The Continuous Fluid-Bed Dryer/Cooler In Sand Processing
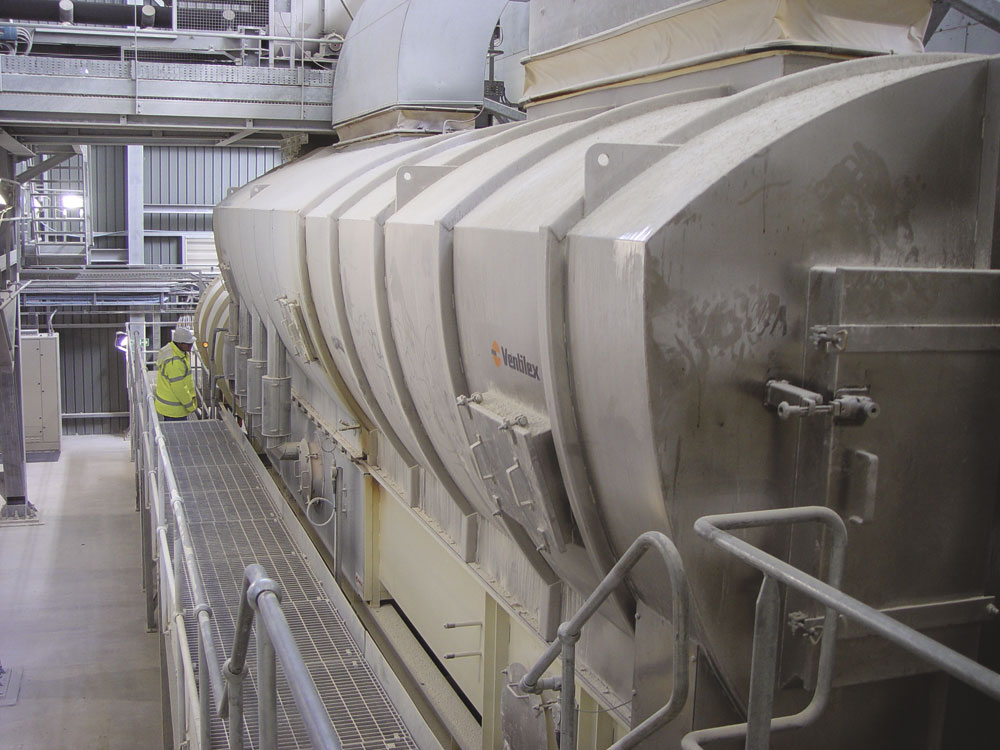
The advantages of continuous fluid-bed drying over alternative sand-drying techniques
A continuous fluid-bed dryer/cooler is a machine in which a continuous flow of damp, granular material is conveyed over a perforated bed, through which air is blown to bring about fluidization. The material is dried in the first section of the machine and cooled in the second. Drying occurs because of the direct contact between the damp material and the hot air blown through it. The air velocity is adjusted to keep the moving layer of material fluidized. The same mechanism applies to the cooling part of the process, except that the air used is either ambient or conditioned (ie cooled). The drying and cooling sections of the machine form a single conveyor in which the hot and cool air flows are segregated. Conveying of the product is achieved either by means of vibration or by the use of a low-frequency, high-amplitude shaker mechanism. This article describes the latter type of machine, which has increasingly supplanted rotary kilns and static fluid-bed dryers as the preferred choice in sand processing during the past few years, particularly in the drying of sand for use in dry silo mortar systems.
In the first stage of drying, free (surface) moisture is removed from the product and all available energy supplied as heat in the drying air is used for evaporation. The temperature of the air moving through the fluidized bed drops as it absorbs moisture up to its saturation point, whereas the temperature of the hot air supply remains constant. In the second stage of drying, after the free water has been evaporated, part of the incoming heat energy is used to remove the residual absorbed moisture and part is used to heat the product. If the temperature of the product at its required final moisture content is known, it can be used to control the dryer. If there is a change in the moisture content of the feed or in the feed rate, the temperature of the air supply is adjusted to maintain a steady product temperature at the exit point of the dryer section.
