Blashford Revisited
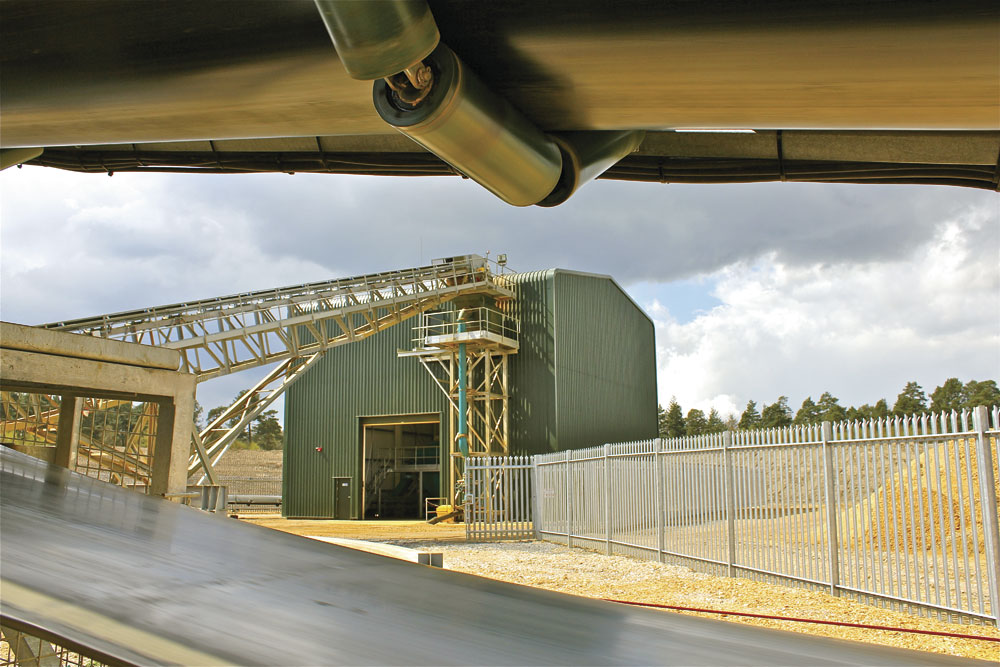
New de-silting wash plant at Burnt Hill proves beneficial for Lafarge Tarmac
In September 2012, Quarry Management reported on a major plant upgrade at Lafarge Tarmac’s Blashford Quarry, near Ringwood, in Hampshire. The replant involved the replacement of the site’s former sand and gravel processing plant, which had been designed to produce up to 290,000 tonnes per annum, with a more modern, higher-capacity, 250 tonnes/h plant capable of producing up to 400,000 tonnes per annum of washed sand and gravel products. The new plant was supplied and installed by DUO Equipment, dealers for Powerscreen and Terex washing equipment, who worked closely with the quarry operator to minimize the risks to those on site – in line with Lafarge Tarmac’s goal of achieving Zero Harm – and to reduce any environmental impacts.
At the time the article on the new plant was published, Lafarge Tarmac were preparing to open up their new extraction site at Plumley Wood to ensure the continuation of operations at Blashford once the extraction of the existing deposit at Nea Farm, which has only a few years’ worth of reserves remaining, reaches completion. Preparations for this move included further modifications and additions to the site’s already extensive and recently upgraded field-conveyor system by Canning Conveyor, including the fabrication of a fully enclosed bridge structure with walkways to carry the conveyor over a minor road.
In addition, since last year’s article, DUO Equipment have supplied, installed and commissioned a new ‘de-silting’ wash plant at Burnt Hill, a former extraction site located between Nea Farm and Plumley Wood. This new 300 tonnes/h plant has been designed to remove the bulk of the silt content from the ‘as dug’ Plumley Wood deposit, thereby providing a cleaner feed to Blashford’s main processing plant, while the silt content will be recovered and used to help reinstate ground levels as part of the progressive restoration of the new extraction area. This plant was installed by DUO engineers over a four-week period during the autumn of 2012 and commissioned in October.
Burnt Hill
The deposit at Plumley Wood, which lies in dry conditions above the water table and is extracted by a Cat 980H wheel loader, represents around 6 million tonnes of reserves, the bulk of which (approximately 5.5 million tonnes) comprises –150mm flint gravel, with the balance being sand. The deposit is undulating in nature but averages around 3.0 to 3.5m in thickness across the planned extraction area. The ‘as dug’ material, which contains up to 10% moisture and approximately 6–8% silt, is fed to the de-silting wash plant at Burnt Hill by a covered field conveyor system at a rate of 300 tonnes/h. Upon arrival at the new wash plant facility, the material is transferred to an inclined radial feed conveyor for delivery into the fully enclosed new plant or for discharge to ground stockpiles as appropriate.
