Prevention Is Better Than Cure
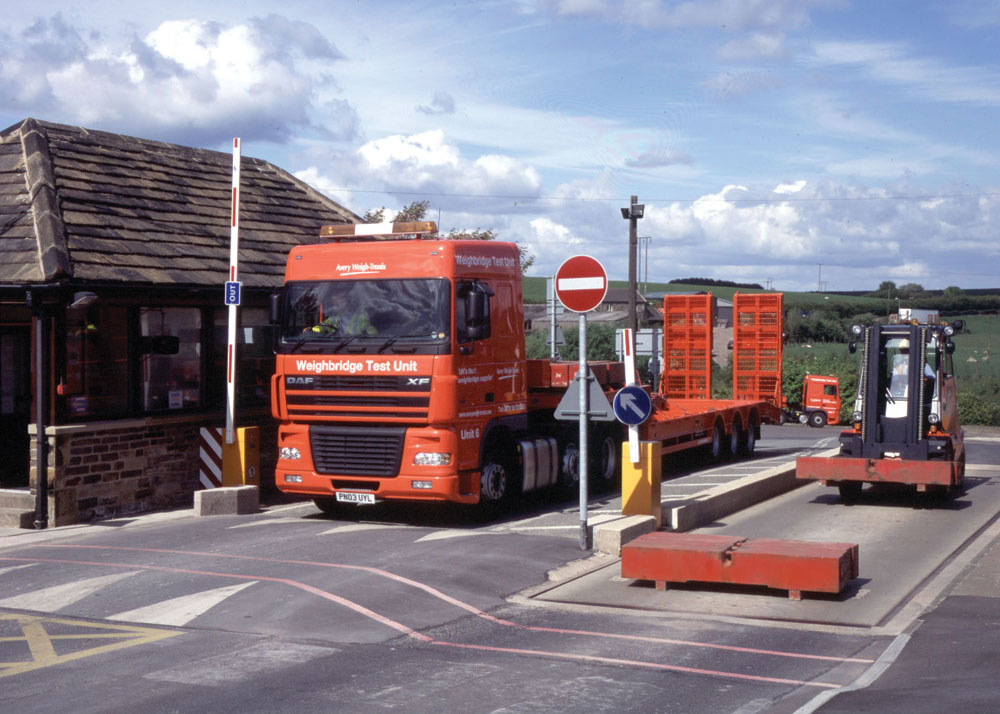
Weighbridge downtime can cost a quarry thousands of pounds an hour, so having an effective preventative maintenance programme in place is vital, argues Chris Thorpe, service manager for Avery Weigh-Tronix
Although accurate figures are hard to come by, probably 50% of quarries operate with a single weighbridge, so any breakdown of the weighing equipment can stop the whole site from operating. This means weighbridges are at the core of any quarry business. They are precision weighing instruments designed to meet stringent Weights and Measures regulations while operating in extremely harsh environments. They are the ‘cash register’ for the business and it is vital they remain operational.
Everyone agrees that prevention is better than cure but how many people actually put that principle into practice? Having the right service and maintenance agreement in place is essential, but there is much that weighbridge operators can do to ensure that equipment stays reliable. To do this effectively, however, operators need to be aware of the most common causes of damage or failure.
For example, if a load-cell or weighbar is left in water, or even in very damp conditions, it can fail prematurely. This is one of the most common causes of inaccurate weighing and leads to rejection by Trading Standards officers.
Another problem is shock loading, which can cause excessive movement of the weighbridge platform and may result in damage to the structure. This can be due to heavy braking by a vehicle, impact damage caused by a loading shovel, or by heavy loads being dropped directly on to the weighbridge or into a vehicle positioned on it.
Another common problem is electrical disruption, including mains-borne interference through the weighbridge indicator supply or a lightning strike, either directly or via dissipation when the surrounding ground becomes electrically charged. Modern weighbridge designs generally incorporate protection against lightning, both within the load-cell and through the fitting of lightning conductors, but it is important to check the weighbridge for damage after any thunderstorm.
Assuming that a quarry operator already has a maintenance contract in place and is aware of the most common problems, what else can be done to help keep the weighbridge operational and legally compliant? The answer lies in housekeeping and good practice, with daily, weekly, monthly and twice yearly tasks.
These simple tasks are important because an accumulation of dirt, debris, water or slurry will affect the integrity of the weighbridge. In the short term this will lead to inaccurate weighing, but if allowed to continue the load-cells or weighbars will fail, making the weighbridge unusable.
