Concept Change At Cross Green
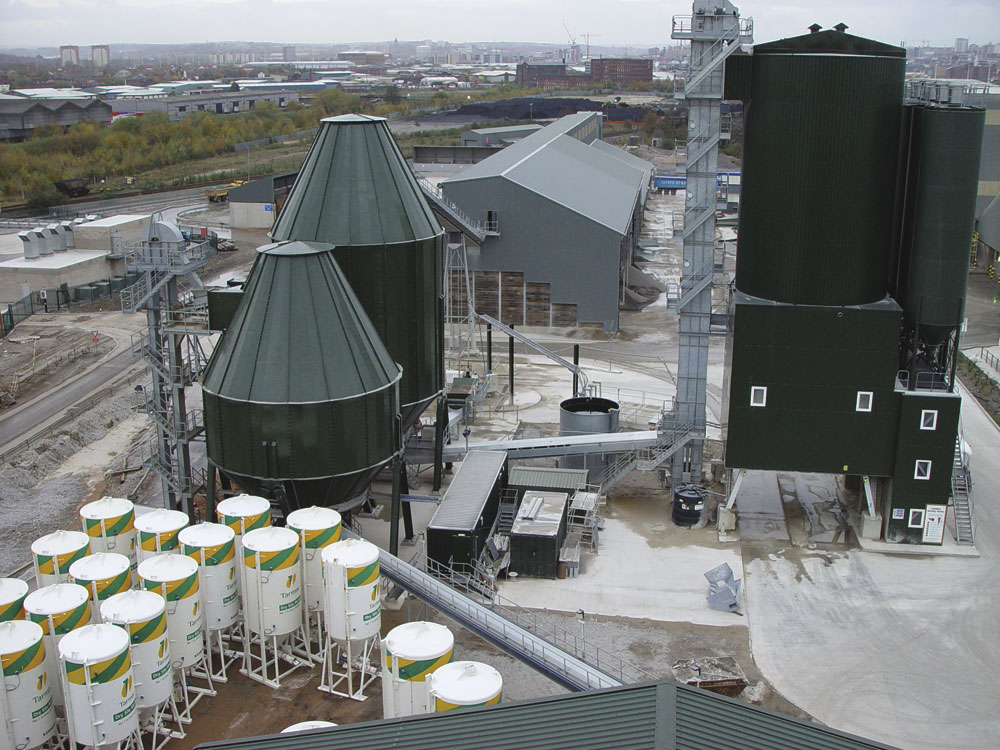
Tarmac pave the way for a new generation of dry silo mortars
The production of ‘dry mortar’ on an industrial basis has been common practice on the Continent for over 20 years but is still a relatively new concept in the UK. However, with the construction sector showing an increasing interest in the use of dry mortar, Tarmac have been quick to embrace the idea and since the late 1990s have been investing heavily in dry silo mortar (DSM) production technology to meet the uplift in demand.
Today the company’s traditional pre-mixed mortar business is complemented by a total of four new cutting-edge DSM plants, and a further two plants are planned. The new plants are capable of producing a full range of lime-based dry mortars, both natural and coloured, to exact customer specifications.
The key to the success of the DSM concept is the use of mobile silos to deliver pre-mixed dry mortar to site, whereupon simple connection to site power and a water supply provides the customer with ready-mixed mortar on demand. Specially adapted truck chassis equipped with a hydraulic lift system are used to transport and place the free-standing DSM silos in position on site where they remain for the duration of the supply contract. During the contract the DSM silos can be topped up with additional dry mortar delivered by road tanker, and at the end of the project the silos are collected and returned to the DSM production facility for cleaning and maintenance.
The increasing number of DSM silos that can be seen appearing on building sites across the country is testament to growing popularity of the product as an alternative to traditional site-mixed or pre-mixed mortars. This is largely due to the many on-site benefits that DSM provides, including: instant availability; consistent mix quality; minimal wastage; no risk of contamination; no retardation problems; reduced site traffic and manual handling; and increased flexibility, productivity and site efficiency. Moreover, any unused dry mortar left over at the end of the contract can be returned for recycling.
Cross Green expansion
One of the latest dry silo mortar plants to come on stream in the UK is at Tarmac Northern’s Cross Green depot in Leeds. Commissioned in July 2003 and representing a £3.9 million investment, the plant serves markets across northern England but especially along the A1 corridor from Barnsley to Newcastle. Markets further north are served by Tarmac Northern’s other recently established DSM plant at Uddingston, near Glasgow, which is identical in almost every respect to its counterpart in Leeds.