When the wash plant is operating the radial conveyor feeds an 8.0m long x 2.5m diameter Eral barrel washer, which was supplied by DUO. A barrel washer was selected for this application rather than a log-washer as it is able to take a larger lump size from the dig. The feed enters the barrel via a heavy-duty feed chute fitted with 25mm thick steel-backed rubber liners. The chute is also equipped with a series of spray bars, fed by 250m3 of water per hour, to slurrify the feed material as it enters the barrel. Made from 18mm thick rolled-steel plate, the barrel itself sits at the top of the plant on a galvanized support frame complete with access steps and walkways, and revolves at 10 revs/min powered by four 22kW drive units, each comprising a planetary gearbox and motor. The feed material is washed and scrubbed as it moves forwards due to the rotary motion of the barrel, before being discharged via a double-skinned polyurethane classification trommel which separates out the –5mm sand and fines, and removes around 80% of the wash water from the gravel fraction.
The –150mm +5mm washed gravel from the trommel is fed, via a 25mm thick steel-backed discharge chute, to a Powerscreen DW146 14ft x 6ft single-deck dewatering screen to ensure minimal water is transported downstream to Blashford’s main sand and gravel processing plant (see earlier article for details). The dewatering screen is equipped with 0.5mm aperture polyurethane screen modules mounted within a robust, stress-relieved frame featuring two high-efficiency 6.2kW out-of-balance vibrating electric drive motors, all supported on heavy-duty oscillating rubber mountings. The entire unit sits upon a galvanized skid-mounted support structure with access steps on both sides and walkways around three sides. Spray bars are not required on the dewatering screen because, ultimately, the clean sand and gravel fractions are mixed back together again. The dewatered gravel is discharged, via a rubber-lined chute, on to a 58m long x 750mm wide ground conveyor which links to the newly extended field conveyor system for delivery to the main processing plant.
Meanwhile, the sand/silt slurry discharged from both the barrel washer and the dewatering screen are piped to a compact Powerscreen Finesmaster FM120C single-grade sand-recovery unit, which was sized for this particular application using grading data provided by Lafarge Tarmac. The unit is equipped with a single 610mm hydrocyclone with rubber-lined fixed-spigot discharge, a 200/150 rubber-lined centrifugal pump (37kW), a self-regulating cyclone tank collection sump with built-in float system, and a 12ft x 5ft dewatering screen featuring two 4kW high-frequency vibrating motors and modular polyurethane screen media. This combination of features serves to remove the –63 micron material and delivers a clean, dewatered sand product, via a rubber-lined chute, on to the ground conveyor where it rejoins the washed gravel fraction. In the meantime, the waste water overflow from the sand plant collects in an adjacent sump tank and is pumped to newly created silt lagoons at Plumley Wood for settlement and subsequent recirculation and reuse in the washing plant. Access to the Finesmaster is catered for by galvanized steps and walkways along both sides and around the rear of the unit.
The entire de-silting wash plant at Burnt Hill is housed within a fully clad building, the exterior of which is painted in dark green to blend in discreetly with the surrounding landscape. The plant is monitored and controlled locally from within this structure by means of a SCADA/PLC system designed, supplied and installed by electrical engineering and control system specialists Axon Power & Control Ltd, in conjunction with DUO’s installation team. In addition, a remote monitoring facility has been provided in the unit manager’s office some 2.5km away at Blashford Quarry’s main processing plant.
Benefits of the de-silting wash plant
With the de-silting plant now fully operational, Lafarge Tarmac have the option to continue processing high-quality, largely silt-free sand direct from their existing Nea Farm extraction site, or, when required, to switch to the coarser washed gravel feed from the Plumley Wood extension. Ultimately, when the deposit at Nea Farm is exhausted, all material processed at Blashford will originate from Plumley Wood.
The de-silting wash plant offers several other benefits. With a much cleaner product travelling down the belt, less washing is required at the main processing plant. This has resulted in the removal of the Powerscrub 120R log-washer, extension of the existing sizing screen feed conveyor and the installation of a new 14ft x 6ft dewatering screen as well as a pump and pipework to allow waste water and silt to be pumped back to the sand plant. Moreover, by not carrying a proportion of unwanted silt to the main processing plant, Lafarge Tarmac are saving on energy costs and retaining silts and fines at the Plumley Wood site for future reinstatement works.
Commenting on the new plant, Derek Haden, Lafarge Tarmac’s Blashford unit manager, said: ‘We are pleased with the outcome of this project. The plant is working very well for us and is regarded as a show site for Lafarge Tarmac. We have worked well with DUO at Burnt Hill and I would consider this project to be the benchmark for future projects in terms of guarding and access.’
DUO director Fintan McKeever added: ‘This has been an excellent project for us too because it not only shows our processing capabilities, but also the high standards we work to from a health and safety perspective.’
Acknowledgement
The editor wishes to thank Lafarge Tarmac for permission to visit the site and, in particular, Derek Haden, unit manager, and Matt Waters of DUO Equipment, for their help in preparing this report.