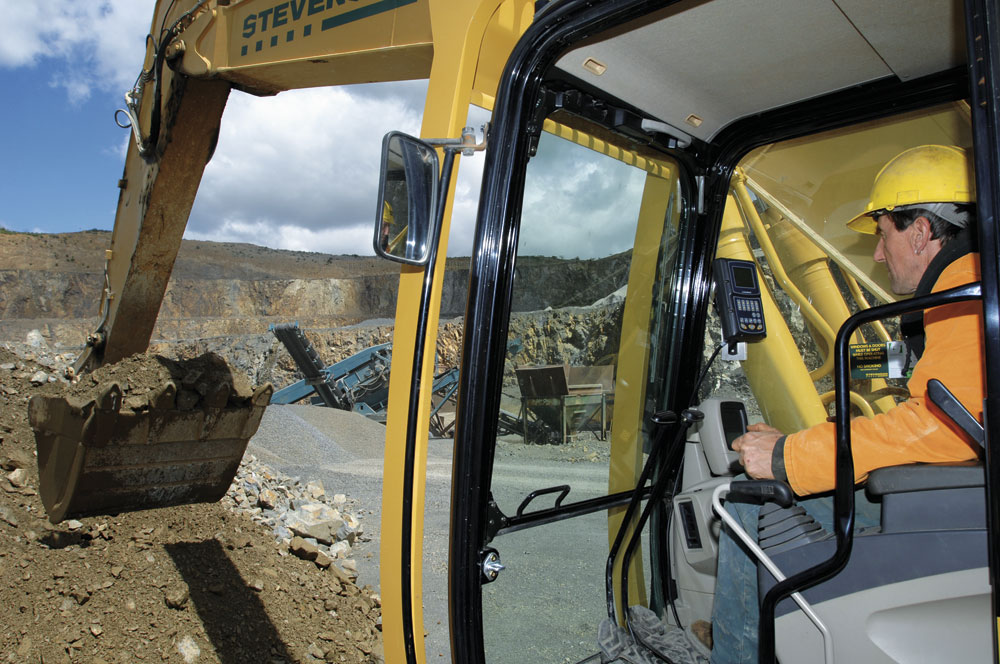
A new innovation in inventory tracking offers quarry companies a fresh way of scrutinizing their operations to improve efficiency, profitability and environmental performance. In this two-part feature, Julian Athawes looks at how the ‘Whole Site Solution’ from weighing specialists Loadrite is set to revolutionize process and cost management, from pit to load-out
In these times of recession and increasing global competition, the quarrying industry, like any other, needs to be leaner and more efficient. The challenge is even greater if the production line is fragmented and spread over possibly several kilometres, shaped by nature rather than neatly boxed by factory walls.
Accurate, continuous measurement and tracking of materials as they move along the ‘production line’ is a particular issue in the extractive industries. A significant part of the conveying process is mobile, undertaken by excavators working around the pit face, and by loaders and trucks making circuits around site.
Individually, these breaking, handling and hauling machines, plus the crushers, screens and conveyors in between, may be at the cutting edge. However, quarry managers have been missing an important tool: equally cutting-edge technology that can provide an integrated view, from pit to load-out, of how efficiently this largely free-form movement of materials is working.
It is this gap that Loadrite, a leading manufacturer of on-board scales, believe they can fill.
Whole Site Solution
With 30 years’ experience in precision weighing and inventory tracking for the quarrying industry, the New Zealand-headquartered specialists have devised the Loadrite ‘Whole Site Solution’.
The capability centres on powerful software, Loadrite’s Material Management System (MMS). This offers dynamic data storage and processing functions for analysing inventory volumes and their progress across the whole quarry operation, from extraction, through processing and production, to load-out.
Loadrite’s high accuracy scales – for excavators, loaders, conveyors etc – provide the building blocks of the system. While providing high-accuracy weighing, they have in-built inventory tracking to feed data to the ‘whole-site’ view of the MMS.
The detailed tracking of product moving down the line, both in terms of volume and speed, yields invaluable information on plant cycle times, downtime and individual machine outputs. With this seamless intelligence, quarry managers can identify and eliminate inefficiencies, small and large, such as mismatches in pit load-out and conveyor rates, plant under-utilization, re-weighs, slow cycle times and bottlenecks within the system.
This can shave significant amounts off operational costs as well as reducing a site’s carbon footprint. Clearly, accurate weighing and inventory tracking of load-out activities could reduce cycle times, resulting in fuel and tyre savings and a lower associated carbon footprint.
At odds
To some extent, the dynamic nature of the quarry environment has led to an entrenched informality towards inventory measurement that is at odds with an industry that works to world-class standards in other areas of its operation.
Measurement of inventory is often disjointed and incomplete, concentrating on some elements and not others. For instance, a quarry may be quantifying raw stone going into its primary crushers, but may not be monitoring what comes out and goes forward down the line. Measurements from monitored areas are sometimes applied to other parts of the process to generate estimates. This is not an ideal basis for identifying inefficiencies, making effective decisions on improvements and forecasting their impact on the bottom line.
