Seeking Sustainability
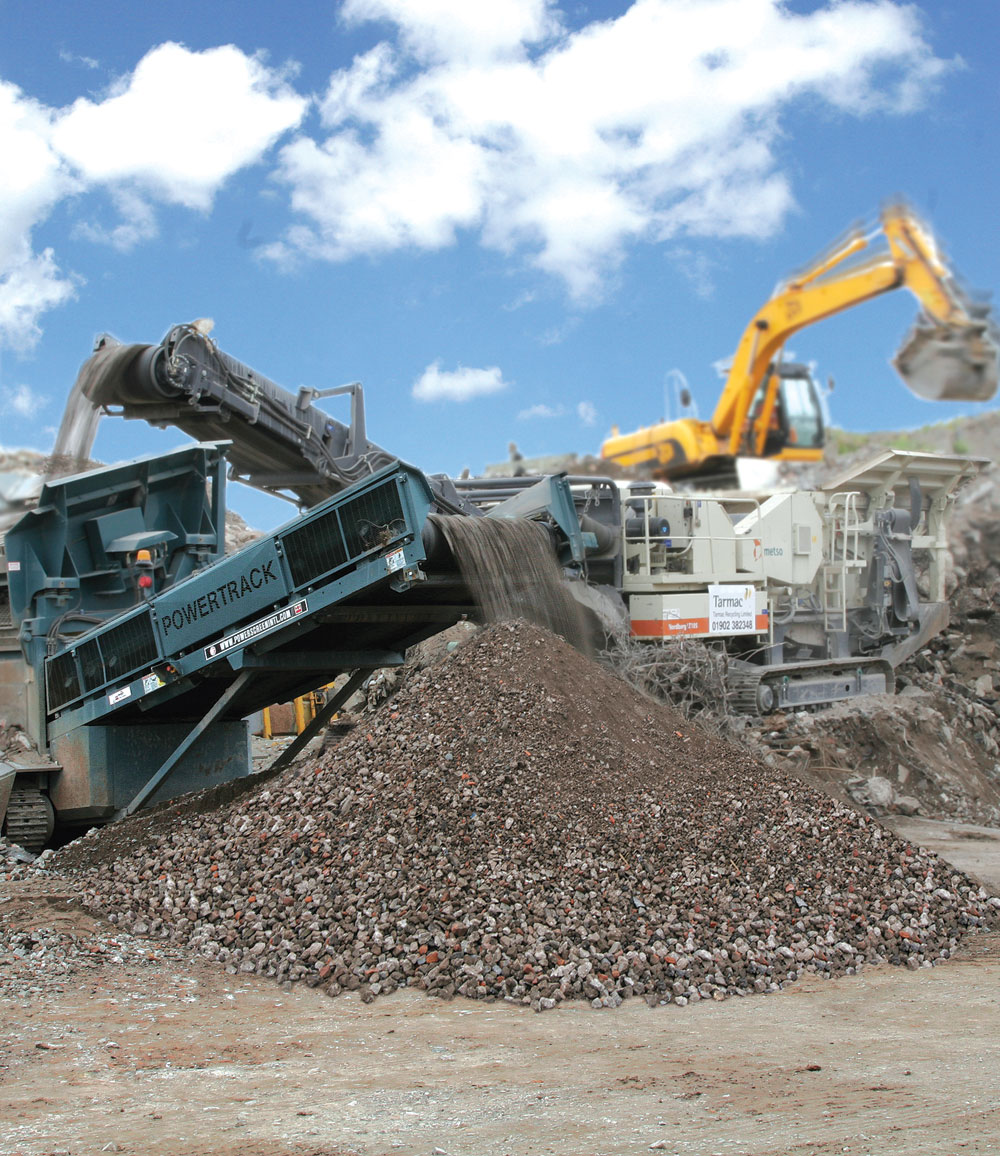
Sustainability and responsible sourcing are becoming increasingly important in the way the construction industry operates. The market share of recycled and secondary materials is expected to rise and, when combined with more efficient site practices, will reduce demand for primary aggregates, but for Tarmac, good sustainable practice is about looking at the bigger picture
It is easy to forget, given the prevalence of green issues today, that a couple of decades ago hardly anyone bothered to consider the impact a building might have on the environment.
