New Benninghoven Plant For Whatley Quarry
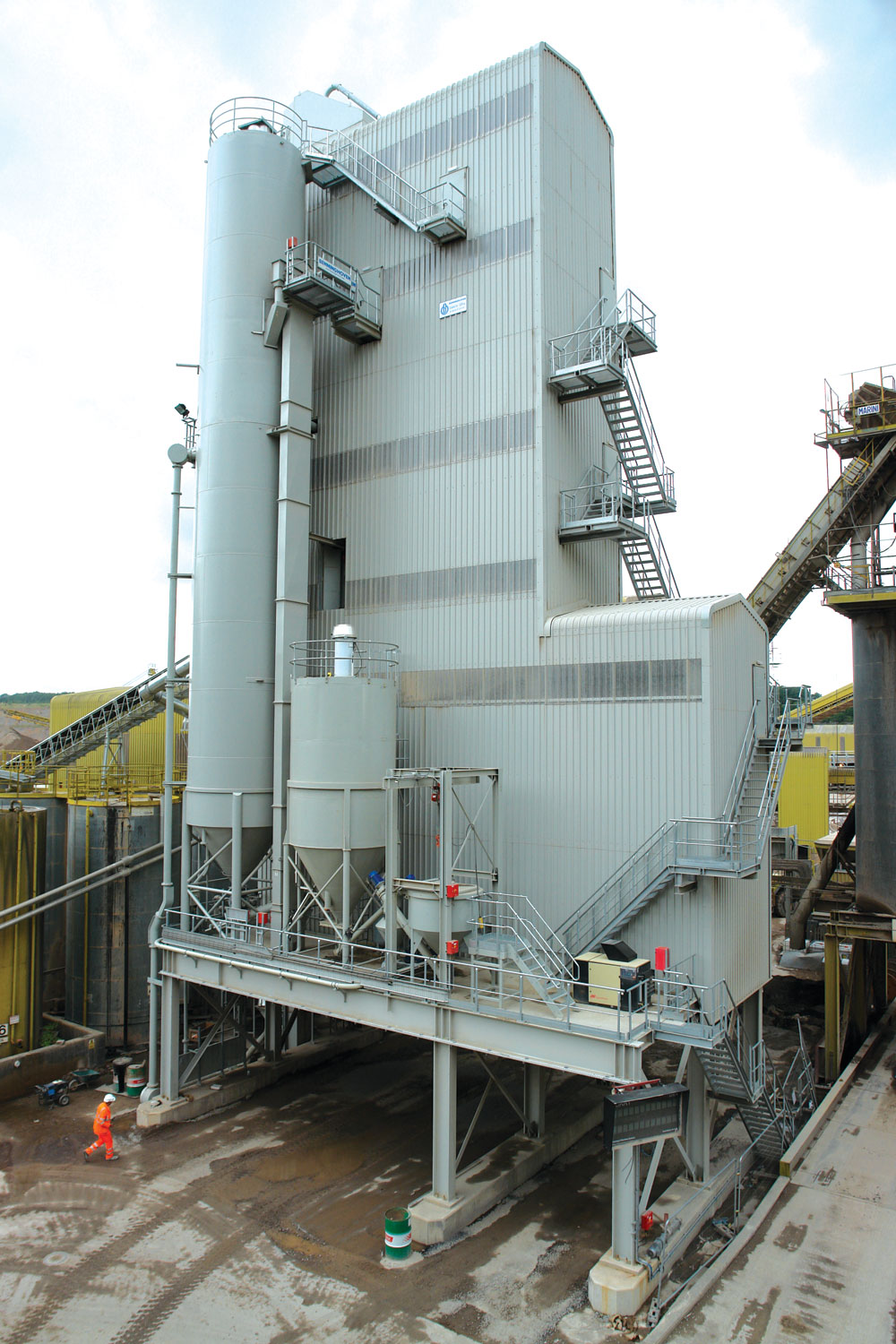
Major facility upgrade at one of the UK’s largest quarrying operations
Whatley Quarry lies at the heart of the UK’s biggest limestone-producing area in the east Mendips, Somerset, and is one of the largest quarrying operations in the country with an output approaching 4 million tonnes a year.
Operated by Hanson Aggregates, a division of the HeidelbergCement group, the quarry supplies crushed rock by both road and rail to markets throughout southern England, and asphalt by road as far afield as Devon, Dorset and Hampshire.
