Twin-Shaft Mixer Boosts Quarry Yield
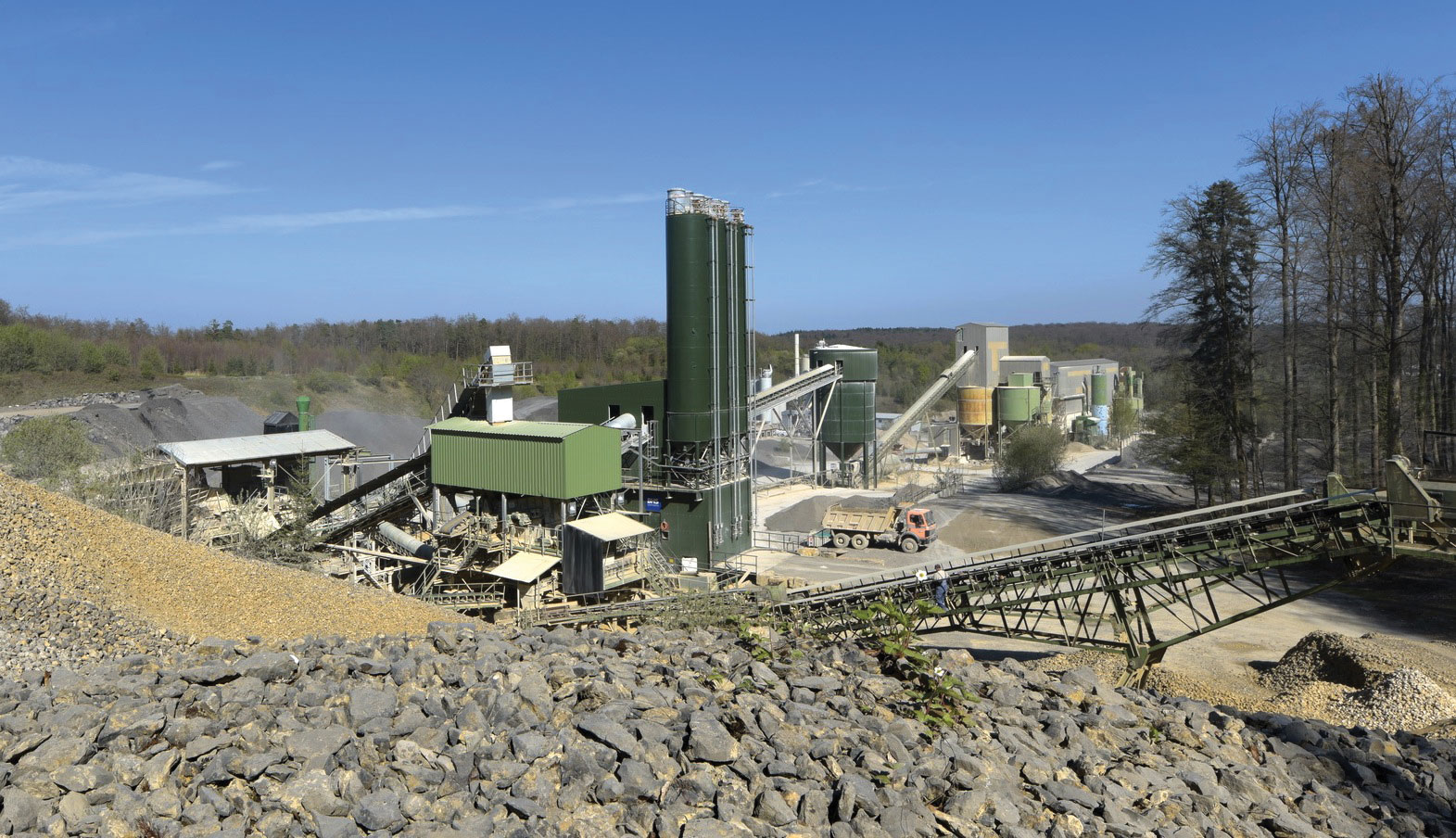
First published in the August 2018 issue of Quarry Management
A German limestone quarry is using a BHS twin-shaft mixer to add quicklime to clay-contaminated pre-screened material, making it possible to completely separate the clay from the rock, most of which can then be processed for sale. As a result of this dry process, 70% of material that was previously being sent to landfill is now usable, as Gerd Schuler and Stefan Kunkel explain.
German quarry products suppliers MSW Mineralstoffwerke Südwest GmbH & Co. KG – a subsidiary of Heinrich Mertz Kies- und Sandwerke GmbH & Co. KG – operate a limestone quarry in Mönsheim, near Stuttgart, producing aggregates mainly for use in road construction.
The shell limestone extracted at the quarry contains large quantities of clay, which used to mean that, on average, 30–35% of the extracted material could not be sold. The pre-screened material comprising a mixture of clay and rock had to be deposited in the quarry as landfill. Therefore, MSW decided to look for a way to increase the yield of ongoing operations at the site whilst, at the same time, making it possible for stored waste material to be made usable.
One method of removing clay from pre-screened material involves wet processing in a log-washer. However, the volume of water available at the Mönsheim site was insufficient for this method. Aside from this, the mandatory water treatment and slurry disposal would have been very complex and expensive.
The solution
For the last six years, a nearby quarry company affiliated with MSW has been running a BHS-Sonthofen MFKG single-shaft continuous mixer for the conditioning of dust extracted from its aggregate processing plant. During a visit by Mönsheim quarry staff to see this mixer, discussions turned to the planned processing of pre-screened material.
