Metso Develop Innovative Aggregate Crushers
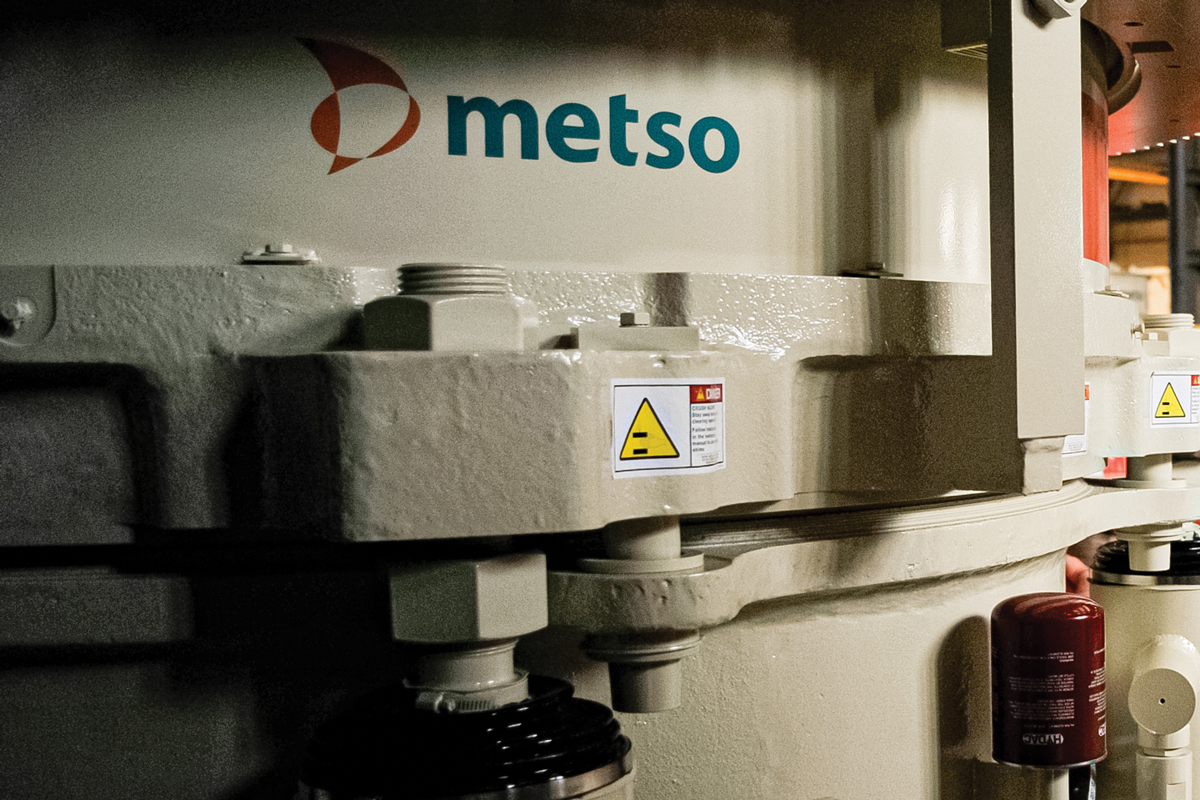
First published in the September 2019 issue of Quarry Management as Metso Milestones
The Finnish manufacturer continues to transform and evolve, developing innovative new products and achieving significant milestones along the way
The last 12 months have been both momentous and transformational for Metso with a number of significant corporate changes and developments, starting last year when the company celebrated its 150th anniversary. Established in 1868 as a Swedish ironworks, Metso have evolved through a series of mergers, acquisitions and divestments, and today operate in more than 50 countries and have over 12,000 employees.
With its headquarters in Tampere, Finland, the company is now a global industrial business providing the world’s mining, aggregates, recycling, and process industries with innovative solutions for the sustainable processing and flow of natural resources. One of Metso’s core areas of expertise is aggregates and minerals processing.
The first innovations that kicked off mechanical crushing and screening processes in mines and quarries were introduced during the late 1800s. In 1886, Finnish migrant Bruno Nordberg settled in Michigan, in the US, and produced some of the first crushing equipment for mines. Nine years later, in 1895, Bergeaud & Bruno were established in Mâcon, France, to manufacture single-toggle crushing equipment.
In 1928 Nordberg acquired the Symons cone crusher technology, an innovation that was to revolutionize crushing practices in mines and quarries, whilst in Tampere, Finland, Lokomo began producing their first jaw crushers at the beginning of the 1920s. These industry pioneers all became key components of Metso’s DNA.