Major investment in a new asphalt plant at Whatley is part of an £8 million upgrade to improve productivity and efficiency at the quarry, and to realign the production process with changing market requirements.
The decision to purchase a 320 tonnes/h Benninghoven asphalt plant was made in order to provide significant operational benefits and cost savings. The plant has a production output of over 320 tonnes/h of dense basecourse at 4% initial moisture, and 200 tonnes/h of 14mm stone-mastic asphalt (SMA). The facility allows Hanson to cater for the wide variety of mixes required by their customers and also to produce material in small batches in a cost-effective and efficient way.
From the initial discussions, Benninghoven’s technical engineers worked closely with Hanson Aggregates in supplying advice and proposal drawings at all stages of the planning process.
Hanson’s area operations manager, Phil Oddy, commented: ‘The new plant, in conjunction with our existing asphalt facility, will give us the flexibility to produce a wider range of products with improved quality control, and to meet all local authority specifications.’
The new plant utilizes the site’s existing rotary dryer system, which feeds the existing Marini asphalt plant. The discharge point of the dryer has been modified to incorporate a new two-way chute that can deliver hot aggregates on to a new 14m long transfer conveyor fitted with a high-temperature, heat-resistant belt, which in turn feeds directly into the Benninghoven plant’s vertical bucket-type hot-stone elevator.
Elevator drive is by a 55kW geared motor and toothed chain wheels at the elevator head. The elevator features outside-located bearings and a safety backstop facility, while a wide platform provides ease of access for maintenance purposes.
Material discharged from the elevator passes into a six-deck screen featuring four 10.6kW ‘bolt-on’ low-maintenance vibrating motors. These drive units are mounted outside the screen housing to allow the high-temperature screening of materials. Wide access doors, together with a rollaway chute provide access to all screen decks.
The hot aggregate section provides a total of 150 tonnes of storage, including the bypass, divided into two lines of six bins with a changeover chute. The bins are all insulated and clad, and each is fitted with a continuous level indicator and overflow chute. A temperature probe is fitted in the sand and dust bins. Discharge is via pneumatically operated radial doors, which accurately regulate material flow to the aggregate weigh hopper, from where the aggregates are discharged directly into the mixer.
Accurate weighing of ingredients is achieved by separate load-cell-mounted weigh hoppers, comprising a 4,000kg capacity aggregate hopper, a 600kg filler hopper and a 480-litre capacity weigh vessel for bitumen. An injection pump forces the bitumen into the mixing unit, which comprises an insulated, 4,000kg capacity, twin-shaft paddle mixer, with drive provided by two 55kW geared motor units. A radiation pyrometer is situated at the mixer discharge to indicate mix temperature.
Mixed material discharged from the mixer falls into a 4,000kg skip unit, which runs on horizontal tracks and distributes the material into three 75-tonne insulated compartments.
All are equipped with high-level warning indicators and fitted with electric trace heating around their discharge doors. A direct load-out hopper of 20 tonnes is positioned beneath the mixer, and all bins are mounted on load-cells to ensure accurate material loading.
As part of the upgrade of the bitumen system, the existing 60,000-litre tank and pump was relocated next to the four tanks currently supplying the continuous plant, together with new fill and discharge pipework on all tanks.
Filler is stored in an external, two-compartment, vertical silo, mounted on a steel support structure, that holds approximately 95m3 of reclaimed filler and 50m3 of imported material. Both compartments are equipped with level indicators and shut-off valves and full aeration facilities.
A gravimetric additive system is also incorporated in the plant to feed granulated material from a 30m3 silo. Each batch of granulate is accurately weighed in a load-cell-mounted weigh hopper before being discharged through a butterfly valve to the mixer. A smaller 3m3 capacity silo for pigment is sited alongside and discharges via a screw conveyer to a weigh hopper.
Modifications were made to the current recycling system, which entailed the removal of the existing scalper/crusher and replacement with a stainless lined chute. In addition, a transfer conveyor was installed to transport materials from the existing recycling hopper to the weigh conveyor, which feeds the recycled material (mainly granulated asphalt) to the mixer via a belt weigher to give proportional batch blending. An extraction duct transfers any steam into the dust-collection system when operating with recycled materials.