Recycling Revamp At Rookery Farm
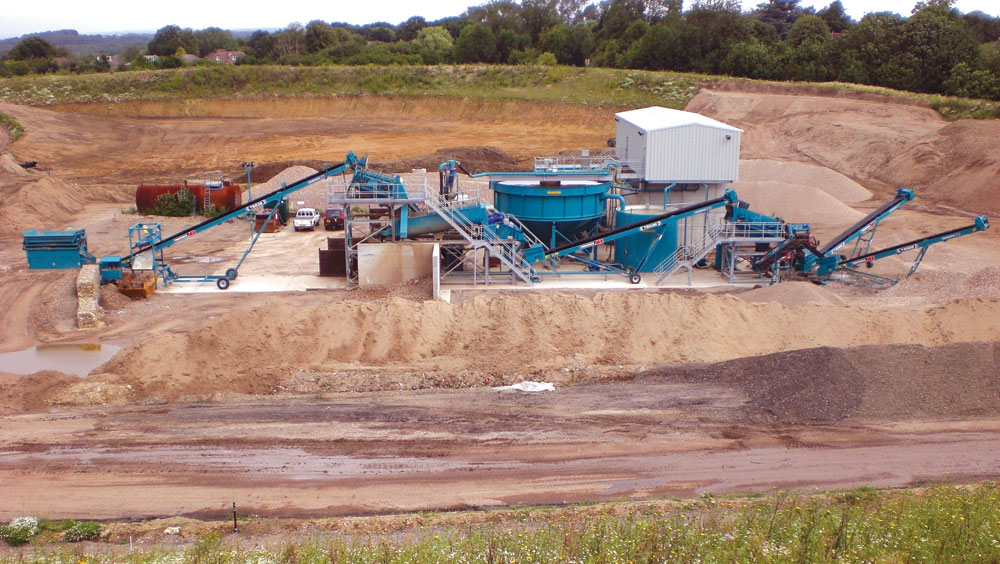
New washing plant produces high-spec recycled aggregates and saves water
Raymond Brown Group recently formed Raymond Brown Minerals & Recycling Ltd specifically to focus on the related businesses within the company. Their operation at the Rookery Farm Landfill and Recycling site, close to Swanwick, near Fareham, in Hampshire, has recently seen the design, construction and commissioning of a modern, ecologically and environmentally friendly washing plant.
Based on Powerscreen equipment working in tandem with a highly specialized silt-management system from Haith Industrial, Raymond Brown’s new washing plant is now producing high-quality, clean aggregates and clays to specification and, significantly, has resulted in considerable reductions in water usage, settlement pond maintenance, and wasteful and costly landfill tipping.
Landfilling at Rookery Farm started in the 1980s, with recycling at the site beginning in 1995 with the crushing and screening of waste concrete. In 2002, a pilot washing plant was installed to develop the production of clean recycled aggregates. The limited silt recovery system at that time required large volumes of water and, when considering a new and more sophisticated washing plant for the site, Raymond Brown focused on enhanced silt recovery to produce quality clays as well as a way of effecting a major reduction in water wastage.
Additionally, a key element of the new plant was to achieve a long-term planning life of at least 15 years to justify the investment. The new plant, supplied and installed by Blue Machinery Southern, is not only capable of attaining Raymond Brown’s target of 65,000 tonnes output of aggregate per annum, plus silts and clays, but has also significantly reduced water consumption at the site. According to Raymond Brown Minerals & Recycling Ltd, the new plant is now fully operational and meeting their high expectations.
Rookery Farm itself is well located for both sourcing raw materials from the surrounding area and easily reaching the markets for the clean, high-quality recycled aggregates and clays produced. In developing and investing in the Rookery Farm plant, the company had to meet stringent planning controls, paying particular attention to the impact on local residents, ecological considerations, highways and traffic, noise and dust reductions, and the landscape.
Steve Cole, environmental & development director for Raymond Brown Minerals & Recycling Ltd, commented: ‘We undertook a major revision of the site layout, constructed an internal acoustic screening bund around the washing plant, increased other screening bunds around the site – all now planted with trees, and re-routed transport away from sensitive boundaries to reduce the site’s impact on the surrounding area. In addition, the washing plant is powered by a fully sound-insulated generator system.’
He continued: ‘Blue Machinery Southern came up with a strong proposal and, coupled with our already excellent and long-standing relationship with the company and the build quality of the Powerscreen equipment they distribute, our choice was obvious. We are looking to move recycling up the value chain and our new plant at Rookery Farm is helping us to achieve this very satisfactorily.’
Recycled materials now being produced at Rookery Farm include: concreting sand; a range of aggregates for pipe bedding; drainage and low-strength concrete; and bulk-fill crushed concrete materials for capping and sub-base. The silt cake produced by the Haith Industrial silt management system is still being assessed and tested for a variety of potential uses, including puddle clay for canal and riverbank work, landfill capping and a soil base with blended compost materials.
The new washing plant comprises a series of Powerscreen machines working in tandem, starting with a Commander 1400 belt feeder equipped with a vibrating grid featuring 60mm heavy-duty fingers. This feeds on to a Powerscreen 6532 feed conveyor equipped with an overband magnet to remove any contaminating ferrous metal fragments.
The feed conveyor discharges on to an 8ft x 4ft double-deck rinsing plant which removes the 0–5mm sand and +40mm oversize and discharges the remainder into a Powerscreen 120 log-washer. This is fitted with a trash screen to remove light waste, wood and plastic from the aggregates, while a wash deck gives the –40mm +5mm products a final rinse.
A Powerscreen 5032 conveyor delivers the aggregates to the final 10ft x 5ft screen, which splits the material into –10mm +5mm, –20mm +10mm and –40mm +20mm, with three conveyors stockpiling the different products.
The sand is processed through a Powerscreen Finesmaster 60, which dewaters the material prior to stockpiling via another conveyor.
The sophisticated water-treatment system at Rookery Farm comprises a thickener tank with an automatic flocculation system, a polyelectrolyte dosing station, a sludge stocking tank with sludge pump, and a Haith overbeam filter press equipped with 1,500mm x 1,500mm plates for cake production. A clarified water tank with pump recycles the clean water back to the washing plant.
The installation is powered by a 500kVA generator, supplied by Woodlands Generators of Evesham, and the central control system for the entire plant has a PLC control panel located in a lockable steel container.
Overall, the new plant has vastly reduced water consumption and settlement pond maintenance through the recycling of process water and with the addition of ground-level tanks that collect spillage water and rainfall. According to Raymond Brown Minerals & Recycling, the site is now 90–95% self-sufficient with regard to its water requirements.
All civil engineering work at Rookery Farm was undertaken by Raymond Brown Construction Ltd and the project benefited from a grant from the Waste & Resources Action Programme (WRAP) under the Capital Grant Scheme, based on a five-year performance agreement. Landfill operations at Rookery Farm have been deferred until recycling ceases.