Drive unit
The shaking action is generated by an eccentric variable-speed drive coupled to a hinged lever mechanism. The dryer/cooler is mounted on pneumatic rubber bellows, in which the air pressure can be adjusted to help achieve the desired mode of movement. The velocity of the product passing through the machine is controlled by varying the shaker frequency (ie the speed of rotation of the eccentric drive); the amplitude remains unchanged. The amplitude of movement achieved by the shaker mechanism is much greater than that normally generated by vibration. Furthermore, the vertical component of the stroke is much higher than the horizontal component. These two factors combine to produce a high degree of lift in the material to be dried, a state that is sometimes described as ‘sub-fluidization.’
Sub-fluidization allows the velocity and volume of the air supply to be reduced, resulting in power savings and a reduction in the amount of fines carried into the dust-filtration system. The bed thickness in normal continuous fluid-bed dryer/coolers is approximately 10–15cm. If the bed depth is increased beyond this level, the spread of product residence time is increased because of the occurrence of lateral mixing within the bed as the material progresses through the machine. This is particularly the case when operating with extended residence times and can cause inconsistencies in product quality. Sub-fluidization makes it possible to operate with bed depths of up to 60cm, even with reduced air loads. The reduction in air flow assists in minimizing lateral mixing within the product bed. It is claimed that residence times in this type of machine suffer almost no spread (ie ‘plug flow’ occurs). The product outlet is equipped with a rotating weir, which continuously controls product discharge. Residence times of up to 2h without the occurrence of undesirable lateral mixing are achievable.
De-dusting of exhaust air
The de-dusting of exhaust air from the dryer/cooler can be carried out using dust filters, cyclones or wet scrubbers. In the case of sand drying, automatically self-cleaning Puls-Jet filter installations are normally used. The filter dust is usually dry and can, therefore, be discharged through a rotary valve, transported to the product outlet by a screw conveyor and mixed with the end product.
Machines driven by low-frequency shaker mechanisms are free of the stresses associated with vibratory equipment. The suction hood may, therefore, be of expanded cross-section and attached directly to the conveyor to form an integral part of the dryer/cooler structure without any risk of it suffering from stress fractures. The expanded volume further reduces the air velocity above the bed allowing a considerable proportion of the entrained dust to drop back on to the bed instead of going to the filter.
Burners
In order to reduce the size of the dryer, the drying air temperature should be as high as possible. Dutch manufacturers Ventilex B.V. typically use the unusually high temperatures of 450–550°C for sand drying. Direct burners are employed and may be fired by natural gas, light fuel oil, propane or heavy fuel oil. The most commonly used fuels are gas and light oil, and dual-fuel burners are available.
Figure 4 shows a typical gas burner, as used in sand-drying installations, built into a specially constructed section of ducting.
High-temperature dryers — design features
As indicated above, Ventilex now use drying air temperatures for sand of up to 550°C, having gradually increased this figure from 400°C. The company claim that this results in greater evaporation per square metre of bed without an increase in air volume. This in turn reduces the power consumption per tonne of sand dried and improves fuel efficiency.
The dryer design must take the special operating conditions into account; specifically, the incoming air chamber must be constructed of steel resistant to high temperatures, sharp corners and edges must be avoided, the structure must be free to expand freely and the whole unit must be efficiently thermally insulated.
The air coming from the cooler section is normally at a temperature of 50–60°C. It is dry and can, therefore, be recycled to the burner inlet, reheated and used again, saving up to 15% of the energy requirement.
Control system
An integrated PLC-based control system is essential for the efficient operation of a continuous fluid-bed dryer. The quality of the software is crucial in ensuring ease of control, rapidity of response and the maximum possible fuel saving. In a typical system the following functions are integrated:
- under-pressure control (under-pressure in the suction hood, controlled by a valve on the exhaust fan)
- product temperature
- exhaust air temperature
- supply air temperature
- product feed-rate control.