By capturing cross-site data in a powerful management tool, Loadrite’s Whole Site Solution aims to change all this. The system draws together the company’s proprietary weighing solutions within the three main areas of a quarry operation – extraction, processing and load-out. The remainder of this article looks at how this approach starts to take shape in zone 1 – the pit, from the blast to the primary crusher.
Breaking down rock accounts for a large proportion of a quarry’s production costs. But, traditionally, little measurement is carried out within the pit of blast patterns and yield, which means this is an area where improved weighing and inventory tracking can bring quick and substantial returns. Weighing of inventory on to haul trucks also suffers from a lack of accuracy. This means that haul truck utilization is not optimized, and if significantly overloaded, can lead to a rapid rise in running and maintenance costs. For example, tyres on large dumptrucks costing upwards of £20,000 a set, need to be treated with consideration.
Banished
Changes in health and safety legislation have also had an impact, specifically the Health and Safety Executive’s SIM version 2: 13/12/2006 relating to ‘Face Heights and Safe Working Practices in Rock Quarries under the Falls from Height Priority Programme.’ This effectively banishes the use of wheel loaders from the pit face, leaving excavators to the job.
Prior to this change, state-of-the-art wheel-loader scales were capable of high-accuracy weighing of loads on to dumptrucks, but until recently there has been only limited choice in excavator scales, and none that have come anywhere close to providing the same level of accuracy and ability to operate without compromising speed of operation. Some quarries have resorted to using dumptruck scales which, while expensive, offer very limited accuracy and have to be fitted to every dumptruck on site.
By developing a high-accuracy excavator scale (the X-weigh 2350), Loadrite aim to revolutionize pit efficiency while realizing a crucial element within their Whole Site Solution.
Together with the Pit Boss tailored productivity reporting system, this innovative excavator scale will monitor blast efficiency, pit activity and haul truck performance. The Pit Boss stores essential data on blast piles and excavator output, as well as identifying loads and cycle times for specific haul trucks.
For the first time, quarry managers can accurately quantify and qualify the effectiveness of the blast in terms of overall tonnage and the proportion of good rock, oversize and overburden yielded.
Blast outcomes
Blasting companies normally cost output on a theoretical basis. Armed with detailed analytical data of actual blast outcomes from the Pit Boss, quarries have a more realistic basis for reviewing and negotiating costings.
They can examine blast patterns with the contractor to assess the ratio of materials produced and experiment with explosive specifications to improve blast quality and yield. This can help reduce the proportion of oversized rock that requires secondary breaking – a high-cost element of site production, especially if an extra machine is needed.
The Loadrite excavator scale plus Pit Boss solution will also optimize the loading of haul trucks. Dumptruck cycle times can be continuously measured to assess, for example, why an excavator may be incurring downtime waiting for trucks to return. The data will help flag whether downstream hold-ups are the cause, or possibly that the haul trucks need upgrading.
Sophisticated matrix
By feeding data from multiple machines working in the pit zone into Loadrite’s MMS productivity software, a sophisticated matrix of time-referenced site activity starts to build up.
It will accurately monitor multiple haul trucks and provide actual weights carried each time. It will measure the actual weight carried from the pit to the primary crusher in order to optimize efficiency and accurately calculate tonnes per man-hour costs. Loads can be tracked by material type, start point (or blast ID), truck ID and destination.
With powerful reporting options, the MMS delivers a valuable layer of management intelligence that can reveal hidden inefficiencies, highlight opportunities for subtle but productive changes, and improve the overall visibility of operating criteria that can help with cost rationalization.
With recession still entrenched in the UK, aggregate companies are looking closely at their cost base for even the smallest opportunities to save cost. But without a very tight rein on inventory at all points of production, quarry operators do not have a clear view of where their real weaknesses and problems lie. Relying on incomplete, inaccurate materials inventory data, and filling in the gaps through guesswork, can be misleading and result in expensive mistakes.
For instance, a bottleneck in production could be attributed to wheel-loader performance, suggesting the machine needs replacing. However, with the benefit of ‘whole-site’ inventory tracking, it might be found that the problem lies with the primary crusher not matching the capacity of the rest of the plant. With this insight, operators can accurately identify the problem, provide an evidence-based justification for equipment purchase, as well as being sure the right kit is replaced.
Strides
The quarrying industry is making great strides with onerous regulations and responsibilities relating to environmental performance, health and safety, sustainable operation and community relations. These often involve investment to ensure a quarry is operating legally and responsibly, and to make it commercially resilient in the long term. But they seldom deliver quick, easily measured returns that reflect immediately in the bottom line.
While it may not meet a legislative or regulatory need, Loadrite’s Whole Site Solution can provide the answers to a longstanding logistical challenge that will help the quarrying industry further tighten its housekeeping and enhance best practice. It also offers quarry operators an investment opportunity that will deliver the fast, substantial returns that they need right now.
Halomec Ltd are the exclusive distributors of Loadrite products in the UK. For further information visit: www.wholesitesolution.com
Part two of this article will examine how Loadrite’s Whole Site Solution links through the production/processing and load-out zones to maximize its contribution to cost control and productivity.