Pegson Crushers For The Western Isles
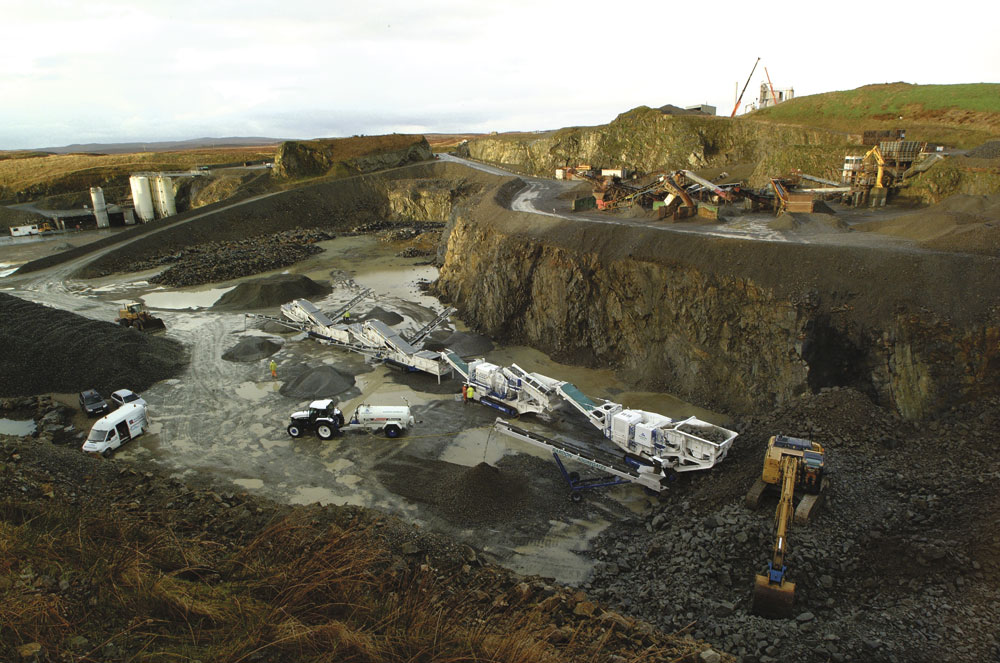
New mobile crushing and screening plant for Marybank Quarry
Marybank Quarry, located just outside Stornoway on the Isle of Lewis, is the base for Aggregate Industries’ Western Isles operations. With the Marybank site being the primary producer of quarried materials on the island, including asphalt, ready-mixed concrete and concrete blocks, the selection of mobile plant to replace the existing fixed plant was no easy task.
With the ageing fixed plant restricting the development of reserves at the quarry and demand increasing at other smaller production units around the Western Isles, traditionally crushed by contractors, it was time for change.
After an initial consultation period BL Pegson Scotland Ltd were chosen as preferred suppliers along with their sister company Finlay Scotland Ltd.
At Marybank Quarry the existing plant had evolved over the years to include four crushers, three screens and three re-feed hoppers to produce all the materials required to service the local market — from crusher run and scalpings through to single-sized aggregates for asphalt, concrete, drainage and surface dressing. The majority of products were produced in one pass but an amount of re-handling and reprocessing was required for some material.
The new plant was required to match the wide range of products produced at all the operational units on the islands with quality and quantity to spare, and to have the ability to be transported around the Western Isles with relative ease and with as little set-up time as possible.
Two crushers, two screens and a stockpile conveyor were selected for their ability to operate together to produce maximum quantities of finished products in one pass without re-handling. After final negotiations in 2003 the plant was dispatched in full Aggregate Industries livery and delivered to site between Christmas and the New Year for commissioning in early January 2004.
The Pegson Premiertrak 1100 x 650 HA primary crushing plant was supplied complete with a Cat C9 engine, full hydraulic drive to the tracks and conveyors, tracking and feeder remote control, abrasion-resistant hopper, vibrating grizzly feeder, electro-hydraulic operation of the clutch for the crusher drive, heavy-duty product belt, integral folding side conveyor, M-series single-toggle jaw crusher, water sprays and dust covers, with optional extras including an extended discharge belt, material discharge level probe, hydraulic drive dust-suppression water pump, auxiliary hydraulic supply to power the additional stockpile conveyor, feeder control by electronic load sensing and the all-new push-button hydraulic shim adjustment. With the crushing plant being fed directly by excavator from a blasted rock pile, a means to clear any potential blockages was included in the package; a quick-hitch and poker (supplied and fitted by Ken Malcolm Equipment) were matched to the existing Caterpillar 330LME excavator.
The Maxtrak 1000 cone-crusher plant features a Cat C9 engine, fully hydraulic drive to the tracks and conveyors, tracking and feed conveyor remote control, electro-hydraulic operation of the clutch for the crusher direct drive, extended feed hopper, variable-speed feed conveyor, metal detector on the feed belt, crusher feed level control, System 2 crusher setting controls with overload protection, medium-coarse auto-max manganese wear parts, interlocked discharge belt, hydraulic drive dust-suppression pump with sprays, conveyor cover and platform walkways.
The Maxtrak can be fed directly from the primary crusher discharge belt or by separate shovel feed, depending on site requirements.
Two Finlay 683 tracked screens were selected to provide sufficient screening of single sizes with minimal screen panel changes. Both of the three-way-split machines feature: a Deutz engine, hydraulic drive to all systems, chevron side belts, 12ft x 5ft top-deck and 10ft x 5ft bottom-deck two-bearing screen box, full screen access platforms, dust covers and dust-suppression sprays. To fulfil Aggregate Industries’ health and safety requirements the screens were fitted with polyurethane panels to help reduce manual handling and noise emissions. A first for Finlay Scotland on a 683, the factory fitted SCS panels were customized on site to suit the application. The finished single-sized aggregate products comply with both the outgoing British Standards and the new European specifications.
The layout of the Maxtrak 1000 crusher and the first Finlay 683 screen allows any oversize from the screen to be fed back to the crusher in a closed circuit, removing the need for re-handling. This consistent blending of the oversize and virgin crusher feed material optimizes the attrition crushing ability of the Automax crusher and maximizes the cubical shape of the finished aggregate.
Angus MacLeod, Aggregates Industries’ director for Stornoway, said: ‘In considering Aggregates Industries’ operations in the Western Isles and the need to produce a diverse range of aggregates for our asphalt and ready-mixed concrete plants throughout the islands of Lewis, Harris and the Uists, a mobile crushing plant was deemed to be the most suitable.
‘Our experience of mobile plants at both Marybank Quarry, Lewis, and Gairbh Eilean Quarry, Uist, led us to choose Pegson as the preferred suppliers. The previous successful use of a Pegson 1100 x 650 primary along with a Maxtrak 1000 cone crusher was found to be ideally suited for the flexibility and the wide range of products required.
‘This mobile set-up will also provide us with the opportunity to use the various items of equipment on specific construc-øtion projects throughout the islands. We are pleased with the production rates and quality of aggregate achieved so far, and BL Pegson Scotland Ltd along with Finlay Scotland Ltd have provided an excellent service from the initial supply stage to the commissioning of the plant.’