Under-pressure control
The amount of exhaust air must be the same as the volume of inlet air plus evaporation. A little extra air is bled from the suction hood to maintain its pressure at 0.5mbar below ambient pressure.
Temperature controllers
PID controllers are usually installed to regulate the inlet and exhaust air temperatures. In the case of sand dryers, the product exit temperature is also controlled.
Standard control systems and the sand dryer control system
In a standard control system the fuel supply is controlled by the exhaust air temperature. The product temperature and the final moisture content are related to the exhaust air temperature, which is set to guarantee that the product temperature is such that the required exit moisture content of the product is always achieved. This means that the product temperature will generally be higher than necessary with a consequent waste of energy.
However, if the fuel input is controlled directly by the product temperature, the latter can be held at the lowest possible level needed to ensure that the product leaves the machine dried to the required extent. The product temperature used by this type of control is set just above the level obtaining at the point at which it starts to rise rapidly (ie when the product is almost dry). This more sophisticated control mechanism saves fuel because of the reduction in the exit temperature of the product.
Set points that can be adjusted by the operator are:
- maximum feed rate
- maximum supply air temperature
- product temperature.
As the product temperature controller is linked with the feed-rate controller, low product exit temperature and low exhaust air temperature are combined with maximum possible throughput rate. Consequently, the system can always run at the maximum capacity of the installation independently of the moisture content of the feed material, if so required.
Advantages
Advantages claimed for the shaker-type of continuous fluid-bed sand dryer/cooler are:
Compared with the rotary drum dryer:
The drying air is more evenly distributed over the product. As a result, the drying air supply temperature and the product exit temperature can be maintained at constant, economical levels, resulting in lower energy costs. Fuel savings of 30% in the drying and cooling of granular dolomite at WBB Minerals’ Warmsworth operation were reported recently in this journal.
The cooler area normally represents about half the size of the unit, and in the dry mortar industry cooling is usually required. A rotary drum dryer requires a separate cooler resulting in a 50–60% increase in the installation cost. A continuous fluid-bed dryer/cooler will always be smaller for a given throughput than a rotary drum installation.
The operation of the continuous fluid-bed dryer/cooler is not influenced by weather conditions and changes in wind velocity and direction. Control is therefore easier, and product quality is constant and maintenance costs are lower.
Most dry mortar plants built in Europe during the past few years include a continuous fluid-bed dryer/cooler. This type of dryer is also commonly replacing rotary drums in a number of older dry mortar plants both in Europe and the US.
Compared with the static fluid-bed dryer
In a static fluid-bed dryer the temperatures of the exhaust air and the dried product are usually 90–100°C and 75–80°C respectively. Comparable figures for a continuous fluid-bed installation are around 60°C and 45°C because of the improved thermal efficiency offered by the ‘plug flow’ characteristics. Consequently, fuel consumption is lower.
Stray oversize pieces of feed material finding their way into a static fluid bed will not be carried out of the machine by the flow of air and will have to be removed manually from time to time. In the case of a continuous fluid bed such oversize lumps are simply and easily conveyed out of the system in the course of normal operation.
Compared with a vibratory fluid-bed dryer
The sub-fluidized type of dryer employs higher drying air temperatures than the vibratory type of machine; 450–500°C instead of 350–400°C. The difference between the supply and exhaust air temperatures is greater. Drying is, therefore, more efficient and less air is required. The result is a reduction in fan size, electricity consumption and the size of the dust filter.
The design is free from the problems of stress cracking and dynamic loadings on surrounding structures are reduced.
The shaker dryer/cooler can operate with a greater bed depth and offer longer residence times. These factors, combined with the higher operating temperature, deliver a higher throughput capacity for a given occupied area.
This article is an abridged version of a paper written by Wilfred Roebersen of Ventilex B.V.