The ‘Testa Rossa’ Solution
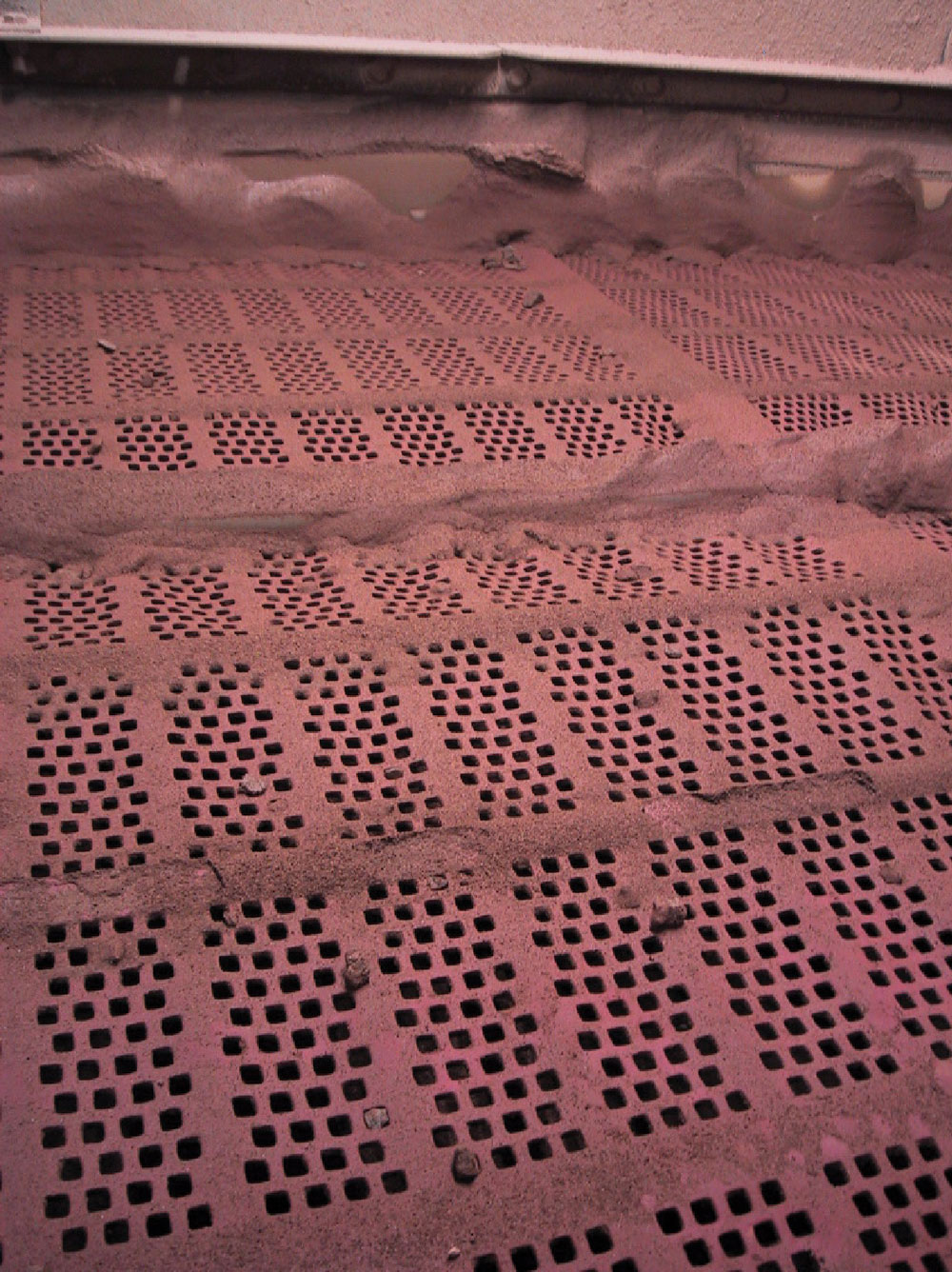
A recent development in the screening of mineral fines
By Brian Mackenzie, managing director of Materials Handling Products Ltd (MHP) and vice-chairman of the Materials Handling Engineers Association (UK)
Despite continuous developments over several decades, the problem of pegging and blinding associated with screening fines and sticky materials continue to be a primary cause of low efficiency and high maintenance in mineral-processing plants. Although several products have been developed to try to address the problem, with varying degrees of success and cost, there remains a major problem to be solved.
