Metso resolve challenging crusher application for Gallagher Aggregates
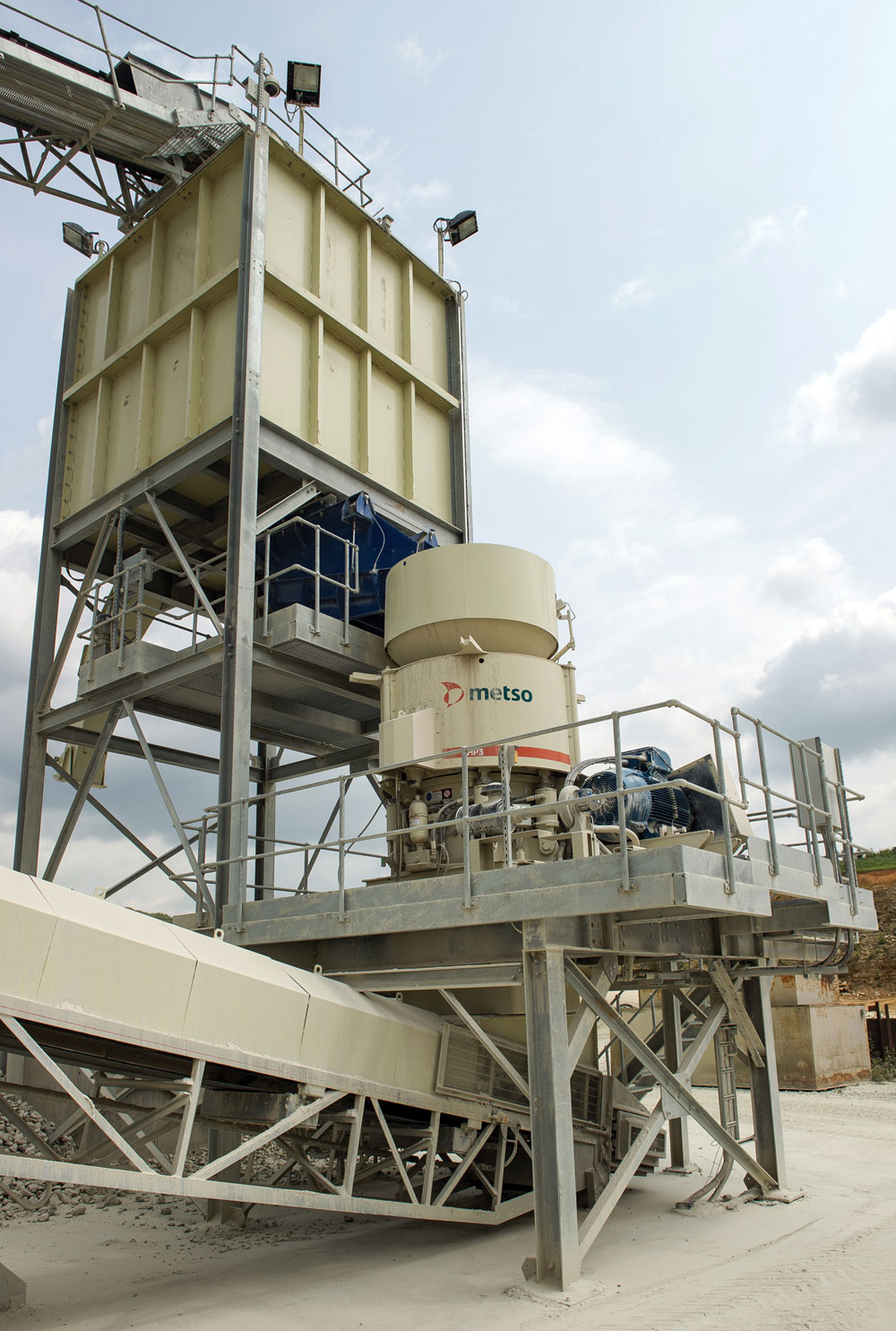
First published in the September 2013 issue of Quarry Management as Madness or Brilliance
Metso HP3 cone crusher provides successful solution in challenging application at Hermitage Quarry
In late 2012, a new state-of-the-art Metso HP3 high-density cone crusher provided a successful solution to a challenging crusher application at the centre of an ambitious business plan for Gallagher Aggregates Ltd’s operations at Hermitage Quarry, near Maidstone, in Kent. The following case study examines the aspects considered and the tests carried out to verify whether the objectives of the scheme could be achieved before the full project investment commenced.
The main objective of the business plan was to significantly increase the production of concrete sand together with single-size aggregate products, and to deliver a shape/quality that would suit both the asphalt and concrete market sectors.
To achieve this, a dedicated tertiary crushing application was required by Gallagher Aggregates, with the feed source for this process being identified as a nominal 80mm x 30mm material; this, in effect, being the mid-size material produced by the site’s existing Metso NP1315 secondary impactor. This material consists of competent Kentish Ragstone from the interbedded deposit at Hermitage Quarry.