The Leeds DSM plant, however, represents just one part of a much wider expansion of the former Tilcon/Raisby Quarries’ coated-stone facility, a joint-venture operation that was first established at the Cross Green site in 1993. Since 2001 current owners Tarmac have invested in excess of £9.0 million in the brownfield site, transforming the former 7-acre asphalt and dry stone distribution facility into a 20-acre consolidated site that also incorporates dry silo mortar and ready-mixed concrete. The site is also includes a recycling centre operated by Tarmac Recycling, as well as a fully automated, rail-fed cement distribution facility run by Tarmac Central.
Cross Green’s expansion programme was also facilitated in part by a £1.3 million Section 8 Rail Grant from the Strategic Rail Authority, which helped fund an extension to the 2,000 tonnes/h rail-unloading facility used to deliver aggregates to the site’s new concrete plant. Currently up to six trains a week, each carrying 1,800 tonnes, deliver limestone aggregates direct from Swinden Quarry.
This ability to import large volumes of material by rail was one of the key drivers in Tarmac Northern’s decision to locate a new ‘high-output’ ready-mixed concrete plant at Cross Green, capable of producing and supplying up to 1,000m3 of concrete a day.
Built at a cost of £1.4 million and commissioned in August 2003, the 28m high plant has a minimal footprint thanks to the use of a vertical bucket elevator to feed the integral storage facility. This holds up to 800 tonnes of coarse aggregates and concrete sand ready for batching, while binder products (OPC and ggbs) are stored in four 100-tonne silos located adjacent to the plant. The mixing section comprises two separate production streams — a 1.5m3 Liebherr pan mixer capable of producing up to 60m3/h, to meet the needs of the collect trade, and a 3.0m3 Liebherr twin-shaft paddle mixer capable of supplying up to 140m3/h for delivery to market by truckmixer. Both streams have their own dedicated batch-control system and weighing facilities, and both utilize the latest microwave technology for moisture measurement/compensation.
Allowing for variations in daily radial miles, the concrete plant is more than capable of servicing 16–20 truckmixers (up to 8m3) while still maintaining an efficient collect business. Meanwhile, any concrete returned to site is discharged into a concrete recycling system to recover the sand and gravel. Process water is also captured and reused within prescribed limits.
The increased rail capacity at Cross Green also serves to ensure an adequate feed supply to the site’s two existing 440 tonnes/h Parker coating plants as well as the new dry silo mortar and ready-mixed concrete plants. Associated with this was the significant expansion of the site’s original delivery, transfer and storage arrangements, including the construction of four covered ground storage bays in addition to the existing 12-bay toastrack structure. Efficient and flexible aggregate supply to the concrete, mortar and asphalt plants was achieved through extension and uprating of the 2,000 tonnes/h overhead tripper conveyor, the installation of a new Benninghoven six-bin cold-feed system, and the creation of 10 additional ground storage bays (both covered and uncovered) for high-PSV aggregates, concreting aggregates, Type 1 sub-base, fills etc.
In addition, dedicated storage facilities were provided for the concrete and dry mortar plants, utilizing Skako’s patented ‘High Silo’ system to create maximum storage volume within a minimal footprint. Two High Silos have been installed, one subdivided into five compartments to provide 1,600 tonnes of storage capacity for 10mm and 20mm concrete aggregates and limestone fines, and the second smaller vessel providing segregated storage for 400 tonnes of concrete sand and 400 tonnes of building sand.
The aggregate High Silo is fed via a new conveyor link from the toastrack tripper conveyor, while the adjacent sand High Silo is charged via a drive-over dump hopper and bucket elevator arrangement. The dump hopper is fitted with an automatic covering system that opens when a truck arrives and closes when its load has been discharged, thereby ensuring the sand is free from contamination and excess moisture. Extraction and distribution of sand and limestone to their respective production processes is via Skako vibratory feeders and covered conveyors.
DSM production
By thermally drying building sand to remove all excess moisture, powdered and granulated binders, pigments and other admixtures can be added, mixed and then stored as a dry mortar for several months without risk of the product ‘going off’. Because the process uses totally dry materials throughout, no liquid waste is generated at the production facility and any solid waste can be returned for recycling.
Building sand extracted from the High Silo is conveyed to Cross Green’s fully enclosed DSM production plant at a rate of 60 tonnes/h and fed into a gas-fired fluidized-bed dryer supplied by the Dutch firm Ventilex. Designed to accept sand containing up to 10% moisture by weight, the dryer incorporates a drying section and a cooling section, with a vibratory action throughout to help maintain material movement. During a 30s residence period the sand is heated to 500°C and cooled to an exit temperature of less than 50°C, resulting in a guaranteed exit moisture content of less than 0.5%. Any dust generated during the drying process is collected by a Ventilex bag-filter system and fed back into the dried sand.
