Silt Problem Solved At Whatley Quarry
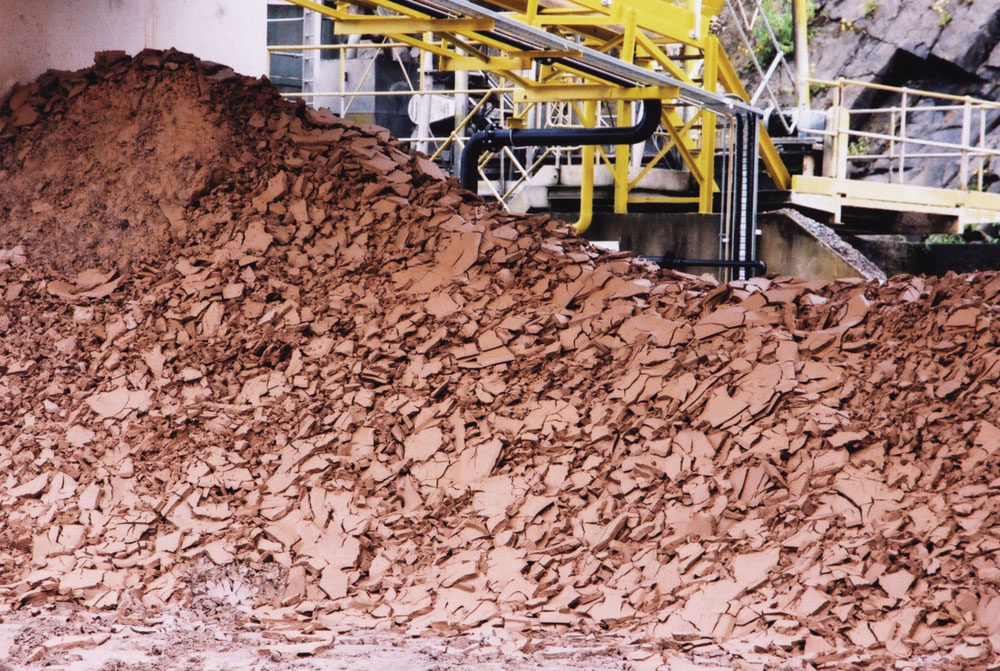
New plate filter press improves washing plant efficiency
The original concept of the washing plant at Hanson Aggregates’ Whatley Quarry, near Frome, Somerset, was to achieve the stabilization of thickened silt by the addition of waste lime collected from the precipitator attached to the lime-burning kiln at the company’s Batts Combe Quarry, near Cheddar.
Commissioned during September 1998, effective production began some four months later, but when the Corus situation at Llanwern began to cause increasing problems with supplies of lime and the production of precipitated dust, which is a by product, trials were carried out using other imported waste materials. However, production capacity was inhibited by the performance of the powders employed, including lime, and as a result short-term storage problems were caused due to overall bulk hardening. The relatively high moisture content also added to bulk volume and handling costs.
Although the washing process produced the desired quality of sand and Type 1 for sales purposes, it was envisaged that a more effective solution to the treatment of slime would be required if the full potential of the washing plant was to be achieved. There followed an extremely comprehensive series of trials, carried out on site and in the laboratory using both belt press and plate filter press plants, with the result that a Latham plate filter press was finally selected.
The press receives the pumped thickened underflow from a 9m diameter deep-cone thickener supplied by Parnaby Cyclones. This is arranged in series with a large-capacity paddle-agitated buffer storage tank. The unit is designed to handle the –75µm waste tailings generated when processing –2mm dust at 90–100 tonnes/h or –40mm scalpings at 120–140 tonnes/h, the aim being to produce a hard, stable filter cake capable of being handled and, if necessary, transported to the waste tip immediately after discharge from the press.
Maximum loadings with either material are estimated at 25 tonnes/h dry solids contained in around 25–35 tonnes/h of wash water, and one of the primary objectives is to minimize wash water consumption rates and resulting make-up requirements, and to reduce overall filter cake transportation costs to the Whatley tip.
Plate filter press performance
The new Latham plant was commissioned at the beginning of June 2002 and entered into full production on 10 June.
Plate filter presses are essentially a batch process comprising successive stages involving rapid-fill, final-cake formation under pressure, and cake discharge. The Whatley press has 139 separate recessed chambers with filter cloths, each chamber measuring 2.0m x 1.5m x 40mm in thickness.
The complete cycle is fully automatic and lasts around 45min. Each filter cake weighs, on average, 0.16 tonnes, which equates to around 22–24 tonnes per pressing, and tests show the achievement of about 85% dry solids operating at 11 bar during the cake formation stage. The press pump has an overall capacity of 14 bar.
From the outset it was clear that the plate filters were able to accept much wider variations in the density of the feed while still producing a hard cake. This was considered to be of great importance, as two different materials with entirely different settlement characteristics are processed at the site.