Prolonging Cone Crusher Liner Life
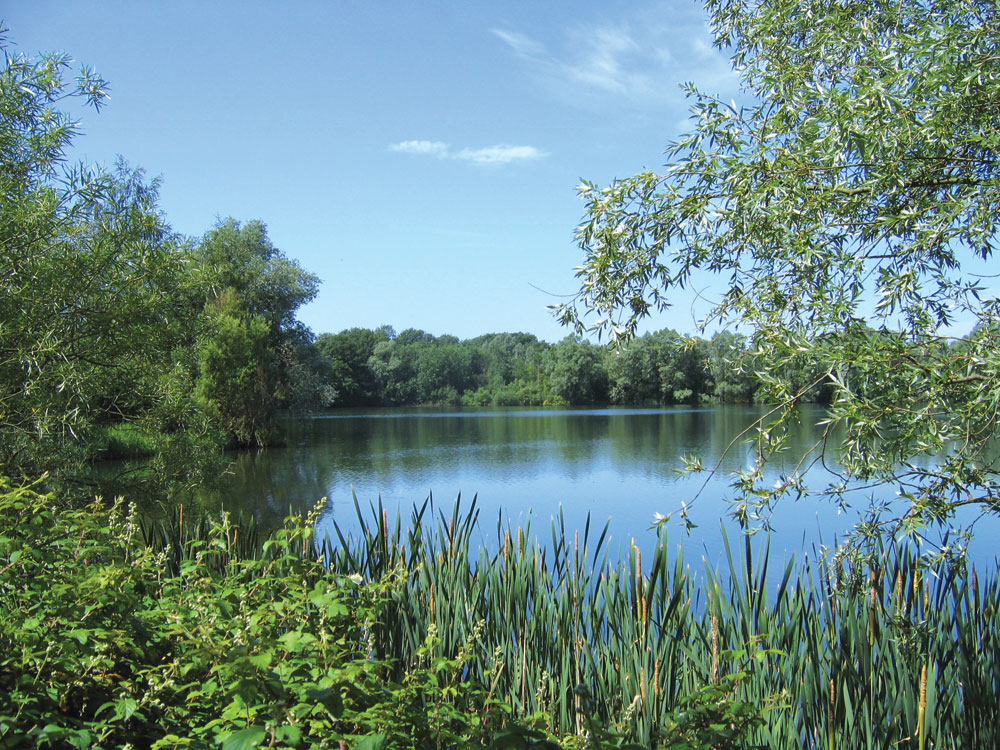
In the current economic climate, cost base is a major factor in managing a successful quarrying business, and wear costs associated with cone crushers can be a major cost centre. This paper explains a method to reduce wear costs by hardfacing crusher liners. Although this process is not new to the quarrying industry, it is not the norm, as there are many sceptics who have tried it in the past with bitter memories. However, the process has been perfected in recent years and can work well in the right applications.
Cone crushers operate by having stone fed into the top of the crusher chamber. The chamber is lined with wear parts, namely the mantle and bowl liners. As the stone drops though the choked chamber, crushing is achieved when the motion of the mantle causes compressive and abrasive forces to act upon the stone and bowl liner, causing the stone to break.
Liners are manufactured from manganese steel rather than normal steel as the manganese content provides protection against abrasion (normal steel generally has a lower tolerance to wear than crushing duties require). Depending on the stone being crushed, the percentage of manganese in the liners can vary from around 12% to 23%. Care has to be taken during selection, as insufficient manganese will not protect the liner, while too much can result in brittleness in the liner, causing failure not through wear but through cracking. Either way, the cost of manganese can be significant but, as this paper will show, this can be reduced.
With continued use the crystal structure of manganese steel changes, becoming more dense. This occurs when the stone being crushed is forced against the liner causing it to ‘work-harden’. ‘Green’ manganese starts off at around 25 Rockwell (250 Brinell) and can achieve a hardness of approximately 60 Rockwell (660 Brinell) after a period of work-hardening.
Crusher selection
Correct crushing chamber selection is crucial when installing a cone crusher. The reduction ratio, which in turn determines the product produced, depends on the chamber selected. In addition, the closed-side setting (the gap where maximum crushing is attained) affects both wear and the product produced. For example, if a standard unit is used instead of a shorthead, a reduction in fine product occurs, resulting in recirculation and, hence, more wear.
The characteristics of the main types of chamber are:
Standard: shallower angle than a shorthead with a longer crushing face. Suitable for a larger feed size, generally +100mm, with a wide feed grading curve. Suitable for use as a secondary crusher but, if smaller feed is introduced, can become susceptible to packing/blockages.
Shorthead: steeper angle than a standard with a shorter crushing face. Suitable for a smaller feed size, generally –100mm, with a short feed grading curve. Suitable for use as a tertiary crusher but will not accept large feed size owing to its smaller feed aperture.
Liner selection
When selecting a crusher the bowl liner also varies in type:
- Coarse: wide inlet aperture
- Medium: medium inlet aperture
- Fine: small inlet aperture
Once again, selection depends upon the product required and the feedstock. Consultation with manufacturers is essential, some of whom will provide computer design facilities and offer wear-analysis services on both their own and other makes of crusher, such is the level of competition.
