Major Investment For Leiths Group
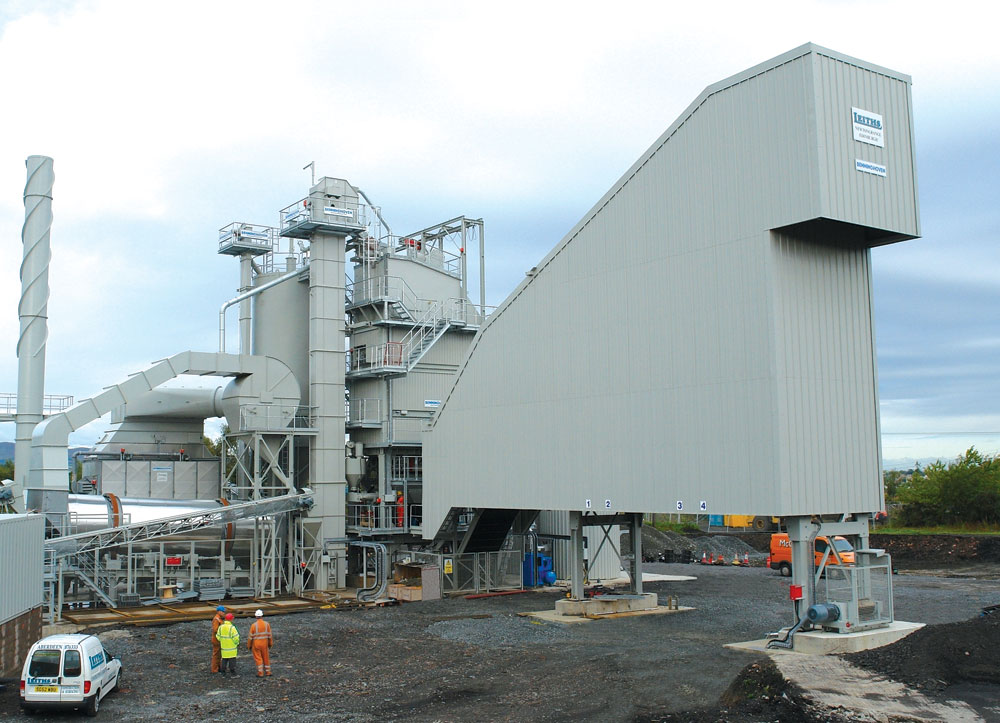
New Benninghoven coating plant for Newtongrange
Leiths (Scotland) Ltd are a family owned construction and construction materials group who have expanded in recent years to become one of the largest independent companies in this sector in Scotland.
The company operate 13 quarries throughout the country supplying materials to their seven coating plants and an expanding ready-mixed concrete and precast concrete business. The group also includes Markon, a major supplier of road marking and planing services, and Lawrie, a specialist demolition company. A large proportion of Leiths’ coated stone output is supplied to their in-house contracting and surfacing arm, which now operates throughout Scotland.
Recognizing that much of Scotland’s growth in construction and infrastructure continues to be focused in the Central Belt, in 2006 Aberdeen-based Leiths secured planning permission for a new state-of-the-art asphalt plant, together with a ready-mixed concrete plant, at Newtongrange, near Edinburgh. The site was previously part of the Lady Victoria Colliery and is strategically placed to serve both the local Edinburgh market and all major infrastructure projects in the region.
‘Much of Edinburgh’s future development is likely to take place to the south of the city and Newtongrange will allow our surfacing arm to expand into this important market,’ said chief executive Simon Russell. ‘This is a major investment for the group and underpins our strategy of adding value to our existing resources.’
To achieve the necessary mix specifications, production targets and the environmental criteria, Leiths selected a Benninghoven TBA240 asphalt plant equipped with a 3,000kg mixer. Capable of delivering a wide range of standard and specialized mixes, the plant offers a production output of up to 240 tonnes/h of dense basecourse at 4% initial moisture.
Design parameters for the new plant called for an installation that would provide a high level of flexibility in terms of mix specifications together with on-demand volume production. Also, because of its urban location, particular emphasis was placed on the plant’s low-profile image and on compliance with stringent local environmental controls.
The mixing tower itself comprises individual pre-built modules that are installed in set positions to form the tower structure. Benninghoven say this configuration allows for standardization of components and provides greater reliability with minimum maintenance.
The aggregate cold-feed system, provided by Leiths, consists of two four-bin units, each bin being fitted with a frequency controlled belt feeder for accurate blending of the aggregates. Two of the hoppers are for sand and are equipped with hopper-wall vibrators to ease material flow, and each of the hoppers has been designed to accommodate 80 tonnes, thereby ensuring optimum direct tipping by delivery vehicles and minimizing the need for ground stocks. The hoppers are sheeted on their sides, ends and roofs to prevent dust emissions when loading and to keep material stocks protected from the weather.
A 10m long x 650mm wide inclined dryer feed conveyor, equipped with a belt weigher to control-plant feed rate, discharges on to a 3.5m reversible slinger conveyor, which in turn feeds the dryer. A vibratory scalping grid with 70mm apertures, mounted beneath the feed conveyor head, is used to reject any oversize material.
