Recycling Matters
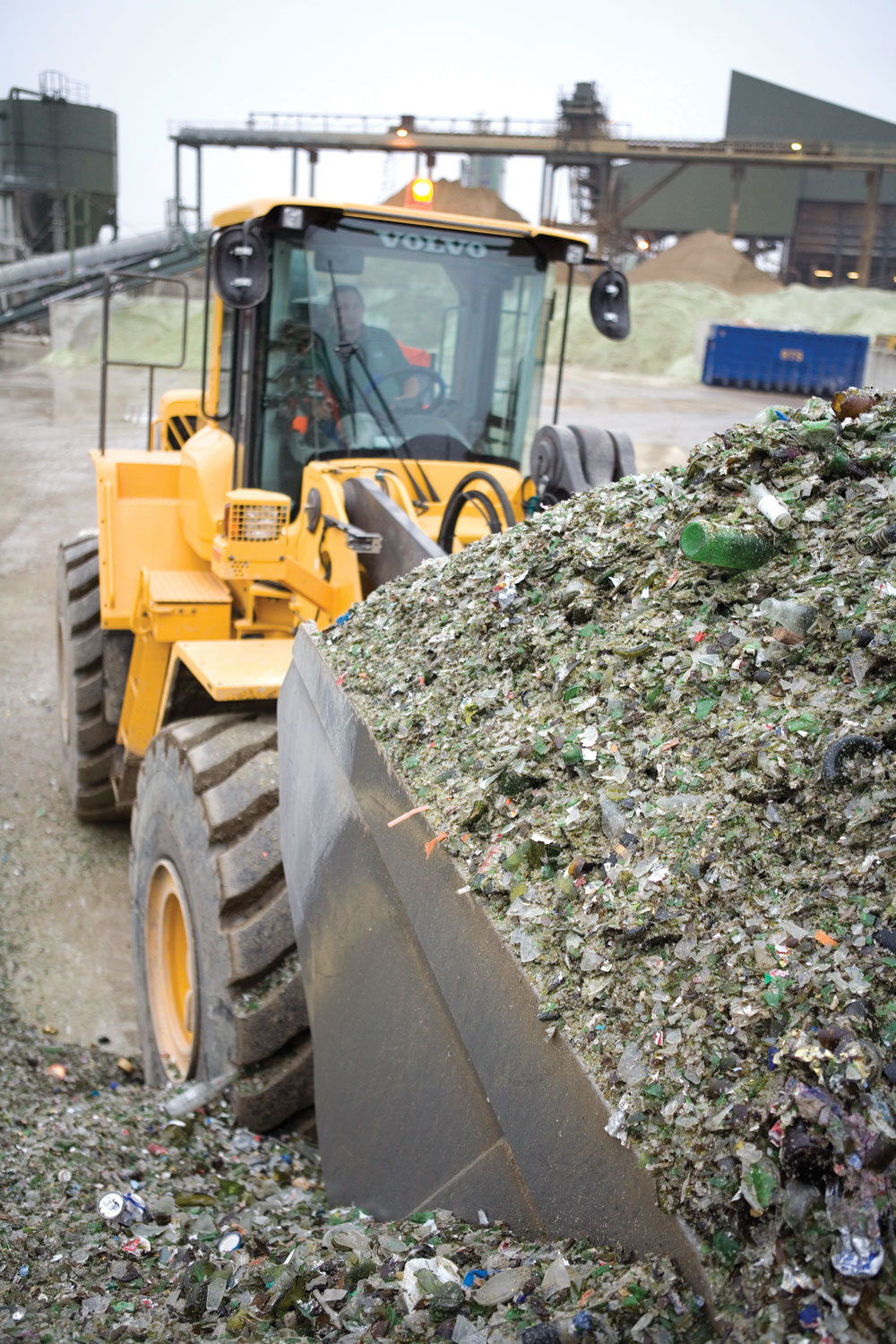
The UK is currently the leading user of recycled materials in Europe – last year around 280 million tonnes of aggregates were used as raw construction material, a quarter of which, some 70 million tonnes, was derived from recycled and secondary resources
It seems everyone has something to say about sustainability, and one of the biggest challenges for the UK building industry at present is sustainable construction. Reducing carbon emissions, improving energy efficiency and minimizing waste represent key parts of the Government’s policy to tackle climate change and move towards a low-carbon society.
In addition, major targets for recycling more construction and demolition waste have been set. The Government’s Sustainable Buildings Task Group has recommended that a minimum 10% of the total materials value of a construction project should contain recycled content.
Add to this an increasing emphasis on corporate social responsibility and more efficient use of resources, and the pressure is now on for contractors to assess how much material is used on site and how much is wasted.