Now environmentalism has entered the mainstream it seems that everyone – from architects and car manufacturers to supermarkets and oil companies – is flaunting their environmental credentials.
This ‘good PR’ is exactly what the Government wants; not only does it raise the awareness of green issues on a wider scale but, more importantly, the UK’s industry sectors will be encouraged to minimize the environmental impact of their operations and make a real and positive contribution to the environment by operating in a more sustainable manner, eg waste minimization, reduced carbon footprint and maximizing reuse of recovered products etc.
As the Government urges developers, designers and builders to become more environmentally conscious in their developments, the construction industry has already taken a huge step forward towards sustainability.
It has been given the challenge of ensuring that the country’s most high-profile project of the decade – the building programme for London 2012 – will result in the ‘greenest Olympic Games in history’, placing the UK at the forefront of sustainable design and construction.
With the new venues and infrastructure currently being built to eco-friendly principles, recycled materials undoubtedly have a key part to play in delivering sustainable low energy buildings of a high standard of excellence.
The Olympic Delivery Authority (ODA) claims that around 90% of the demolition materials will be reused or recycled, and at least 20% of materials used in the sports facilities and residential developments will derive from recycled sources.
No waste
The wider quarrying industry fully supports recycling and it is true to say that the use of recycled and secondary materials is already well established in the UK; it currently accounts for around 25% of the total aggregates market.
The demand for recycled aggregates is set to rise further over the next few years, possibly to around 40%, and some of the important drivers for this will be the growing cost of waste disposal and increased legislation, eg Site Waste Management Plans (SWMPs), which are now a legal requirement for construction projects costing over £300,000 in England.
Some clients and contractors are also beginning to use primary materials more efficiently by maximizing the reuse of on-site indigenous/waste materials through in-situ recycling/stabilization and remediation as alternatives to landfill, reducing the need for virgin materials.
Taking this sustainable approach will help companies manage their waste more effectively, provide a safer and more productive site, reduce costs and demonstrate how they are managing their environmental performance.
Sustainable future
Sustainable building practices are expected to become the norm in the construction sector and recycling itself will continue to play a critical role in the choice and purchase of construction materials.
However, Neil Roberts, development director for Tarmac’s recycling division, believes organizations must take an intelligent approach to the use of recycling, acknowledging the fact that it is not always the most sustainable solution and that the quarrying industry, together with the construction sector, needs to take a look at the bigger picture.
‘With government initiatives such as Constructing Excellence and WRAP driving forward sustainability, I think aggregate suppliers will have to look at different ways of how they can produce and supply materials in a more environmentally friendly manner whilst ensuring this is also economically viable,’ he explained.
‘Sustainability is changing the outlook of the quarrying sector and the key challenge for us, as a industry, is to come up with sustainable whole-life solutions that meet the Government’s sustainable construction agenda.’
Indeed, there is a constant need for aggregate producers to be forward-thinking and innovative, bringing in new ideas, processes and products to the market. Tarmac, for example, works closely with a wide range of companies and organizations, developing eco-friendly solutions that can help customers meet their green agendas and improve their environmental performance.
‘We’re not a company that just manufactures recycled aggregates,’ continued Mr Roberts. ‘We are now moving towards being a business that focuses on providing our customers with holistic, integrated and sustainable solutions that addresses their exposure to escalating waste disposal, health and safety, carbon and environment costs whilst improving productivity and reducing design risk.
‘Our challenge is to embed this philosophy throughout the supply chain by engaging local authorities, clients and their contractors. I run a team who try to influence mindsets positively to create awareness of the cost and environmental benefits Tarmac can offer to their business if they look beyond the commodity price. Personally, I believe materials are not truly recycled in a beneficial and sustainable way until the loop is closed and that they have been reused locally.’
While it is now imperative to deliver construction projects with higher recycled content, as London 2012 will demonstrate, it is also important for contractors to take into account their energy consumption, carbon footprint, disposal of excavated materials and the environmental effects of recycling.
