Exploring The Synthetic Aggregates Alternative
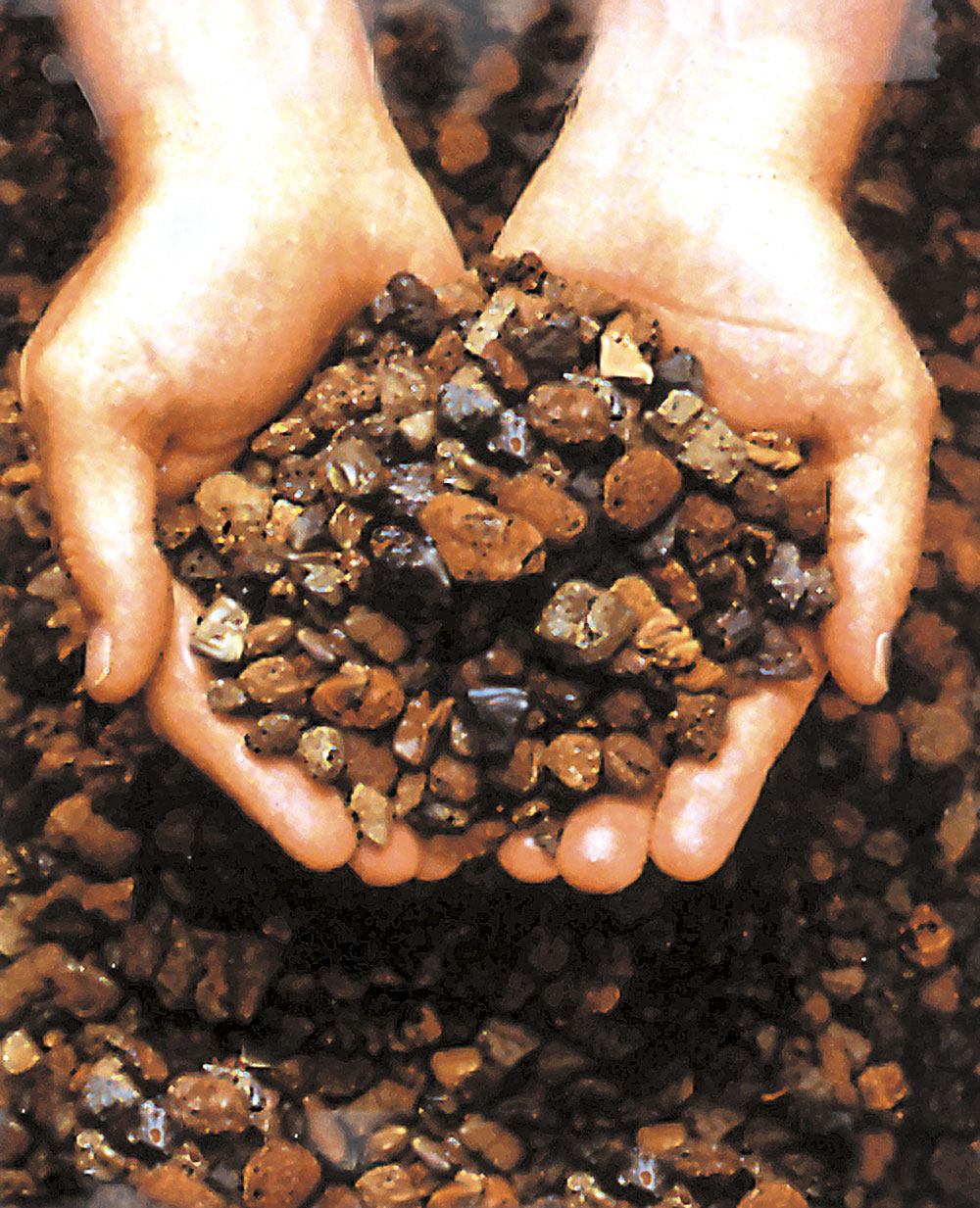
Although relatively new, synthetic aggregates hold the potential to become a true competitor in certain applications
By Tom Kuennen, contributing editor
Synthetic aggregates — also known as lightweight aggregates — are quickly becoming known as ‘heavy hitters’ to those material specifiers looking for an alternative to natural aggregates.
These aggregates fall broadly into two categories: pyroprocessed ceramic aggregates formed by intensely heat-treating natural matter such as clay, shale or slate, and an even newer product formed by intensely heat-treating reclaimed industrial by-products and post-consumer plastics.
