Dry Mining Cornish China Clay
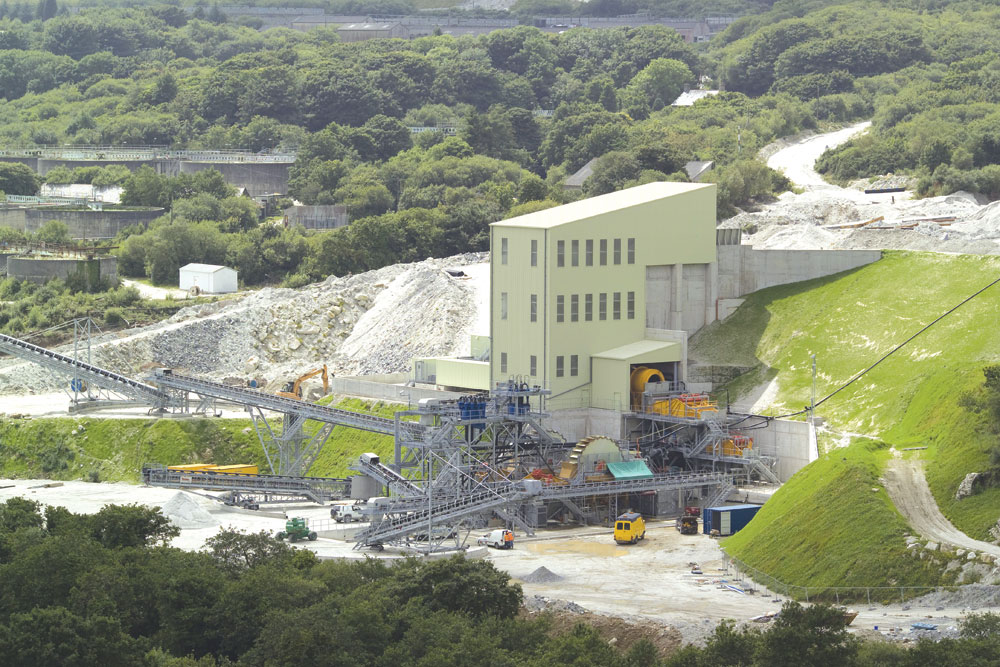
Imerys switch from traditional wet extraction methods to a dry mining process at two mines in their Western Area kaolin operations
Imerys, the world leaders in industrial minerals, have recently invested £6.9 million to convert the operation of two of their largest china clay quarries in Cornwall from traditional high-pressure wet extraction into classical extraction and processing of the kaolinic matrix in a central washing plant. This allows the company to have greater control over its variable costs and reduces the impact of energy price increases. It also reinforces Imerys’ commitment to ensuring Cornwall remains an essential element of the company’s global kaolin production portfolio.
Cornwall is a county known for its historical mining heritage. Unlike its tin and copper mines, however, the extraction of Cornish kaolin is one of the few significant mineral processing industries remaining in Britain today.
Kaolin came to prominence in the mid-18th century when its value as a component in white porcelain was recognized by Plymouth chemist William Cookworthy. He first discovered kaolin deposits in Cornwall in 1746, at Tregonning Hill, near Helston, and two years later found even more extensive deposits in the St. Austell area. Cornish kaolin was found to be not only abundant, but also of an exceptional quality with properties that would ensure its use in a wide variety of industries throughout the developing world.
Soon, leading potters and ceramic producers began to mine their own pits. Wedgwood started Treviscoe Pit – the industry’s oldest operational site – in 1785 before selling it to the Martyn family, one of the three largest kaolin producers who amalgamated to form English China Clays Ltd in 1919.
Imerys acquired English China Clays plc in 1999 and today the company operates 120 mining sites in 47 countries worldwide, producing 29 different minerals or mineral groups. Imerys’ Western Area kaolin operation, located in mid-Cornwall, near St. Austell, produces in excess of 500,000 tonnes of kaolin per annum, making it one of the largest mining operations within the Imerys group.
Traditional methods
Traditional ‘wet mining’ has always been the standard method of kaolin extraction in the UK. It begins with the removal of topsoil, which is used for landscaping, after which the overburden covering the kaolinized granite matrix is loaded on to large dumptrucks and taken to a local tip. The kaolinized granite is then charged with explosives and blasted, before being pushed into piles by bulldozers ready for washing by a high-pressure monitor (water hose). The resulting mixture of water, kaolin, sand and mica forms a slurry which flows to the lowest point of the pit. It then passes through a series of mechanical classification systems to remove any unwanted sand and mica before being pumped to the surface of the pit by centrifugal gravel pumps.