The aggregate dryer drum, which is manufactured from 12mm Abro steel and measures 2.4m diameter x 9m in length, is insulated and clad for heat retention and noise reduction, and is fully flighted with Benninghoven’s high-efficiency lifters. The drum is friction-driven by four support rollers through individual 18.5kW frequency inverter geared motor units.
The burner is a Benninghoven Rax Jet 4 model, which can operate on both oil and natural gas. It is equipped with a full range of operating and safety devices to deliver high-efficiency fuel usage. In addition, an air inlet silencer is connected to the burner to suppress noise levels, and the burner and silencer are mounted on a track to allow the unit to slide back from the dryer for routine servicing.
The plant’s dust-collection system is rated at 64,000Nm3/h and achieves emission levels of less than 20mg/m3. A centrifugal-type primary skimmer unit mounted alongside the dryer separates any coarse dust from the airstream, which passes to the hot-stone elevator feed boot via a gravity flap valve and chute. A secondary cassette bag-filter system collects any remaining dust and transfers it, via a screw conveyor, to the filler elevator and into the reclaim silos. Dust is also collected from nuisance points at the screen, weigh hoppers and elevator, while a dust monitor mounted on the exhaust stack provides a remote read out in the operator’s cabin.
Any excess dust collected can be discharged from the reclaimed dust silo through a rotary valve into a twin-shaft paddle conditioner, into which water is introduced through spray nozzles. This provides an environmentally friendly method of purging the excess reclaimed dust.
Hot aggregates are transported from the dryer up to the screen by a vertical bucket-type elevator. This is totally enclosed and features a heavy-duty double-strand chain and wear-resistant steel buckets with replaceable liner plates at impact points. Elevator drive is by a 22kW geared motor and toothed chain wheels at the elevator head. The elevator features externally located bearings and a safety backstop facility, while a platform and wide inspection doors allow for easy maintenance.
Material discharged from the elevator passes on to a six-deck screen featuring two 19kW low-maintenance bolt-on external drives, to allow for high-temperature and superheated mixes when the plant is using recycled materials. An extraction fan ensures negative pressure is maintained within the screen housing for optimum dust control. The screen is also fitted with a by-pass facility.
The hot storage section has a total capacity of 80 tonnes and comprises eight bins, including two fines bins for asphalt sand and crushed rock fines. All the bins are insulated and clad and each is fitted with continuous level indicators and an overflow chute. Discharge is by pneumatically operated radial doors, which accurately regulate material flow to the aggregate weigh hopper.
Accurate weighing out of ingredients is achieved by separate load-cell-mounted weigh hoppers – a 3,000kg capacity aggregate hopper, a 600kg filler hopper and a 300-litre capacity weigh vessel for the bitumen. Rapid and thorough mixing takes place in an insulated, 3,000kg capacity, twin-shaft paddle mixer, with drive provided by two 37kW geared motor units through synchronized gears. All lubrication points are centrally located to aid routine maintenance and a radiation pyrometer is situated at the mixer discharge to indicate mix temperature.
Bitumen is supplied from three electrically heated and insulated tanks that provide a total storage capacity of 260 tonnes. These are filled using the latest pumping and control system, which ensures the safe transfer of bitumen without pressurization of the road tanker. A 900 litres/min injection pump is used to force the bitumen into the mixer
Mixed material is discharged from the mixer into a 3-tonne skip unit, which runs on an inclined track and distributes the material into four storage silos of 320 tonnes total capacity. All four are equipped with high-level warning indicators and are insulated and fitted with electric trace heating around their discharge doors. The silos are mounted on load-cells for accurate material loadout.
Imported and reclaimed filler is stored in a 100m3 capacity, three-compartment vertical silo. All three compartments are equipped with level indicators and shut-off valves, while three screw conveyors transfer the filler from the silo direct to the weigh hopper.
A cold RAP system for granulated asphalt has been incorporated in the facility to deliver precise percentages into the plant mixer. The system comprises a steep-sided, 10m3 capacity feed hopper fitted with a grid and vibrator. A belt feeder mounted beneath the hopper discharges on to a 21m long transfer conveyor, which feeds into the elevator feed boot hopper.
Both the plant tower and mixed material storage are sheeted to minimize noise and to provide a pleasing aesthetic appearance to the whole plant.
Plant control is via Benninghoven’s advanced on-line Batcher 3000 computer system, which displays all plant functions via colour graphics. This system, which offers the latest hardware within a user-friendly package, is housed in the customer’s existing control centre overlooking the plant. The system is modem linked and provides storage for up to 500 asphalt mix recipes.
The plant was supplied, installed and commissioned in compliance with current CDM and UK health and safety regulations by Benninghoven UK Ltd, with Leiths acting as principal contractor on site. Other site facilities at Newtongrange include twin 16.5m x 3m 60-tonne Avery weighbridges, a laboratory and workshops. A ready-mixed concrete plant is currently in the design phase.
Summing up the new coating facility, Simon Russell said: ‘The plant and the site has been designed with a rapid turnaround for our customers as an essential feature. What was a derelict site has been brought into a second useful life. The plant was commissioned in November 2007 and we are now servicing the market. All in all, it has the makings of a sound investment for the company.’
Acknowledgement
The editor wishes to thank Simon Russell, chief executive, and Louie Gray, production director, of Leiths (Scotland) Ltd, and Nigel Moreton of Benninghoven UK, for their help in preparing this report.