Both types of materials are referred to as ‘lightweight aggregates’ because they weigh less than 70 lbs/ft3 and more than 55 lbs. Aggregates weighing less than 55 lbs/ft3 are used in insulation, among other applications, but are too weak for use in robust applications.
The ceramic lightweight aggregates are much more established in construction than those based on recycled materials. Ceramics have already been shown to perform in Portland cement concrete for bridge decks and pumped concrete for high-rise construction; their use provides a strong concrete that weighs less than concrete made with traditional aggregates. They can also be used in hot-mix asphalt, although this is a marginal application.
In road construction, ceramic lightweight aggregates are most commonly used in chip seals (surface dressings), where their porous structure ensures superior bonding with the asphalt emulsion, and they have shown the ability to stand up to traffic and provide superior skid-resistance.
While research is just getting under way on the merits of lightweight aggregates made from recycled materials, it has already been shown that the plastic content of this synthetic aggregate forms a unique bond with hot liquid asphalt that can lead to pavement performance benefits.
Will these synthetics ever replace natural stone and gravel in construction applications? Certainly not any time soon. But they are competitive for specific applications today, and the menu of applications is expected to expand in the years to come.
Pyroprocessed aggregates
Ceramic aggregates are made by heating shale, clay or slate to temperatures in excess of 1,000°C in a rotary kiln. This process, called ‘pyroprocessing’, causes the material to expand into a synthetic lightweight aggregate (SLA), according to the Expanded Shale, Clay and Slate Institute (ESCSI).
Clay is a very fine-grained, moisture-retentive, naturally occurring material composed principally of silicates of alumina, derived from the decay of igneous micas and feldspars, such as found in granite. Sedimentary rock made from clay is called shale, and if it is metamorphosed it becomes slate. Thus pyroprocessing of all three materials results in essentially the same product: a lightweight aggregate that is ceramic in nature.
Another expanded industrial by-product is lightweight blast-furnace slag aggregates, produced as a non-metallic by-product during the smelting of iron and steel. At temperatures between 1,200°C and 1,400°C molten slag is combined with carefully controlled amounts of water. This causes steam to form and quickly cools the slag. A cellular structure within the slag particles is formed from the expansive action of the entrapped water as it turns to steam and from the reaction of small amounts of constituents in the slag with the water vapor. The slag is usually crushed after the cooling process.
Special uses
Bridges and concrete: In bridges and other structures, lightweight aggregates result in lightweight concrete, with some very big benefits. Weight reduction optimizes land use by affording a smaller footprint, and it uses less building materials.
‘The reduction in foundation loads may result in smaller footings, fewer piles, smaller pile caps and less reinforcing,’ says ESCSI. ‘Reduced dead loads may result in smaller supporting members (decks, beams, girders and piers); [and] reduced inertial seismic forces.’ With bridge construction or re-decking, this may allow a wider bridge deck with additional lanes to be placed on existing structural supports, with minor or no modifications.
Compacted fills and geofoam: Compacted fills made of lightweight ceramic aggregates are about half the weight of fills using common materials. This load reduction, coupled with the high internal friction angle of the lightweight aggregate, can reduce vertical and lateral forces by more than half. As a result, ceramics have been used to solve numerous geotechnical engineering problems, and to convert soft and unstable soil into usable property. According to ESCSI, pyroprocessed lightweight aggregates also provide durable, inorganic insulation around water and steam lines, and other thermally sensitive elements, because of their high thermal resistivity.
Chip seals: ESCSI also claims that lightweight ceramic aggregates form a superior bond to asphalt in chip seal applications, resulting in a significantly improved surface treatment that is safer, more economical and longer-lasting than conventional aggregates.
‘Wet or dry, road surfaces of lightweight chip seal provide superior skid-resistance that is maintained throughout the surface life,’ says ESCSI. ‘Lightweight aggregate does not polish as it wears, and because it is light in weight, there are transport and handling cost advantages for the contractor.’
The newly released National Cooperative Highway Research Program (NCHRP) Synthesis 342, Chip Seal Best Practice, cites third-party research that confirms many of ESCSI’s claims. One comprehensive report concludes: ‘lightweight aggregate proved to be a highly successful cover aggregate for chip seals.’ Another study found that ‘lightweight synthetic aggregate furnished a superior ability to retain its skid-resistance’ and, later, that they ‘carry the additional benefit of a significant reduction in windshield breakage claims, because their specific gravity is approximately 25% of that of natural stone aggregate.’