On exiting the dryer unit the sand passes through a small oversize protection screen fitted with a 6mm mesh deck. This protects downstream processes from oversized material while the underflow reports directly to a belt and bucket-type sand elevator. Screw conveyors are used to transfer the dried material from the elevator’s high-level discharge into four 100-tonne capacity bulk storage silos. These are grouped together with four similar-capacity, pneumatically filled silos for the bulk storage of binder materials (currently OPC, PFA and hydrated lime). In addition, two dedicated 50-tonne capacity silos cater for returned dry mortar; this is blended into new dry mortar mixes as and when mix designs permit.
Dry pigments and admixtures are stored in 2-tonne ‘pencil’ silos (six for pigments and four for admixtures, although not all of the silos are currently in use). These thin silos have been cleverly located in the voids between the larger bulk silos to make best use of available space in the DSM building.
Accurately controlled weighing and blending of four basic synthetic iron oxide pigments (red, black, brown and yellow) allows mortar to be produced in 108 different colours.
All the silos in the DSM plant are fitted with silo-management systems to monitor material levels, prevent overfilling, guard against over/under pressurization, and minimize the risk of material spillage. Apart from the four sand silos, which are gravity-fed, all the others are pneumatically filled via an intricate but clearly labelled network of fill pipes. Silo discharge to the batch weigher is controlled via a system of manual isolation valves and electro-pneumatic control valves.
With a maximum batch size of 4,500kg, the pre-weighed ingredients are discharged from the batch weigher into a 3m3 capacity German-built M-Tec single-shaft paddle mixer. A 4min mixing cycle is sufficient to produce a fully homogenized dry mix which is discharged into a holding vessel (blow pot) from where it is pneumatically delivered, at a controlled rate, to the final-product storage facility. This comprises six 100-tonne capacity silos mounted above a vehicle load-out bay equipped with a weighbridge. Both mixing and load-out are fully computer controlled by an M-Tec batch process control system, which also provides full traceability of ingredients and stock control.
The loading of tankers and dry silos is via a totally enclosed, zero-spillage loading spout. Once a vehicle is in position on the weighbridge, the tare weight is recorded, a load is dispensed under full computer control to prevent overfilling, and the sales ticket is printed. Cross Green currently operates one ‘lugger’ vehicle to transport the 22.5m3 capacity dry silos to site and has three tankers available for subsequent refilling. At present, Tarmac Northern have some 300 dry silos in service (split between Cross Green and Uddingston) but the company plans to increase its total inventory to 400 units by the end of 2005.
The silos themselves measure 7.2m in height and have a 3m x 3m footprint. They are delivered with approximately 14 tonnes of dry mortar on-board but when filled to capacity can weigh up to 35 tonnes. Each silo is equipped with a low level sensor to indicate when additional mortar needs to be ordered. Installation on site is quick and simple, requiring nothing more than a suitable concrete base with adequate access, together with a 240V electrical supply and a water supply at a minimum 2 bar pressure. Once connected, at the press of a button water is added to the customer’s specified dry mortar mix and the blend is mixed and discharged using a mixing unit manufactured by WAM Group of Italy. This unit is mounted beneath the silo and provides instant workable mortar. When no longer required on site the DSM silo is returned to Cross Green for cleaning, repair and maintenance prior to subsequent deployment.
The DSM plant itself is fully clad and features a double insulated roof to minimize the effects of internal condensation. To aid cleaning, the entire building is served by a central vacuum system with flexible hose connections at each floor level.
Throughout the expansion programme at Cross Green Tarmac Northern’s appointed managing contractor, Fairport Engineering, worked closely with the various sub-contractors including Canning Conveyor and Skako on the mechanical handling and storage elements, M-Tec and Ventilex on the DSM plant, and Liebherr on the concrete plant. Given the scale and complexity of the project, not to mention the diverse nationalities of the personnel involved (including British, German, Danish and Dutch operatives), it is testament to the skill, experience and effectiveness of the management team, and indeed the commitment of all those involved, that the entire project was completed on schedule and without a single lost-time incident.
The net result of the significant investment Tarmac Northern have made at Cross Green is a fully integrated site located in the centre of Leeds and at the heart of northern England, providing a highly efficient and versatile operation to meet the requirements of the building materials market. The site is also a prime example of how best-possible customer service is being provided through the optimization of resources. From start to finish Cross Green has been a story of focused investment.
Today, limestone aggregate is supplied by rail from Swinden Quarry, which was itself fully replanted in 2001 at a cost of £16 million, providing what is arguably the most efficient quarry in northern England. At the same time, the rail infrastructure was improved and significant investment was undertaken at Cross Green. The final step was investment in the new ready-mixed concrete and mortar operations. This has been completed and Tarmac are now uniquely positioned to service the region’s building materials markets from Leeds.
Acknowledgement
The editor wishes to thank Tarmac Northern Ltd for permission to visit Cross Green and, in particular, Ian Atkinson, area engineer, and Mark Spenceley, site manager, for their help in the preparation of this article.