Moisture-reduction system solves wet stockpile problem for Quinn Glass
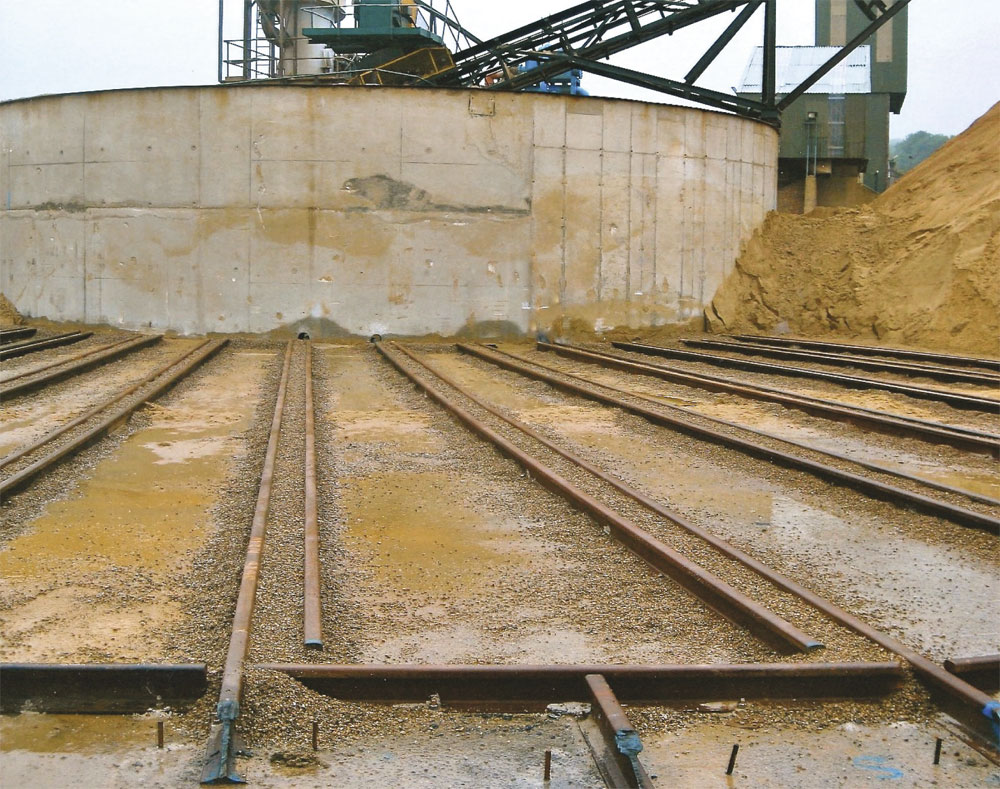
First published in the August 2013 issue of Quarry Management as Between the Lines
Innovative moisture-reduction system solves Northern Ireland glass-maker’s wet sand stockpile problem
When the directors and mangers of Northern Ireland-based Quinn Glass began to complain about the cost of melting the sand for their glass-making operation, particularly in light of a doubling in fuel prices over the past five years, it was quickly identified that something needed to be done to reduce the moisture content in the sand stockpile at the company’s glass sand producing quarry in Derrylin.
Gravity drainage of the saturated sand stockpiles was proving too slow, hampering production and leaving the base of the stockpile unstable, causing slumping and making it difficult for the front-end loaders to operate. The moisture content in the stockpile could still be as much as 15% even after many hours of gravity drainage, which was far too wet for the glass plant to operate efficiently.
In search of a solution, Quinn’s wash plant manager, Tommy Dolan, contacted Len McGarry of Congleton-based Moisture Reduction Systems Ltd, to see if anything could be done to reduce the moisture content of the stockpiles using MRS’s vacuum-assisted accelerated pumping system.
Len McGarry visited the Derrylin site and carried out an initial site survey to assess basic technical details such as estimated (k) permeability value (10–4 m/s), particle size and shape, stockpile size, percentage moisture retained after gravity drainage production cycles etc.
Moisture Reduction Systems Ltd also conducted a small drawdown pumping test on the material, the results of which showed that moisture levels could be reduced to approximately 4–5% retained moisture after only a few hours pumping using the MRS system.
The design proposal and budget quotation submitted incorporated a unique installation technique methodology involving laying the perforated, filter-wrapped drainage pipe between two sets of railway lines in a ‘rip rap’ configuration at the interface between the base of the sand stockpile and the concrete floor (see fig.1). This installation method has since proved very successful in ensuring that the front-end loaders cannot damage the drainage pipe.
As the moisture-reduction system had to be installed in three separate operations, to ensure that uninterrupted sand production could continue throughout, MRS worked at ‘off-peak’ times to suit the customer’s production programme.
Attached to the special perforated drainage pipe between each set of railway lines is a non-perforated vacuum/water conveying pipe leading to a six-take-off pump manifold connected to two D100 7.5kW Selwood electrically driven pumps (one duty pump and one stand-by pump) fitted with extra-large, twin-diaphragm, vacuum-pump systems (see fig. 2).
A filter media was placed around the drainage pipe to arrest any transported fines in the accelerated flow paths, thus preventing the migration of fine particles from blocking the pipe once operational.
Commenting on the system now in operation, Tommy Dolan said: ‘The MRS installation is now saving between £25,000 and £35,000 (sterling) per week, which, when multiplied by 50 weeks’ production, equates to £1.75 million in fuel savings alone each year. In addition, our materials are now drier and easier to handle. The system is simple to operate and reliable, and we are very pleased with our investment.’
For more information or to arrange a free drawdown pumping test/report and/or budget quotation, contact: Len McGarry (Northern Office) on tel: (07836) 516216; email: drysand@btconnect.com; or Andrew Burden (Southern Office) on tel: (0203) 397 8565; mobile: (07872) 182277; email: andrew@moisturereductionsytems.com
- Subscribe to Quarry Management, the monthly journal for the mineral products industry, to read articles before they appear on Agg-Net