Initial trials used an impact crusher to carry out the tertiary crushing stage, but while this resulted in good shape, wear rates proved uneconomical and the proportion of oversize was prohibitive. The next stage involved using a classic cone crusher, but with such a large feed size (80mm) and by attempting a large reduction ratio of approx 5.0, it came as no surprise that this resulted in many compromises. The net effect of the classic cone crusher was insufficient production to meet the market demand for high-quality single-size aggregates and high volumes of concrete sand. Thus, a much more dynamic and creative solution was required to meet the business needs.
With knowledge of the advantages that the new Metso HP3 high-density cone crusher claimed to deliver, a challenge was presented to Metso UK to verify the theory behind the HP3’s design. The objectives of this challenge can be summarized as:
- Feed size: 80mm x 30mm at 130 tonnes/h
- Crushability: 41.7% (LA 20)
- Crusher product: majority –20mm
- Flake index: 10mm and 14mm products to have less than 15%
- Sand: maximize 0–4mm material for use in ready-mixed concrete
- Reduction ratio: 5.0–5.7 (feed size passing 80% divided by the crushed product size passing 80%).
Anyone with reasonable knowledge of cone crushing (ie with classic cones) would immediately suggest that in order to produce high-quality aggregate with the nominated feed size, a multi-stage cone crusher system would be required. Normally, the maximum reduction ratio for high-quality final aggregates would be in the range 2.0–2.5, so to invest in a single crushing stage to meet the high specification could be regarded as verging on madness.
However, believing in the design principles of their new HP3 high-density cone crusher, Metso UK accepted the challenge and proposed a system with a single HP3 unit, as shown in figure 1. Their expectation was that the crusher would make a large reduction and produce high-quality aggregates along with a good proportion of 0–4mm concrete sand. This was subsequently accepted by Gallagher Aggregates Ltd.
Principle of the high-density crusher
The principle behind the effectiveness of the high-density crusher lies in the design of the chamber kinematics, which involves a large eccentric stroke and a chamber profile that ensures a completely choked crushing chamber through to the point of exit. As a result, no weak (flaky) stone can survive in the crushed product.
This is combined with the effect of increased stroke at the top of the chamber, where there is now more crushing, together with better distribution of the reduction stages over the full length of the chamber (see fig. 2).
It was quickly appreciated by both parties that the risks involved in making a large investment hinged on the performance predictions of the new-concept HP3 crusher, ie product gradation, shape and throughput. Full-scale testing was, therefore, deemed to be mandatory.
Metso set up a date for the test at an existing HP3 installation in France, and Gallagher Aggregates Ltd transported their Ragstone material to the site. At the test site normal production was isolated and tests at various settings were conducted to verify the earlier predictions. The crusher tests were conducted with the same feed material at various closed-side settings to provide data for evaluation. The results are shown in table 1.
Review of the results
The results confirmed the effect of the new crusher design:
- The reduction ratios required were achieved without ring bounce and machine stress beyond the determined thresholds, due to the HP3’s design and it ability to accommodate higher crushing forces.
- Best aggregate shape was generated by the high density in the chamber, ie where high reduction was taking place and where power demand was maximized.
- The minimum setting was determined by the point at which the crusher density started to ‘pack’ crushed material into aggregate chips – a limit imposed by the rock type rather than the design of the crusher. The limit in this case was at a closed-side setting of 9mm, at which point the test was judged as void.
Conclusions
The results proved categorically that the crusher could deliver the performance required by the project objectives. They also provided the confidence required to give the ‘go ahead’ for the complete crusher installation, including new surge bin, conveyors, screen, HP3 cone, IC7000 control system, increased power supply and new plant control system.
While some had opined that it would be ‘madness’ to adopt a single-stage crushing concept, the end result can be regarded as an entrepreneurial vision of ‘brilliance’ that firmly reinforces the claim that the Metso HP3 high-density cone crusher is capable of delivering a performance not possible with any other crusher currently on the market.
It should also be noted that this ‘lifting of the bar’ on crusher performance is sustained by the Windows-based IC7000 crusher control system (fig. 3). This, used in conjunction with automatic crusher setting control, provides dedicated control of start-up and shutdown, together with a continuous display of the crusher’s health.
Andy Bate, managing director of Gallagher Aggregates Ltd, commented: ‘The new HP3 has enabled our business plan to deliver a solution not possible with any other type of crusher, and has enabled us to drive our products higher up the aggregate value chain, providing us with a significant competitive edge.’
Adam Orr, Metso’s capital equipment sales manger for the UK & Ireland, verified that the new HP design has had similar success wherever it has been installed, and that there is now a significant global population with a total of 26 HP3 units, 296 HP4 units and 30 HP5 units installed worldwide.
For further information contact Adam Orr on tel: +44 (0)1788 532100; mobile: 07775 702760; fax: +44 (0)1788 547883; email: minerals.info.uk@metso.com; or visit: www.metso.com/miningandconstruction
Acknowledgement
Metso UK would like to thank Andy Bate and Steve Copland, managing director and maintenance manager, respectively, with Gallagher Aggregate Ltd, for their co-operation in the production of this article.
- Subscribe to Quarry Management, the monthly journal for the mineral products industry, to read articles before they appear on Agg-Net