According to WRAP, one of the leading organizations in raising the awareness of recycling across a number of key industries, construction, demolition and excavation waste amounts to around 120 million tonnes per year, with only half of this being recycled or reclaimed.
With a construction boom well under way in many parts of the UK, particularly in London where the 2012 Olympic Games will take place, there is a clear case at every level of the building industry to deliver projects with higher recycled content.
Taking a greener approach to construction and waste management will help ensure a building project not only meets the Government’s wider sustainability targets, but also help numerous construction businesses fulfil their regulatory responsibilities and environmental aspirations.
A requirement to use a fixed percentage of reclaimed materials, as the Government has called for in construction, would help make waste more valuable and, therefore, less likely to be disposed of in a careless way.
John Barritt, aggregates technical advisor for WRAP, said: ‘The aggregates industry has a pivotal role to play in helping the UK construction sector improve its materials resource efficiency and achieve its sustainability targets. Part of our aim is to promote the greater use of recycled aggregates and waste minimization at every stage of a project, from planning and procurement through to design and construction. The UK market for recycled aggregates has grown steadily in recent years; around 25% of the total construction aggregates produced annually now come from sustainable resources, which is more than any other country in Europe.’
Over the next few years, the national aggregate supply met by recycled and secondary materials could rise to 30%, as the availability of sustainable aggregates and the specifications for their use are now greater than ever. The introduction of a wide range of recycled and secondary aggregates within the Highways Agency’s ‘Specification for Highway Works’ in 2001, followed by the European Standards for aggregates in 2004 has meant that recycled and secondary materials can be used across a broad range of applications.
The Landfill Tax (introduced in 1996) and the Aggregates Levy (2002) have, of course, continued to encourage the use of sustainable aggregates and minimize waste from an environmental and cost-savings point of view.
But perhaps the biggest driver for the growing use of recycled aggregates is that many companies within the construction and aggregates sectors have placed sustainability at the top of their agendas.
‘Corporate strategies have been moving towards sustainability because the businesses that are materials resource efficient, eco-friendly and less wasteful are the most competitive in the industry,’ explained Mr Barritt. ‘Good sustainable practice helps companies save money and reduces their environmental impact.’
While recycling is an important part of resource management, it is not the first option in terms of sustainability or profitability. The environmental benefits and cost savings associated with preventing waste actually far exceed those relating to recycling. These include: reduced material, energy and disposal costs; lower carbon emissions; and improved resource efficiency.
However, waste minimization has traditionally been overlooked in the drive to recycle – but this is expected to change with the legislation of the Site Waste Management Plans, introduced this month, which aims to reduce the amount of waste produced on UK construction sites and prevent fly-tipping.
Achieving ‘zero waste’ in any industry is a tough target to reach but the combined ethos of waste prevention and continued improvement of recycling facilities and rates will significantly reduce what goes into landfill.
Earlier this year, the Scottish Government announced ambitious plans for a zero waste strategy with tougher new targets aimed at increasing recycling and cutting down on waste sent to landfill.
It has also urged public bodies in Scotland to set minimum requirements for recycled content as part of their tendering process; at least 10% of the total value of materials used on publicly procured building projects should derive from recycled content.
The demand for recycled aggregates has consistently grown since 1990 (see table 1) but despite playing a key role in helping to make the construction industry more sustainable, one of the major concerns that is often raised when using recycled materials is the level of quality compared with primary aggregates.
‘Initially, there was a general public perception that recycled and secondary materials were not as good as primary aggregates,’ said Mr Barritt. ‘When a recycled aggregate was supplied to a site and it did not meet the quality that the specifier expected, the customer would accept it, thinking that recycled aggregates were always poor quality. This is why some aggregate suppliers have continued to produce low-quality materials because customers still buy substandard products.
‘I’ve spent years telling people that if they ordered a material to a specification – it has to be to that specification. If it doesn’t, send it back and the producer will be unlikely to supply the substandard aggregate again.’
A majority of recycled aggregate suppliers today are quality managed, providing recovered materials to recognized specifications that are high quality, but, as Mr Barritt warned, there is still a small section of producers who are not complying with the Quality Protocol, WRAP’s quality benchmark for recycled aggregates.
Developed in collaboration with the Environment Agency, the Highways Agency and the QPA, the purpose of the Protocol is to provide a uniform control process for producers of recycled aggregates to demonstrate that products have been fully recovered and are no longer waste. This, in turn, will help specifiers identify and purchase quality-managed products that meet common aggregate standards by segregating materials that do not comply with the Quality Protocol.