Typically, screens become blinded by adhered and agglomerated fines which attach, initially, to the more static parts of the screen media, such as side borders and reinforcement areas, and subsequently extend over the surface of the apertures until, in some cases, throughput is reduced to zero. Mechanical devices have been designed in an attempt to clear this material but always run the risk of damaging the screen media itself, which, by definition, is particularly fragile at this separation size (–6mm).
Frequently, manual ‘de-pegging’ is required, which obviously impacts on production, is extremely time-consuming and can raise health and safety issues, as access is often confined and/or exposed and very dusty. Moreover, such intervention can itself lead to screen membrane damage.
Observations
It has long been established that softer screen media offer greater resistance to material build up owing to the effect of surface flexibility dislodging adhered particles. This is also true of mineral fines handling in general, including chute and hopper linings. One of the original benefits of synthetic rubber screen surfaces over metallic plate screens was the reduction of build-up on the screen surface.
When polyurethane screening systems were first introduced they were confined to wet screening applications owing to their greater tendency to peg and blind when working with dry aggregates. Since then, softer materials with the required mechanical properties have been developed and have proved more successful, and it remains the case that soft rubber offers better ultimate blinding resistance and continues to be the predominant medium, with several proprietary systems on the market.
However, the performance improvement offered by softer rubber is not restricted to difficult-to-screen materials. Surprisingly, even with easy-to-process, wet, rounded alluvial gravel, a significant improvement in the volume of material passing through the screen apertures can be achieved when a softer screen medium is used. In one test, a screen handling this type of material was equipped with 90 Shore hardness modules on one side and 65 Shore hardness modules on the other, but both with the same size apertures. Approximately 5% of the material was rejected by the 90 Shore modules whereas no material was rejected by the softer modules. Although this could be measured quantitatively, the result would be very dependent on aperture size, material type and a number of other parameters, making it of little practical value. It is, therefore, sufficient simply to observe that the phenomenon exists.
Open area is vitally important in fines screening, especially if this is compromised by some of the problems mentioned above. Modular systems often reduce the effective open area owing to the additional structural members required, and this, therefore, favours the use of traditional tensioned media. Recently, however, several open-area systems have been developed which actually offer an increase in the open area over tension mats owing to narrower borders. At typical aperture sizes of 4–6mm, the open area is likely to be less than 20%, so any pegging or blinding has a very significant effect on the overall throughput and screening efficiency. Furthermore, modular systems tend, by their nature, to be more rigid in the support areas, which encourages the initiation of material build-up.
Damage resistance is always a problem on fragile screen media and conventional soft rubber surfaces suffer particularly in this respect. To address this, several proprietary systems use bonded-on reinforcing members to accommodate transverse tensioning forces and to control elongation. These tensioning members give rise to several difficulties, including making the finished screen difficult to manipulate in the confined space of a screen machine, as well as the risk of detachment and limitations on the screening panel size and proportions.
Existing approaches to the problem
There are a number of different, partially effective solutions currently in use, which can be categorized as follows:
1. Soft rubber membrane screens with extra-skeletal tensile members:––considerably better performance than conventional screens
- limited mechanical strength in the screening area
- tensile members make handling difficult
- fixed screen panel sizes
- complex and relatively costly production.
2. Thin-membrane PU modules:
- considerably better performance than conventional screens
- not as resilient as rubber and, therefore, ultimately less effective
- thin membrane vulnerable to damage
- not generally a lower-cost option.
3. Cold-bonded dual-layer rubber screens:
- some improvement over conventional screen
- the lamination process is an inherent weakness and can be overstressed during the punching process
- labour-intensive production increases cost.