Companies need to understand that sustainable construction is about looking at the lifetime performance of buildings and highways, and not just about the embodied carbon, materials and energy involved in building them in the first place. The whole process, from planning and procurement to design, whole-life energy performance and construction, needs to demonstrate good sustainable practice, and there are already measurement schemes in place, most notably BRE’s BREEAM, which assesses the environmental performance of new and existing buildings.
Mr Roberts believes everyone in the materials supply chain should strive to engage strategically with both customers and their clients to reap the full environmental and financial benefits. ‘As suppliers, it’s certainly the approach we take as a business,’ he said. ‘There has been growing pressure for our clients to establish their green credentials and comply with legislation and one of the ways for them to meet today’s sustainable challenges is recycling, which ties in with waste avoidance – a key legislative driver.
‘By taking a consulting approach and involving us at the early stages of a contract or project, we can work together with our customers to help develop sustainable solutions to their problems that effectively reduce the impact on the environment. For example, we can help cut haulage movements to reduce their carbon footprint, ensuring recycled aggregates are transported in a more environmentally efficient way.’
‘We can also look at ways of improving their waste avoidance, in line with legislation. Our general view is that if we can offer such solutions to our clients, saving them costs by driving out inefficiencies within their business, then they will use us for other aspects of their operations.’
Case study: Recycling and re-use of utility trench arisings
According to WRAP, the utility sector produces around 4.8 million tonnes of trench arisings across the UK each year, over half of which is currently going to landfill. In a bid to reduce waste sent to landfill and increase the uptake of recycled and stabilized materials in the utility sector, last year saw the launch of the Utilities Industry Agreement.
Signing up to this industry-wide agreement, which includes a supporting agreement for the construction sector, utility companies and their contractors have pledged their support to achieving greater materials resource efficiency, eg set company targets aimed at reducing utility trench arisings sent to landfill and/or use procurement and contractual arrangements to meet sustainable targets.
WRAP also sees the landmark agreement as a catalyst for sharing best practice in the wider industry, from the recycling of trench arisings and their reuse as granular and bound fill material to determining the overall performance of completed reinstatements.
National Grid was among the first companies to commit to the Utilities Industry Agreement and, through their subsidiary West Midlands Gas Alliance (a partnership with Morgan Est), teamed up with Tarmac to undertake a trial to develop a sustainable solution that will eliminate their trench arisings going to landfill.
During the two-year trial, the two companies worked closely with local authorities in the West Midlands to recycle trench spoil by grinding and mixing the waste followed by adding a stabilizer to produce an alternative sub-base for footpaths and Type 2, 3 and 4 roads – a recycled material classified as ‘Stabilized Material for Fill’ (SMF).
The success of the scheme has shown that by reprocessing and refining trench waste carefully at a one-stop shop, it can be recycled and reused in trench reinstatements, thereby reducing the cost of tipping and transporting material.
‘Recycling and reusing waste materials locally has not only brought environmental benefits for National Grid, but also potential productivity savings of around 20% in fuel, labour and the use of vehicles,’ explained Mr Roberts. ‘Before the trial we carefully looked at how West Midlands Gas Alliance worked and sought ways of improving their efficiency, which, in turn, will help them deliver further cost savings associated with using recycled materials in the long term.
‘National Grid has pledged to reduce the amount of waste sent to landfill to zero, and our role is to continue to help the utility industry and local councils across the UK to meet their recycling and productivity targets.’
Indeed, Staffordshire Council has been so impressed by the groundbreaking recycling process that it has approved SMF for use in the county’s highways.
It is hoped that other local authorities and utility firms will learn and gain confidence from the trial and be encouraged to recycle their own trench arisings.
Resistance to change
Although the UK construction industry is currently the leading user of recycled and secondary materials in Europe, WRAP believes there is still a lot of work to be done in reducing more waste to landfill and ensuring the whole supply chain recognizes the environmental and economic impacts of waste disposal and recycling.
One of the major obstacles to the increasing use of recycled aggregates is a lack of direction shown by the clients, particularly those in the public sector. According to WRAP, around half of all local councils use recycled materials in highways projects, but only 20% are currently setting requirements in contracts that actively encourage contractors to maximize use and seek the associated cost savings.
