New Inner-City Asphalt Storage Solution
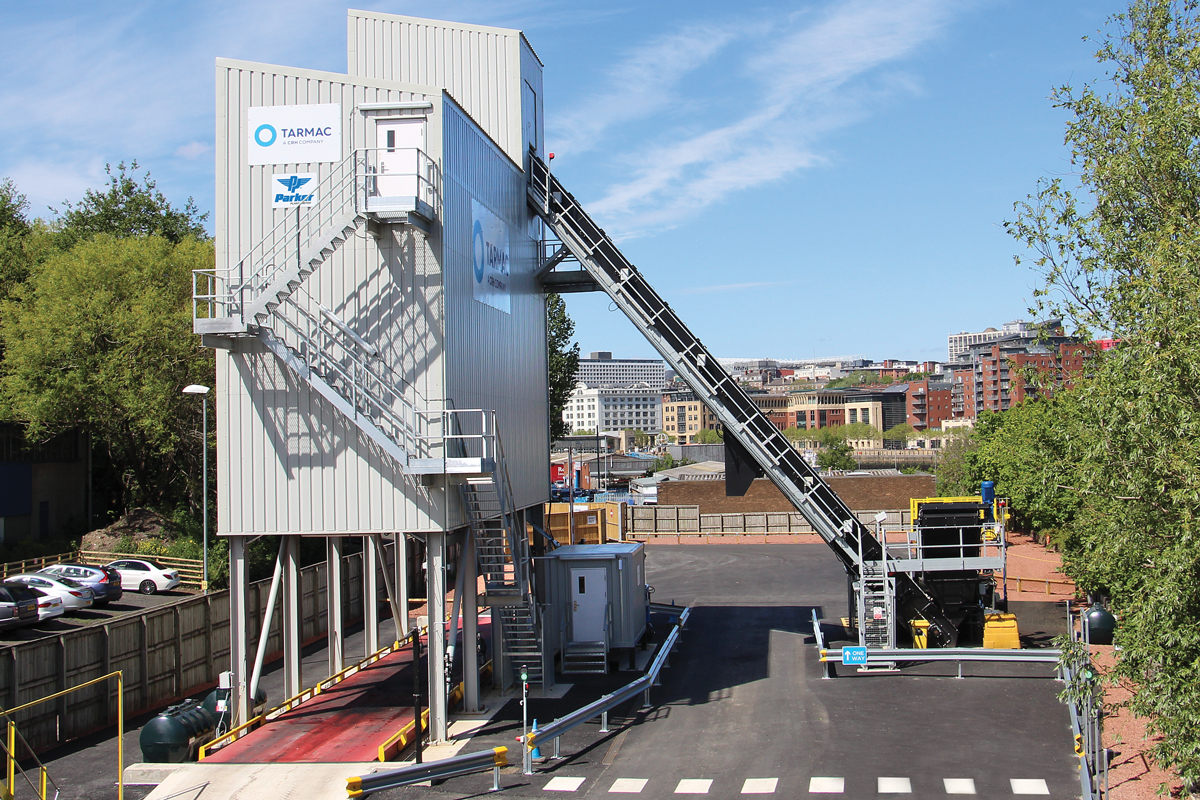
First published in the July 2019 issue of Quarry Management
Parker Plant have recently installed a satellite mixed-material storage system for Tarmac’s Asphalt2Go operation near the centre of Gateshead
The facility operates on the principle of providing rapid local access to ‘pre-mixed’ asphalt for immediate use in Gateshead, Newcastle and the surrounding area. Mixed material from Tarmac’s existing asphalt plants situated outside the Tyneside conurbation is brought to the site in the early morning or late at night to avoid daytime urban road congestion. The system stores mixed material at the correct temperature and its central location provides councils and contractors with instant access to high-quality ready-made asphalt for use in building, repairing and maintaining local roads, along with projects ranging from driveways and cycle-paths to pavements and car parks.
At the opening ceremony, the then Mayor of Gateshead, Councillor Jill Green said: ‘We’re delighted that Tarmac have chosen to open up this new facility in the east of Gateshead, providing the council and others with access to heated asphalt quickly and without fuss. This new venture is ideally located to help local businesses access this material, which will help meet the daily challenges faced by construction professionals.’
John Riley, Tarmac’s area director for the company’s materials business in the North East, added: ‘We are very excited about our new Asphalt2Go site in Gateshead. It underlines our commitment to providing a convenient supply of local material which will help support the local council and other customers to deliver surface repair and construction activity with greater ease.’
Imported mixed material is delivered to site and discharged into a surface-mounted ground hopper. Large side augers and vibrators on the hopper bed move the material into a wide-bodied, twin-chain slat feeder which discharges into the main slat conveyor. An adjustable, hydraulically operated gate controls the feed rate into the slat feeder.