4. Soft rubber moulded screens with internal reinforcement:
- currently the best-available anti-blinding performance
- internal reinforcement incorporated where required
- labour-intensive production increases cost.
Development of the ‘Testa Rossa’ solution
In 2005 MHP began a progressive development process to build upon the existing technology, using the company’s expertise and experience as screen media manufacturers, to address the problems of fines screening.
Much of the expertise in screen media tends to be shrouded in ‘black art’ terms, which can often be a cover for lack of understanding of the processes involved. It is certainly true that, as a random process with many variables, precise mathematical modelling can be difficult and is not always justified, as designs frequently need to address local issues, particularly the nature and condition of the material being handled. Consequently, MHP decided to develop the concept in a ‘live’ production situation, which took place with the co-operation of Aggregate Industries and Lafarge Aggregates at two sites handling granite fines.
The development process had several specific objectives:
- To use soft rubber-based screening media to maximize self-cleaning.
- To develop a means of support that offers enhanced structural strength and, hence, damage resistance compared with existing solutions.
- To make use of internal rather than external reinforcement.
- To include some reinforcement in the screening panels themselves, between the apertures, to increase strength.
- To manufacture the apertures by punching rather than moulding to control cost.
- To allow complete freedom of panel size in order to adjust screen performance.
To minimize costs, a specially compounded soft layer with very high abrasion resistance was laminated, by means of hot vulcanization, on to a conventionally manufactured rubber carcass containing polyester tension cords. Previously, this process had been tried with different rubbers using cold bonding, which was inherently less secure and prone to failure owing to the stresses involved in the punching process. With the Testa Rossa solution, the reinforcing component was distributed over the entire area of the screen, allowing complete freedom during subsequent manufacturing, while minimizing the mechanical stresses on the softer component. As a result of this homogeneous reinforcement system, some cords are present in the transverse bridges between apertures, thereby enhancing both their strength and damage resistance.
Having developed a suitable base material, the focus then moved on to the punching process to produce an aperture with a shape designed such that the only part of the screen involved in the sizing is the softer material, with the harder and stiffer reinforcement remaining clear of the process. In effect, this involved the production of a more exaggerated ‘cooling tower’ profile in the rubber than would normally be the case. This was achieved through the use of special tooling design and punching procedures (see fig. 1).
Crucially, as a result of the modified aperture profile, all of the separation takes place in the softer upper layer, with the harder reinforced layer beneath remaining well clear of the material path, resulting in a significant improvement in pegging and blinding.
The area of flexibility was addressed in two ways. First, the punching pattern was designed such that most of the reinforcement would be cut in the screening areas, thereby increasing flexibility. Moreover, this could be varied, as required, making a new control parameter available to the screen designer. Secondly, the method of reinforcement used allows greater freedom to adjust the size of the panel, thus providing more effective control over the natural resonance of the screen and making an additional new parameter available to the designer. This latter property controls the fluidization of the material being screened and also the motion of the screen media itself, which has an impact on surface build-up.
Outcomes
As well as optimizing the anti-blinding/ pegging nature of the screen medium through the use of the new material, two useful new control parameters were created – the differential strength of reinforcement in the screening area and the ability to adjust the natural frequency – in addition to aperture size and pitch.
In practice, some testing and experimentation was necessary to learn how to use these new controls but, after some inevitable setbacks, a set of screens was produced for Lafarge’s Mountsorrel Quarry that virtually eliminated pegging and blinding on a line of 10m x 3m GEC screens handling –6mm granite. This area had previously suffered in excess of 50% blinding and required regular manual cleaning.
Conclusions
The ‘Testa Rossa’ principle has proved to be a valuable addition to the arsenal of solutions for tackling the problems of pegging and blinding in fines screening. It is effective in the 4–20mm size range and benefits from relatively low conventional production costs when compared with alternative systems. Moreover, the freedom to change the size and layout of the screening panels without restriction from tensile support, combined with the option of tuning the resonance of individual panels, has introduced new design parameters that have been shown to be effective in this difficult area of mineral processing.
The ‘Testa Rossa’ principle is protected by worldwide patents pending.