‘Over the next two years, we’ll be strenuously tightening up the quality of recycled and secondary aggregates being supplied in the UK,’ said Mr Barritt. ‘There are still a number of aggregate suppliers out there who are not producing to the industry standards but are selling waste, and why there are businesses still buying such material is beyond me.’
To address this key concern, WRAP and the Environment Agency will be informing all the parties involved in the supply chain – from specifiers to purchasers to producers – of what they should look for in terms of quality management and sustainability through a number of initiatives. WRAP has also published a guide listing the recycled content and other information on a wide range of construction products, so specifiers can identify materials with high recycled content.
Increasingly, aggregate producers are raising the awareness of quality too, mainly by providing information about the recycled content of their products (eg product data sheets).
With sustainability now a buzzword in the wider quarrying industry, it comes as no surprise to learn that many companies are keen to showcase their green credentials, but Adam Day, chairman of the QPA Recycled Aggregates Committee and contracts director at Day Aggregates, warns that there are a number of businesses who are misusing what it means to be ‘sustainable’.
‘Some of the environmental claims that companies are making about their products are exaggerated,’ he said ‘It’s primarily there to put a green spin on what they do, and it’s not right. Today, a lot of recycling is actually done by waste companies who don’t have the right background and level of knowledge of the aggregates industry.’
As major aggregate suppliers, Middlesex-based Day Aggregates understand the importance of offering their customers quality products. All of the company’s recycled aggregates are produced within the guidelines set out by WRAP’s Quality Protocol.
‘We operate under a strict regime from the quality control procedure for incoming materials and the acceptance criteria through to the process control and testing of finished products,’ continued Mr Day. ‘We also ensure customers are fully informed of the recycled content of our products.’
Recycling is a key part of Day Aggregates’ operations. The company produce and supply around 800,000 tonnes of recycled aggregates a year from three strategically located state-of-the-art recycling plants in Brentford, Purley and Greenwich.
The facilities, which are all rail-linked or river-connected, are equipped with dry processing and washing plants that allow them to produce high-quality recycled aggregates for use in the construction and civil engineering sectors.
The plants recycle around 700,000 tonnes of construction and demolition waste a year; producing mainly sub-base and capping material. Two of the recycling plants (Brentford and Greenwich) also handle around 100,000 tonnes of glass waste per year, which is equivalent to two million bottles.
‘The recycling of glass bottles represents a valuable sustainable resource,’ enthused Mr Day. ‘The glass is crushed, graded to size and washed to produce a clean –5mm ‘washed glass sand’, which we’ve called EcoSand. It is safe to handle and meets the technical requirements for a laying course under paving slabs and block paving.
‘EcoSand has been a success; we’ve demonstrated that the use of recycled glass can help specifiers, designers and contractors address issues of sustainability. First, there is no need to extract marine-dredged or land-based sand, so this reduces the environmental impact of raw materials used on a project. Secondly, since the glass for EcoSand is collected and processed locally, low energy is used in its production and transportation. Finally, EcoSand is a manufactured product that contains re-used content and, therefore, supports projects requiring a certain percentage of reclaimed materials to be used.’
Other recycled products being manufactured and supplied by Day Aggregates include: EcoBlend Type 1, a mixture of recycled and primary aggregate for use as a sub-base under flexible or rigid pavements and footpaths; Hasopor, a ‘green’ lightweight foam glass aggregate for ground floor and basement insulation; and utility spoil as a base aggregate to produce general fill.
In the future, Mr Day hopes sustainability will become the norm in the aggregates industry, but for this to happen, designers, contractors and suppliers must understand the production of sustainable aggregates is not all about recycling.
‘I think people need to understand that the sustainability of aggregates doesn’t mean a product has to contain 100% recycled aggregate,’ he explained. ‘A sustainable product, for example, can have 20-30% of reclaimed material blended in with a primary aggregate. Mixing is, therefore, acceptable and the industry goal is to have a sustainable balance of using primary and recycled materials, which will benefit everyone in the long term.’
While quality and sustainability are fundamental issues for both the QPA and WRAP, they also recognize the need for innovation, most notably the way recycling plants operate abroad.
‘What strikes me when I visit other countries is the number of well presented and better managed recycling facilities that are producing consistent, quality aggregate products,’ added Mr Day. ‘This is something that the industry is trying to do, but many companies tend to put price over quality.’
One of the key objectives of WRAP is to help aggregate recyclers invest in reprocessing infrastructure to produce higher-quality recycled products. To date the organization has provided more than £9 million of capital grant funding, which has increased aggregates recycling capacity by more than 3 million tonnes a year.
The development and broader use of washing plants has been a technical incentive for companies to recycle waste and manufacture reclaimed products. And there is now a growing emphasis on developing reprocessing plants that will feature hydraulic binders for stabilizing unbound aggregates.
