Sand Solutions
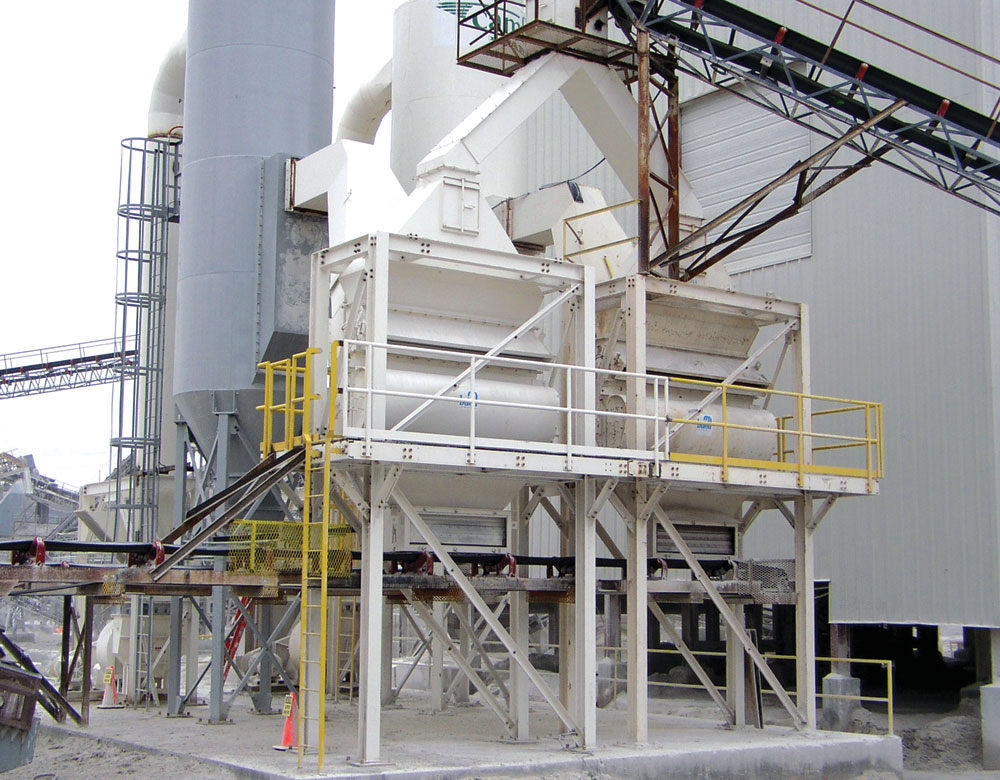
Replacing natural sand in concrete
By Sven-Henrik Norman, product manager, Nordberg AC-series Air Classifiers, Metso Minerals
During the past 10–15 years it has become evident that the availability of good-quality natural sand is decreasing. Apart from a few local exceptions, this seems to be a global trend. The reasons for this also seem to be common around the globe: existing natural sand deposits are being exhausted at the same rate as urbanization, and new deposits are, in many cases, located either underneath or too close to already built-up areas, or too far away from the areas where the material is needed, eg the towns and cities where the manufacturers of concrete are located.
Environmental concerns are also being raised against uncontrolled extraction of natural sand, with arguments mostly relating to protecting river beds against erosion and the importance of natural sand acting as filter for ground water.
All the above, combined with issues of preserving areas of natural beauty, recreational value and biodiversity, are now an integral part of the process of most local government agencies around the world when granting permission for rock, minerals or natural sand extraction.
Because of the situation facing the construction industry today, which most agree will not change dramatically in the foreseeable future, crushed aggregates are now replacing natural sand and gravel in many countries, and statistics from Norway (table. 1) show a trend which is common in most parts of the world.
Manufactured sand – the natural replacement?
For particle sizes from 4mm and upwards, crushed aggregate can generally replace its natural counterpart in most construction applications, unless there are specific requirements for a very rounded shape and smooth surface. This is probably why there has been a natural shift towards crushed aggregates in most markets in the past two or three decades, similar to the Norwegian example referred to in table 1.
For fine aggregates (by European industry standards, those products under 4mm) the replacement of natural sand in concrete is a more complex issue.
Historically, fine aggregate has been a by-product of the crushing and screening process. Due to its rough surface texture, flaky and elongated particle shape and often inadequate size gradation, its performance in most concretes has been poor. Water demand, and subsequently cement demand, has been very high in order to achieve a workable concrete, which has, understandably, caused many concrete manufacturers to shy away from using crushed sand.
In recent years, however, a change has taken place, driven by the sometimes acute need to find a product which can match the properties of natural sand in concrete. A lot of research and development projects have been initiated on a national basis by manufacturers’ associations and by individual companies wishing to be at the forefront of developments.