The hopper and slat feeder conveyor bases are both electrically heated to minimize temperature loss. Stainless steel is used for the bed of the hopper and the flights of the auger to assist in cleaning. The base wear plates for the auger and slat are fabricated from chromium carbide.
After the truck has fully discharged into the hopper, the front section of the hopper bed is hydraulically tilted to a high angle, which clears any residual material from the hopper. A grid which tilts with the hopper provides added protection from the moving parts while still allowing free flow of material. A galvanized access platform facilitates maintenance to the head of the slat feeder.
The main twin-chain drag-slat conveyor is driven by a shaft-mounted motor and gearbox and the bed is fitted with chromium carbide floor plates which are electrically heated and insulated. The casing of the drag slat is made from a single fabrication, ensuring alignment of the bed plates, and galvanized access walkways each side of the casing provide access for maintenance purposes. The top of the drag-slat conveyor feeds into a batch hopper with pneumatic discharge doors which batch the material into a horizontal skip. The batch hopper and the horizontal skip sides are insulated and the batch hopper doors are electrically heated. The skip, in turn, feeds into any one of four internal 50-tonne mixed-material storage silos, as required.
The entire storage system has been designed with regard to thermal efficiency. Each 50-tonne silo is insulated with 200mm of high-density mineral wool. The pneumatically operated silo inlet doors are also insulated and fitted with grease seals to remove any gap between the door and the silo top, thereby reducing heat loss. The silo discharge doors are electrically heated, further improving operational efficiency.
The cone section of each silo is also fitted with electrically heated blanket insulation and insulated secondary doors underneath the cone completely enclose the insulated bottom section of the silo when not discharging. This aids thermal efficiency and provides additional safety.
The silos use twin outlets which are spaced to evenly spread the load into the width of the receiving truck. This also allows the filling of individual compartments in twin hot boxes. For the customer, this means that each hot-box compartment can have a different grade of asphalt loaded from two different silos.
The silos and associated equipment are integrated within a fully sheeted fabricated structure of pre-assembled steel sections which can be erected rapidly. The silos are insulated and fitted out at the factory before being transported to site as single items, thus reducing site installation time. Lockable doors into the building and lockable fence guards at the bases of the staircases prevent unauthorized access. Access is via a main staircase with secondary access via the walkway on the side of the main slat conveyor. The silo tops are fully guarded along their length for safe operation.
Translucent sheeting along the sides at the top of the structure provides ample illumination during daylight hours and internal lighting is provided for night-time use. Special attention was paid at the design stage to minimize gaps in the sheeting where the main drag slat enters the structure.
A vehicle weighbridge is situated beneath the storage silos for accurate loading of trucks via the computerized control system. The weighbridge is surface mounted, thus avoiding the need for a pit, and is fitted with wheel guides for the receiving trucks.
The facility is fitted with external lighting on the feed hopper, around the silo discharge area and along the sides of the main drag-slat conveyor to allow night-time operation.
The plant’s electrical starter panels are incorporated in an air-conditioned motor control centre adjacent to the plant to minimize electrical cable runs. Remote computerized control of the plant is from a customer’s control room some 80m away.
Other features of the control system include two large screens to display all aspects of the material flow from the feed hopper to truck load out, assignment of material recipes to different silos to eliminate contamination and load-out errors, continuous monitoring of storage silo levels, product temperature display and voice alerts of plant alarms in plain language. Once a truck has been loaded with the desired mix recipe, the truck driver automatically receives a receipt prior to leaving the weighbridge.
To further assist the plant operators, CCTV cameras are located at the receiving hopper, batch holding hopper, skip platform and under each of the four storage silos.
One of the main challenges of the project was the site’s location on the bank of the river Tyne, close to the water level. This forced all construction to be kept above ground level, ruling out any subsurface workings such as a sunken feed hopper or truck load out. However, an added benefit of surface-mounted construction is that the whole plant is sited on one level, which simplified the installation and eliminated any delay arising from additional groundworks. Another key factor, as with many other inner-city developments, was the size and shape of the plot available. In this instance, there was not enough space for the normal positioning of the feed hopper in line with the main conveyor and at 90o to the storage silos. The solution was to rotate the hopper and feeder at right angles to the main slat conveyor to fit the site footprint, so that delivery trucks can discharge alongside the main plant without interfering with load-out operations.
The hopper and feeder were fabricated in one piece, fully assembled and tested and then transported to site as a single item, thus reducing installation time. The main drag-slat conveyor was also fully assembled before being transported to site as a single item, further minimizing installation and commissioning time.
Parker Plant’s installation and service director, Tony Butler, said: ‘I would like to thank the Tarmac engineering team, local management and plant operatives for their contribution to the success of this project.’
- Subscribe to Quarry Management, the monthly journal for the mineral products industry, to read articles before they appear on Agg-Net.com