Forward Thinking
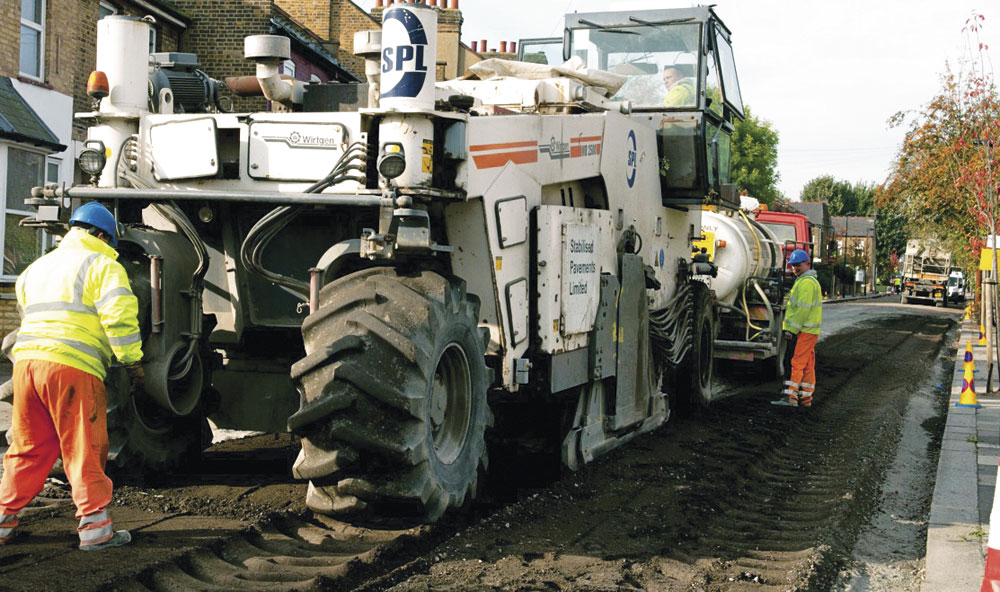
The benefits of in-situ road recycling
Enfield Council has made substantial savings in cost and time, and achieved huge environmental benefits on a series of road maintenance projects in the borough. The Council has saved £1.75million and several weeks work, while at the same time considerably reducing traffic disruption and saving an estimated 59 tonnes of carbon dioxide (CO2) emissions.
These impressive savings, and the bonus benefit of producing a lower carbon footprint, have been achieved by the forward-thinking Council’s decision to reuse the existing material in eight different roads. The Council has treated, strengthened and recycled the material in situ instead of adopting more expensive, slower and more disruptive traditional road reconstruction techniques of replacing old materials with new.
The decision to use the faster, more cost-effective and environmentally beneficial in-situ road recycling method was strongly influenced by the Council’s discovery of hazardous tar-bound materials during testing of core samples taken from the eight damaged roads. ‘We estimated that there were approximately 2,500 tonnes of hazardous tar material in these roads, which would have had to be planed off and taken to a specially licensed tip about 90 miles away in Peterborough,’ said Enfield Council’s principal highways maintenance engineer, Ian Sturrock.
‘The cost of removing the tar-bound material, which has to be treated as hazardous waste, costs more than £100 per tonne and would have been around £250,000 in total. The main cost saving on these roads was achieved by not having to take the tar-bound planings to a licensed tip as hazardous waste.’
Enfield Council is believed to be the first local authority in London to choose to partially reconstruct hazardous tar-bound roads by in-situ recycling, instead of using conventional full-depth pavement reconstruction techniques with new bituminous materials. ‘Roads constructed in the UK prior to 1980 or surface dressed prior to the late 1980s may contain tar,’ said Mr Sturrock. ‘Programmed maintenance works on these roads may, therefore, involve excavation of materials containing tar, and disposing of them to landfill is expensive and unsustainable.’
According to the Council, the cost of traditional reconstruction of the eight tar-bound Enfield roads would have been approximately £2.5 million – just over three-and-a-half times the cost of the £0.75 million for the in-situ recycling process. Treating the roads in situ also took about a third of the time needed for traditional reconstruction, thereby also considerably minimizing disruption to residents and local traffic, and saving on extended road-closure costs. In addition, an estimated 59 tonnes of CO2 emissions between in-situ recycling and conventional reconstruction has been saved on this road works programme.