It is impossible to quickly summarize all the results of this vast body of work, but in general the findings point towards good possibilities of replacing natural sand with crushed fine aggregates. Recent research implies that manufactured sand offers other positive effects on concrete. For example, figure 1 shows a higher 28-day compressive strength achieved with manufactured sand from Velde Pukk A/S in Norway, compared with a high-quality reference natural sand.
An often-noted conclusion in various research and debate forums is that a change of view and mindset is needed. In order to succeed, aggregate producers need to move away from trying to use the ‘waste’ from an aggregate plant as a direct replacement for natural sand in concrete, and instead look at the complete process that is needed to produce a sand with the correct properties. The term ‘manufactured sand’ has emerged as a more fitting description to material which has been produced to meet the quality requirements of the concrete (and asphalt) industry.
For the aggregate producer, however, it is not always easy to know exactly how to define the quality requirements for manufactured sand. While there is a well defined set of standards describing the properties of coarse aggregate (shape index, elongation index, PSV value etc), the requirements for fine aggregate are not so easy to define. For example, particle shape – which is crucial for fresh concrete workability – is not easy to measure and describe for particle sizes from 0.063–0.5mm.
The level of fines
Another important issue is the fines content of manufactured sand. This is often much higher in manufactured sand than in natural sand, due to the fact that the fines produced during nature’s ‘sand production process’ have been washed away. Industry standards, such as ASTM C33 and most concrete producers’ specifications for fine aggregate, allow only limited amounts of fines (0.063–0.125mm particles) in the fine aggregate. Even if recent research and a growing number of commercial examples point towards the advantages of using higher amounts of fines, the optimum amount of fines will vary depending on what type of concrete the sand is intended for. Hence, there is a need to remove the fines and then blend them back in, regardless of the level required.
Research from Chile (CDT – Corporación de Desarollo Tecnologico) has attempted to establish the optimum level of fines for different concrete qualities (fig. 2).
Metso sand solutions
Metso Minerals have identified a need to develop systems and processes that can assist their customers in finding markets for high-quality manufactured sand. To this end, a work group has been assembled to bring together the company’s wide experience in sand production. The solutions Metso Minerals are offering have been optimized from both customer feedback and successes in the field.
In addition, the Metso Minerals sand solution equipment offering has been rationalized based on what is known to work, with efficient crushing and screening systems utilized to reduce production costs and to offer consistent product quality, thereby allowing customers to drive down total production costs while maintaining high product yields.
Circuit selection
To ensure that sand of the highest quality is produced, all feed material must pass the crusher at least once. Crusher selection is detailed in table 2. The preferred circuit selection is post-screen closed-circuit, with oversized material recirculated back to the crusher for further reduction. For screening purposes, TS elliptical-motion screens are preferred, owing to their highly efficient material throughput and accurate separation.
Manufactured sand typically contains an excess of fine material between 0–0.25mm, compared with the concrete grading specification envelope widely used in the industry. This is outside the practical operation range for most conventional vibrating screens, so traditionally these fines were removed using wet process equipment, such as sand wheels or hydrocyclones.
However, the Nordberg AC Series Air Classifier range uses air instead of water to remove the excess fines (fig 3). This offers two main advantages: first, because no water is used there is no need for water treatment or recovery, which can be a costly procedure; and secondly, dry end-products mean potential savings in production costs, as there is less need for drying, which is of particular significance in asphalt production.
Crusher selection
Crusher selection is based on the abrasiveness of the source rock, the feed fraction to the circuit and the nature of the sand required. In an application where there is a long feed curve (ie X–0mm) VSI crushing is the preferred method. Where the feed fraction is shorter (ie X–Y) high-speed compression crushing can be applied. Table 2 shows the range of parameters for the selection of a suitable crusher.
Key criteria in the selection of crushing equipment, which are heavily related to final application, are:
- Product quality
- Consistency
- Yield
- Operating costs
- Filler generation.
Summary
The correct source rock and correct crushing and screening process are the key factors in successful production of manufactured sand. The choice of crushers and screens depends on the feed material and required end-product use, eg ready-mixed concrete, mortar sand, asphalt sand etc.
Metso Minerals believe that manufactured sand will play an increasing role in the future, because the predictability of the end product, in terms of particle shape, gradation and moisture content, will lead to potentially big savings and earnings for both the aggregate producer and the concrete manufacturer.
For the aggregate producer, less waste material will be produced and a high-value sand will increase sales potential. For the concrete manufacturer, savings in cement will be a big motivator. High levels of predictability will also lead to lower costs due to reduced rejection rates.
It is clear that the most suitable replacement for natural sand – a product created by the great forces of nature, albeit in a random process – is a product created by an industrialized and repeatable process.