Daily tasks
On a daily basis it is best practice to visually inspect the platform to ensure that it is free from debris. Operators should check that the side and end frames are not fouled, and ensure that the digital display reads zero before a vehicle drives on to the platform.
Vehicles should approach the platform slowly, avoid sudden braking and, for an accurate weight reading, ensure that all the wheels are on the weighbridge.
For pit-mounted installations, if T-section rubber is fitted operators should check that it is located correctly and that any pit drainage system and/or automatic pumps are also working correctly. For surface-mounted weighbridges there should be adequate clearance between the superstructure and the ground.
Weekly tasks
Weekly tasks involve carefully checking the load-cell assemblies for debris build-up, which should be removed carefully without damaging the load-cell cables. Operators should also carry out a weekly weigh check using a loaded vehicle, comparing the vehicle’s weight when weighed at each end of the weighbridge with its weight at the centre of the platform. Any discrepancies of ±2 indicated divisions should be reported.
In figure 1 the weight is displayed in 20kg increments. At 25,980kg the weight is acceptable at –1 indicated division, but at 26,060kg on the front end of the platform it is unacceptable at +3 indicated divisions.
Monthly tasks
Pit-mounted weighbridges should be checked every month for possible ‘ponding’ of water, debris build-up or other damage to the leading edge of foundations and/or the side and end frames of the platform. If the platform has moved excessively since the last inspection it should be reported to the maintenance service provider.
Operators should also repeat the end-middle-end test, as detailed in the weekly tasks, and record the readings. The weighbridge should then be jet washed to remove any loose debris and/or any build-up of material beneath the platform, taking care to avoid the load-cells or weighbars. After this the weighbridge should be rebalanced reset to zero and the end-middle-end test carried out again. The results of these ‘before’ and ‘after’ tests should be compared and any discrepancies reported.
Twice yearly tasks
Once every six months operators should check for any signs of structural damage to the weighbridge. For example, foundations should be inspected for any significant movement or cracks and any sign of damage reported to the maintenance service provider. For surface-mounted weighbridges the load-cell cables should be checked and once again any damage should be reported.
Electrical welding should never be carried out on the weighbridge structure without first consulting the service provider, as this can seriously damage the load-cells or weighbars.
Preventative maintenance
With proper care a weighbridge will provide trouble-free operation between planned maintenance visits. However, operators should not get carried away with DIY servicing. Detailed repair or maintenance work should not be attempted as this may affect the weighbridge’s operation and contravene Weights and Measures regulations.
This is where a planned maintenance contract is essential, taking into account both the way a weighbridge is used and its frequency of use, as this varies from quarry to quarry.
Maintenance contracts should be flexible and able to meet operators’ specific needs. Avery Weigh-Tronix generally find that a basic package is satisfactory for a new weighbridge in its first year, with extra cover added progressively as the equipment ages.
A basic package will typically only include a scheduled preventative maintenance visit or visits, which could range from monthly to annually. Additional features could include emergency cover for breakdowns, labour costs for repairs, costs of parts, and even the replacement of load-cells or weighbars.
If replacement parts are fitted it may be necessary to get the weighbridge re-verified to ensure that it meet Weights and Measures legislation. Operators should check whether their service supplier can do this, as not all service and repair companies have the necessary skills, tools and experience.
To meet due diligence obligations it is also recommended that the weighbridge is calibrated regularly – at least once a year. Again, a maintenance service provider should be trained and qualified to offer this service.
If the worst should happen, operators should also check their contract for service response times. Even in the remotest regions of the UK an 8h response time is achievable and much shorter response times should be available for critical operations.
Conclusion
A weighbridge is one of the most important elements of any quarry business. If it is not functioning properly operators risk mismeasurement, which usually leads to under- or overcharging and poor productivity and efficiency figures. Worse still, if the problems build up and the weighbridge becomes inoperable, it could slow down or even close the entire operation.
Ultimately, there is the nightmare scenario of non-compliance with Weights and Measures and the risk of legal action by Trading Standards, with all the damage this inflicts on the operator’s reputation, not to mention the direct financial losses.
Even though a weighbridge may look like a simple, robust, heavy-duty piece of kit that can look after itself, a few minutes spent on basic housekeeping each day, an hour each week and a couple of hours each month will make a significant contribution to the reliable, trouble-free operation of the ‘cash register’.
Operators should also make sure that their service and maintenance contract is up to date, covers everything they need and is with a supplier who has trained people available on the ground to respond quickly and professionally.
For further information contact: Avery Weigh-Tronix, Foundry Lane, Smethwick, W. Mids B66 2LP; tel: (0870) 90 50061; email: info@awtxglobal.com