Recycled and Secondary Aggregates Producers Step Up Operations
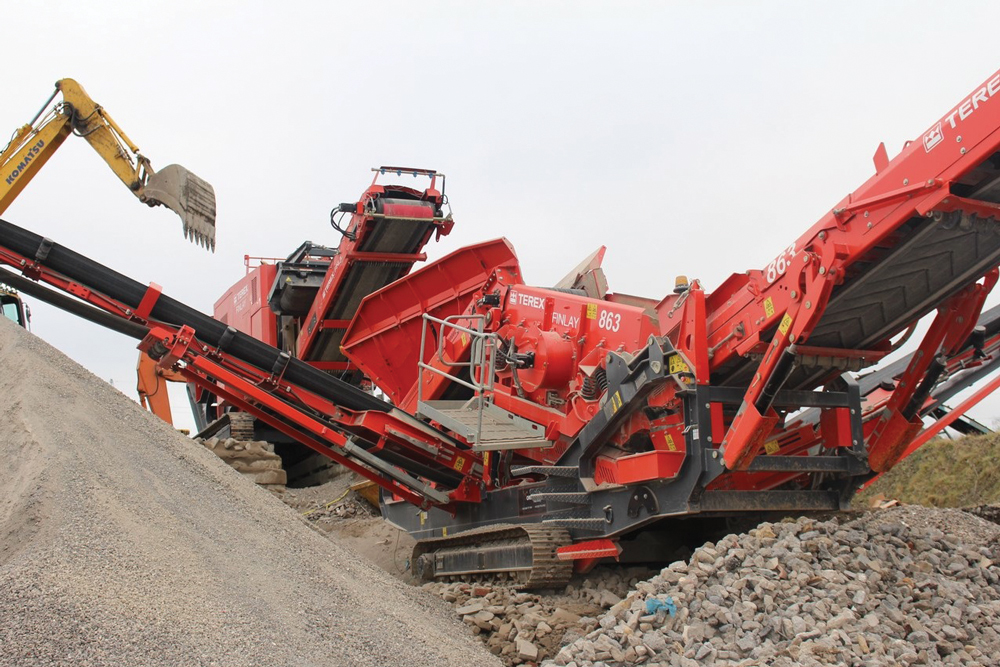
First published in the November 2017 issue of Quarry Management
In their latest bimonthly market report, BDS Marketing Research comment on developments in the recycled and secondary aggregates sector
Companies involved in all aspects of the construction and civil engineering industry, and those manufacturing heavy building materials have become regular and committed users of recycled aggregates since they became accepted alternatives to the use of primary (natural) aggregates around 25 years ago. An increasing focus on reducing waste to landfill, reuse and recycling, as well as pressure on costs and margins for end-users, achieving sustainability targets and the protection of natural aggregates reserves, have all been key drivers in their increasing use.
The recycled aggregates market is an area that leading industry consultancy BDS Marketing Research have been reporting on for 20 years, and the primary aggregates market for almost 30. In their most recent report, which has just been published, BDS estimate the market for recycled aggregates in 2016 at just below 50 million tonnes. This represents around 20% of the total market for aggregates in Great Britain and the fourth consecutive annual increase in volume and number of plants.
In defining the recycled aggregates market, BDS have based their research on the production of recycled aggregates from construction and demolition waste at static plants only. Most of these plants are active throughout the year, with some operating intermittently, often by hiring in crushing and screening plant as required, but the location of the recycling site does not move.
The latest report identifies almost 700 individual static recycled aggregates plants, operated by more than 460 separate companies. These include the major primary aggregates producers such as Tarmac, Hanson, Aggregate Industries, CEMEX and Breedon, as well as regional players with multiple large-scale operations, and individual specialist operators with a single plant servicing a local market.
The recycled aggregates sector differs significantly from primary aggregates with regard to company market shares. The largest producer of recycled aggregates accounts for only 4% of total output in Great Britain, with the top 10 companies holding a combined share of around 17%. In primary aggregates the market is much more consolidated, to the extent that the five largest primary aggregates producers represent around 70% of the market. One of the conclusions to draw from this is that there are significant opportunities for growth by acquisition in the sector. In addition, the barriers to entry for the recycled aggregates market are lower than for primary aggregates, making it more accessible for new entrants or expansion by existing players.
The phrase ‘recycled aggregates’ is often used as a generic term that also includes secondary aggregates. This latter title covers a group of products that are produced from the waste output of a separate manufacturing or processing activity. As such, these represent an important, but additional, source of materials for the construction industry and building materials producers, such as ready-mixed concrete and block manufacturers.
There are a number of industries that provide raw materials for processing into secondary aggregates. In Cornwall, around 2 million tonnes of sand are produced annually through the processing of waste generated by the china clay industry. Some of this is transported by rail to markets in London and the South East.
Coal-fired power stations continue to operate in parts of Great Britain, with pulverized fuel ash (PFA) being an important by-product. It is of particular value when processed into a cement substitute. It was announced in October this year that Tarmac, the leading suppliers of primary aggregates in Great Britain and third largest ready-mixed concrete producers, had acquired the remaining 50% share in ScotAsh, a significant supplier of products manufactured from PFA.
Earlier this year Hanson announced the reopening of their ground granulated blast-furnace slag-grinding (ggbs) plant at Teesport Docks, in Middlesbrough. A by-product from the steel producing industry, ggbs is also used as a cement substitute. Previously mothballed in 2009, this investment represents increased optimism in the construction industry. The actions by Hanson and Tarmac also reflect concerted efforts by some of the major companies with integrated operations to secure and control their own sources of supply.
Another increasingly important channel is the processing of domestic, commercial and industrial waste at energy-from-waste (EfW) plants. Those utilizing incineration technologies produce IBA (incinerator bottom ash), which is then processed to produce road sub-base or bulk filler for use in construction and in cement-bound materials. Companies such Day Group, Ballast Phoenix and Raymond Brown Group all operate IBA processing plants. In many cases these are supported by long-term deals signed with major waste companies operating EfW plants in locations such as South Wales, London and Oxfordshire, among others.
Air pollution control (APC) residues are a further output from EfW plants. Carbon8 now have several plants manufacturing lightweight aggregates from APC residues, which are used extensively in the block-making industry.
The secondary aggregates market is estimated by some industry observers to produce in excess of 10 million tonnes of products annually, and is growing. If added to the output of the static recycled aggregates sector, around 60 million tonnes of products are currently being sent to market. This represents around 25% of the total aggregates market, so should be looked at closely for opportunities by existing producers and those looking to invest in the industry.
For more information on any of these markets, contact Andy Sales on tel: (01761) 433035; email: andy.sales@bdsmarketing.co.uk; or visit: www.bdsmarketing.co.uk
- Subscribe to Quarry Management, the monthly journal for the mineral products industry, to read articles before they appear on Agg-Net.com