New Washing and Screening plant for Lightwater Quarries
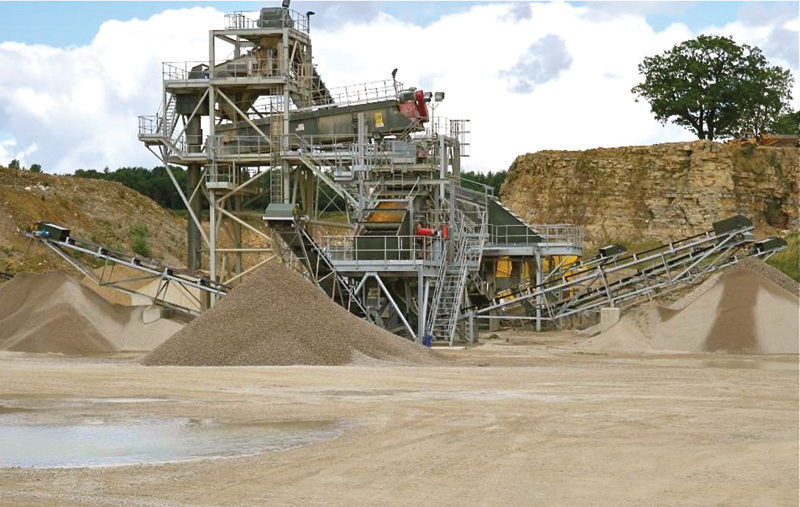
First published in the February 2014 issue of Quarry Management as Production Boost for Potgate
Lightwater Quarries’ new washing and screening plant delivers increased production with ease
Potgate Quarry, near Ripon, in North Yorkshire, is owned and operated by family-run Lightwater Quarries Ltd. In recent years, Lightwater have experienced a growth in demand for aggregates for use in concrete or as filter drainage material, which has led the company to focus on premium products such as sand and small-sized washed limestone rather than crushed rock for fill. A decision to improve the quality of the company’s materials by washing was one of the main drivers behind a recent decision to invest £1.5 million in a new washing and screening plant.
With Whitwick Engineering of Coalville appointed as main contractors, all the process equipment for the new plant was specified and supplied by Syscom BV. Whitwick subsequently designed a galvanized steel structure that would allow site personnel to ‘walk’ the entire process, providing safe, easy and permanent access to every element of the plant for maintenance purposes.
Ed Reed, managing director of Whitwick Engineering, commented: ‘The plant was designed with generous access for ease of maintenance as well as a considerable amount of detailed design attention to achieve the lowest possible long-term cost of operation and ownership in terms of both energy consumption and repair and maintenance costs.’
With the sticky clay at Potgate Quarry being the main operational issue, a decision was made to purchase a large second-hand log-washer – a fully refurbished Eagle Iron Works (EIW) 46in x 35ft unit – along with other equipment, including:
- an EIW 30in x 25ft fine-material washer
- a Krebs gMAX20 cyclone and SlurryMAX 6 x 6-17
- a Hewitt Robins VX-13 1.6m x 4.2m heavy-duty single-deck scalping screen
- a Hewitt Robins VC-13 1.6 x 4.2m triple-deck washing screen
- a Hewitt Robins VC-16 1.8m x 6.0m triple-deck washing screen
- a Hewitt Robins LPE-6 1.0m x 3.0m single-deck dewatering screen
- Tema Isenmann screen media, including ‘PS-Gitter’ pressure-welded wire mesh and WS85 modular polyurethane.
Guido Pas, managing director of Syscom BV, commented: ‘Lightwater’s request was simple: provide a solid plant that won’t break down and that will allow us to supply really clean products to all our customers. This all sounded very simple, but having seen their deposit it was clear that they needed the best equipment available.
‘The deposit can be extremely dirty with patches of tough, non-soluble clay and up to 50% silt, so this meant supplying the heaviest scrubber available and a reliable sand washing system to wash out the high silt content with minimal wear.
‘To make it all happen we found two excellent local partners in Hewitt Robins International for the supply of all the screens, and Whitwick Engineering for combining all the equipment into a user-friendly and robust plant.’
The new plant is fed from a remote tracked primary crusher fitted with a live roll grizzly that separates the clay from the rock. While the crushed product meets the full specification for MOT Type 1, all the material that passes through the grizzly is sent to the wash plant via a dump hopper equipped with a very wide, slow-moving belt that discharges on to a inclined delivery conveyor which is set at 90° to ensure no funnelling or channelling takes place.
The inclined conveyor feeds into the Hewitt Robins VX-13 1.6m x 4.2m heavy-duty inclined single-deck scalping screen. Fitted with Tema Isenmann ‘PS-Gitter’ pressure-welded wire mesh with an 85mm aperture, this screen is designed to protect the EIW 35ft log-washer, which can only accept material up to 100mm. Water is added at this stage to begin the process of breaking down the clay.
Wet –85mm material from the screen is fed into the EIW log-washer where more water is added, whereupon the action of the log-washer breaks up the clay while the water weirs out of the front and rear of the unit on to the first sizing screen – the Hewitt Robins VC-16 1.8m x 6.0m triple-deck washing screen (all three decks being equipped with Tema Isenmann WS85 modular polyurethane screen media). This takes out the +40mm, –40mm+20mm, –20mm+5mm and sand, with the –20mm+5mm product being fed on to the Hewitt Robins VC-13 1.6m x 4.2m inclined triple-deck washing screen, which separates it into 5mm, 10mm and 20mm clean material.
Material from the sand deck passes into an EIW slow-moving screw which drags the grit and +1mm fraction out of the sandy liquor and feeds it on to the Hewitt Robins LPE-6 1.0m x 3.0m single-deck dewatering screen (which is fitted with 0.5mm aperture Tema Isenmann WS85 screen modules). Water and the bottom end of the sand fraction weirs off into a sump before being pumped to the Krebs gMAX20 cyclone which makes an accurate cut at 70 microns and adds the fine sand on top of the bed of coarse sand exiting the screw. The resulting mixture of two sands, which effectively meets the specification for medium grit sand, is conveyed from the dewatering screen, in a reasonably dry condition, to the stockpile.
According to Lightwater Quarries, the new plant has been a total success and has allowed production to be increased from 100 tonnes/h to approximately 180 tonnes/h, although rates of up to 220 tonnes/h are possible.
Kevin Parker, general manager with Lightwater Quarries, commented: ‘Syscom and Whitwick have put together a plant that meets my specification for employee safety, productivity, efficiency and product quality. They understood my requirements and were able to offer a bespoke solution. Their knowledge and experience were obvious from the outset.’
The new wash plant has provided more material for the three Lightwater Quarries–Concrete4U mobile batching plants that supply and mix concrete at customers’ premises. With the aggregates from Potgate being much stronger than the more chalky type of limestone found in other parts of North Yorkshire, the new washing and screening plant is fulfilling the demand for better quality material over a wider area.
- Subscribe to Quarry Management, the monthly journal for the mineral products industry, to read articles before they appear on Agg-Net