‘Many local authorities we work with are doing a good job when it comes to recycling, but some are simply not doing enough to ensure that the aggregates are recycled and reused locally,’ explained Mr Roberts. ‘Along with clients in the private sector, they’ve got to approve and encourage the use of recycled aggregates by specifying requirements in contracts that will help meet their own environmental targets.’
Traditional procurement attitudes, therefore, need to change, as clients will have to engage directly with all parts of their supply chain, demonstrating support and delivery of using products recovered from waste.
‘One of the key reasons why there is resistance to change is that some businesses only look at the commodity price of purchasing construction materials and not at the whole-life cost savings that can come with taking a more holistic approach to recycling and sustainability,’ said Mr Roberts. ‘There is a clear lack of knowledge and they need to be aware of the benefits that recycled materials can bring to a project in the long term.’
With good procurement practice in place, there are clear financial benefits to be gained from using recycled products and recycling techniques, eg avoidance of waste disposal charges and landfill tax.
Clients will also improve their sustainability credentials in compliance with national strategies and government requirements, eg reduced carbon footprint of transporting aggregates if recovered materials are reused locally.
As more businesses recognize the environmental advantages and substantial cost savings to be gained from recycling and the efficient use of materials, Mr Roberts believes market demand may drive the price of recovered recycled materials above primary materials. The materials price will, however, become an increasingly small part of the cost when looking at the extensive cost-savings associated with using sustainable recycled materials. He said: ‘It will certainly be an educational change for the traditionalists to change mindsets and realize how much they can save on waste disposal, fuel, labour tax and production costs, as clients and contractors increasingly look to work more sustainably.’
Leader of the pack
The UK is currently leading the way in aggregate recycling technology. Washing systems, in particular, have evolved rapidly in recent years and are expected to have a huge impact on halving construction, demolition and excavation waste going to landfill by 2012.
‘Historically, the problem has been removing clay and silts from waste products, but with the new technology available, most of these fines can be removed and this will lead to better-quality aggregates,’ said Mr Roberts.
New advances in washing systems will, therefore, be greatly welcomed as impending new legislation and sustainable working practices are introduced, but Mr Roberts warns that there is still a lot of encouraging and convincing to do in the mainstream.
‘While the technology is there to stabilize materials, there’s a challenge to get the clients to buy into the concept of taking back and reusing materials,’ he said. ‘If we’re going to make the investment in recycling technology worthwhile, closing the whole loop will be key to the success of using the latest technology.’
Despite the economic crisis and slowdown in the construction market, the aggregates industry is going through a period of environmental change; more stringent legislation, a greater awareness of green issues and the need to cut CO2 emissions are now beginning to convince clients and contractors to adopt eco-friendly working practices.
The message from Tarmac is that sustainability and recycling is not simply about passing waste management on to third parties and achieving material resource efficiency, but also about encouraging local reuse and changing attitudes. It is only when people take responsibility for their consumption of energy, products and services, and recognize that the negative local and global environmental cost impacts are not positioning them favourably to secure more work, that they will take action to minimize it. Only then will sustainability ever truly be achieved.
Driving the use of recycled aggregates
After significant investment, the Ettingshall recycling plant is one of Tarmac’s first dry processing facilities that began operating in 1999.
Last year the plant recycled around 120,000 tonnes of waste (eg utility trench arisings, tiles, brick, foundry sand, road planings etc), producing approximately 80,000 tonnes of recycled products, such as recycled Type 1 sub-base, capping and a range of single-size materials.
The Ettingshall plant also manufactures Toptrec – a 100% recycled pathway material made from selected waste products from highway reconstruction and maintenance works. All recycled products from Tarmac strictly comply with the industry’s Quality Protocol.
Tarmac’s recycling division supplies recycled materials to local civil engineering and utility firms, including Severn Trent Water, Morgan Est and National Grid. The site also manufactures products for use in highways and pathways projects for Wolverhampton City Council, Walsall Council and Dudley Metropolitan Borough Council.