The amalgamation of Svedala Industri AB into Metso in 2001 and the introduction of solutions such as primary gyratory crushers, grinding mills and vertical-shaft impactors were key elements in the creation of a full-scope offering for crushing and screening.
Today, after a century and a half of helping to shape and build the modern world, digitalization, sustainability and energy efficiency are among the focus areas in Metso’s current research and development, one example of which is the Metso Metrics concept – a cloud-based, remote-monitoring and data-visualization service for mobile crushing plants.
Continuing their corporate evolution, in February this year Metso moved their Pumps business area under their Minerals segment as part of future growth plans, then in June the company signed an agreement to acquire McCloskey International, the Canadian mobile crushing and screening equipment manufacturers, to expand its offering to the aggregates industry globally and strengthen its customer reach in the general contractor market.
Just a few weeks after this came the announcement that Metso and Outotec had agreed to combine their businesses to create a leading company in process technology, equipment and services, serving the minerals, metals and aggregates industries.
Aside from these recent notable corporate transformations, however, new product development has also continued apace during the past 12 months, with a number of announcements heralding the launch of the renewed Lokotrack LT200HP mobile cone crusher, the brand new Superior MKIII primary gyratory crusher and MX3 Multi-Action cone crusher, and the expansion of the company’s wheel-mounted NW Rapid range. Moreover, in June 2019 Metso reached a significant milestone with the sale of their 10,000th Nordberg HP-Series cone crusher.
Renewed Lokotrack
In October 2018 Metso announced the launch of a renewed, more efficient version of their Lokotrack LT200HP mobile cone crusher, designed for secondary and tertiary crushing operations. Thanks to its direct V-belt drive from the gearbox, the renewed solution is said to deliver fuel consumption savings of at least 15% compared with hydraulic-driven cone crushers. Moreover, the LT200HP complies with European Stage V emission regulations.
‘Fuel consumption and efficiency are always at the top of our customers’ priority lists, and reducing emission levels has become an increasingly important issue in recent years,’ said Kimmo Anttila, vice-president of Lokotrack Solutions at Metso. ‘In this respect, the LT200HP delivers on all counts with fuel consumption savings of 15% or more.’
In addition to being more efficient, the renewed LT200HP features several safety and maintenance improvements. These include elevated service platforms to ensure safe, easy access to service and maintenance points, and improvements that make daily maintenance quicker and easier. The LT200HP is also available with the Metso ICr wireless information and control system, which allows customers to monitor and control the crushing plant from an excavator cab. An entire train of Metso Lokotrack mobile plant can be controlled with Metso ICr for a complete crushing and screening solution.
New gyratory
Last October also saw Metso announce the launch of their new Superior MKIII primary gyratory crusher, which is said to provide a significant leap in comminution circuit performance. Guillaume Lambert, vice-president of mining crushers at Metso, said: ‘Our customers are facing increasing pressure to optimize capital expenses and improve the efficiency of their comminution circuit. With the new MKIII, we are addressing these challenges directly by offering peak performance and maximum throughput, while reducing the cost of primary-stage infrastructure.’
Designed for the most demanding primary crushing conditions and featuring the new, patented SmartStation for optimized production, the Metso Superior MKIII is designed to bring a new level of cost-effectiveness and reliability to operations. It is said to be the first high-speed primary gyratory crusher on the market, surpassing traditional primary gyratory crushers by up to 30% in speed and thus having a 30% higher capacity. Moreover, the rotable top shell ensures safe maintenance and reduces downtime by up to 70%. The MKIII can also be paired with the Metso Metrics digital solution for predictive maintenance and online asset management.
‘The MKIII is the third generation of our trusted primary crushing technology and has been developed through close dialogue and co-operation with our customers,’ continued Mr Lambert. ‘With the Superior MKIII, it is possible to use smaller machines to achieve the same highest-duty performance, making it the most capex-efficient technology on the market for the primary stage.’
Expanded range
In late 2018 Metso announced the expansion of their wheel-mounted NW Rapid range with the launch of higher-capacity models and the introduction of a variety of cone crushers, including the first model featuring Metso’s MX crusher.
NW Rapid crushers can be delivered in standard containers from the factory and are designed to be easily movable from one location to another using standard prime movers. Models in the NW Rapid range are designed to be set-up and dismantled in 24h, with 11 pre-designed layouts to speed up planning of the crushing process. The solution consists of modules that can be used to create a variety of combinations as needed.
