A New Approach To Waste Management
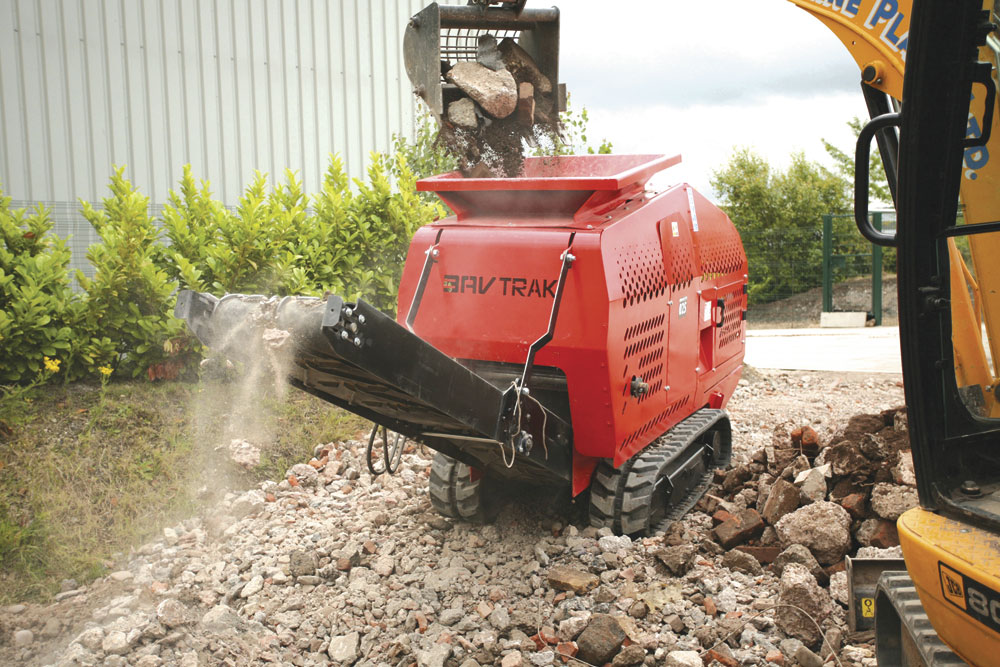
As the construction trade braces itself for the introduction of Site Waste Management Plans (SWMPs) and the prospect of more EU legislation, Digbits’ managing director, Marcus Clay, takes a look at how recycling measures will force quarry managers to re-evaluate their traditional business models
This month sees the introduction of new regulations that mean any construction project in England costing over £250,000, whether new build, maintenance, alteration, installation or removal of services, such as sewage or water, will need an SWMP. Put simply, every principle contractor will have to state how their building materials and resulting waste will be managed throughout the entire project.
A cornerstone of the Government’s new approach to waste management is the Proximity Principle, which states: ‘waste should be managed as close as practicable to the point at which it is generated’. This means if construction managers can recycle on site, then they must do so. The Proximity Principle is also reinforced by waste-transfer legislation, which means that, strictly speaking, if waste concrete and brick is moved from a site – even it is taken back to a base for recycling – a waste carrier’s license is required. On top of this, planning authorities are increasingly using the planning process itself to dictate recycling. This raises some serious questions for quarry managers across the country regarding their traditional business avenues.
Of the 280 million tonnes of aggregates used every year in UK construction, only 25% is currently from recycled sources, but these new regulations will make all contractors more accountable for the entire site. Failure to comply will hit hard, with fines in the UK already set at up to £5,000, enforceable by both local councils and the Environment Agency. These fines are on top of other potential fines that companies may unwittingly incur, including those for unlicensed waste carrying, even if it is backwards and forwards to a quarry.
For decades, larger developers, especially on brownfield sites, have had to take a ‘whole site’ approach to jobs. They investigate and evaluate risks below ground, such as contamination, and also look at the potential risks above ground, such as asbestos or unsafe structures. They also know that on larger sites they will generally be required to recycle any concrete and rubble and keep vehicle movements to a minimum.
The real problem facing the industry is not the regulations, or a lack of affordable solutions, but the lack of awareness. A survey conducted through the Federation of Master Builders has found that although awareness of Site Waste Management Plans (SWMPs) has increased from 34% of those surveyed in January this year, to 62%, 38% were still unaware that SWMPs are set to become a legal requirement. However, this gives quarry managers a great head start to begin to educate their customers on how they can overcome the change in legislation and, at the same time, address and resolve the same issues that will affect their business.
There is a real gap in the market to supply smaller developers with access to on-site aggregate crushing machines as and when they are needed. Quarry managers are in the ideal position to re-evaluate their traditional lines of business and embrace the change by swapping emphasis from skip and lorry hire to recycling machinery, which could ultimately prove to be very lucrative. Alternatively, with large amounts of available space to site 50-tonne crushing machines, quarries can cater for larger developers who need to recycle aggregate and rubble in volume but cannot do it on site because of dust or noise restrictions.
Manufacturers, including Digbits, are already investing heavily in developing new tools for compact concrete and rubble recycling to address the imminent change in legislation. There is a real demand from smaller developers for an effective crusher that weighs less than three tonnes and is able to access restricted sites. Digbits’ BAV crushers are fast, straightforward and safe to operate with good manoeuvrability and plenty of crushing strength. Three grade options make it simple to adjust the size of the crushed material without the need for extra tools.
The 2.95-tonne Bavtrak 025 is the latest aggregate crusher to be developed by Digbits. Using patented ‘alligator crusher’ technology to process concrete, rubble and reinforcing wire, the machine can transform heavy waste into variable grades of reusable hardcore on a wide variety of demolition sites. Measuring 1,200mm wide by 4,550mm in length with 300mm wide rubber tracks, it is powered by a two-cylinder air-cooled Hatz ‘Silent Pack’ engine that produces 33hp (24.4kW) net flywheel power at 3,000 rev/min.
The Bavtrak 025’s generous 630mm x 330mm jaw feed area allows it to process large, single chunks of concrete, as well as making it less susceptible to jamming, while its hydrostatic twin-jaw crusher ensures that brick, concrete or stone are reduced with ease.
Moreover, by increasing the size of the hopper feed, developing patented designs to ensure operator safety on site, using hydrostatic jaw crusher systems, tailoring the size, weight and manoeuvrability of the machine, as well as removing the need for an operator to marshal the concrete, Digbits say they have been able to overcome many concerns from contractors and have developed a machine that offers a more effective and easier to maintain solution for hirers.
With the entire industry having to face up to the impact of SWMPs, construction and project managers will be looking for simple and cost-effective solutions that can be put in place quickly, and what better place to turn than their local quarry – somewhere they already know, use and trust. And, with quarry managers having no choice but to change and adapt to remain viable, the ability to offer recycling facilities either within a quarry or by investing in equipment that can be hired out, it may just be that everyone will come out of the Government’s latest environmental drive feeling less ‘crushed’ than they might have imagined.