Over the years, however, the china clay pits have become much deeper and extraction has become more dependent on energy to pump the large volumes of water and clay slurry to the surface. This has prompted Imerys to move to a dry mining operation at two of their quarries in the Western Area, whereby the matrix is transported to a central washing plant for processing, in order to extract the kaolin.
Dry mining process
Designed to process several million tonnes of matrix a year from the Melbur and Virginia quarries, the new plant operates six days a week and is shut down one day a week for routine maintenance. By processing this volume of matrix, Imerys are able to recover a significant quantity of saleable product, the difference being that the waste streams of rock, gravel, sand and mica are removed at various stages of the dry mining process. This change makes it possible to revisit the way mining operations are conducted, in particular in terms of grade definition and the level of in-pit selectivity.
During the day a fleet of 65-tonne payload dumptrucks transport the matrix to the washing plant, where they either tip directly into a feed hopper or into one of the storage bays where stockpiles are built and then subsequently used during the night. This allows the plant to remain operational 24h a day.
To achieve maximum recovery from the wide range of feed material delivered to the dry mining site, the process is fed at different rates and controlled by the speed of the apron feeder situated at the bottom of the feed hopper. For example, a semi-kaolinized, low-yield matrix feed will be processed at almost twice the hourly rate of a well-kaolinized, high-yield matrix.
From the apron feeder, the matrix drops on to a reinforced grid where any oversize rocks (+800mm) are trapped and subsequently broken with a hydraulic rock breaker. Material passing through the grid travels over a grizzly feeder where it is blasted with high-pressure water to break up the material. The oversize rock is discharged from the grizzly feeder into a jaw crusher, while the crushed material is transported by belt conveyors before being stockpiled by a radial conveyor.
The underflow from the grizzly feeder is fed into a rotary washing barrel where the majority of the kaolin is released from the matrix. The rotational speed of the barrel can be changed depending on the type of matrix that is being processed. Semi-kaolinized material can be passed through the barrel fairly quickly, whereas a highly-kaolinized material requires more work input to release the kaolin. The mix stays in the barrel for approximately 60s, although this is adjustable to suit specific conditions through the use of a variable-speed drive.
Having passed through the washing drum the material is separated into gravel and finer fractions of clay, sand and mica by means of a drain screen. The gravel is then washed on a wash screen to remove traces of clay and sand before being transported by belt conveyor to a radial conveyor for discharge to a stockpile.
Meanwhile, the clay, sand, mica and water from the drain screen flows into a sand-separation system comprising two bucket wheels and two dewatering screens.
The kaolin and mica is removed as a slurry and pumped to a bank of 12 primary cyclones, where the majority of the mica is removed to leave a final clay slurry comprising 0.2% +53 microns, which is pumped to the refinery for further classification and processing.
The underflow or residue from the cyclones can be added to the sand on the bucket wheel dewatering screens, from where it can be conveyed to the sand stockpile or pumped directly to a mica residue dam.
The sand that has been separated on the bucket wheels is dewatered on the dewatering screens and conveyed to the radial spreaders. Here, it is stockpiled ready for transportation to waste tips by the mobile plant fleet. Sand is the single largest waste stream derived from the original matrix and can be generated at a rate in excess of
300 tonnes/h.
The system has been designed to operate as economically as possible, particularly in terms of water usage. With this in mind, there are many recirculation facilities within the process that can be used to maintain high-density final product; ie several tank overflows can be used for make-up water supplies further upstream in the process.
Imerys worked closely with Fairport Engineering Ltd to develop and implement the new dry mining operation and appointed the company as principal contractor. Fairport are one of the few organizations in the UK who can claim to be both a consultant and contractor with both minerals-processing and materials-handling expertise, and capabilities available from in-house resources, which was one of the main reasons why Imerys commissioned Fairport to assist with an initial feasibility study.
During the early stages of the project Fairport undertook formal design reviews and risk assessments that allowed a detailed installation plan to be developed and implemented during the course of the project’s construction. The partnering approach adopted with Fairport allowed both parties to enjoy a high level of visibility in apportioning project risk and reward, and has formed a significant part of a continuing smooth and productive relationship.
Summary
Against a background of rising energy costs, the ‘dry mining’ project has allowed Imerys to keep their production and energy costs under control, and to offer their customers in the ceramics industry products with the same quality and technical know-how at a controlled price.
Imerys’ long-term commitment to their UK kaolin business is demonstrated by their recent £35 million capital investment programme, of which the move to dry mining in the Western Area represents 20%. Cornwall remains an essential element of Imerys’ global kaolin production portfolio, with around 88% of its annual production exported to more than 60 countries.
For further information, contact Mathieu.Parfait@imerys.com or LWhite@Fairport.co.uk