MEP hydrosizer for Pyford Brook Quarry
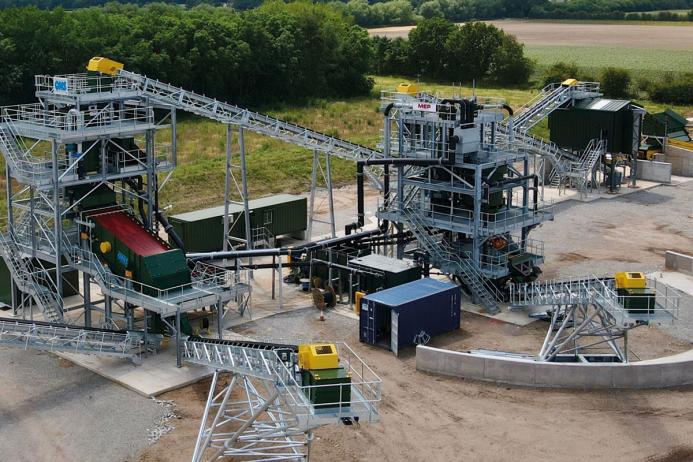
First published in the August 2023 issue of Quarry Management as Losing the Lignite
MEP deliver two-stage lignite-removal system as part of contract to supply new sand and gravel plant for Cemex’s Pyford Brook Quarry
Mineral Engineering Processes (MEP) Ltd, first incorporated in 1983 as part of the R.O. Stokes group, have been operating since 2002 when they took over the sales and service of the Stokes range of specialist products. In that time MEP have built a dedicated customer base supplying equipment around the world, primarily in the UK, to the mining and quarrying sectors.
MEP specialize in mineral process engineering, providing sales and service for their specialist range of proprietary equipment, including TBS Hydrosizers, hydrocyclones, thickeners and other allied equipment. They are also the UK sales agent for the Pozzato range of log-washers and screens. The company says its unique selling point is efficiency and building bespoke plants based on the customer’s needs rather than picking a plant from a standard catalogue.
Providing added value to clients is central to MEP’s work, whilst designing and developing equipment and solutions for the beneficiation and classification of quality products created from raw minerals. The intention is to deliver the highest-quality service, on time and on budget, providing well-designed, user-friendly machines that exceed customers’ expectations.
In 2021 Cemex awarded MEP the contract to design, deliver, construct, and commission a new, fully operational mineral washing and processing plant at the new Pyford Brook Quarry, near Alrewas, in Staffordshire. The quarry processes Trent Valley sand and gravel which contains lignite throughout. MEP have resolved this problem at many sites producing clean, well-graded, de-lignited sand to the levels required for this project. The company’s experience of supplying de-ligniting equipment for the Trent Valley dates back to the 1970s when BCA first installed hydrosizers to remove lignite from concrete sand.
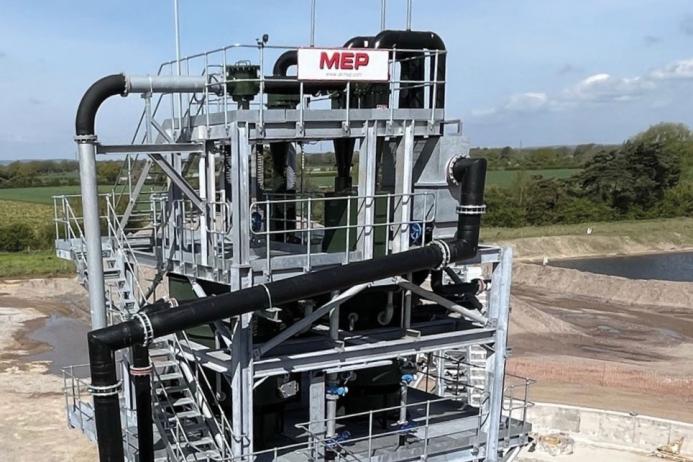
The project
The project involved the supply and installation of a bespoke 230 tonnes/h sand and gravel plant, with the ability to process 300 tonnes/h including re-crushed material. The plant is designed to produce 4–10mm and 10–20mm aggregates, both with 1,000-tonne stockpiles, and a washed concrete sand with a lignite content of <0.04% by weight, with a 2,000-tonne stockpile.
The primary gravel section consisting of a feed hopper, belt feeder, cone crusher, and a primary and secondary screen were subcontracted to Quarry Manufacturing & Supplies (QMS), with an MEP Hydrolig integrated into the primary process to remove coarse lignite before the MEP two-stage de-ligniting sand plant.
The Hydrolig is a variation of the TBS Hydrosizer, which is a hindered settling classifier that uses an upward current of water to separate materials by specific gravity. It is designed to handle material up to 40mm, however at Pyford Brook it receives the –20mm fraction. The Hydrolig uses water and sand particles to create a natural media within the vessel of the tank. The lower-density particles, such as sand and lignite, float to the surface and overflow to an MEP sieve bend which separates the coarse lignite from the water and sand. The heavier gravel sinks and is discharged through the spigot and falls by gravity to the QMS secondary screen and on to conveyors producing the 4–10mm and 10–20mm aggregates.
The MEP two-stage de-ligniting sand plant receives the –4mm material together with the water from the Hydrolig plant. The feed material and water report to the primary sump and are pumped to two primary high-capacity cyclones, which partially dewater the material and remove some of the silts. The primary cyclone underflows report to the primary TBS Hydrosizer.
The TBS Hydrosizer underflow discharges on to a dewatering screen to produce a concrete sand. The overflow, which contains lignite together with the finer sand, reports to a sieve bend. The sieve bend overflow passes, by gravity, to the effluent tank. The underflow reports to the secondary sump where it is pumped to a secondary high-capacity cyclone which discharges to a secondary Hydrosizer. The Hydrosizer underflow discharges to the SDS dewatering screen, where it is dewatered and discharges to a QMS radial stockpile conveyor. The overflow from the secondary Hydrosizer reports, by gravity, to the effluent tank.
David Hakes, senior project manager for Cemex, commented: ‘The team at MEP have a proven track record working with this material and with Cemex, having installed a similar plant at our nearby Willington Quarry. Following numerous technical and commercial discussions, we placed a contract with MEP. The plant was built to meet our continually improving standards for safety in operation and maintenance.’
Steve Slingo, sales manager at MEP, commented: ‘The new plant, which was designed to achieve clean, well-graded sand and gravel, has exceeded the customer’s expectations. Our unparalleled expertise, experience, and track record, together with our desire to work with the customer at all levels to ensure the best possible outcome, is industry leading.’
MEP would like to record a special thanks to their contractor team including Boast Site Services, Darren Lee Construction, Intelect Midlands, and QMS for their work on the Pyford Brook project.
Subscribe to Quarry Management, the monthly journal for the mineral products industry, to read articles before they appear on Agg-Net.com