‘A large share of our customers supply aggregates for public infrastructure projects that can last from a few months to a couple of years,’ explained Julius Mäkelä, Metso’s director of portable and modular solutions. ‘Depending on the project phase, our customers must have the ability to offer very high capacity. The new NW Rapid crusher models allow production capacity to be temporarily increased up to 500 tonnes/h, which is equal to the capacity of a fixed plant. Because of this flexibility, customers can better respond to short-notice orders and can accept contracts that cannot be carried out with traditional fixed solutions.’
The NW Rapid series models are electrically driven and equipped with Metso’s IC Series crushing automation as standard. In addition, they can be connected to the Metso Metrics remote monitoring service, which allows central monitoring of the entire crushing fleet’s production and energy consumption. The latest NW Rapid crusher models include the screen-equipped NW330GPS and NW300HPS cone crushers, along with the NW4MXS model featuring the MX4 Multi-Action cone crusher. Serial production of the NW4MXS unit begins this year.
New cone crusher
Earlier this year Metso announced the introduction of the latest addition to their MX Multi-Action cone crusher series. The new MX3 model is said to offer improved crusher productivity and lower operating costs with a design optimized especially for mid-sized quarrying applications.
‘Our customers are constantly looking to improve their operational efficiency and to optimize yield for the most desired product fraction. With MX Multi-Action technology, we can help our customers to achieve these targets,’ said Arto Halonen, Metso’s vice-president of aggregate crushers. ‘After successfully introducing MX4 to the market in 2017, we are excited to launch the MX3 model, so that an even wider range of aggregate producers can benefit from the unique advantages the MX and Metso can offer.’
According to Metso, the MX ensures cost-effective and safe operations with a high reduction ratio, superior product shape and consistency. The patented Multi-Action technology is also said to deliver greater uptime and savings in the cost of crushing operations. With the selective production features the MX series offers, crusher production can be optimized to maximize the yield of desired fractions. Moreover, crusher operations have been made easy and safe with advanced Metso IC series automation.
The MX3 cone crusher, which is suitable for secondary, tertiary and quaternary crushing stages, is designed for both hard and soft rock applications and will initially be available for stationary solutions.
Meanwhile, following its introduction two years ago, the MX4 cone crusher has proven itself at various customer sites around the world. Mathieu Kasprzak, director of operations at Durance Granulats in France, said: ‘The MX4 has met our expectations and delivered instantaneous flow rate as well as improved crushing energy efficiency. We have also been piloting the MX3 on the quaternary stage since April 2018 and we are fully satisfied with its performance and plan to continue with it.’
Major milestone
This year has also seen Metso achieve a significant milestone by reaching 10,000 global sales of their Nordberg HP-Series cone crushers. With the HP Series celebrating its 30th anniversary this year, the 10,000th unit was handed over to French aggregates and asphalt producers and urban infrastructure development company Eurovia during a special ceremony in June at Metso’s Mâcon facility, in France.
‘The HP is undoubtedly one of Metso’s most widely used innovations,’ said Arto Halonen, vice-president of aggregate crushers at Metso. ‘It’s a technology that has been evolving throughout the years to meet customers’ changing needs, making their operations more successful through proven performance and reliable output. That is most likely why the HP has become an industry standard for a variety of aggregates and mining applications.’
The origin of the HP Series cone crusher can be tracked back to Milwaukee, in the US, in the early to mid-1980s. Technological breakthroughs by the Nordberg research programme redefined crushing performance and provided the basis for a new type of cone crusher introduced in 1989: the Nordberg High-Performance cone crusher series, now simply known as the HP.
Today, HP cone crushers are engineered and manufactured at Metso’s competence centre in Mâcon, France, with manufacturing also taking place in Brazil, China and India. The versatile crusher is said to be suited to a wide range of fixed and mobile applications, from limestone and ballast production to manufactured sand.
‘Know-how from developing the HP and from thousands of customer applications around the world has played an integral part in Metso research and development initiatives in crushing,’ continued Mr Halonen. ‘This is an important milestone for Metso and we want to thank our customers for their continued confidence in us during the first 30 years of the HP’s journey and look forward to exploring new development possibilities in the years to come.’
- Subscribe to Quarry Management, the monthly journal for the mineral products industry, to read articles before they appear on Agg-Net.com