The same study also pointed out that lightweight aggregates are generally more expensive than natural aggregates and may have high water absorption. A survey undertaken for the new NCHRP synthesis indicated that 29% of US road agencies used lightweight aggregates in chip seals, compared to 43% in Australia, New Zealand, the United Kingdom and South Africa.
‘Plastic’ aggregates
The newest type of synthetic aggregate is formed primarily or entirely from reclaimed materials. The primary components are usually reclaimed plastic and high-carbon-content fly ash from coal-burning power plants.
Some states’ recycling programs encourage lightweight aggregates made from reclaimed materials. New York State, for example, has determined that coal-combustion bottom ash can be used as a component of asphalt or traction agents on roadways, car parks and driving surfaces, and that coal-combustion fly ash or gas-scrubbing products may be used as an ingredient of lightweight aggregate.
Another potential material for this type of lightweight aggregate comes from the air pollution ‘scrubbers’ in high-sulphur-coal-fired power plants. In this process, limestone in the scrubbers combines with sulphur compounds in the flue gases to create gypsum compounds, and the recovered ‘flue gas desulphurization’ sludge can be used to form synthetic lightweight aggregates.
At Tufts University and the University of Massachusetts at Lowell, researchers are studying high-carbon-content fly ash and 100% reclaimed post-consumer plastics that are combined into an extruded and granulated aggregate. ‘We are looking at synthetic aggregate using 100% waste materials as raw input,’ says Dr Chris Swan, associate professor and chair of the Department of Civil & Environmental Engineering at Tufts University. ‘Our aggregate is made, not mined.’
Dr Swan’s process combines up to seven different types of recyclable plastic to eliminate the high cost of sorting and separating them. He also uses high-carbon fly ash that otherwise would be landfilled because its carbon content exceeds 6%, the cut-off for fly ash that can be used as a concrete admixture.
‘We are taking the worst fly ash that would have been landfilled, and are not competing with the concrete industry for this product,’ Dr Swan stresses. ‘With only 33% of all produced fly ash reused, we are combining that poor quality fly ash with the worst plastic to create a useful aggregate.’
Performance report card
A 2001 TRB paper co-authored by Dr Swan, ‘Lightweight Fly Ash/Plastic Aggregates in Concrete’, shows that lightweight concrete can be manufactured with fly ash/plastic synthetic lightweight aggregates, although the strengths were relatively low in comparison to equivalent batches of concrete with traditional lightweight and normal weight aggregates.
While plastic/fly ash aggregate lacks the compressive strength of conventional aggregates, Swan found that it has other unique benefits. ‘Concrete made with our synthetic aggregate is much more ductile. It will have some residual strength after reaching a peak value. Most concrete, once it snaps, it is finished. In our case, you actually get some residual strength or resilience, with additional load deformation capability. Our concrete, while it is not as strong as that using regular aggregate, provides an increase in the ductility that would be beneficial in sudden loadings like auto accidents or even earthquakes.’
By using partial substitution of this material for conventional aggregates, concrete will retain its conventional strength while gaining ductility, Dr Swan said. This will make it appropriate for bridge decks, pavements and other outdoor structures.
Dr Swan’s aggregate also has some significant advantages with hot-mix asphalt because a chemical bond develops between the plastic in the aggregate and the hot liquid asphalt in the mix. ‘With hot liquid asphalt, the (synthetic aggregate) will not melt or disintegrate,’ he observes.
‘What you do get is a partial melting — a very nice surface bonding between both substances, which are both derived from petroleum. The plastic in the aggregate makes a much better matrix bond with the asphalt binder and you get a much better asphalt pavement as a result.’
Dr Swan’s contentions are borne out in a 2004 TRB paper, ‘Evaluation of Use of Synthetic Lightweight Aggregate (SLA) in Hot Mix Asphalt’, in which the authors Hooper, Mallick, O’Brien and Kashi found an enhancement of both strength and stiffness of hot-mix asphalt with the addition of aggregate containing fly ash and reclaimed plastic.
The road ahead
Lightweight aggregate technology is in the early stages of evolution. Ceramic aggregates are well established for chip seal applications, but their use in other applications is in the early stages of acceptance.
Synthetic aggregate formed from fly ash and plastic is even less advanced, as it is just beginning the voyage from the laboratory to test applications.
Nevertheless, both types of product are likely to garner ongoing attention from road professionals as they offer important potential solutions to some of the problems ahead.
This article first appeared in Aggregates Manager magazine in the US and is reprinted here by kind permission.