Logistics Management Solutions
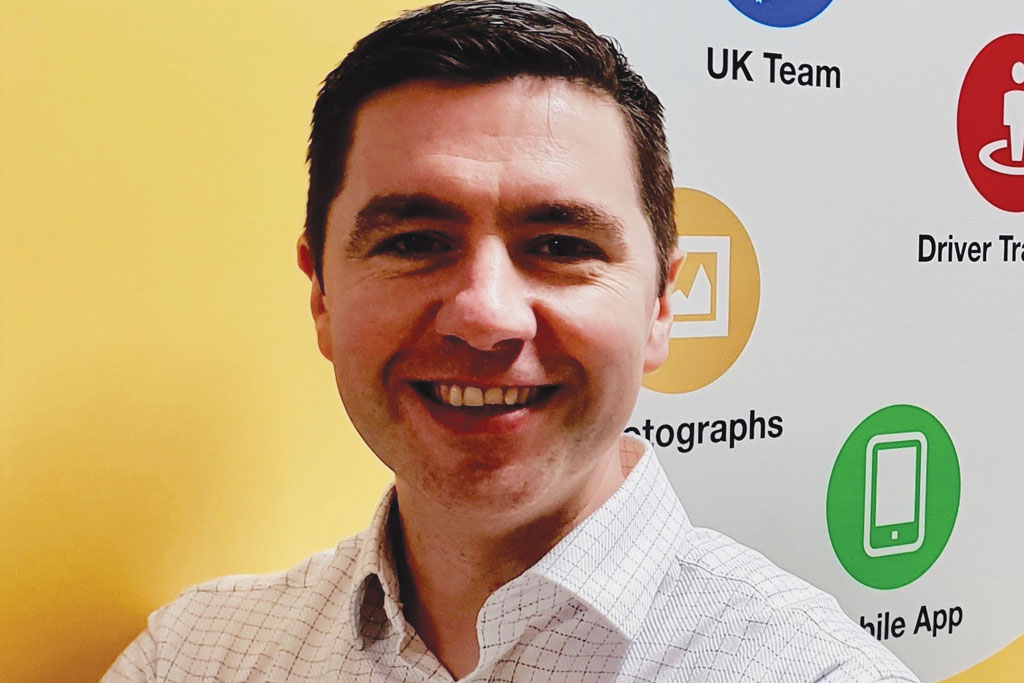
First published in the April 2019 issue of Quarry Management as Smarter Deliveries
Colin McCreadie, managing director of PODFather, believes site delivery strategies for the quarrying industry should focus on the smartphone and not paper-based documentation, to improve visibility.
The collection and delivery scheduling of raw building and construction materials from the quarry to the construction site needs to look closely at its supply chain fulfilment strategies.
Does a ‘paper trail’– the traditional method of signing-off transported loads – still have a place within the quarrying industry? Or, like any number of home delivery services, can the transportation of quarried material adopt seamless cloud-enabled tracking and proof-of-delivery technologies? This move is critical to achieving quite substantial and often complex operational efficiencies.
Delivery loads used to be identified by paper tickets and tallying them up at the end of a day would give the number of loads delivered. There is now broad acceptance that electronic proof of delivery, or ePOD, is key to optimizing logistics procedures rather than trying to reconcile paper documents against a lorry load of building material.
Paper-based delivery fulfilment is giving way to easy-to-deploy apps on standard Android or iOS (Apple) devices. It is now extremely rare for anyone not to have a smartphone in their pocket, making it easy to email a customer with an ETA and a signed electronic delivery note within seconds of delivering product or materials.
Tarmac have rolled out ePOD technology across their 1,800-strong UK vehicle fleet, providing instant access to electronic proof-of-delivery tickets and real-time tracking for customers across the country in the latest stage of their digital-transformation journey. The system uses sign-on-glass technology and accurate live updates via smart mobile devices, providing seamless integration, greater visibility and traceability for all material deliveries from quarries to construction sites.
Generating millions of delivery tickets every year, Tarmac have now created a streamlined, robust and paperless administrative process by giving their drivers mobile devices preloaded with PODFather’s ePOD software. Moreover, this has been extended to cover the company’s subcontract fleet, so it too can record a detailed and chronological log of each delivery; including routing information, dates and times, and details of signatories, which can be accessed remotely via a single portal.