However, Mr Barritt believes the biggest factor in the increasing use of recycled aggregates in the future will be the Government’s policy to tackle carbon emissions. ‘Reducing the carbon footprint of projects is the next big influence as part of the Government’s drive towards sustainable construction,’ he said.
‘It has become a vital component of construction design, procurement policy and delivery. As a result, it is important for contractors and aggregate recyclers to be more aware of their carbon footprint by assessing the energy used in the production and transport of their materials.
‘The Environment Agency has already shown its commitment to a lower carbon strategy by using a carbon calculator to measure the CO2 emissions on all its major construction projects, so it can specify materials with care and consider more energy-efficient solutions.
‘In the future, the level of carbon footprint will greatly influence the commercial decisions in material choice and, of course, recycled aggregates that are used effectively in sustainable construction will, in most cases, be the lowest carbon produced material.’
WRAP has made a significant contribution to the mainstream use of recycled aggregates and is continually helping remove barriers to growth.
‘One of the major obstacles to the production of recycled aggregates is the low level of Landfill Tax on inert waste,’ continued Mr Barritt. ‘Landfill Tax was introduced to encourage businesses to recycle and produce less waste, but inert landfill and other disposal options, the majority of which don’t charge Landfill Tax, remain a cheap option of waste disposal.
‘The low cost disposal of inert waste, on which Landfill Tax where applied, will increase from £2 to £2.50 per tonne in April 2008, is a key disincentive to recycling. To overcome this, we should significantly increase the cost of landfill as another important driver for recycling waste. Some of the highest recycling rates in Europe are currently in Holland and Germany, where landfill taxes are sky high.’
Diverting a significant amount of waste from landfill is also supported by Mr Day. ‘I’ve recently come back from a trip to Holland with the Recycled Aggregates Committee, which we found very educational,’ he said. ‘The Dutch Government has an open policy in terms of recycled aggregates output because the country does not have cheap landfill, so contractors are forced to recover the maximum amount of material that they can from waste.’
As the construction industry takes a huge step forward in operating in a more sustainable way, utility companies are also placing sustainability at the top end of their agendas. In the UK, water and gas capital and maintenance trench works generate around 4.8 million tonnes of excavation waste a year, and environmental pressures to recover arisings and to use recycled materials are ever increasing.
Many utility companies are generally in favour of recycling trenchwork arisings and using recycled materials when reinstating trenches, however, they have varying degrees of commitment to driving this agenda because of the requirements they agree with their contractors.
Pressures of time and perceptions of quality, combined with a lack of knowledge on non-traditional materials and where to purchase them, have discouraged many main contractors and sub-contractors. The general response from utility companies and main contractors is to stick with tried and tested materials and techniques.
But under the second edition of the Specification for the Reinstatement of Openings in Highways (SROH), HAUC 2002, the utility sector has been encouraged to use and trial non-traditional materials and techniques to reinstate trenches. The Specification states that recycled, secondary or virgin materials, or any combination thereof, are permitted, provided they meet the performance requirements and any compositional requirements for the relevant material layer.
‘One of the biggest changes in the aggregates sector over the next few years will be the increased recycling of utility trench arisings,’ said Mr Day. ‘Utility businesses are currently under massive pressure, both commercially and environmentally, to reduce their waste going to landfill, so the energy sector is striving to be innovative in its approach to recycling and waste minimization. This has seen companies turning to hydraulically bound materials as part of their trench reinstatement works.’
Indeed, with a range of recycled reinstatement materials and processes now available, utility companies, contractors, material suppliers and local authorities all have a fundamental part to play in the efficient use of materials associated with the recycling and re-use of trench arisings.
In particular, Mr Day believes utilities need to take control of their aggregate purchasing in creating an example of good practice. ‘Aggregate purchasing in the utility sector is very dispersed at present because of the number of main contractors and sub-contractors involved,’ he explained.
‘Utility companies need to shoulder that responsibility by taking a more informed approach to materials purchasing. In order for them to meet their sustainability targets, they need to unify and produce industry standards that can be used to demonstrate to local authorities and approving public bodies that the environmental process is in place and materials are fit for purpose. Thames Water are already making headway by working closely with their supply chain via a framework agreement to minimize the environment and social impacts of their products and services.’
As recycling and waste minimization becomes increasingly sought after, there has never been a better time for the construction industry to improve its sustainability credentials. Minimizing landfill, reducing carbon emissions and conserving finite resources of primary aggregates, not to mention significant cost savings, are just some of the major benefits of recycling waste. The rewards are definitely worthwhile.