RubbleMaster Makes the Grade for Gallagher
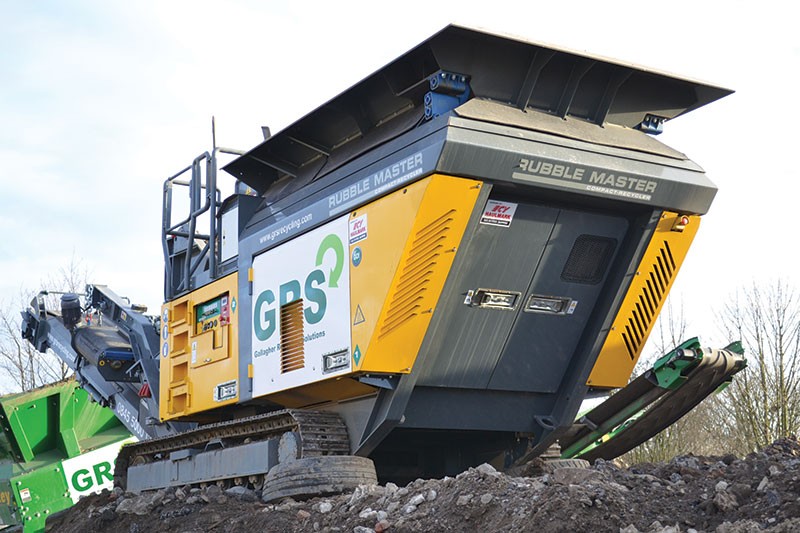
First published in the October 2014 issue of Quarry Management
Gallagher Recycling Services highlight the use of an RM70GO crusher in the processing of utility trench arisings for re-use as backfill material around new services
Although the recycling of utility trench arisings is not a new concept, the addition of a binding agent to allow the material, when screened, to harden over time is a service being offered by Manchester-based utilities contractors Gallagher and their recycling arm GRS.
Formed in October 2010, GRS (Gallagher Recycling Services) are based in Salford, a few miles west of Manchester city centre. The company operates a similar recycling set-up at its Derby depot and is also contemplating opening additional recycling centres as and when significant contracts allow.
Working as main contractors for United Utilities on mains repair and replacement works, Gallagher have 40 teams of operatives and fourteen 8x4 grab wagons working in and around the Manchester area, and have taken almost 50,000 tonnes in arisings for recycling in the last 12 months.
Company director Vincent O’Connor explained the theory behind company’s decision to use recycled trench fill: ‘We wanted to reduce our impact on the environment and the most obvious way to reduce our carbon footprint was to reduce the amount of vehicle movements that we were undertaking on a weekly basis. By recycling both our and others’ trench arisings, we can effectively cut down on the amount of raw materials quarried and transported from the Derbyshire area.
‘We now bring a load of material into the recycling centre and take a load of recycled trench fill back out. Not only do we reduce the amount of vehicle movements, but we also cut costs for each vehicle because they are travelling fewer miles. An added bonus is the quicker turnaround for the grab trucks, which means that the reinstatement of trenches can be completed more quickly.’
The make-up of the incoming materials ranges from soils and tarmac to concrete and stone. ‘Unlike a traditional recycling company, we will only take these materials, making the recycling process easier,’ commented Mr O’Connor. ‘We may encounter some rebar, but that is the only non-reusable material we want to see in the stockpile. We look to recycle 100% of incoming materials and currently manage to turn 95% of the material into a reusable product, although this figure can be affected by wet weather.’
GRS now have a protocol and control ‰ system in place for the compliant production of an Appendix 9 soil-stabilization product from utility arisings, which is a non-flowable SMR (structural material reinstatement). The finished material has undergone rigorous testing to meet WRAP protocols, including co-efficiency testing, particle size distribution and compressive testing, which, encouragingly, produced results averaging 2.5kN for the test cubes – equivalent to concrete.
‘We now have full traceability of the product which not only benefits our customers using the SMR, but also covers our ourselves and our clients. All test certificates are available for anyone to view online and it this openness that shows our clients that we have every faith in our product,’ explained Mr O’Connor.
As well as GRS’s recycling services, the Salford depot is also home to the utilities gangs and Gallagher’s own traffic-management company, GTM, and whilst the premises occupies a large area, the company has opted for the use of more compact equipment to produce the SMR material. ‘We originally trialled a conventional jaw crusher to process the incoming materials but the results were not up to the standards we wanted,’ said Mr O’Connor.
The company, therefore, looked elsewhere for a solution, which led them to Warrington-based attachment specialists ECY Haulmark and their range of Austrian-built RubbleMaster compact recycling machines. The original purchase of a quality used RM60 gave the company the results they desired and led to the more recent purchase of a brand new RM70GO machine.
Weighing 19.5 tonnes, the RM70GO is a crawler-mounted impact crusher capable of producing up to 120 tonnes/h. Although this output is more than ample for GRS’s operation, it is the consistency and quality of the processed material that matters most to the company.
Among the main benefits of the RM70GO are its compact dimensions; measuring just over 10m in length and 2.3m in width when ready for work, it offers an ideal solution for inner-city and smaller sites, while its low height (2.66m) means that even smaller excavators can load the feed hopper. Fitted with Hardox 440 liners, the 2.5m x 1.8m hopper holds up to 2.0m3 and delivers the material, via an asymmetric vibrating channel, into the RubbleMaster HMH impact unit. The crushing unit can be equipped with either two or four hammers depending on the application and the desired finished material.
The RM70GO is powered by a Tier 3a-compliant Deutz four-cylinder diesel engine developing 103kW, which is connected to a 40kVA, 400V synchronous generator. The diesel-electric drive unit means that the RM70GO is very quiet in operation, which is perfect for inner-city recycling. The fuel-efficient engine consumes approximately 15 litres/h when working at maximum capacity.
For ease of transportation between sites, the RM70GO’s single 2.7m long x 800mm wide discharge conveyor folds hydraulically. It also comes equipped with a powerful overband magnet capable of removing steel to either side of the crusher.
GRS say maintaining the RM70GO is easy thanks to large canopy doors that give access to the engine and generator. Access to the hammers is also relatively straightforward, due to the hydraulically opening crusher unit, which allows changes to be made within a couple of hours. Operating the RM70GO is very simple with machine controls grouped in colour-coded panels. A wireless remote control comes as standard, allowing the operator to reposition the machine while keeping a safe distance from the unit.
The Salford recycling operation uses an ageing Daewoo DX225 crawler excavator to load the RM70GO with incoming material. Material processed by the crusher is fed directly into another new purchase – a fuel-efficient McCloskey 4m x 9m tracked screener. Finished materials, oversize and 0–6mm pipe bedding, another material that Gallagher use in their utility operations, are stockpiled and then either sent back through the crusher (in the case of oversize), or mixed in prescribed quantities with the binding material to form the final SMR product. The SMR is held in bays for up to seven days (its maximum shelf life). Should it remain unused within this period, it is fed back through the system and fully recycled once again.
Vincent O’Connor and his team at Salford say they are delighted with the performance of the RubbleMaster crusher and are particularly pleased with the way in which ECY Haulmark and their staff offered a bespoke solution and have looked after them since the start of the project. Moreover, client acceptance of the SMR is gaining strength and the reduction in the company’s carbon footprint means they are managing to reduce their operational impact on the environment.
- Subscribe to Quarry Management, the monthly journal for the mineral products industry, to read articles before they appear on Agg-Net