This was a phased roll-out, beginning in Tarmac’s North and Scotland region in October 2018, followed by the South and South West region in November and concluding with the Central region at the start of December.
Helping smooth the bumps in the road
ePOD can help with road-surfacing processes by communicating the ETA and live tracking position of each delivery vehicle to the people who need it most; the operators of the road-paving machinery.
Asphalt loads delivered at timely intervals are required to continuously feed the paving machine to produce smoother, better-quality road surface. Accepting that there can be delays in either asphalt production or traffic between a plant and delivery location, communication of these delays using intuitive and real-time technology can help the paving crew decide if they should start work, maintain current speeds or slow down to allow the next load more time to arrive before the paver runs out of material and an additional task to join loads of material together is required.
Ready-mixed concrete delivery works on almost the same premise and communication of delivery information can aid site staff in their own logistics management and site activity.
Delivery workflows can be customized through the ePOD system to ensure drivers capture the right information based on the type of delivery being carried out. For example, you may wish to automatically record the amount of time spent on site to help resolve disputes about excessive waiting time. You may also wish to capture photographs of deliveries completed if there is no one available to sign.
There can be different delivery workflows for different types of job. How and where asphalt is delivered may differ to how ready-mixed concrete is delivered, so it is important that drivers always capture the right data. Bespoke intelligence can be built into ePOD system workflows to, for example, warn the driver the volume of water added to a load of ready-mixed concrete is going to exceed BSI standards.
More than just proof of delivery
A number of health and safety benefits can also be integrated into ePOD apps, such as capturing safety incident reports on site and reporting this back to a safety manager – all done in real time.
Communication regarding issue resolution can also be reported back to the driver. This is equally important as more people are encouraged to report faults if they feel they are being listened to, and when the faults are rectified, they feel a sense of responsibility that what they reported has been acted upon.
Daily vehicle checks are another paper-based process than can be improved using ePOD. These checks can be enforced through the app before a driver leaves the depot and before they can see their delivery jobs lined up for that day, thereby improving compliance procedures.
If a fault is reported on a vehicle, the functionality in ePOD can escalate this to the transport manager so they know to arrange the necessary repairs in advance, thus potentially reducing the amount of time the vehicle is off the road.
Vehicle- as well as customer-specific checks that go beyond the usual DVSA requirements can be incorporated. This is important because a lot of construction projects require higher standards of vehicle safety on site. Crossrail, Thames Tideway Tunnel and HS2 are just three high-profile projects that are helping improve vehicle safety standards in the construction industry. Ensuring your vehicles, and those of your sub-contractors, are compliant with these exacting standards can be the difference between working on these projects, or not.
Efficiency savings all round
Often, attitudes are slow to change. Many smaller independent transportation businesses are still largely reliant on paper documentation to complete deliveries because they are tied into the processes and procedures of their customers and suppliers.
For the supplier, reducing administration and eradicating paper handling will make significant savings. From the customer’s point of view, receiving a notification at the start of the working day detailing exactly what will be delivered and when it will arrive at their site gives them a chance to run their sites more efficiently.
Construction site traffic flowing in and out of busy developments might offload hundreds of building material loads every day, so the auditability of electronic proof of delivery is vitally important. When delivery loads have been signed for, a supplier will know who signed it, when and where it was signed for, and, if required, be able to offer photographic evidence. In other words, full track-and-trace visibility.
The level of data even extends to the precise co-ordinates pinpointing where each load has been deposited on the site, something that could not be discerned from the information on paper tickets.
At weighbridges too, there is no need to invoke a paper ticket trail. A customer signing for a load will receive email confirmation through the company’s accounts processing systems, once again cutting out the administration of dealing with a piece of paper and allowing the supplier to invoice the job faster and improve cash flow.
The quarrying industry no longer needs to issue paper tickets for collections or deliveries; the entire process can be streamlined. Just pull your smartphone out of your pocket to start the journey. For more information visit: www.thepodfather.com
- Subscribe to Quarry Management, the monthly journal for the mineral products industry, to read articles before they appear on Agg-Net.com