BHS-Sonthofen personnel pointed to the successful processing of clay and rock mixtures in France, where BHS mixers use the dry Combimix process to make around 90% of contaminated feed material usable. BHS developed the method for this application for French companies that were seeking an economical and environmentally friendly solution suitable for industrial processes. These companies include international market leaders such as CEMEX Granulats and LafargeHolcim, as well as medium-sized companies such as Gachet TP, an innovative producer of construction and recycled materials.
The process of mixing the clay-contaminated pre-screened material with quicklime in a BHS twin-shaft mixer changes the properties of the clay. The mixing process dries out the clay, while the mechanical stresses imparted by the mixing tools cause it to detach and separate from the rock. Following this separation, the valuable rock fraction can easily be screened from the clay and fed to the next processing step.
This alternative approach was so attractive to the management of MSW that they immediately sent material from the quarry at Mönsheim to
BHS-Sonthofen’s technical center for testing. After just four days the first tests using a laboratory twin-shaft mixer were initiated at Sonthofen, in southern Germany. Within minutes it became clear that the mixing process was delivering the desired outcome. This finding was confirmed by several additional tests, which involved analyzing the sample at the MSW laboratory. These tests showed that adding 1–3% of quicklime delivered promising results, even after short periods of mixing.
The project
However, still missing was evidence that it was possible to consistently clean larger quantities of material with a specified maximum particle size of 120mm. It was also necessary to test the response of the existing processing system, which includes screens and a finger roller screen. For this reason, MSW and BHS-Sonthofen joined forces with the suppliers of the quicklime, Märker Kalk GmbH, to perform a large-scale test at the quarry. This test showed that the processed material was clean and usable, even if the feed material contained large stones. Subsequently, MSW gave the project go-ahead and, with the help of BHS, redesigned the plant based on the new mixer. It was possible to use existing components for the steel construction, and three large silos for binding material were already available on site.
The technology
Today, approximately 1% of quicklime is added to the twin-shaft mixer containing pre-screened 0–120mm clay and rock mixtures, whereupon the proven three-dimensional mixing principle utilized by the BHS-Sonthofen twin-shaft mixer is a key factor in achieving good results, whilst a material retention time of 90s provides sufficient time for the lime to be thoroughly mixed and react with the clay-contaminated rock. The vigorous movement of material during mixing further assists the cleaning process.
Up to 520 tonnes/h of stone is fed into the plant. From this initial feed material, the roller screen separates out 240 tonnes of clay and rock mixtures with a particle size of 0–120mm and delivers it to the BHS mixer.
The mixer output is screened using a 22mm finger roller screen. Each hour, 150–180 tonnes of clean material with particle sizes larger than 22mm are fed back into production. In this way, raw material utilization increases to more than 90% from its previous level of approximately 65%.
Clay-contaminated waste material with particle sizes of 0–8mm can be sold as dam-building material, while material with particle sizes of 8–16mm can be monetized as loose aggregates.
Initial experiences
MSW officially commissioned the plant in June 2016. Today, it is fully integrated into the Mönsheim quarry’s production processes. Since commissioning, the mixer has been running reliably and expectations for the output material have been met in full. After the additional processing step of crushing and screening, the material is clean enough to be sold. This has been confirmed by test reports from recognized testing bodies that perform third party monitoring of the facility.
Experience gained in the first few weeks showed that the addition of approximately 0.8% quicklime to the dry material results in a very good separation of the clay and rock mixture.
About 70% of the material that would previously have been deposited as landfill is now usable. Before implementing this process the maximum volume of saleable material that could be produced was 280 tonnes/h. Supply capacity has now increased to 430–460 tonnes/h. In other words, to produce the same quantity of goods per year, MWS would previously have needed to extract around 620,000 tonnes of limestone. The company now extracts about 432,000 tonnes, which corresponds to a relative reduction of approximately 30%.
Thus, the new process conserves limestone resources and extends the usable life of the quarry. Furthermore, the plant’s daily operating period is now considerably shorter; it is in operation for 2h less each day, which results in reduced energy and personnel expenses.
This benefit is reflected in solid business figures. In contrast to wet processing, the dry process does not incur costs for supplying water or for re-slurrying, filtering and disposing of the slurry.
Also, since the entire plant is operating for shorter periods of time, energy costs are reduced by around 19.5%. This translates into a potential reduction in CO2 emissions of around 30 tonnes per year. The shorter production hours lead to cost savings in energy, fuel and personnel, totalling approximately €240,000 per annum. The savings are offset by the cost of buying the quicklime, which amounts to around €120,000 per year. Given annual savings of approximately €120,000, the investment will pay for itself in four-and-a-half years.
This calculation does not take into account the potential of ‘reactivating’ the large volumes of material that have already been deposited as landfill. During times when no quarrying activities are taking place, the new plant can clean clay and rock mixtures that were deposited over a period of two decades because they were considered unmarketable in the past. As a result, several millions of tonnes of additional material can now be processed and sold. Furthermore, valuable landfill space is freed up, and the time spent storing and retrieving material, and distributing it within the landfill, is significantly reduced.
This was the first time that this innovative and resource-saving technology had been used on a large scale for the efficient and sustainable use of raw materials in the construction industry. For this reason, Germany’s Federal Environment Ministry provided MSW Mineralstoffwerke Südwest with funding. After the system was commissioned, BHS-Sonthofen and MSW Mineralstoffwerke Südwest received the German Resources Efficiency Award from the German Federal Ministry for Economic Affairs and Energy for the development and successful implementation of the Combimix process.
About the authors: Gerd Schuler, is mixing & crushing technology field representative with BHS-Sonthofen GmbH, and Stefan Kunkel is plant manager at MSW Mineralstoffwerke Südwest GmbH & Co. KG
- Subscribe to Quarry Management, the monthly journal for the mineral products industry, to read articles before they appear on Agg-Net.com