‘You don’t normally associate recycling with roads, but we’re looking at all of our options and found that this is a really unusual but efficient way of saving a lot of money,’ said Enfield Council’s cabinet member for the environment, Chris Bond. ‘This scheme helps reduce the amount of hazardous waste we produce, reuses valuable raw material and saves the taxpayer money. We’ve been forced to deal with unprecedented government spending cuts and this is an innovative way of making every penny we spend count.’
Cold in-situ recycling contributes to considerably reducing CO2 emissions as the technique vastly reduces the need for extraction and transportation of existing in-situ materials to landfill sites, and the production and transportation to site of virgin materials extracted from natural sources.
‘In-situ recycling has proven to be less disruptive to local traffic than conventional reconstruction, as we have saved about 300 movements of 20-tonne wagons and improved our carbon footprint,’ said Ian Sturrock. ‘The advantage of recycling, compared with other methods, is that the work can be completed quickly with minimal disruption.
‘Additionally, scarce resources will be saved by recycling the road and there will be a reduction in CO2 emissions. Recycling the road is quicker, more cost-effective and better for the environment than conventional replacement.’ Mr Sturrock added that the process is carried out in accordance with the Transport Research Laboratory (TRL) Report’s 386 and 611: Design guide and specification for structural maintenance of highway pavements by cold in-situ recycling and A guide to the use and specification of cold recycled materials for the maintenance of road pavements, respectively.
The in-situ recycling process used on the eight Enfield tar-bound roads initially involved the top uncontaminated layer being planed off and disposed of as reusable road planings. Then the underlying damaged sub-base layers of each of the roads were broken up and rotovated by a special machine to a depth of 200mm. A layer of cement blended with pulverized fuel ash (PFA) was spread over the surface of the rotovated material. The special in-situ recycling machine returned to rotovate and mix the cement and PFA blend into the material to the full 200mm depth, while at the same time water was added into the mix to produce the required optimum moisture content.
Any excess material was taken off site and mixed with crushed concrete before being used in the Borough’s roads and footways as Type 1 sub-base. The in-situ stabilized and strengthened material was then compacted with a roller, re-profiled and rolled again, prior to spraying the surface with a bonding tack coat and covering it with grit so that the road could be temporarily opened to residential traffic. The recycled road was subsequently paved with a new 50mm thick surface layer and opened to full traffic.
The mix recipe for the recycled, stabilized and strengthened material was designed and determined from testing and analysing core samples taken from the tar-bound roads. The cement and PFA complement each other as the cement provides an initial strength gain for the recycled road materials, while the PFA slows hydration and contributes to increased strength over time.
The in-situ recycling at Enfield was carried out by specialist road recycling and stabilization contractors Stabilised Pavements Ltd. The company, based in Lutterworth, Leicestershire, used its purpose-built 500kW Wirtgen WR2500 cold recycler, which is capable of pulverizing to a depth of 320mm, to treat and stabilize in situ nearly 13,000m2 in the eight roads and provide a 20-year design life for 0.5 million standard axles.
‘I believe our in-situ recycling technique has to be the way forward for treating tar-bound roads in the UK,’ said Stabilised Pavements director Gerry Howe. ‘It also provides the bonus of a saving on CO2 emissions.’
Ian Sturrock concluded: ‘This has been my first experience of in-situ recycling and I anticipate using it on similar road-strengthening schemes in the future. Enfield is probably not alone with roads containing tar-based materials and this process could save other London boroughs a fortune in disposal costs.
‘Up to a fifth of our budget could be spent on tar removal and that money, which would have been needed for disposal, can now be directed straight into treating and repairing in-situ failed tar-bound roads. SPL have done an excellent job for us on these first roads that we identified as containing tar and we anticipate they will be returning in the spring to continue on the next programme of works.’
For further information contact Stabilised Pavements Ltd on tel: (01858) 880499; email: info@stabilisedpavements.co.uk; or visit: www.stabilisedpavements.co.uk