Big Savings With In-situ Road Recycling
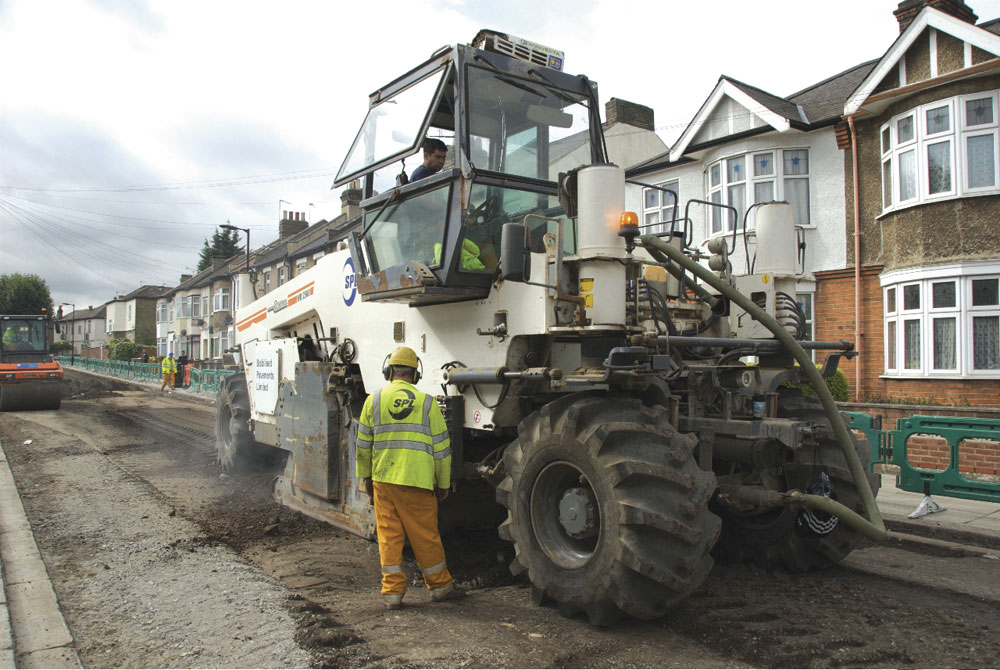
Newham Borough Council benefit from cost, time and environmental savings
The first road to be repaired in London in the last 20 years using the in-situ recycling process of rejuvenating and strengthening the existing damaged road materials has provided considerable cost, time and environmental savings for Newham Borough Council. The Council’s highways department saved around £80,000, four weeks of disruption and over 9 tonnes of CO2 emissions by conducting in-situ repairs to Dersingham Avenue – a one-way residential road on a major bus route with heavy parking on both sides.
Vehicles running along the central strip of the carriageway had been using the same wheel paths, resulting in severe deformation, rutting and potholing. Repairing the damaged road using conventional reconstruction techniques would have cost around £320,000 and taken about seven weeks, but by adopting the in-situ recycling process Newham BC was able to considerably minimize disruption for residents by eliminating about 90 movements of 20-tonne wagons and completing the carriageway repairs in just three weeks, at a total cost of around £240,000.
The Council highways department’s consulting engineers, Jacobs, produced the design philosophy of in-situ recycling just the central, heavily trafficked strip of the road and inlaying the less trafficked edges. Then, term maintenance contractors F M Conway, based in Dartford, Kent, carried out the necessary preparatory works prior to a start on the in-situ repair part of the project. This was subcontracted to specialist road recycling and stabilization contractors Stabilised Pavements Ltd (SPL), based in Lutterworth, Leicestershire.
SPL rejuvenated just under 3,800m² of the road using the in-situ recycling process and provided a 20-year design life of 2.5 million standard axles. For the in-situ recycling work, they used their 500kW Wirtgen WR2500 recycler with a multi-tooth rotating drum cutter. The machine can rotovate a road to full depth while simultaneously delivering accurately metered quantities of water, bitumen emulsion or foamed bitumen into the mixture to strengthen and rejuvenate damage pavements in compliance with client specifications. On this particular contract, SPL used a blend of Ordinary Portland Cement with pulverized fuel ash.
SPL began by pulverizing the damaged road pavement to the required depth of 250mm. This was then reshaped using a motor-grader and lightly compacted back to the finished level by a Hamm HD90 double-drum vibratory roller. Blended OPC/PFA was then accurately applied in a thin blanket across the surface by a special lorry-mounted spreader, at a ratio of 8% by volume of the material’s dry density. This was mixed in a single-pass operation by the Wirtgen, to the designated depth. At the same time, water was injected into the mixture, from nozzles in the crown of the WR2500’s rotovating drum chamber, to achieve the required material moisture content.
During the process, the independent materials testing laboratory Bureau Veritas took samples to test and verify the design recipe. The rejuvenated and strengthened road base material was then re-profiled and levelled with the grader, prior to several passes of the Hamm roller to finally compact the strengthened road base to 95% of refusal density.
Once the required level and compaction had been achieved, the in-situ repaired section of the carriageway was sprayed with a sealing tack coat and gritted as a temporary running surface. F M Conway then followed on by overlaying the full 6.6m width of Dersingham Avenue with a 60mm thick asphalt binder course followed by a 30mm surface course for a full and final return to traffic.
‘This is the first time in the last 20 years or so that in-situ recycling has been used to repair a damaged road in London,’ said Stabilised Pavements director Gerry Howe, who has over 30 years’ experience of the process. ‘The process is much faster, cheaper and less disruptive to traffic than conventional repairs, and also has a much lower carbon footprint. On this job we have saved about 9 tonnes of carbon dioxide emissions, so it is also far more environmentally acceptable.’
F M Conway senior contracts manager Paul Padfield added: ‘The overall project only took three weeks, with the in-situ repair taking just four days. I’m not aware of any other similar schemes programmed at the moment, but if the right job came along I would push to use the in-situ recycling technique again.’