Health and safety implications
On most cone crushers, rough-cast manganese liners are fitted to the head assembly and concave using an epoxy material commonly known as crusher backing. Exposure to this backing material has been known to result in cases of sensitization, a condition which can lead to people having violent allergic reactions upon minute exposure, causing possible respiratory failure. Any reduction in wear part changes will not only reduce exposure to backing compounds (an improvement to employees work conditions required under COSHH), but also reduce the use of cranes or overhead winches, thereby further reducing the frequency of potentially hazardous situations. Some cone crushers do not use backing but instead have precision-cast and machined liners. Work to reduce wear on these has been carried out but is not discussed in this paper.
One of the most common sources of wear is the silica content of the stone being crushed.
Rock with a low silica content, eg good-quality limestone, does not normally give rise to high wear costs, whereas rock which contains a high silica component, eg sandstone, sand and gravel etc, invariably does. The problem is usually encountered as soon as the liners are fitted, with the manganese being worn away before it has a chance to work-harden. The resulting wear costs can be considerable, as new liners, cranes, fitters and associated downtime are usually all involved.
Hardfacing
In order to prevent liner wear during the initial period of work-hardening, specialist contractors can coat the liners with a protective surface. This process has to be carried out with great care because the manganese liners can distort and/or shrink during the process, causing a poor fit in the crusher. Small distortions are generally not a problem in crushers using backing compound, as the backing material compensates for any such irregularities. To apply the protective coating, the liner is placed on a rotating turntable and carefully preheated. A bead of 3mm thick chrome carbide is welded on to the liner as the table revolves. The areas requiring treatment are determined by the wear pattern on a normal set of liners, and by experimenting with resultant wear patterns on treated liners. Hardfacing can give the liners a protective coating of up to 62 Rockwell until it is worn off, but by this time the manganese should have work-hardened to its maximum hardness of around 60 Rockwell.
In trials undertaken at Quartzite Quarry the mantle of a standard 3ft Nordberg crusher had 3mm thickness of hardfacing applied from top to bottom, overlain with another 3mm from the middle to the bottom, with another 3mm near the bottom (ie a total thickness of 3mm where stone enters the crusher, 6mm where crushing is apparent and 9mm at the point of discharge). Wear was not as bad on the bowl liner, therefore this was treated with a single 3mm thickness across its entire surface. The stone being processed was a quartzite with an 85% silica content, a PSV of 65 and an AAV of 2.
Results
The 18% manganese liners used prior to the trials lasted for a maximum of 12 weeks (16,800 tonnes through crusher). The first trial liners using hardfacing lasted 38 weeks (53,200 tonnes through crusher), providing 216% extra life. As this proved such a success, it was decided (correctly) that a lower-cost manganese could be used. A set of 14 % manganese liners was then treated. These liners lasted for 48 weeks (67,000 tonnes through crusher), providing 298% extra life.
Cost implications
Including the cost of the manganese and crane hire, but not downtime, the hardfacing added 35% extra to the cost of a normal liner change, however the overall saving was 234% of the total budgeted for replacement liners in the first trial. In the second trial, because of the cheaper manganese steel used, the hardfacing added just 32% extra to the budgeted liner cost but overall savings rose to 319%. Moreover, exposure to the backing compound was also significantly reduced as just one liner change was required per year instead of four.
Restrictions to use
When applied, the chrome carbide bead forms a step which can slow the passage of material through the crusher. This holding effect can move the point of wear to the step area during the phase when the bead is being polished. While this did not prove to be a problem during the trials at Quartzite Quarry, it is a factor that should be considered. In some applications, mostly with shorthead crushers, it is not possible to use hardfacing as the opening aperture on the crusher is only just big enough to allow the entry of, for example, –100mm stone. When hardfaced, one bead on the mantle and one bead on the bowl liner will result in a 6mm reduction in the inlet aperture, thereby only allowing –94mm stone to enter, which could be critical. This can sometimes be compensated for by opening the crusher closed-side setting to widen the inlet, but this is not always possible.
Ancillary applications
Crusher feed trays were also fabricated with 6mm of chrome carbide hardfacing material and these have been found to be almost wear free; one feed tray installed over two years ago shows no sign of wear despite having had over 70,000 tonnes of material pass over it. This compares very favourably with the Hardox wear plates used previously which had to be changed every three months after 20,000 tonnes of material had passed over them. Again, this has reduced downtime and costs.
On chute applications hardfacing material did not prove effective over the entire chute length. At impact points it wore out as quickly as mild steel, and the main benefits are to be found where sliding contact takes place. Chrome iron tiles have since been fitted at points of impact and to date the results look promising, but it is still to early to quantify the benefits.
Conclusions
Hardfacing using chrome carbide can be effective in prolonging life in cone crusher liners. This results in reduced downtime, lower liner costs, less exposure to crusher backing and fewer lifting operations. While not a panacea for all wear problems, hardfacing is certainly worth exploring with crusher manufacturers and specialist welding companies. In addition, some wear part companies will supply ready-to-use hardfaced liners. The cost-effectiveness of hardfacing depends entirely on the application. For example, the process would probably not be cost-effective on a low-wear application, but even in some high-wear applications wear life may not be extended to the extent where it becomes cost-effective. Nevertheless, considering its low initial cost, there is little to lose but a lot to gain by trying hardfacing at least once.
Acknowledgements
The author would like to thank Martin Gardner, Robin Piper, Peter Knight, Barry Retallack, Neville Pearce, David Gee, Dave Clayton and Brian Rowe for their advice and assistance.